The platen material selection and design of die-casting machine is a comprehensive engineering problem, involving multiple fields such as material science, mechanical engineering and cost control. 5 types of the material: H13, 3Cr2W8V, SKD61, 4Cr5MoSiV, Copper alloy.
The die-casting machine platen is the core component in die-casting technology, which directly affects the quality and production efficiency of die-casting parts. This article will discuss the material selection and design of die-casting machine platen to ensure the efficiency and stability of the die-casting process.
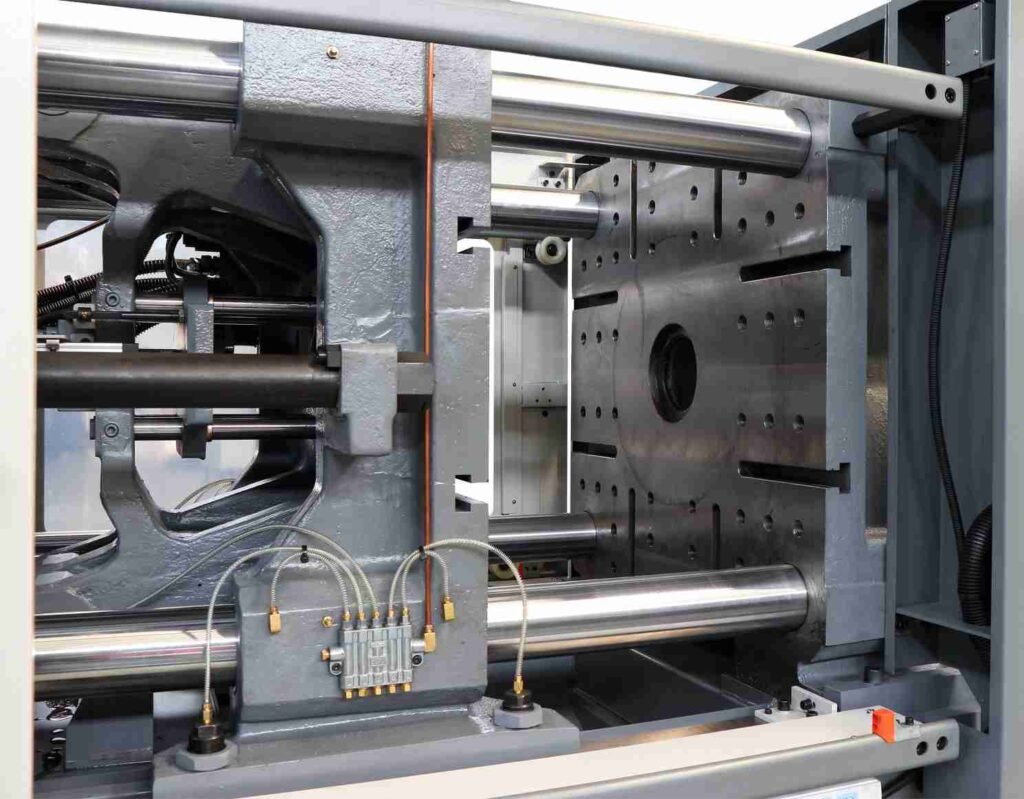
What materials should be selected for die-casting machine platen
When platen material selection and for die-casting machine platen/templates, multiple factors need to be considered comprehensively, including the working environment, service life, production requirements, and cost budget of the mold. The following are several commonly used die-casting mold materials and their characteristics:
- H13 mold steel: H13 mold steel is widely used in aluminum alloy die-casting molds due to its good toughness and red hardness, and has a high cost-effectiveness. It is suitable for manufacturing molds with high temperature, high stress but not subjected to impact loads, such as cores, sprues, etc.
- 3Cr2W8V (Three Chromium Tungsten Eight Vanadium): This material has good heat resistance and is suitable for the production of die-casting molds for aluminum alloys and copper. It is also commonly used in cold chamber die-casting molds.
- SKD61: SKD61 material has a high price and is suitable for mold making with high requirements and large order volumes. This material has high strength, high hardness, and good wear resistance, making it suitable for mass production.
- 4Cr5MoSiV: This material has high hardenability and wear resistance, making it suitable for molds that require high strength and high temperature resistance.
- Copper alloy: Copper alloy is commonly used in die-casting molds under high temperature and high pressure conditions due to its excellent thermal and electrical conductivity. It can maintain mold accuracy and stability, reduce wear and damage.
Other materials, such as DH-3840841H, 13Cr2W8V, 234W302 and other special steels, are also commonly used in the manufacturing of die-casting molds. They each have their own characteristics and are suitable for different application scenarios.
The selection of suitable die-casting mold materials should be based on specific production needs and cost budgets, while considering factors such as mold working temperature, mechanical properties, wear resistance, and corrosion resistance to ensure the service life and production efficiency of the mold.
Key factors in platen material selection
The die-casting machine platen is a key component that withstands high pressure, and its performance is crucial to the quality of die-casting parts. Material selection needs to consider mechanical properties, thermal properties, corrosion resistance, processing performance, cost-effectiveness and environmental adaptability. Suitable materials can improve the durability and production efficiency of die-casting machines.
- 1. Mechanical properties: The platen needs to have sufficient strength and hardness to withstand high pressure and wear. At the same time, good toughness can prevent the platen from breaking under high pressure.
- 2. Thermal properties: Since a lot of heat is generated during the die-casting process, the thermal expansion coefficient and thermal conductivity of the material are particularly important. This is related to the durability and temperature control of the platen.
- 3. Corrosion resistance: The die-casting process may come into contact with corrosive substances, so the material needs to have good corrosion resistance.
- 4. Processing performance: The material should be easy to process for easy manufacturing and maintenance.
- 5. Cost-effectiveness: While meeting performance requirements, cost is also an important consideration.
Common platen materials and their properties
When choosing platen materials, common choices include steel, cast iron, aluminum alloys, copper alloys, and composite materials. The following are the properties of common platen materials.
- 1. Steel: such as 4140, 4340, H13, etc., are widely used due to their good mechanical properties and heat treatment properties.
- 2. Cast iron: lower cost, but not as strong and hard as steel.
- 3. Aluminum alloy: lightweight, but not as strong and wear-resistant as steel.
- 4. Copper alloy: has good thermal conductivity, but higher cost.
- 5. Composite materials: such as carbon fiber reinforced plastic, provide excellent strength and stiffness, but higher cost.
Key elements of platen design
The design of the platen needs to consider size and shape, cooling system, fastening and positioning, and convenience of maintenance and replacement. A well-designed platen can ensure the accuracy and efficiency of the die casting process. An effective cooling system helps control the platen temperature and prevent overheating. Proper fastening and positioning ensure the stability of the platen, while convenient maintenance and replacement reduce downtime.
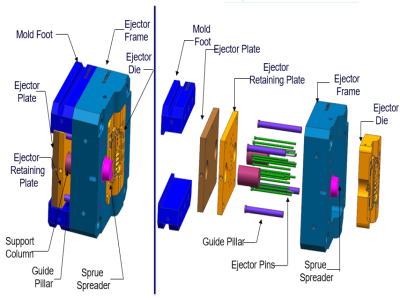
Balance between platen material and design
It is crucial to find a balance between the material and design of the die casting machine platen. On the one hand, the material needs to have enough strength and hardness to withstand high pressure and wear; on the other hand, the design must ensure that the platen can work stably under high pressure and high temperature. This balance ensures the long-term reliability and efficient production of the die casting machine.
The material selection and design of the die casting machine platen are the key to ensure the quality of die casting. By carefully selecting materials and optimizing the design, we can improve the performance of the die casting machine, reduce production costs, and improve the economic benefits of the entire production process. This is not only a technological advancement, but also a manifestation of industrial art.