An extractor for die casting machine is a type of automated equipment.
It automatically removes moulded castings during the die casting production process.
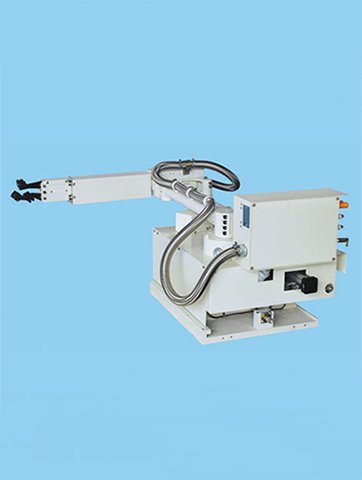
1 Such equipment typically includes manipulators or robots that can accurately grasp.
Carry and stack castings from the die casting machine to improve productivity and reduce labour intensity.
2 The design and application of die casting machine pickups involves a variety of technologies and structures.
For example, some extractor use a four-link mechanism and a servo motor as the driving element.
lifting and lowering is achieved by worm gear and screw mechanism.
While the extension and extraction of the hand claw is controlled by a linear module.
There are also designs that use double-armed manipulators.
Which combined with spray functions, to adapt to the needs of different types of moulds and improve the level of automation and intelligence.
3. The application of this extractor is not only just to do a single pick-up action, but also includes and die casting machine other functions such as spray, cooling, etc.
Integration, the formation of an integrated production line, further enhance the production efficiency and product quality.
Die casting machine extractor is an indispensable part of modern die casting production line.
It through a high degree of automation and intelligent design, effectively solve the manual pickup of labour intensity, low efficiency problems.
While ensuring the safety and continuity of the production process.
Specific types of Extractor for die casting machines
There are various types of die casting machine extractors (Extractor), which are mainly classified according to their structure and function.
Several common types of die casting machine extractor for:
1.Manipulator equipment
2.Two-axis three-axis extractor
3.Hot room machine die casting automatic extractor
4.Traverse cantilever automatic extractor
1. Manipulator equipment:
This kind of extractor is usually used in automated production line, can efficiently complete the die casting parts pickup work.
For example, like five linkage extractor, six joint degree die casting robot load 50KG die casting pickup robot.
And an Aluminium die casting machine with automation extractor and so on.
2. Two axis three axis extractor:
This kind of extractor is usually used for specific die casting process, has high flexibility and adaptability. For example, Haichen custom zinc alloy die casting special two-axis three-axis extractor.
3. Hot room machine die casting automatic extractor:
This kind of extractor is suitable for hot room die casting process, can effectively deal with high temperature die casting.
4.Traverse type cantilever automatic extractor:
This type of extractor is usually used in need of long-distance movement occasions, suitable for large-scale die casting pickup work.
The main design technology and structure of the Extractor for die casting machine

The design technology and structure of the die-casting machine extractor has five main aspects:
1.Extractor Mechanical structure design
2. Extractor Control system design
3. Extractor Software simulation and optimisation
4.Extractor Intelligent and automation design
5. Extractor Parametric design and document management
1.Extractor Mechanical structure design:
the design of die-casting pickup robot usually adopts linkage mechanism, servo motor drive, worm gear and screw mechanism to achieve accurate positioning and control.
For example, the linkage type servo pickup robot adopts four linkage mechanism, the movement plane is vertical plane, servo motor as the driving element, the lifting part adopts worm gear and spiral mechanism, driven by asynchronous motor.
There is also the use of ellipsometer mechanism trajectory for the lower part of the circle structure of the linkage robot, to achieve the requirements of the horizontal linear motion automatic pickup.
2. Extractor Control system design:
die-casting pickup robot control system design is usually based on PLC (programmable logic controller), combined with multiple servo motors to establish a digital Cartesian coordinate system.
Through the PLC’s A/D module and temperature sensor communication, acquisition and monitoring of the temperature of the mould cavity, to achieve the precise control of the robot.
For example, the control system of one-machine dual-arm spray pickup manipulator uses PLC as the main control core, based on multiple servo motors and three-phase AC motors for frequency conversion speed regulation.
The HMI interface is developed through the touch screen to realise the switching between manual and automatic operation, and the setting of working speed and operation mode.
3. Extractor Software simulation and optimization:
In the design process, SolidWorks, ADAMS and other software are used to carry out three-dimensional modeling, kinematic analysis and simulation of the manipulator, as well as kinetic simulation, in order to verify the rationality of the design and optimize the design.
For example, through the ADAMS virtual prototype technology before and after the improvement of die casting machine pickup robot trajectory and acceleration simulation analysis, optimisation of the design of the new pickup robot operating space is compact, clamping trajectory is reasonable, smooth operation.
4.Extractor Intelligent and automation design:
with the development of intelligent manufacturing, die casting pickup robot design tends to higher level of intelligence and automation.
For example, HCD-280C horizontal cold compression chamber die casting machine pick up pieces spray integrated Cartesian coordinate manipulator design.
The use of PLC closed-loop control loop and has a fault code display function, through the control of four AC servo motors to drive the ballscrew sub
5. Extractor Parametric design and document management:
In order to improve the design efficiency and project document management efficiency, die-casting robot inlay pickup robot parametric design and document management system development.
The use of SolidWorks secondary development technology for parametric design, and in the SQL server for the design of data tables, the use of JAVA language compilation and design of document management system software.
The design technology and structure of the die-casting machine extractor covers mechanical structure design, control system design, software simulation and optimization, intelligent and automation design and parametric design and document management, etc., aiming to improve the production efficiency, reduce labour intensity, improve product quality, and realize the automation and intelligence of the die-casting process.
How the Extractor works in the die casting process?
In the die casting process, the work of the extractor (Extractor) is mainly to cooperate with the automated production of various types of die casting machine, its content involves the following five steps:
1. Extractor Detect the state of the mould
2. Take out the casting
3.Extractor Place the casting
4. Extractor Integrity check
5.Cooling and slag package
1. Extractor Detecting the mould condition:
Firstly, the extractor confirms the condition of the mould by means of sensors or other detection devices.
Ensure that the mould has been fully opened and that the die casting has cooled to a state where it is safe to remove.
2. Extractor Take out the casting:
When confirming the mould state is normal, the extractor starts to move.
Typically, the extractor uses multi-joint robotics to remove the casting from the mould by means of robotic arms, suction cups or grippers.
For different shapes and sizes of castings, the extractor can use different clamping methods, such as three-jaw chuck, cylinder rod clamping mechanism.
3. Extractor Placement of castings:
After removing the castings, the extractor will place the castings on the conveyor belt or in a designated location.
Some extractors can also be linked with subsequent post-processing equipment (e.g., trimming machines) to directly feed the casting into the post-processing equipment for further processing.
4.Extractor Integrity Check:
Prior to placing the casting, the extractor will typically perform a casting integrity check to ensure that there are no small pieces or other defects remaining.
This step can be accomplished with equipment such as an opposing photoelectric switch.
5. Cooling and de-slagging:
In some cases, the extractor also performs air or water cooling to further reduce the temperature of the casting and remove unwanted parts such as slag packs and venting channels.
The whole process is automatical and requires no human intervention, greatly improving productivity and safety.
Haichen specialises in providing die casting machines Extractor
As we can see, the Extractor of the die casting machine plays a crucial role in the die casting process. Haichen, as a company that has been deeply working in the field of die casting equipment for many years.
Has accumulated a number of examples on the design and improvement of the die casting machine and its extractor.
Haichen adopts the advanced mechanical design theory and design method, combining with the motion principle of the linkage mechanism to select the suitable structure of the hand, wrist, arm and body, and design and calculate the structure of each component.
This shows that when we design the take-out mechanism, we need to consider the rationality and functionality of Extractor mechanical structure.
We also combined the design of the secondary ejector mechanism and the unloading plate push tube to push out the die casting mould twice.
To improve the taking out efficiency and to solve the problem of difficult to take out the mould of complex shell die castings.
These designs achieve a more efficient take-out process by increasing the complexity of the mechanical structure, while also solving the problem of workpiece deformation.
Haichen die casting machine acceptance and commissioning attention to detail.
For example, checking the quality of the paint on the surface of the die casting machine and the setup of the oil collector discs are also key factors.
These details helping ensure the overall performance of the die casting machine and the reliability of the take-out mechanism.
Haichen has full experience of die casting machine Extractor.
Which includes all aspects from design and manufacture to commissioning and maintenance. Through continuous technical improvement and practical accumulation, we are able to provide efficient and reliable die casting machine take-out solutions.