Die casting steps are manufacturing process in which molten metal injecting into a metal mould cavity under high pressure.
Causing it to solidify and take shape rapidly.
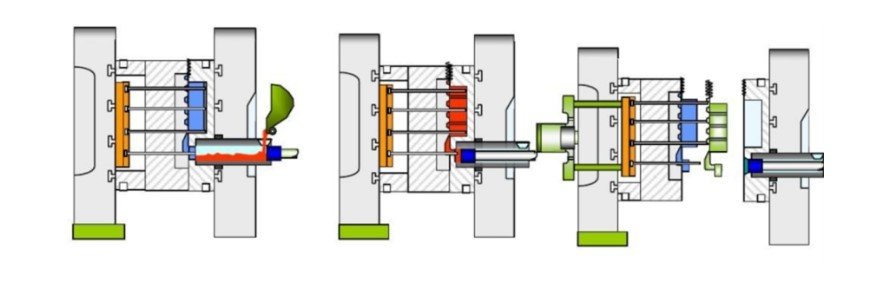
The steps of die casting summarise in the following main stages:
1. Mould testing and preparation.
2. Preparation of molten metal
3 Injection of molten metal
4 Cooling and solidification
5. Opening the mould and removing the casting
6.Post-treatment
7.Heat treatment
1. Mould testing and preparation:
First need to test the die-casting mould is in good condition.
And spray lubricant in the mould cavity, reduce friction and improve product quality.
2. Preparation of molten metal:
Selecting the right material and melting it into a molten state.
This step may include melting the metal material in a furnace, stirring the molten metal and adding metal solvents during the stirring process.
3. Injection of molten metal:
The molten metal injecting into the mould cavity through the injection head.
This step can be carried out in different ways.
For example by using vacuum technology to prevent oxidisation.
By controlling the flow and filling of the molten metal through a specific injection system design.
4. Cooling and curing:
The molten metal is cooling in the mould cavity.
This step may involve the design of the mould’s cooling system to ensure that the molten metal solidifies evenly and quickly.
5. Mould Opening and Removal of Castings:
When the molten metal is fully cured, the mould will open and the castings are removed.
This step may require the use of a pusher or other mechanical device to assist in the removal of the casting.
6. Post-treatment:
The removed castings may require further treatment such as deburring, cleaning, finishing, etc. to improve the quality and surface finish of the castings.
7. Heat treatment:
In order to improve the mechanical properties and corrosion resistance of the castings, the castings sometimes need to heat treat.
These steps outline the basic flow of the die casting process, but specific operational details may vary depending on different materials, product design and production requirements.
How to prepare molten metal for die casting
The process of preparing molten metal for die casting involves a number of steps.
Including metal selection, melting, handling, and safety measures.
1. Selection of suitable metal materials
2. Melting process
3. Handling of molten metal
4. Safety measures
5. Quality control
1.Selection of suitable metal materials: according to the requirements of die casting to select suitable metal materials. Common die casting materials include aluminium, copper and magnesium.
For example, magnesium alloy is widely using in the automotive industry due to its lightweight property.
2. Melting process:
the selected metal material is heated above the melting point to form a molten state.
For example, copper alloys are usually melted in an oxidising atmosphere to avoid the absorption of hydrogen.
3. Treatment of the molten metal:
During the melting process, alloying elements may need to be added or deoxidised to improve the properties of the metal and reduce defects.
For example, in zinc alloy die casting, understanding and managing the characteristics of the slag can significantly reduce production costs.
4. safety measures: due to the high temperature and flammability of molten metal, must take strict safety measures.
Magnesium alloys, for example, are prone to oxidisation and combustion in the molten state and therefore require special attention to safety.
In addition, the use of automated equipment for loading reduces the risk of manual handling and increases safety.
5. Quality control:
In the die casting process, the quality of the molten metal needs to be strictly controlled to ensure the quality of the final product.
This includes monitoring the chemical composition and physical state of the metal, as well as maintaining the proper temperature and pressure during the casting process.
By following these steps, the molten metal used for die casting can be effectively prepared to ensure the production of high quality die castings.
How to open the mould and take out the casting in die casting process?
Die casting process of opening the mould and taking out the casting is a complex and critical step, involving a number of technical and mechanical design details are mainly:
1. Open mould process:
2. Remove castings:
3. Automation and efficiency improvement:
1. Mould opening process:
After the die casting machine has finished injecting the liquid metal.
The mould needs to be separated either hydraulically or mechanically.
This is usually achieved through the die casting machine’s die opening and closing system.
Which can quickly and accurately control the opening and closing of the die.
When the die is opened, the moving and fixed dies of the die are separated, allowing the formed casting to be removed from the die.
This process may require the use of specific mechanisms to assist in the opening of the mould, such as the rapid mould opening and closing spreading system.
which achieves fast and stable opening and closing action by means of an alloy steel seat and a curved elbow spreading mechanism.
2. Removing the casting:
Removal of castings usually involves the design of mould release mechanisms. These can be simple actuators or more complex tilting slides, flap type unloading devices or other automated equipment.
For castings with complex shapes or internal structures, it may be necessary to use a secondary ejector mechanism or a mould design with a self-locking push-out mechanism to ensure that the casting is removed from the mould smoothly and completely.
In some cases, in order to reduce the adhesion between the casting and the mould, a release agent may be applied to the mould surface, or special starting slopes may be designed to help the casting separate more easily from the mould.
3. Automation and efficiency improvement:
With the development of technology, more and more die casting process began to use automation equipment to improve production efficiency and reduce manual operation.
For example, the use of robots to automatically remove castings can significantly improve the speed and safety of the production line.
In addition, through the optimisation of mould design and die casting process parameters, can further improve the quality of castings and production efficiency.
Die casting process of opening mould and taking out castings is a comprehensive process involving a variety of technologies and equipment.
By reasonably designing moulds and selecting suitable die-casting machines and their accessories, production efficiency and casting quality can be effectively improved.
Importance of die casting post-treatment process
Die casting after treatment process in the manufacturing process of die casting has a vital role:
1. Improve the surface quality and mechanical properties
2. Improve the internal organisation performance
3. Enhance the reliability and safety of the product
4.To meet specific customer requirements
5. Optimising production costs
1. Improve the surface quality and mechanical properties:
Die casting in the moulding often exists burr, oxide skin and other defects, these defects will affect the appearance of the product and the use of performance.
Through deburring, shot blasting, vibration grinding and other surface treatment processes, can significantly improve the surface finish of die castings, to meet the technical requirements of customers.
In addition, surface treatment can also increase the fatigue strength of die casting, prolong its service life.
2. Improve the internal organisation performance:
Die casting in the rapid cooling process, the internal grain structure may not be uniform, affecting its mechanical properties.
Through heat treatment process, such as solid solution treatment and aging treatment, can change the metallographic organisation of die casting, remove internal stress, so as to enhance the mechanical properties and dimensional stability of the product.
3. Enhance the reliability and safety of the product:
Post-treatment process not only affects the surface quality and mechanical properties of the die casting, but also directly determines the reliability and safety of the final product.
For example, through the infiltration treatment can improve the airtightness of the die casting, suitable for applications that require high sealing.
4. To meet specific customer requirements:
Different customers and application scenarios have different requirements for die castings.
The post-treatment process can be customised according to customer requirements, such as electroplating, chemical conversion of the skin film, etc., in order to meet specific functional requirements.
For example, in zinc alloy die castings, passivation can significantly improve corrosion resistance and extend service life.
5. Optimise production costs:
Although post-treatment processes can increase production costs to a certain extent, cost savings can be achieved by optimising production routes and process control. For example, early scrapping can avoid wasting finishing time, thus reducing overall production costs.
Die casting after-treatment process plays a vital role in improving product quality, meeting customer needs, ensuring product reliability and safety. Therefore, in the die casting production process, it is necessary to pay attention to and optimise the post-treatment process to ensure the performance and market competitiveness of the final product.
Haichen die casting machine can provide you with perfect die casting steps
Haichen’s die casting machine can provide the perfect solution for your die casting steps.
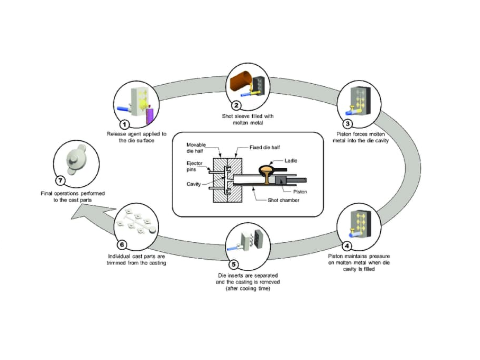
Haichen die casting machine adopts international advanced injection technology and full-automatic operation, which can ensure smooth pressure and low impact, thus improving the quality of castings.
In addition, our die casting machines can running high speed injection and stable energy saving, which can meet different production requirements.
Haichen die casting machine with high degree of automation.
With the development of automation technology, our die casting machine has achieved a high degree of automation.
In addition, we have also adopted robots to replace manual labour, further enhancing operational efficiency and market competitiveness.
Haichen’s die casting machine is applicable to a wide range: our die casting machine is suitable for die casting of a wide range of materials, including but not limited to aluminium, zinc, copper and other non-ferrous alloys.
Whether it is mass production or medium or large volume production mode, our die casting machines can meet the needs of different industrial sectors.
Haichen die casting machine focuses on environmental protection and safety: in the design and manufacturing process, we fully consider environmental protection and safety factors.
For example, by reducing noise and pollution and adopting measures such as automatic spraying device and automatic lubrication device, we ensure the environmental protection and safety of the production process.
Haichen’s continuous technological innovation: We constantly introduce and develop new technologies to meet the needs of the market and customers.
For example, our die-casting machines steps adopt advanced hydraulic feedback control system and PLC programmable control, which ensures high reliability and easy operation of the equipment.
while focusing on environmental protection and safety, and continuous technological innovation, it is fully capable of providing perfect solutions for your die casting process.