Die casting is a metal forming process featuring the injection of molten metal under high pressure into a reusable steel mould.
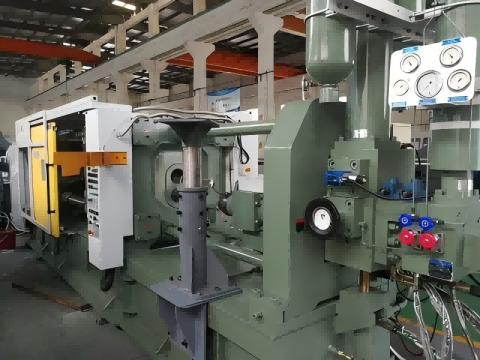
This process is capable of producing metal parts with complex geometries, precise dimensions and smooth surfaces.
What is Die Casting?
Die Casting is a metal casting process that involves injecting molten metal under high pressure into a reusable steel mold (called a die) to efficiently produce complex, high-precision metal parts. Here are the key details:
Process Overview
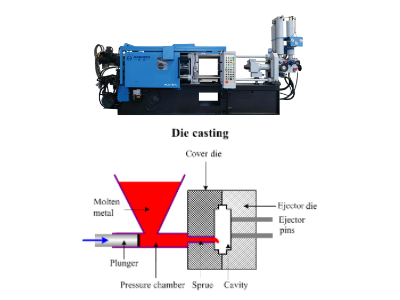
- Mold Preparation: The die consists of two halves (fixed and movable) with cooling systems to accelerate solidification.
- Metal Injection: Molten metal (e.g., aluminum, zinc, or magnesium alloys) is injected into the die cavity under high pressure (7–350 MPa).
- Pressure Holding & Cooling: The metal solidifies under pressure to ensure part density.
- Mold Opening & Ejection: The die separates, and ejector pins push out the part. Excess material (flash) and gates are trimmed.
Common Materials
- Alloys: Aluminum (e.g., A380, 356.0), zinc, magnesium, and copper/lead/tin-based alloys.
- Suitability: Ideal for low-melting-point metals, enabling thin walls (as low as 0.5 mm) and intricate geometries.
Key Advantages
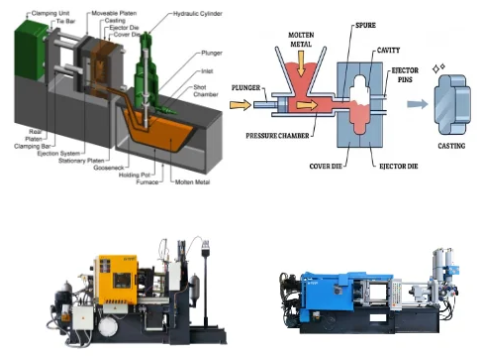
- High Efficiency: Suitable for mass production; mold lifespan exceeds 100,000 cycles.
- Precision & Finish: Tight dimensional accuracy and smooth surfaces minimize post-processing.
- Material Efficiency: Recyclable scrap supports sustainable manufacturing.
- Design Flexibility: Supports insert molding and complex shapes.
Applications
- Automotive: Engine components, transmission housings, structural parts.
- Electronics & Appliances: Heat sinks, housings, connectors.
- Industrial Machinery: Tools, hardware, mechanical parts.
- Aerospace: Lightweight structural components.
Techniques
- High-pressure Die Casting (HPDC): Dominant method for high-volume, precision parts.
- Low-pressure/Gravity Die Casting: Used for thicker walls or high-integrity components.
- Hot-chamber vs. Cold-chamber: Zinc alloys often use hot-chamber machines; aluminum uses cold-chamber systems.
Sustainability
Die casting has a low environmental footprint due to recyclable alloys and eco-friendly surface treatments (e.g., Micro-arc Oxidation, MAO) that avoid heavy-metal pollution.
What Are the Steps Involved in Die Casting?
An overview of the die casting process usually includes the following basic steps:
1. Mould preparation
2. Melting the metal
3. Injection
4. Cooling and demoulding
5. Post-treatment
1. Mould preparation:
First, need to cleane and lubricate the mould to ensure that it releasing smoothly after injection.
The mould usually consists of two halves, called cavities, which are tightly closed together to withstand the high pressures generated when the molten metal is injected.
2. Molten metal:
The metal used is usually melted in a furnace, and common alloys include zinc, aluminium, magnesium, copper, lead and tin.

Depending on the metal used, die casting machines are divided into two types: hot chamber and cold chamber.
Hot chamber die casting machines are suitable for low melting point metals such as zinc and magnesium alloys, while cold chamber die casting machines are suitable for high melting point metals such as aluminium alloys.
3. Injection:
Molten metal is injected into the mould cavity through an injection system.
Injection is carried out under high pressure to ensure that the metal completely fills the mould and to prevent defects such as porosity.
4. Cooling and demoulding:
After the metal is injected into the mould, it needs to be kept under pressure until it is fully cured.
The mould is then opened and the finished part is pushed out.
The cooling time depends on the type of metal used, the thickness of the casting and the complexity of the design.
5. Post-processing:
The finished part may need to be trimmed or deburred to remove excess material.
In addition, surface treatments or other machining may be performed to achieve the desired specifications.
The advantage of die casting is its ability to produce high quality, dimensionally accurate parts quickly for high volume production.
It is widely used in industries such as automotive, consumer electronics and home appliances.
However, moulds are more costly and therefore more suitable for mass production.
Die casting is an efficient and cost-effective method of metal forming that meets the needs of modern manufacturing for complex geometries and high-precision parts.
Mould preparation in the Die Casting Process
In the die casting process, mould preparation is a key step.
It directly affects the quality of the final product and production efficiency.
Mould preparation usually includes the following aspects:
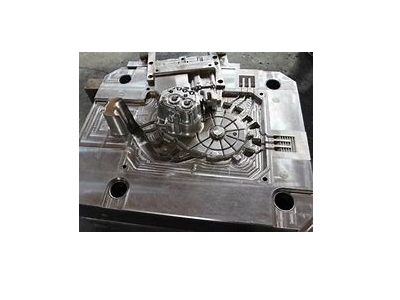
1.Mould design and manufacture
2. Assembly and clamping of mould semi-finished products
3. Mould cleaning and heating
4. Mould lubrication
5. Maintenance and optimisation of the mould
1.Mould design and manufacture:
The design and manufacture of moulds is fundamental to ensure high quality castings.
Moulds must making in high quality tool steel and properly do heat treat to achieve the hardness and durability.
Mould design needs to take into account a variety of factors such as wall thickness, chamfers, parting lines and cooling systems to ensure accuracy and consistency of the castings.
2. Assembly and clamping of mould halves:
The mould consists of two halves: a fixed mould half and a moveable mould half.
In the preparation phase, these two halves will be assembleing correctly and pressurised with a mould press to ensure that they fit tightly together. This step is crucial to ensure that the mould can withstand high pressures and temperatures during the injection process.
3. Mould cleaning and heating:
Before the molten metal is injecting into the mould, engineers need to clean and heat the mould.
This step is to ensure that the mould surface is clean and at the proper temperature to prevent premature solidification of the metal in the mould.
4. Mould Lubrication:
In order to reduce the friction between the metal and the mould and to improve the release performance of the casting.
The internal surface of the mould is spraying with a layer of lubricant or refractory material.
This lubricant not only helps to reduce internal friction, but also helps to maintain the temperature of the mould.
It prevents premature solidification of the metal in the mould and facilitates the removal of the casting from the mould.
5. Mould maintenance and optimisation:
Regular maintenance and optimisation is essential in order to extend the life of the mould and maintain its performance.
This includes cleaning the mould, checking for wear and tear, and repairing and adjusting as necessary.
Through the above steps, the mould preparation stage lays the foundation for the subsequent injection of molten metal, cooling and curing, as well as the removal of castings.
The successful execution of this stage is directly related to the efficiency of the entire die casting process and product quality.
How the metal melting during the die casting process
During die casting, the melting of metal is happening in two main ways:
Hot chamber die casting and cold chamber die casting.
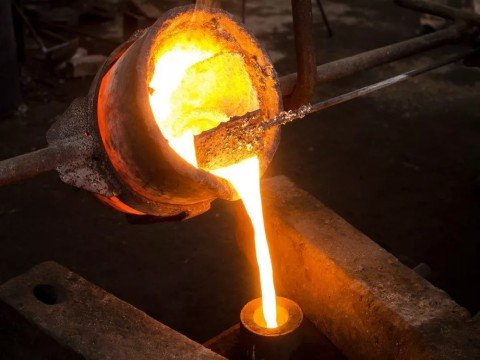
1. Hot chamber die casting:
This method is suitable for low melting point metals such as zinc, tin and lead alloys.
In hot chamber die casting, the molten metal is heated to a molten state and held in a molten pool inside the casting machine.
When die casting is running, a hydraulic or pneumatic piston pushes the molten metal from the molten pool into the mould cavity.
Since the molten metal is in direct contact with the machine, production will carry out quickly and efficiently.
2. Cold chamber die casting:
This method is suitable for high melting point metals such as aluminium, magnesium and copper alloys.
In cold chamber die casting, the metal is first heated to a molten state in a separate furnace.
The molten metal is then fed into the injection chamber of the die casting machine via a pouring system.
During this process, the metal does not come into contact with the machine, thus reducing the risk of erosion and corrosion.
This process is to produce castings of complex shapes because of its faster cooling rate and the possibility of cooling while maintaining high pressures.
In both methods, the melting of the metal is done in specially designed furnaces.
These furnaces can be induction furnaces, electric arc furnaces, or other types of furnaces, depending on the type of metal .
For example, aluminium alloys are often using induction furnaces, as these furnaces provide uniform heating and reduce oxidation.
In addition, in some modern die casting processes, electromagnetic induction heating technology may to melt the metal.
This technique offers the advantages of fast heat-up, ease of control and high melting efficiency, while reducing fume emissions.
Whichever method it is, the metal is injected into the mould when it reaches the appropriate melting temperature and is rapidly cooled and solidified under high pressure to form the desired casting shape.
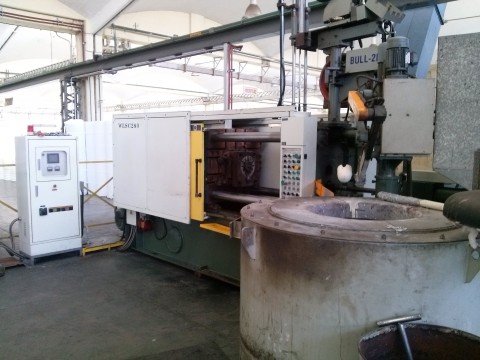
This process requires precise control of temperature, pressure and time to ensure the quality and accuracy of the final product.
How the die casting process in cooling and de-moulded
Cooled and de-moulded are two key steps in the die casting process.
They are done through the flow of coolant and cooling by spraying the release agent.
This is work in conjunction with a pick-up machine.
1.Cooling process
*Cooling method:
Die casting moulds are usually cooled by oil cooling.
Set cooling water channel in the mould, through the cooling oil to take away the heat absorbed by the mould, so as to achieve the effect of cooling.
Indirect cooling is also a commonly method, which can avoid the contamination of the workpiece.
That is, the cooling oil does not directly contact the workpiece, but is recycling through the cooling channels inside the mould.
* Cooling control:
The cooling time needs adjusting according to the size of the die casting.
Wall thickness and other factors to ensure that the metal liquid can solidify completely.
In high-efficiency production and large thick-walled castings in die casting, often need to be forced cooling to maintain the thermal balance of the mould.
In order to improve production efficiency and casting quality.
* The role of the mould release agent:
In the die casting process, in order to prevent the high temperature metal liquid from sticking to the mould, mould release agent usually spraying to the mould surface .
The water in the release agent evaporates quickly at high temperatures, forming a protective film that prevents the liquid metal from adhering to the mould.
The release agent not only helps cooling, but also reduces the thermal shock to the mould and prolongs the life of the mould.
2. Mould release process
* Mould release method:
When the die casting is finish, the die casting is ejected from the mould using special ejector equipment.
Mould release can be carried out by ejecting, pushing out, rotating, etc., depending on the structure of the product and the design of the mould.
*Cautions:
Care should be taken during the demoulding process avoding damage or deformation to the die casting.
After demoulding, trimming and surface treatment of the die casting will to improve the quality and performance of the product.
* Post-treatment:
After demoulding, the die castings may processing by removing remnants, trimming, deburring and other processing treatments.
According to the requirements of the product, surface treatment such as painting and plating also carring out to improve the corrosion resistance and aesthetics of the product.
Die casting process of cooling and mould release is to ensure product quality and production efficiency is an important link.
Through reasonable cooling design and demoulding technology, can effectively improve the quality of die casting, and prolong the service life of mould.
What Are the Most Suitable Materials for Die Casting?
Die casting is a manufacturing process that requires materials with specific properties such as fluidity, strength, and thermal stability. The most commonly used materials include aluminum, zinc, magnesium alloys, and copper alloys. Below is a detailed analysis of their characteristics and applications:
1. Aluminum Alloys
- Advantages:
- Lightweight, high strength-to-weight ratio, corrosion resistance, and dimensional stability.
- Ideal for complex geometries and thin-walled components (e.g., automotive parts like the Tesla Model Y rear chassis, aerospace components, and electronics).
- Process Compatibility:
- Typically processed via cold chamber die casting due to high melting temperatures.
- Recyclable and environmentally friendly.
- Common Grades:
- Alloys like A380 and A360 are widely used for their low viscosity and excellent flow properties.
2. Zinc Alloys
- Advantages:
- High ductility, low melting point, and superior surface finish (minimal post-casting machining required).
- Ideal for small, precision parts (e.g., gears, connectors, and decorative hardware).
- Cost Efficiency:
- Lower tooling costs for hot chamber die casting, suitable for medium-to-low-volume production.
- High-volume production may require durable tool steels to extend mold life.
3. Magnesium Alloys
- Advantages:
- Extremely lightweight (density ≈ 1.8 g/cm³, two-thirds that of aluminum) with excellent machinability.
- Used in weight-sensitive applications (e.g., automotive frames, laptops, and drones).
- Challenges:
- Requires strict control of melting conditions (e.g., inert gas shielding) to prevent oxidation.
4. Copper Alloys (Brass/Bronze)
- Advantages:
- High thermal and electrical conductivity, ideal for electrical components and heat sinks.
- Brass die castings are common in plumbing fixtures and valve parts.
- Limitations:
- High melting points necessitate cold chamber die casting and advanced mold materials (e.g., H13 tool steel).
- Higher production costs limit widespread use.
Other Materials
- Tin/Lead Alloys: Rarely used, mainly for specialized applications like bearings.
- Iron/Steel: Not feasible for traditional die casting due to extremely high melting points.
Key Selection Criteria
- Production Scale: Aluminum suits high-volume production (cost-effective tooling).
- Part Complexity: Aluminum and zinc excel in intricate designs; magnesium is optimal for lightweight structures.
- Performance Needs: Copper alloys for conductivity; high-silicon aluminum alloys for strength.
- Sustainability: Aluminum and magnesium are highly recyclable; zinc offers lower upfront costs.
Aluminum, zinc, and magnesium alloys dominate die casting due to their balanced properties and versatility. Copper alloys fill niche roles in thermal/electrical applications. Material choice depends on technical requirements, production scale, and cost considerations. Collaborating with experienced die casting manufacturers ensures optimal solutions tailored to specific needs.
Advantages and Disadvantages of Die Casting
Advantages of Die Casting
- High Dimensional Accuracy and Surface Finish
Die-cast parts exhibit stable dimensions with tight tolerances, making them ideal for precision applications. The surface finish is excellent, often eliminating the need for post-processing, which reduces secondary machining costs. - High Efficiency and Economies of Scale
Short production cycles (as low as seconds) make die casting suitable for high-volume manufacturing. Unit costs decrease significantly with increased production volumes. Reusable molds further enhance productivity. - Complex Geometries and Thin-Wall Capability
Intricate details and thin-walled components (e.g., aluminum alloys with walls as thin as 0.5mm or zinc alloys at 0.3mm) can be achieved, which are difficult with other processes. High-pressure injection ensures complete mold filling, enabling high design complexity. - Superior Mechanical Properties
Die-cast parts have higher strength, hardness, and durability compared to sand-cast parts, with tensile strengths up to 415 MPa. Low porosity designs improve overall part performance. - High Material Utilization
Reduced waste generation, combined with near-net-shape technology, minimizes metal consumption.
Disadvantages of Die Casting
- Limited Material Options
Only low-melting-point metals (e.g., aluminum, zinc, magnesium) are suitable. High-melting-point alloys (e.g., steel) cannot be die-cast due to mold thermal damage. Copper alloys face limitations in application. - High Initial Investment
High tooling and equipment costs (molds can cost 12,000–12,000–15,000) make die casting uneconomical for small batches. Production volumes typically need to exceed 5,000 units to justify costs. - Gas Porosity and Heat Treatment Limitations
High-pressure injection can trap air, causing internal gas porosity. Subsequent heat treatment may induce cracking, restricting use in high-strength applications. - Design Complexity and Mold Life Constraints
Mold complexity affects feasibility, and high-melting-point alloys reduce mold lifespan. Draft angles and ejector pin marks may compromise part aesthetics. - Unsuitable for Low-Volume Production
High tooling costs and rapid production cycles make die casting cost-ineffective for small batches.
Haichen Die Casting Services
Die casting is a popular metal manufacturing process due to its precision, efficiency and low cost. Although the concept of die casting is fairly simple, it requires expertise and experience, so finding the right supplier is crucial.
We at Haichen have a team of knowledgeable and experienced engineers. We pride ourselves on providing the highest quality products based on our customers’ needs.
Contact Haichen anytime to send your metal product design for a free instant quote.