Furnace of Die Casting
Furnace of die casting is a device used for melting metals,like aluminum, Zinc, and Megunsium.
After the metal heated to a liquid state, the die casting machine will injecte melting metal into mold.
The design of die-casting furnaces often takes into account melting efficiency and insulation performance to improve production efficiency and reduce energy consumption.
For example, some modern die-casting furnaces adopt advanced insulation technology, such as using super insulation cotton to extend the temperature drop time interval, thereby reducing energy consumption.
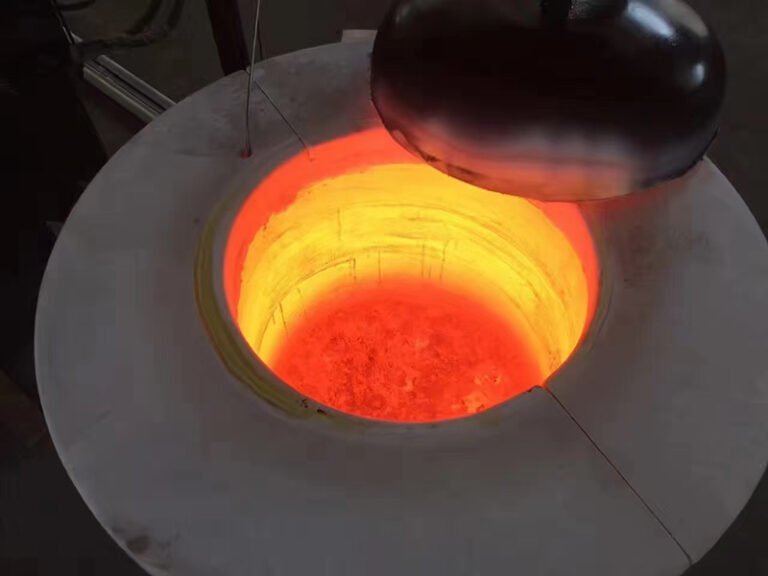
5 types of die casting furnace
The equipment types of die-casting furnaces mainly include the following:
- Electric furnace: used for melting high melting point metals such as steel or nickel based alloys.
- Induction furnace: suitable for melting various metals, especially in situations where rapid heating is required.
- Natural gas furnace: Use the natural gas heating the furnace.
- Holding furnace: commonly used in the production of aluminum, bronze, and brass castings, and is one of the most common types of furnaces in aluminum die-casting.
- Centralized melting furnace: a specialized equipment for centralized melting and insulation of aluminum alloys, suitable for continuous melting and uninterrupted operation.
Electric furnace
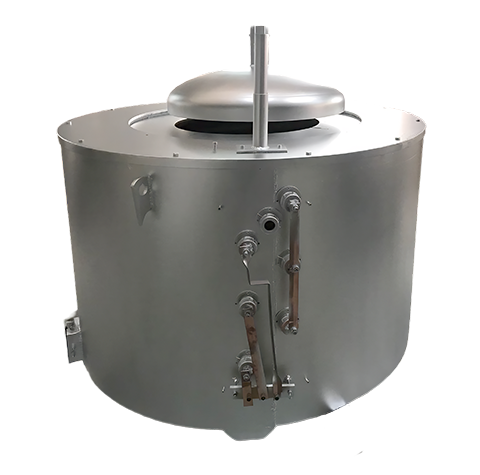
Electric furnace types:
Die casting electric furnaces include electromagnetic induction furnaces, resistance furnaces, crucible furnaces, etc. These electric furnaces can be used for melting and insulation of various materials such as aluminum alloys, zinc alloys, copper alloys, etc
Application field:
Die casting electric furnaces are widely used around die-casting machines to melt metal materials such as aluminum ingots and zinc alloy ingots, and maintain them at suitable temperatures for die-casting molding
Energy saving and environmental protection:
Embedded furnace electric heating devices save 30% more electricity than ordinary electric furnaces. In addition, induction heating technology has also been applied in die-casting electric furnaces to improve energy efficiency and reduce environmental pollution
Natural gas furnace
Technical features:
Natural gas furnaces are commonly used for melting and insulating non-ferrous metals such as aluminum alloys. These furnaces can provide a stable high-temperature environment to ensure that metal materials remain liquid during the die-casting process.
Environmental impact:
When using a natural gas furnace for metal melting and insulation, a certain amount of exhaust gas emissions will be generated, including pollutants such as particulate matter, sulfur dioxide (SO2), and nitrogen oxides O (Nx).
In order to reduce the emissions of these pollutants, many factories have installed low nitrogen combustion processors and exhaust pipes to comply with environmental standards
Economic performance:
Compared to traditional gas stoves, natural gas stoves have lower operating costs and higher melting efficiency. It can significantly reduce energy consumption and production costs, and enhance the competitiveness of enterprises.
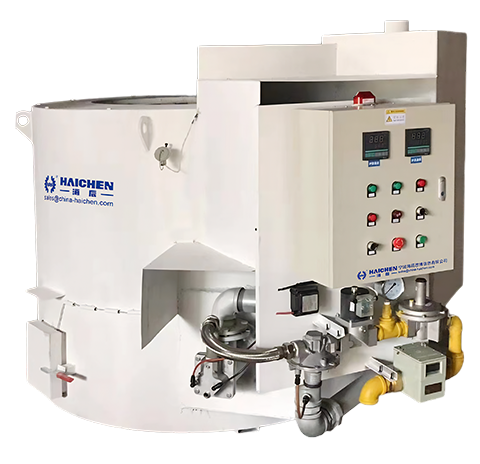
Related articles about furnace

Ceramic melting crucibles for casting
Ceramic melting crucibles for casting are mainly used to hold and melt metal materials. They are widely used in various casting processes due to their high temperature resistance, corrosion resistance and high mechanical strength. Ceramic melting crucibles for casting application The melting crucibles have a wide range of applications in the field of casting, especially in the production of complex