Types of sprayer for die casting machine:
- Robot spray
- Continuous spray
- Manual spray
- Traditional Copper Tube Spray
The design features and functions of different spray types mainly depend on the type of die-casting machine, the complexity of the mold, and production requirements.
Choosing the appropriate spray type and nozzle design can enhance spraying efficiency, reduce defects and improve product quality.
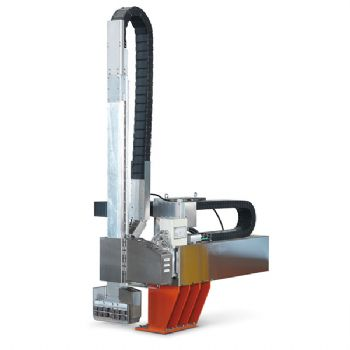
Continuous sprayer
The Continuous spraying system of the die casting machine is an automated release agent spray system used in the die casting process.
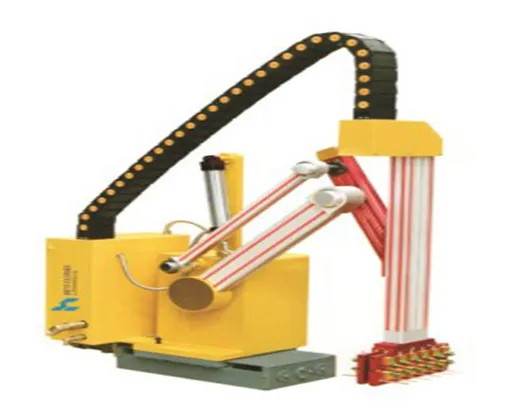
Robot sprayer
The robot spraying system has a variety of modes, which is suitable for the spraying needs of different moulds and products.
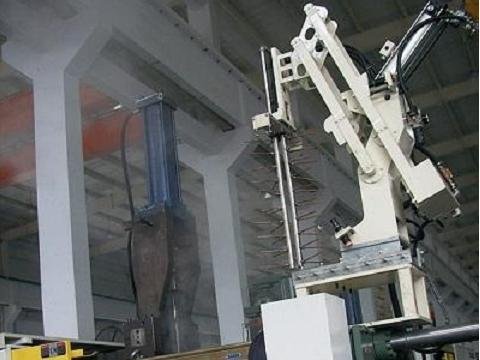
Manual sprayer
Although labor-intensive and unsafe, it is still a common spraying method.
Traditional Copper Tube Sprayer
This method is sprayed through multiple groups of copper tubes, but it is prone to uneven flow problems.
There are four main types of die casting machine sprays: servo-mechanism spray, robotic spray, manual spray, and traditional copper tube spray.
Working principle of sprayer for die casting machine
- Cooling and lubrication
- Mechanical linkage principle
- Automatic control
- Spray types and applications
- Environmental protection and energy saving
Cooling and lubrication
In the die casting process, the mold temperature is usually very high.
In order to prevent the mold from being damaged due to high temperature or causing defects in the casting.
The spray system achieves rapid cooling by spraying coolant (such as water or coolant) onto the mold surface.
Mechanical linkage principle
The spraying device usually extends into the mold cavity through the mechanical linkage principle for spraying operation.
This allows for uniform coverage of the mold cavity, ensures that the release agent adheres effectively to the mold surface, and the position and angle of the spray can be adjusted as needed.
Automatic control
Modern die casting spray systems usually adopt automatic control technology, and adjust the parameters such as spray time, pressure and flow through PLC control system to adapt to different production needs.
In addition, robotic spraying systems are becoming more common, which can automatically complete spraying tasks according to a set program, improving production efficiency and product quality.
Spray types and applications
There are many types of spray systems, including continuous spray systems, batch spray systems, automated lubrication systems, and manual lubrication systems.
Each system has its own unique application scenarios and advantages.
Such as continuous spray systems for large-scale production, while manual lubrication systems for small batch production.
Environmental protection and energy saving
The new spray system also focuses on environmental protection and energy saving, such as the Minimum Spray System (MMS).
Which reduces water consumption and wastewater treatment costs by spraying concentrated release agents in small doses, while extending mold life and reducing energy and compressed air consumption.
And spray it evenly to the surface of the mold through the nozzle to achieve the purpose of rapid cooling, lubrication and demoulding.
In addition, modern spray systems combine automatic control and environmentally friendly and energy-saving technologies to further improve production efficiency and product quality.
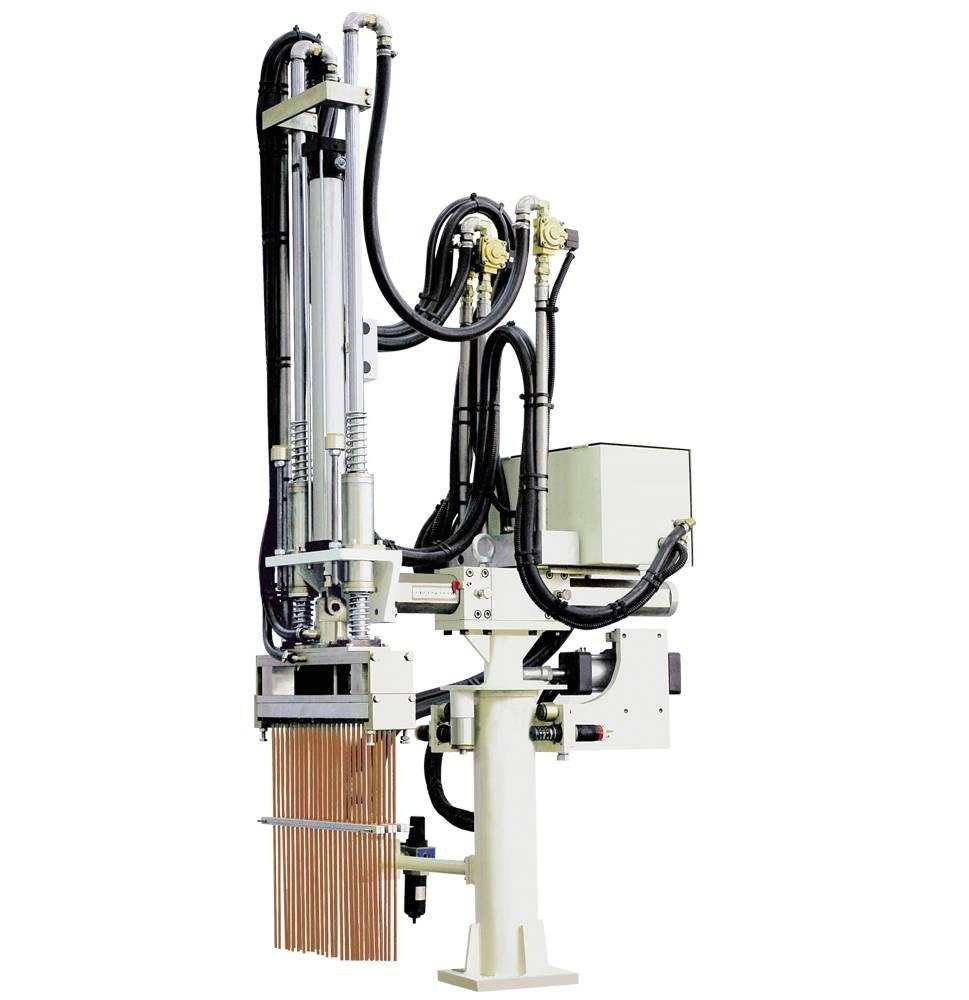
Advantages of Sprayer for die casting machine
- Improve mold life
- Improve surface quality
- Reduced scrap rates
- Improve production efficiency
- Cost savings
- Environmental protection
- Flexibility and adaptability
- Safety
Improve mold life
The spray system prevents the mold from overheating by cooling and lubricating the mold, thereby extending the service life of the mold.
Improve surface quality
Spray can effectively reduce the surface defects of castings, improve the qualified rate of finished products, and make the surface of castings smoother.
Reduced scrap rates
By precisely controlling the position and amount of spray, you can ensure that the release agent evenly covers the mold cavity, reducing scrap rates.
Improve production efficiency
The spray system can quickly adjust the spray volume and speed to adapt to the needs of different molds, improve the efficiency of mold change, and reduce production cycle time.
Cost savings
The spray system can reduce the amount of release agent used, reduce production costs, and reduce material waste due to its efficient atomization effect.
Environmental protection
The spray system reduces the pollution to the surrounding environment, while reducing the consumption of water resources and the need for wastewater treatment through optimized design.
Flexibility and adaptability
The spraying system can be adjusted according to different production needs, adapt to the production of diversified die-casting products, and improve the use efficiency.
Safety
The spray system works in a high-temperature, corrosive gas environment.
Which can replace manual operation, improve the working environment, and improve worker safety.
In a word, the spray system of die casting machine has significant advantages in improving product quality, prolonging mold life.
Reducing production costs and environmental protection, and is an indispensable and important equipment in modern die casting production.

Release agent used for Sprayer
- Water-based release agents
- Oil-based release agents
- Environmentally-friendly release agent
Water-based release agents
The main ingredients include modified silicone oil, organic aliphatic esters, emulsifiers, oxidized waxes, water, etc.
Other ingredients may include polymer waxes, synthetic oils, additives, etc.
These release agents produce volatile organic compounds (VOCs) such as non-methane total hydrocarbons at high temperatures.
Oil-based release agents
The main ingredients include polymer additives, synthetic oils, polyolefins, organic amines, defoamers, biocides, etc.
These release agents produce soot and organic off-gases at high temperatures.
Environmentally-friendly release agent
Use water-based environmentally friendly release agent, used at room temperature, no exhaust gas generated.
Can be recycled through the release agent recovery machine, and add a certain proportion of fresh stock solution for recycling.
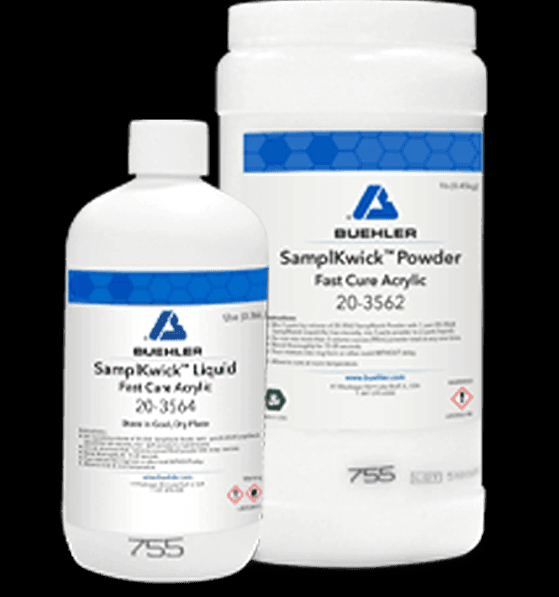
The role of Release agent used for Sprayer
- Effect on Mould
- Effect on Casting quality
Effect on Mould
The amount of release agent sprayed needs to be well controlled.
Otherwise it may cause a sharp drop in mold temperature, which can cause mold cracking or cracking.
The use of a thermally stable release agent can prevent the release agent from carbonizing.
And scaling at high temperatures, thereby extending the life of the mold.
Effect on Casting quality
The spraying of the release agent not only helps the casting to release smoothly
But also plays a certain cooling role to avoid defects caused by the high temperature of the mold.
There are many different types of coolants and release agents used in die casting machine spray systems.
And their composition and use have a significant impact on the quality of molds and castings.
Haichen’s sprayer application
Haichen die-casting machines use servo sprayers in the spraying technology.
- reduce material waste
- independently control
Independently control
Which can independently control the spray position and flow rate.
Especially for customers who need efficient spraying of special-shaped moulds.
Haichen adopts a special copy sprayer to reduce redundant actions and increase the number of nozzles.
Reduce material waste
In addition, servo spray systems reduce material waste and environmental impact, while improving the quality of the finished product.
The robotic spraying system has shown significant advantages in Haichen’s die-casting production.
The effect of improving the qualified rate of finished products
And reducing the labor cost of on-site mould maintenance for customers.
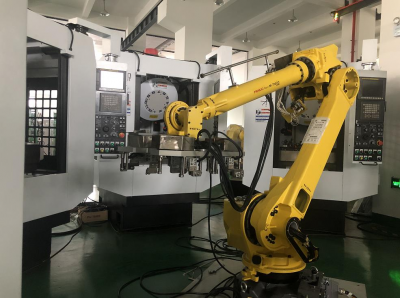