Casting pressure of die casting is the pressure at which a liquid or semi-solid metal or alloy is filled into a mold cavity at high pressure and speed during the casting process. This casting pressure of die casting ensures that the metal completely fills every nook and cranny of the mold, resulting in a high-quality, detailed casting.
Casting pressure of die casting is a key parameter in the casting process, which directly affects the quality, dimensional accuracy and surface finish of the castings.
The significance of the application of casting pressure
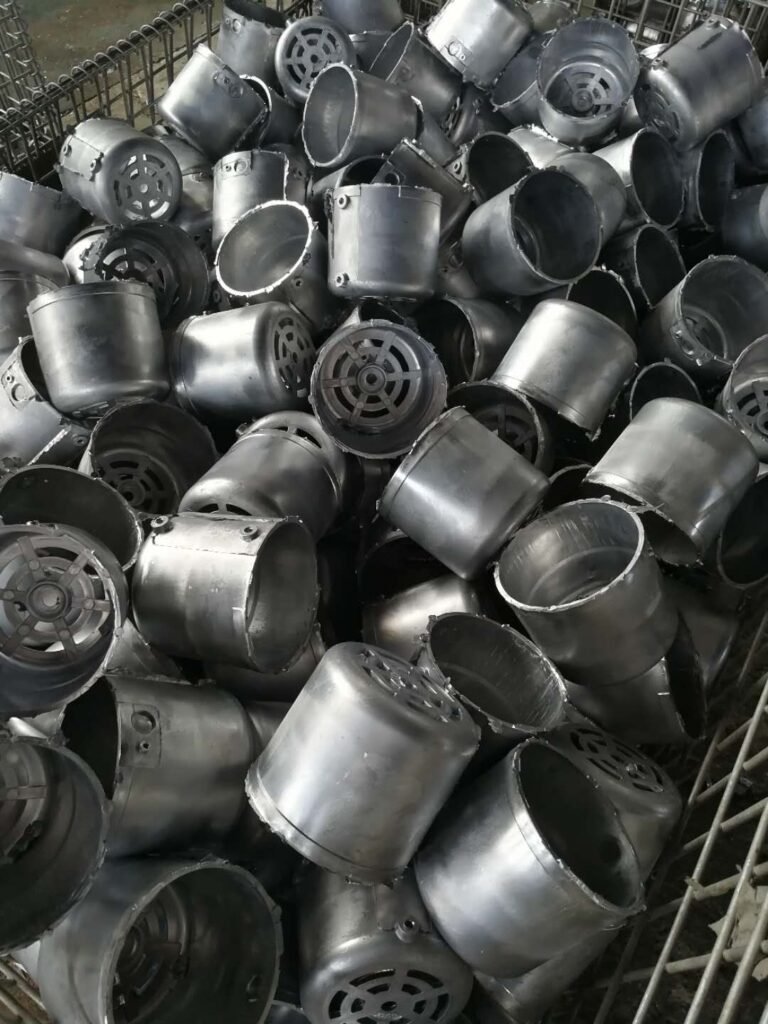
The significance of the application of casting pressure of die casting is that by adjusting the casting pressure, not only can improve the microstructure and mechanical properties of the casting, reduce casting defects, improve the denseness of the casting and the surface quality, but also optimize the performance of the casting, improve production efficiency and product quality.
Mainly reflected in the following aspects:
- Improve the casting microstructure and mechanical properties: by adjusting the casting pressure, can effectively improve the casting microstructure, such as grain refinement, dendrite spacing reduction, etc., so as to improve the casting mechanical properties
- Reduction of casting defects: Proper casting pressure helps reduce defects such as porosity and shrinkage in castings.
- Improve the denseness and surface quality of castings: the increase in casting pressure can significantly improve the internal microscopic pore defects in the rheological pressure castings, increase the density of castings.
- Optimize the performance of castings: by adjusting the casting pressure, you can optimize the performance of castings to a certain extent.
- Improve production efficiency and product quality: through the computer numerical simulation system and fluid dynamics modeling and other technologies, can effectively control product quality and improve production efficiency.
How to calculate the casting pressure required for die casting products
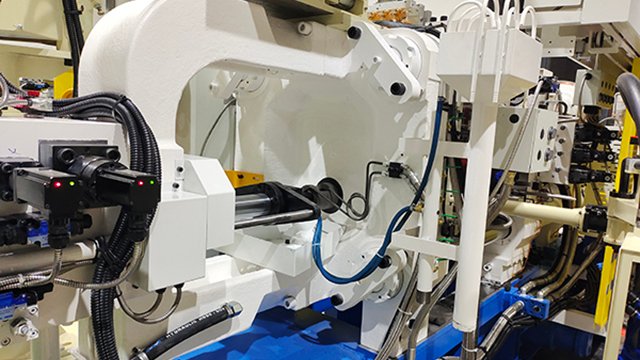
Calculating the casting pressure of die casting required for die-cast products is a complex process involving multiple factors and steps.
Here is a detailed calculation method:
1. Determine basic parameters
The following basic parameters need to be determined:
- Casting volume: The required amount of metal is determined by calculating the volume of the casting.
- Cylinder piston cross-sectional area: This is the cross-sectional area of the cylinder piston, which is used to calculate the filling injection force.
- Hydraulic pressure after boosting: This is the hydraulic pressure after boosting in the cylinder, which is used to calculate the boosting injection force.
2. Calculate the filling injection force
The filling injection force is calculated from the pipeline working pressure of the hydraulic system of the die-casting machine and the cross-sectional area of the cylinder piston.
3. Calculate the boosting injection force
4. Consider the change in the cross-sectional area of the casting
The cross-sectional area of the casting will change during the filling process, so it is necessary to design an adaptive pressure curve. The automatic calculation of the casting cross-sectional area can be realized through the secondary development of CAD software, and the UG software can be used to assist in identifying the location of the sudden change in the casting cross-sectional area, and then design an adaptive pressure curve that changes with the change in the casting cross-sectional area.
5. Consider heat transfer coefficient and heat transfer boundary conditions
When calculating the filling pressure, factors such as the heat transfer coefficient and heat transfer boundary conditions between the casting and the mold shell need to be considered. For example, the article mentions that the filling pressure required for the casting to be completely filled is about 15kPa.
6. Design the graded pressure curve
According to the change curve of the cross-sectional area of the casting, the casting is graded and the graded pressure curve is designed. This ensures that the casting can get the appropriate filling pressure under different cross-sectional areas.
7. Adjustment in practical application
In practical application, it may be necessary to make adjustments according to the specific casting material, mold design and production conditions. For example, the pressure on the extrusion rod should be greater than the die casting pressure, and the selection of the extrusion cylinder piston diameter must be verified by calculation, and it is better to be slightly larger.
8. Reference standards and specifications
During the calculation and design process, relevant standards and specifications can be referred to, such as the provisions in the horizontal cold chamber die casting machine group standard T/ZZB2712-2022, to ensure the accuracy and reliability of the calculation results.
Through the above steps, the casting pressure required for die-casting products can be calculated more accurately.
The casting pressure of Haichen die casting machine
The following is a table of parameters for our Haichen die-casting machines, which you can find in our full range of product catalogs.
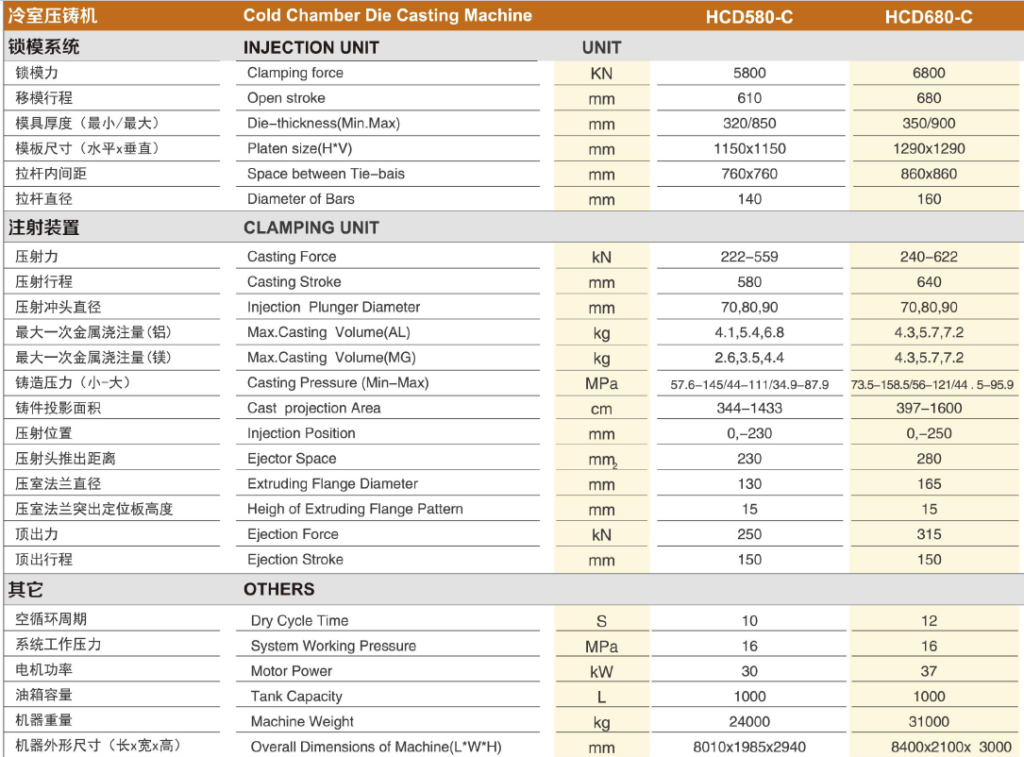
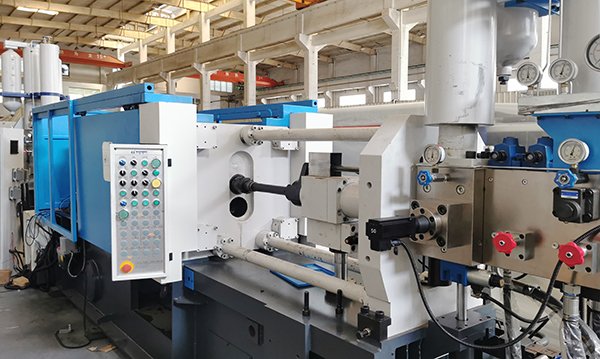
By referring to the table, you can check the design rated injection pressure of each of our die-casting machines. You can choose a die-casting machine with different injection pressures according to the design requirements and production requirements of your own products. If you need more similar technical support, please leave us a message, and we will ask you to calculate the solution at any time.
The casting pressure of die casting machine is the main date of machine. It can ensure the products can be produce well or not.