Die casting machine control system in the modern die casting process plays a vital role.
Its application is wide and versatile.
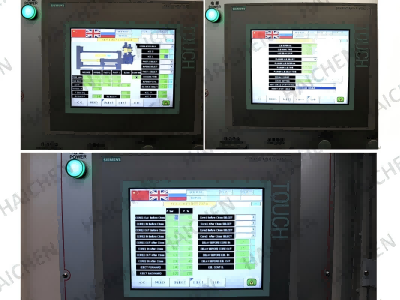
Die casting machine control system detailed applications
Some detailed applications of die casting machine control system are mainly as follows:
- Automated production and remote monitoring
- Process optimisation and quality control
- Fault diagnosis and prediction
- Vacuum-assisted die casting
- Real-time closed-loop control
- Integrated management and data acquisition
Automated production and remote monitoring:
Modern die casting machine is usually equipped with intelligent control system, can realise automated production process and remote monitoring function.
Intelligent control system can make adaptive adjustments according to different product requirements to better ensure product quality and consistency.
It can also real-time monitoring equipment operation status and energy consumption.
Help enterprises better manage equipment resources and reduce production costs.
Process optimisation and quality control:
Through the use of robots, sensors and data analysis technology, automated systems can monitor and control the entire die casting process
From material preparation to finished product handling.
These systems can improve efficiency, quality and safety.
For example, microprocessors can acquire data such as metal velocity.
Fault diagnosis and prediction:
Artificial Intelligence (AI) and Machine Learning (ML) technologies have a promising application in die casting machines.
By applying these technologies to intelligent control, process optimisation, fault diagnosis and prediction, and production management.
It is possible to optimise and manage the die casting production process.
Improve production efficiency and product quality, and reduce production costs.
Vacuum-assisted die-casting:
Multi-directional high-speed real-time control of the vacuum suction system in high-pressure vacuum die-casting has been applied to the production of large-scale complex clutch shell and other parts.
This system almost completely eliminated the aluminium alloy die casting in the porosity and shrinkage hole defects, improve the internal quality of the product and qualified rate.
Real-time closed-loop control:
In the high-pressure die casting process, real-time closed-loop control system is used to monitor and control the flash edge and impact pressure.
So as to improve the benefits of low impact control system.
Integrated management and data collection:
The introduction of smart factory (MES) systems has enabled many small and medium-sized die casting companies to collect facility data and monitor it.
However, due to problems at the manufacturing site, these companies are often unable to fully utilise the data collected and are only able to monitor under what production conditions.
Die casting machine control systems have a wide range of applications in automation, process optimisation, quality control, fault diagnosis, real-time monitoring and data management, etc.
The application of these technologies not only improves production efficiency and product quality, but also reduces production costs and promotes the intelligent development of the die casting industry.
Application of automated production and remote monitoring of die casting machine control system
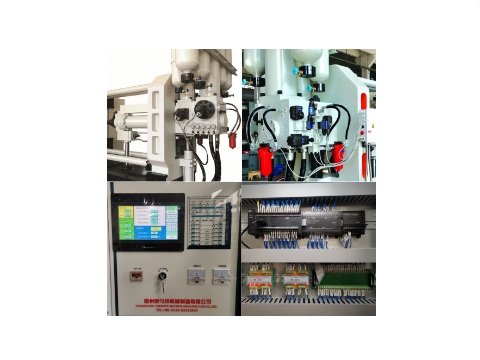
There are five application scenarios for the application of automated production and remote monitoring of die casting machine control systems:
- Automation control
- Remote monitoring and data acquisition
- Intelligent management and analysis
- Remote fault diagnosis and technical support
- System integration and scalability
Automation control
Automation control: modern die casting machine control system by means of closed-loop control, status monitoring and alarm, quality monitoring and process parameters optimisation configuration, significantly improve the die casting equipment automation level and product manufacturing efficiency and quality.
For example, the closed-loop control mode, the product qualification rate of up to 90% or more, through real-time closed-loop control of the pressure, displacement and speed of the die injection process, improve the process consistency and repeatability accuracy.
The system introduced by Haichen is capable of real-time monitoring and controlling various parameters in the production process, such as pressure, speed, process parameters, etc., to achieve quality consistency over a long period of production.
Remote monitoring and data acquisition:
Through industrial Internet and IoT technology, die casting machine can realise remote monitoring and data acquisition.
For example, through OPC and Ethernet technology, the main production control equipment PLC can be real-time remote monitoring, optimise die-casting process, improve casting quality and production efficiency.
The smartphone-based die-casting machine status monitoring system measures air pressure through sensors and transmitters, and stores the data in a cloud database for online real-time data access.
Intelligent management and analysis:
Intelligent die casting control system can not only achieve automatic operation, but also improve production efficiency through data analysis and auxiliary design function.
For example, Haichen system through online setting process parameters, avoiding product quality problems caused by manual setting errors, and realise sales, technology, production and other aspects of automated management.
Intelligent cloud die-casting control system realises real-time monitoring and data collection of the die-casting process by connecting the die-casting machine.
The cloud server and the control unit, and connecting it to the mobile phone APP through industrial internet.
Remote fault diagnosis and technical support:
Some systems also have remote fault diagnosis and technical support functions.
For example, Haichen’s die casting machine control system provides remote troubleshooting function to help solve production problems and improve production efficiency.
The controller supports remote management, allowing managers to communicate remotely with operators through smart devices.
System integration and scalability:
modern die casting control systems usually need to be interconnected with other management systems (such as MES or ERP) in order to achieve unified management of the entire smart factory.
For example, intelligent die casting unit management system needs to be dispersed within the unit of a variety of peripheral equipment data integration into a central system to achieve prospective control.
HCD series cold room die casting machine with networking monitoring function, can be connected through the network on the die casting machine parameters and production process parameters real-time monitoring.
Die casting machine control system automated production and remote monitoring application through a variety of technical means to achieve the production process of efficient, intelligent and standardised management, significantly improve the production efficiency and product quality.
Die casting machine control system how to do fault diagnosis and prediction
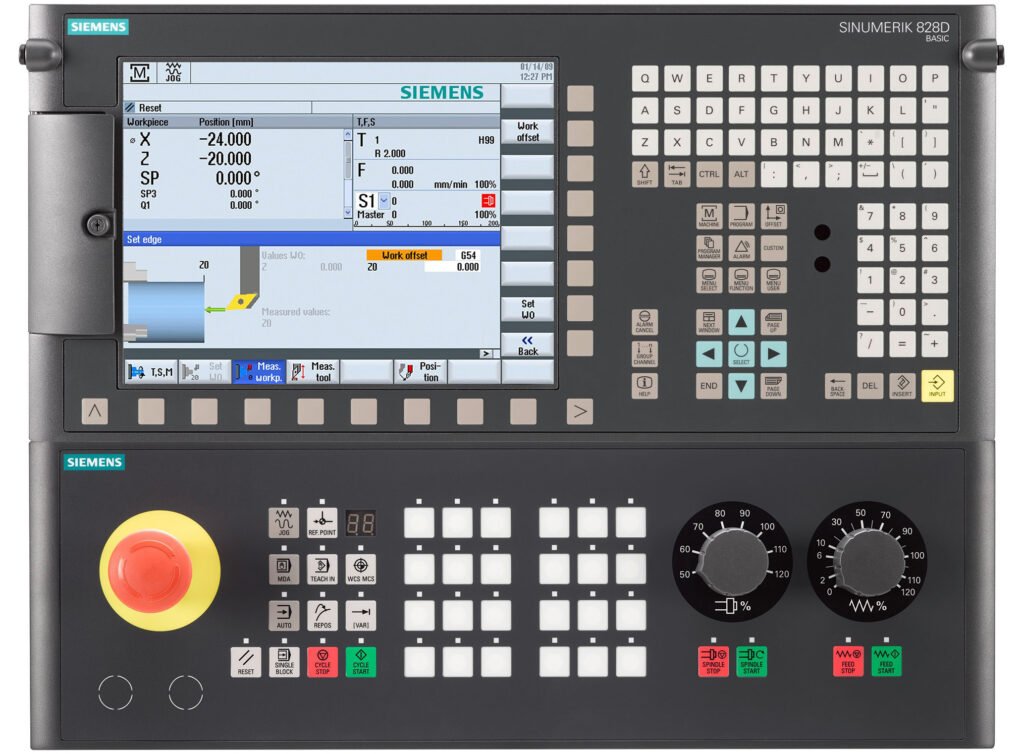
Fault diagnosis and prediction of die casting machine control system mainly relies on the comprehensive application of advanced control theory, neural network technology, industrial Internet technology and real-time monitoring technology.
These are six more advanced technology methods:
- Fault diagnosis method based on RBF neural network
- Hydraulic system fault diagnosis based on FARX and RBFNN model
- Application of industrial Internet technology
- Real-time control system design
- Application of intelligent management system
- PLC redundant control technology
Fault diagnosis method based on RBF neural network:
By establishing a radial basis function neural network (RBFNN)-based control system sensor fault diagnosis observer model, the fuzzy K-mean clustering algorithm is used to select the clustering centre, determine the residual difference between the sensor output value and the actual output value, and thus determine whether the sensor is faulty.
This method has strong nonlinear processing and arbitrary function approximation ability, high prediction accuracy, short learning time, fast network computing speed, stable performance, and can meet the requirements of sensor fault diagnosis.
Hydraulic system fault diagnosis based on FARX and RBFNN model:
Through the blurring of the ARX model to retain its autoregressive coefficient of the change law of the fault state to reflect the very sensitive characteristics, and can achieve a more accurate description of the nonlinear fault characteristics.
In the fault diagnosis, the FARX model is firstly established for the fault state of the target system, and the fault characteristics are extracted as the training samples of the RBF network, and the fault types are determined according to the output results of the RBF network.
The application of industrial Internet technology:
Through the application of industrial Internet technology in die-casting machine, the remote monitoring technology of die-casting machine is realised, and the working status and fault of die-casting machine can be monitored online.
The application of this technology improves the efficiency and service quality of die-casting machine maintenance and reduces the after-sales service cost of equipment manufacturers.
Real-time control system design:
The use of ARM or DSP as the control core of the real-time control system, through the adaptive fuzzy PID control strategy on the pressure injection accumulator and booster electro-hydraulic proportional valve corrective control.
Complete the closed-loop control and real-time monitoring of parameters such as injection speed and boost pressure.
This design improves the automatic control level of die casting machine, and provides technical support for improving the quality of die castings.
Intelligent management system application:
Die-casting unit intelligent management system (Smart Cell Management, SCM) can be all the equipment in the unit data acquisition and processing, diagnosis and solve all kinds of unexpected downtime.
Based on data analysis and advanced algorithms, can predict the potential failure of downtime, to improve the unit’s operating efficiency.
PLC redundant control technology:
the use of dual-CPU redundant control mode and PID control mode improves the reliability and accuracy of the control system.
The application of this technology ensures the stability and reliability of the die casting machine in the production process.
Fault diagnosis and prediction of die-casting machine control system by combining neural network technology, industrial Internet technology, real-time monitoring technology and intelligent management system and many other advanced technologies, realising the real-time monitoring of the working state of die-casting machine, accurate diagnosis of faults and the prediction of potential faults, so as to improve the degree of automation of the die-casting machine, the production efficiency and product quality.
Haichen Advanced Applications for Die Casting Machine Control Systems
Haichen die casting machine control system advanced application for our die casting machine production to provide full technical support, is our customers’ production of the biggest help.
We focus on five aspects of control system applications:
- Application of real-time control technology
- Intelligent level enhancement
- Application of fuzzy PID control strategy
- Application of full closed-loop real-time control technology
- Development of high vacuum control system
The application of real-time control technology:
Through the use of embedded soft PLC control system, the real-time control of die-casting machine ejection process is realised.
The response speed of die-casting machine control system is improved, which has an important application value to ensure the quality of die-casting production.
Our ARM-based die-casting machine control system, through the embedded real-time operating system μC/OS-Ⅱ transplantation
Ensure the real-time nature of the whole system, realising the real-time control and monitoring of the die-casting process.
Intelligent level enhancement:
The study of open control technology based on PC-Control platform provides a friendly man-machine interface.
Can improves the running speed of the system, and enhances the functional expandability.
Application of fuzzy PID control strategy:
Adaptive fuzzy PID control strategy is used to correctively control the electro-hydraulic proportional valve of the pressure injection accumulator and booster。
This to complete the closed-loop control and real-time monitoring of parameters such as injection speed and booster pressure, and to improve the level of automatic control of the die-casting machine.
The application of full closed-loop real-time control technology:
Cold chamber die casting machine ejection system of the whole process of closed-loop real-time control technology application.
The development of high vacuum control system:
For the application of high vacuum die-casting technology status quo.
It can match with the existing die-casting machine, adapt to the die-casting machine of the ordinary die-casting (no vacuum) and high vacuum die-casting work mode.
Ensure that the high vacuum die-casting production reliability and stability.
Haichen die casting machine control system of advanced application mainly focuses on real-time control technology, intelligent level enhancement, the application of fuzzy PID control strategy, the application of full closed-loop real-time control technology and the development of high-vacuum control system, etc.
The application of these technologies has significantly improved the control accuracy of die casting machine.
The level of intelligence and production efficiency.