In die casting, mold installation and maintenance means that the mold must be installed accurately to ensure alignment and sealing.
Die casting is an accurate, fast method of manufacturing that creates the intricately detailed metal components.
Die maintenance and installation play a crucial role in maintaining productivity and effectiveness in terms of die longevity. Periodic upkeep prevents errors alongside prolonging service life while proper mounting maintains exact positioning and maximizes blend efficiency.
Following set guidelines can enhance productivity whilst managing costs effectively Within this post, we would like to explore further the concepts of installation technology, techniques, and procedure maintenance employing production case studies.
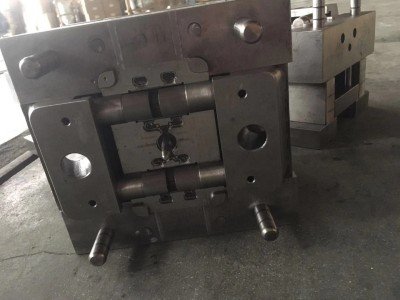
Basic process flow of die casting molds
Die casting molds utilise the injection of liquid metal into the mold cavity at high pressure to achieve rapid solidification and molding of the metal. When it comes to the design of moulds, there are a number of factors to take into consideration. These include material selection, the cooling and exhaust systems, and the strength of the mould structure. The purpose of this is to ensure the quality of the cast product and the longevity of the mould.
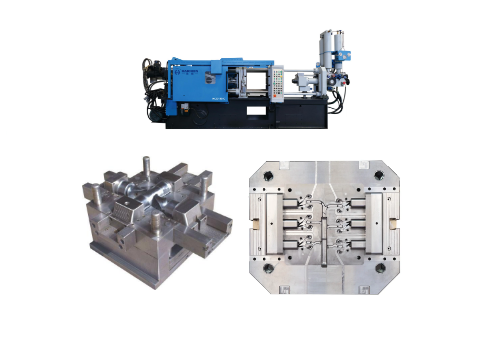
Installation of die casting molds
The installation process of die-casting molds is a precise and meticulous process. As a die-casting machine manufacturer, we can assure you that it is crucial to ensure that the mold is correctly positioned and securely fixed in the die-casting machine. This can achieve the best performance and safety of die-casting molds.
- Preparation
- Alignment
- Fixing
- Temperature control
- Test run
Preparation
Before installing the mold, workers must thoroughly clean the surface of the mold and die-casting machine. Any debris that may affect mold alignment or cause casting defects needs to be removed.
- Check mold size: Before installation, please carefully check the mold size to ensure it meets the specifications of the die-casting machine. Small differences in mold size may lead to improper positioning, which may cause damage to the mold and machine.
- Cleaning molds and machines: Next, it is necessary to remove dust, grease, and any other foreign objects from the installation surfaces of the molds and machines. It should be noted that a clean environment is crucial for preventing pollution and ensuring safe installation. Once, we encountered a situation where a small piece of metal fragment on the installation surface caused uneven mold installation, resulting in uneven metal flow and casting defects. So you must remember.
Alignment
It is vital that the mould is correctly aligned with the injection axis of the die casting machine. This ensures that the molten metal is evenly distributed within the mould cavity.
- Use Proper Lifting Equipment:Moulds can be heavy and delicate, so it is essential to take the necessary precautions when handling them. It is essential to utilise appropriate lifting equipment to handle the mold safely. In a recent production run for a large industrial pump casing, we utilised a crane equipped with state-of-the-art mold handling attachments. This enabled us to accurately lift and position the mold without causing any damage.
- Align the Mold with the Machine:This alignment is critical for the mold to close correctly and maintain the required tolerances. In a case involving the production of precision aerospace parts, even a millimetre misalignment could have led to dimensional inaccuracies in the final product.
Mounting & Securing
After alignment, securely fasten the mold to the machine using clamps or locking mechanisms. Ensure proper tightness to prevent movement during high-pressure injection.
Key Steps:
- Even Clamping Force – Once positioned, engage the machine’s clamping system and tighten evenly to avoid uneven stress distribution. Example: During mass production of electronic housings, precise clamping force adjustment prevented mold warpage.
- Closing Verification – Perform a dry-run closure check to confirm proper alignment without gaps. Case Study: Early detection of micron-level misalignment in jewelry production avoided batch defects.
Temperature Management
Adjust mold temperature per material specifications, typically using integrated heating/cooling channels. Best practices:
- Conduct thermal balance tests for new molds
- Maintain temperature parameter logs
Test Run
Execute trial shots to verify:
- Leak-free sealing
- Complete cavity filling
- Proper ejection system operation
Document any issues and adjust accordingly. Recommendation: Keep first-off samples as quality benchmarks.
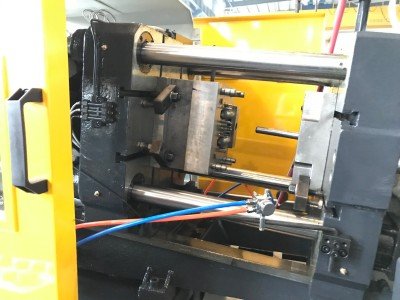
Maintenance of Die Casting Dies
Regular maintenance is essential for the longevity and consistent performance of die casting dies.
- Regular Cleaning
- Inspection and Repair
- Lubrication and Coating
Regular Cleaning
- Removing Residual Metal and Shards of over production units: During every shift or cycle of production, it is necessary to clean the mold from residual aluminum alloys, flashes, or any other dirt. This avoids spoilage of quality for the next castings. For example, in a continuous production line for bicycle frame components, regular cleaning of the mold ensured consistent surface finish and dimensional accuracy.
- Cleaning Agents Must Not Be Corrosive:Every product needs to have different sorts of chemicals while being cleaned up. Avoid Harsh Chemicals which may result in damage on surface parts of mold. In relation to an issue in casting medical equipment portions, we used a mild non corrosive cleaning agent in order to preserve residue free while keeping the devoid walls intact.
Inspection and Repair
- Examine For Surface Flaws :Make it a routine to check the surface of the mold for wear, cracks, or erosion as they may cause casting defects. While performing an inspection for automotive brake components molds, we found a small crack which if unchecked would have increased in size causing damages. Timely repairs made sure no unnecessary complications arose.
- Repair Mold Surfaces Flawingly Casted Parts: All surfaced flaws must be fixed effectively to maximize functionality. Restore parts that have been damaged through welding, grinding and polishing. Efficient repairs allowed us retain precision while casting heavy machinery parts through expedient repair of worn areas in the mold cavity surface.
Lubrication and Coating
- Lubrication and Coating Apply Mold Release Agent: Apply a suitable mold release agent to the surface of the mold before every production cycle. This assists in smooth ejection of the castings, thus minimizing wear on the mold. During a production run for plastic toy parts, the application of a suitable mold release agent minimized risk of sticking and assisted in complete casting ejection from molds without issues.
- Maintain Coating Integrity: If a special coating is given to the mold like non-stick or wear-resistant coating, ensure that it is preserved properly. Reapply coatings as necessary to enhance performance and prolong functional life of the tool. In one case concerning casting processes for high-temperature alloys using specialized molds, preserved coating integrity allowed seamless exposure to extreme temperatures reducing repair needs significantly.
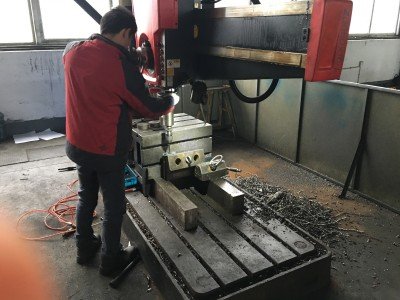
Importance of mold maintenance
1.Maximizing Mold Lifespan
- Regular maintenance preserves mold integrity
- Prevents premature wear and damage
- Significantly reduces unplanned downtime
2. Ensuring Consistent Product Quality
- Maintains precise dimensional accuracy
- Delivers superior surface finish
- Minimizes casting defects and scrap rates
3. Optimizing Production Economics
- Lowers emergency repair costs
- Reduces mold replacement frequency
- Enhances overall equipment effectiveness
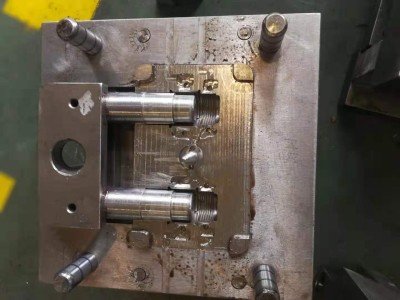
Die casting molds will be more effective and last longer when users abide by these installation and maintenance practices.
HAICHEN, as a die casting machine designer and manufacturer, pays great attention to high-quality mold solution provision. We assist our clients in improving productivity and product quality while ensuring sustainable operations through proper mold installation and systematic maintenance. For in-depth assistance on accurate mold installation and maintenance procedures, we encourage you to reach out to the HAICHEN technical support team.
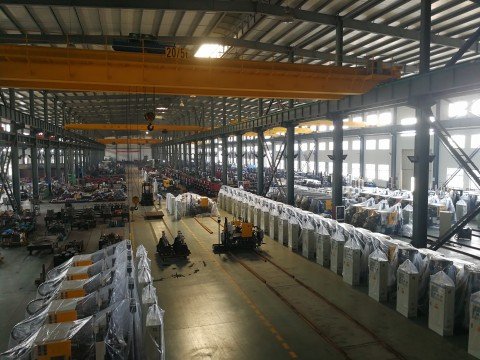