The system working pressure of a die casting machine is the normal pressure in a hydraulic system of die casting machine.
Usually the system working pressure determined by the output pressure of the hydraulic pump. During the die-casting process, system working pressure plays a crucial role in ensuring that the molten metal can be effectively pushed and filled into the mold cavity, while maintaining a certain pretssure during the solidification process of the molten metal to form high-quality castings.
Some times the system working pressure is same as the pressure used to inject molten metal into the mold cavity during the die casting process.
This pressure is one of the core parameters of the die casting process and is usually expressed in megapascals (MPa) or pascals (Pa). Depending on the type of die casting machine and the process requirements, the system working pressure can vary greatly.
The injection pressure acting on the molten metal during die casting ranges from a few MPa to tens of MPa, sometimes even up to 500 MPa. For example, in some high-pressure die casting processes, the pressure can reach 4500 psi (about 31.03 MPa). In addition, the pressure and flow of the hydraulic system in the die casting process are usually controlled by an electro-hydraulic proportional valve to ensure that the pressure and speed of the processes such as mold closing, mold opening, core extraction, ejection, and injection are automatically adjusted according to the set process parameters during the production process.
The system working pressure of the die casting machine is a key factor to ensure that the molten metal quickly fills the mold cavity under high pressure and solidifies under pressure to form castings.
What is the relationship between the system pressure and injection force of a die casting machine?
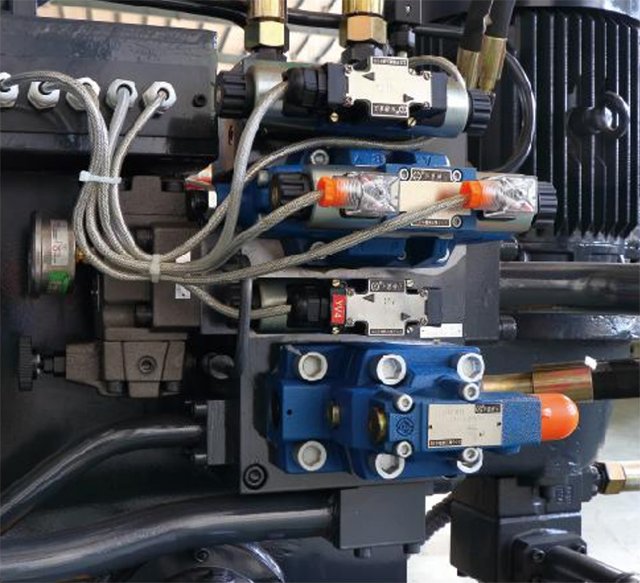
The relationship between the system working pressure and the injection force of the die-casting machine is mainly reflected in the management and control of the pressure during the injection process. The injection force is calculated by the inner diameter of the injection cylinder and the steady-state value of the pressure after pressurization.
The specific formula is:
Fd=P2 × R
Fd = the injection force
P2 = the inner diameter of the injection cylinder
R = the steady-state value of the pressure after pressurization
During the injection process, the system working pressure is used to store energy and convert it into power, thereby driving the injection punch to quickly fill the cavity with liquid metal. The stability and control accuracy of the system working pressure directly affect the stability and consistency of the injection force. For example, the pressure drop value detection of the fast injection accumulator requires setting the fast injection accumulator pressure to the system rated pressure and setting the fast injection stroke as required.
In addition, the design of the hydraulic control system also affects the realization of the injection force. For example, the use of a discrete circuit injection system (SCSystem) can ensure that different levels of injection do not interfere with each other and keep the pressure stable and constant. In actual operation, the slow injection speed adjustment will affect the injection follow-up speed when the mold is opened, thereby affecting the quality of the casting. The relationship between the system working pressure and the injection force of the die-casting machine is achieved through the design and control of the hydraulic system, ensuring that the injection force can be output stably and accurately under different process conditions to meet production needs.
What is the impact of die casting machine system working pressure on production efficiency?
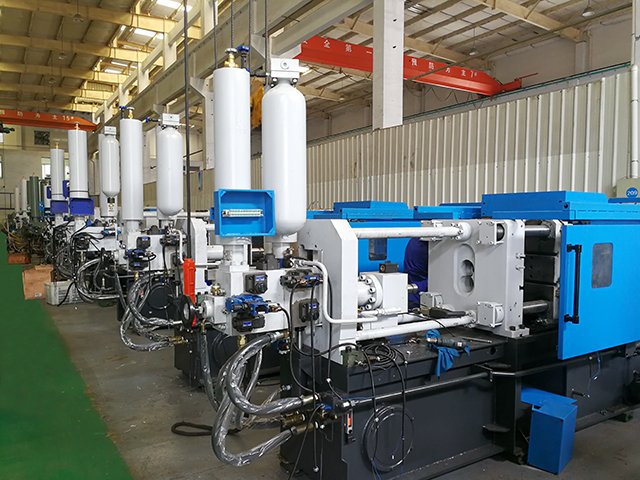
It is mainly reflected in the following aspects:
Influence on the filling speed and quality of molten metal: When the pressure is low, the filling speed of molten metal in the mold is slow, which may cause defects such as pores and shrinkage holes inside the casting, thus affecting production efficiency. On the contrary, excessive system working pressure may cause excessive splashing of molten metal, mold damage and other problems, which will also affect production efficiency.
Influence on the mold opening time and clamping action: During the die-casting process, the size of the clamping pressure needs to be set according to the size of the mold to ensure that the clamping action is fast and smooth. If the pressure is not set properly, it may affect the mold opening time, thereby affecting the overall production efficiency.
Influence on the quality of die-casting parts: By controlling the pressure, the density of the product can be increased, the formation of shrinkage holes can be reduced, and the product quality can be improved. High-quality castings can reduce rework and scrap rates, thereby improving production efficiency.
Influence on the operation and maintenance costs of die-casting machines: Excessive system pressure may cause equipment wear to increase and increase maintenance costs. Therefore, a reasonable setting of system working pressure not only helps to improve production efficiency, but also reduces equipment maintenance costs.
Impact on the degree of automation and ease of operation of die-casting machines: Modern die-casting machines are usually equipped with counter-pressure measures to eliminate pressure peaks and reduce water hammer phenomena, thereby improving production efficiency. In addition, reasonable pressure control can also simplify the operating process and improve the degree of automation.
The impact of die-casting machine system working pressure on production efficiency is multifaceted, including affecting the filling quality of molten metal, mold opening time, quality of die-casting parts, and equipment maintenance costs. Therefore, in actual production, it is necessary to adjust the system working pressure and mold opening time according to the specific situation to achieve the best production effect.
System pressure of Haichen die casting machine
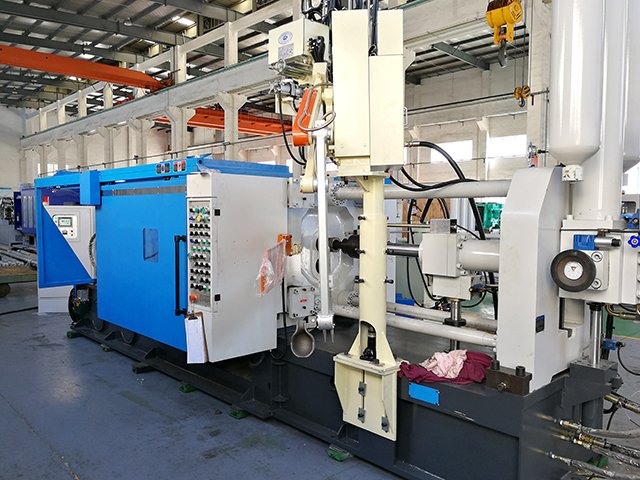
When choosing a Haichen die-casting machine, the system working pressure is an important consideration. According to the evidence, the tonnage calculation formula of the die-casting machine is based on the product of the clamping force and the casting pressure, which shows that the system pressure directly affects the tonnage selection of the die-casting machine. In addition, the design of the die-casting machine needs to consider the maximum pressure it can withstand to ensure that sufficient clamping force can be generated in long-term continuous operation.
When choosing a die-casting machine, it is also necessary to consider parameters such as injection speed, boost mode and pressure building time, which can be set and adjusted according to product characteristics. For example, the new generation of dual closed-loop full real-time control injection system developed by Ningbo Haitian Metal uses a Siemens control system to perform closed-loop control of casting pressure and injection speed, and closed-loop control of boost pressure and pressure building time. The boost pressure can be set in six sections.
Therefore, when choosing a Haichen die-casting machine, the system working pressure is a key factor, which needs to be comprehensively considered based on parameters such as product size, weight, wall thickness, etc., and the appropriate die-casting machine model and configuration should be selected to ensure product quality and production efficiency
The system working pressure is the engine of the machine, it will show if the die casting machine powerful or not. So it is an important factor when you choose the die casting machines.