The best die casting temperature depends on a number of factors.
including the type of alloy, the mould material, and the quality of the casting required.
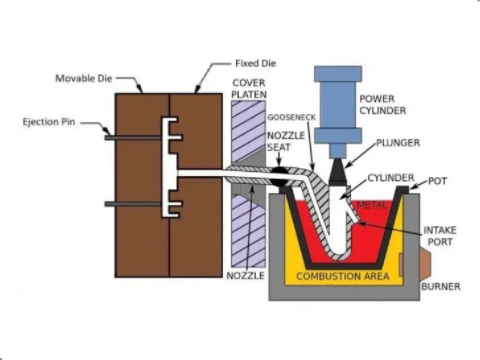
1.For high-pressure die casting of A380 alloys.
Studies have shown that the appropriate mould temperature should be above 200°C. In particular, for parts with complex geometries, such as trapezoidal frames for motor motors.
The best mould temperature better to be between 210°C and 215°C to minimise defects and maximise the production of defect-free parts.
2.For ADC12 aluminium alloy
The best die temperature is 150°C under super slow speed (SSS) die casting conditions.
Which helps to improve the microstructure and mechanical properties of the castings.
However, for the die casting of piston products, the best mould temperature should to be 320°C,
Because at this temperature, although shrinkage defects can occur, these can be within acceptable limits.
3.In addition, for the die casting of ferrous alloys
The best mould temperature ranges from 220°C to 260°C.
For the high-pressure die casting of the magnesium alloys MRI 153M and MRI 230D.
The physical and metallurgical properties as well as the solidification characteristics during HPDC differ from those of the AZ91D alloys due to the presence of specific alloying elements.
The optimisation of the process parameters, such as the melt and mould temperatures as well as the injection profile.
All things considered, the best die casting temperature depends not only on the alloy type, but is also influenced by the mould material, the casting design and the required quality criteria.
Therefore, there is no fixed ‘best’ temperature for all cases.
For example, for A380 alloy, the best mould temperature is between 210°C and 215°C; for ADC12 aluminium alloy.
The best mould temperature is 150°C under SSS conditions; and for ferroalloys, it is between 220°C and 260°C.
The specific alloy type, mould material and casting requirements must calculating into account when determining the best die casting temperature.
Best die casting temperature setting for aluminium products
The best die casting temperature setting for aluminium alloy products depends on a number of factors, including the chemical composition of the aluminium alloy, the structural characteristics of the die casting, and the required mechanical properties.
For different aluminium alloy materials and application scenarios, we recommend different best casting temperatures.
1.For Al-10Si-0.3Mg aluminium alloy
The best casting temperature is 650°C, at which the mechanical properties and thermal conductivity of the alloy are optimal. And for ADC12-0.15V0.03In aluminium alloy case cover, the best casting temperature is 685°C. This shows that even for similar types of aluminium alloys.
The best casting temperature may vary depending on the specific composition of the alloy and the application requirements.
2. For the A356 aluminium alloy clamp body bracket
The best liquid aluminium casting temperature is 630°C, while the best casting temperature for the AlSi9Cu aluminium alloy for automotive use is 700°C.
These data further emphasise that the choice of best casting temperature is dependent on the specific aluminium alloy type and intended application properties.
3.Taken together, although there is no single best casting temperature for all aluminium alloy products, some trends are observe.
For example, for some aluminium alloys, such as Al-10Si-0.3Mg and ADC12-0.15V0.03In, lower casting temperatures (around 650°C to 685°C) seem to provide better mechanical properties and thermal conductivity.
For other aluminium alloys, such as A356 and AlSi9Cu, higher casting temperatures (~630°C to 700°C) may be more appropriate.
Therefore, determining the best die casting temperature for aluminium alloy products requires .
Comprehensive consideration of the specific chemical composition of the aluminium alloy, the expected application properties and the structural characteristics of the die casting.
We recommend to optimise the die casting process parameters through experiments and numerical simulations in actual production to achieve the best production results.
Best temperature setting for zinc alloy hot chamber die casting
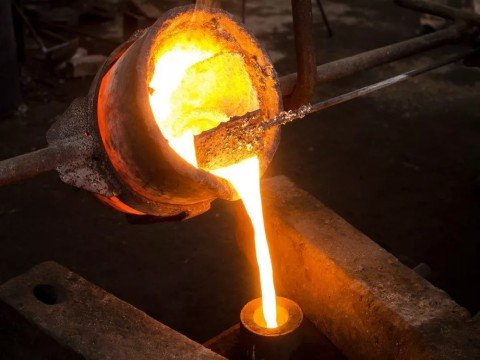
The best temperature setting for hot chamber die casting of zinc alloys requires a combination of factors such as the melting point of the gold, the parameters of the die casting process, and the expected quality of the die casting.
We give three favourable recommendations after a long period of practice:
1.The melting point of zinc alloy is usually around 407.1℃.
Therefore, the pouring temperature of the zinc alloy during the die casting process should be higher than this temperature to ensure that the alloy can fully melting.
2.For ZZnAl4Y zinc alloy, studies have shown that when the casting temperature is 300°C.
The zinc alloy under the melt rapid cooling fusion casting process has the best organisational uniformity and mechanical properties.
This indicates that the setting of the casting temperature is crucial for obtaining high quality die castings in the hot chamber die casting process.
3.The die casting process parameters optimised by numerical simulation include a pouring temperature of 435°C and a mould temperature of 220°C.
This data provides another perspective that the setting of pouring and mould temperatures has a significant impact on reducing defects on die castings (e.g., shrinkage, shrinkage and air rolls) as well as improving the quality of die castings in actual production.
So the best temperature setting for zinc alloy hot chamber die casting should include high pouring temperature (close to or slightly higher than the melting point of the alloy.
And moderate casting temperature (about 300 ℃), in order to ensure that the alloy can be fully melted and obtain good organisation uniformity and mechanical properties.
At the same time, the mould temperature setting should also be optimised according to the specific die casting requirements and process conditions in order to further improve the quality of the die castings.e castings.
Best temperature and safety for magnesium die casting
The best temperature and safety of magnesium alloy die casting involves a number of factors.
Including pouring temperature, injection speed, injection specific pressure, and mould temperature.
We have four suggestions:
1. Melt temperature
2. Injection speed and injection ratio pressure:
3. Mould temperature control
4. Safety
1.Melt temperature:
The recommended pouring temperature varies from study to study, but most studies show that better performance can be obtained with a pouring temperature between 670°C and 730°C.
For example, the best casting temperature for AZ91-SrCe magnesium alloy is 690°C, while the best casting temperature for Mg-8Gd-4Y-0.3Zr-0.3Ti magnesium alloy is 710°C.
This suggests that the best casting temperature may vary for different magnesium alloy compositions.
2.Ejection speed and ejection ratio pressure:
Ejection speed and ejection ratio pressure are also important parameters affecting the die-casting performance of magnesium alloy.
For example, the best ejection speed of magnesium alloy for automobile shell is 200 m/min, and the best ejection ratio pressure is 120 MPa, while for the magnesium alloy for the shell of new machinery.
The best ejection speed is 3 m/s, and the best ejection ratio pressure is 80 MPa.
3.Mould temperature control:
Mould temperature on the performance of magnesium alloy die casting also has a significant impact.
For example, the best mould temperature of AZ91 magnesium alloy is (100±10)℃, while the mould temperature of Mg-xSm-0.3Zn series magnesium alloy ranges from 200 to 280℃.
4.Safety:
Magnesium alloy in the die-casting process there is a risk of oxidation and combustion, so it is necessary to take appropriate protective measures.
For example, the use of air plus a small amount of SF6 atmosphere or CO2 plus a small amount of SF6 atmosphere can effectively protect the molten magnesium alloy from oxidative combustion.
In addition, the development of gas-heated magnesium alloy dosing and melting holding furnaces demonstrates the importance of safety considerations. The best temperature and safety for magnesium alloy die casting depends on the specific alloy composition and desired properties. In general, casting temperatures range from 670°C to 730°C.
Injection speeds and injection ratios need culcalting according to the property requirements of the specific alloy, and mould temperatures are usually lower range to reduce defects. At the same time, appropriate protective measures such as the use of air-insulated lids to cover the molten metal liquid are essential to ensure safety.
Haichen die casting machine’s best temperature control ability
The best die casting temperature control capability of Haichen die casting machine is mainly reflected in the high pressure superheated water mould temperature control device it adopts. This device has multi-channel design, pressure of 0.6 MPa, maximum heating temperature up to 160 ℃, flow rate of 50 L/min. This device has the functions of mould preheating, mould cooling, automatic water replenishment, automatic pressure stabilisation and automatic temperature control.
Specifically, this high-pressure superheated water mould temperature control device can quickly preheat the mould temperature to over 100°C in a short period of time.
Which is about 60°C higher than the traditional oil-type mould thermostat.
At the same time, the heating time for preheating the mould to the same temperature is reduced by about 50% and energy saving is about 40% compared to the oil type mould temperature controller.
These features make the device outstanding in terms of mould preheating efficiency and preheating speed, and it is easy to use, energy-saving and does not pollute the site environment.
In addition, the device has been successfully applied to the production of a complex communication frame die casting, the effect is good, replacing the oil-type mould thermostat.
Therefore, it can be considered that the best temperature control ability of Haichen die casting machine lies in its efficient high pressure superheated water mould temperature control device.
Which can significantly improve the efficiency of mould preheating and energy saving effect.