Advantages of die casting Furnace significantly:
- Improve product quality,
- Increase production efficiency
- Reduce production costs
- Achieve high efficiency and energy savings
- Making them indispensable
- Important equipment in modern manufacturing.
These advantages of furnaces make die-casting machine furnaces widely used in the field of metal parts manufacturing. Especially in automotive, home appliances, aviation, and many other industries.
Die casting machine melting furnace is used to heat the metal material to the melting point above, for casting equipment. In die-casting production, the main role of the melting furnace is to melt the metal(e.g. aluminum, zinc, magnesium, copper, etc.). And to ensure that the alloy melting to get the chemical composition by the provisions. Also the liquid metal has good crystallization organization and less gas and inclusions. Furnaces usually use electricity or natural gas as a heat source and can be crucible or crucible-less melting furnaces.
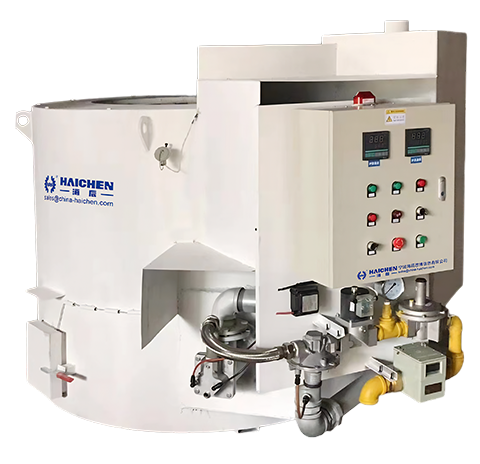
In the die casting process, the furnace is not only used to melt the metal but also plays a role in keeping the metal warm. It maintain the liquid metal at a suitable temperature before die-casting in the crucible. The hot chamber die casting machine furnace is usually integrated with the machine. Its pressure chamber immersed in the molten metal. While the cold chamber die casting machine will be the pressure chamber and crucible separately, needing to remove the liquid metal from the furnace for die casting.
Die casting furnaces offer a variety of advantages that make them widely used in modern casting processes. In the following artical, we will explain in details about the dvantages of die casting Furnace.
Energy efficiency:
Die casting furnaces can improve the energy efficiency of the casting process through the use of new processes. Such as the constrained fast induction melting single shot up casting process. This means that energy savings can be achieved at all stages of melting, alloying, mold making, pouring, curing, and surface treatment.
Provision of high–quality metal fluids:
Die-casting furnaces are also capable of delivering high-quality liquid metal. For example, casting furnaces with a hydraulic tilt design smoothly control the flow of liquid metal. And ensuring a uniform temperature and low hydrogen content of the liquid metal during the casting process, as well as precise level control. This high-quality liquid metal contributes to improved surface quality and mechanical properties of the castings.
Automated control systems:
Die casting furnaces often have automated control systems, which not only increase ease of operation but also reduce the potential for human error. At the same time, the design of these furnaces often includes easy-to-clean smooth interiors and large doors, which help maintain cleanliness and extend the life of the equipment.
Energy saving optimization:
Die casting furnaces as the main equipment for melting and heat preservation, have high energy consumption, and low energy efficiency features. Its energy saving to reduce manufacturing costs and achieve energy saving and emission reduction has important significance. Optimizing the process parameters of the furnace, such as melting speed, the highest and lowest height of the holding tank, stop melting time, etc.,. It can effectively reduce the overall energy consumption and melting burnout.
Good product quality:
Die casting has excellent mechanical properties, when the liquid metal solidifies under high pressure, the product is fine, dense, and crystalline, with high hardness and strength.
High dimensional accuracy:
Parts produced by die-casting have high durability and dimensional accuracy, and can maintain their dimensional accuracy even under harsh conditions, reducing the need for machining and improving the utilization of alloys.
Haichen Advantages of die casting Furnace
Haichen Machinery has rich experience in producing die casting products of different die casting materials. The furnace has many types, like electrical furnaces, gas furnaces… We can give you professional technical support from choosing raw materials, customizing molds, and selecting molds to after-sales service. If there is any demand for die casting machines and die casting molds, welcome to visit our website to learn the production information of different products.