The main types of chillers (coolers) in die casting machines include screw, piston, centrifugal and drum types.
These types of chiller different classification lies in different refrigeration compressor and heat exchange medium.
According to different die-casting production needs to choose the appropriate chiller.
- Screw chiller
- Piston chiller
- Centrifugal chiller
- Drum type chiller
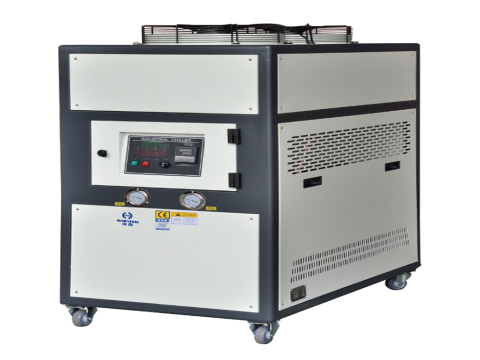
Screw chiller:
This type of chiller is usually more expensive than other types of chiller (such as centrifugal and piston) because of its higher efficiency and reliability.
Screw chillers are categorised into single screw and twin screw.
With single screw chillers being less expensive and simpler to maintain.
Piston chiller:
This type of chiller uses a piston as the compressor and is usually used in applications that require high precision control.
Centrifugal chiller:
Centrifugal chiller has a large single cooling capacity, cooling capacity is usually greater than 1000 kilowatts. Small footprint, low energy consumption, high reliability.
Drum type chiller:
This type of chiller is usually used in applications that require high efficiency and low noise.
For die casting machines, the cooling system is an important part of ensuring production efficiency and product quality.
In the automotive brake system and aluminium casting manufacturing, cooling system is used to control the temperature of casting parts.
Prolong the life of electrical components and avoid overheating damage.
In addition, the cooling system of die casting machine can also solve the inadequacy of traditional air conditioning cooling system in high temperature environment by using thermoelectric cooling system.
Therefore, when selecting a chiller for a die casting machine, it is necessary to consider its cooling capacity, energy efficiency, maintenance costs.
And suitability for specific production environments and process requirements.
Each type of chiller has its own unique advantages and applicable scenarios, so in the actual application should select according to the specific needs.
Characteristics of oil-cooled type chiller for die-casting machines
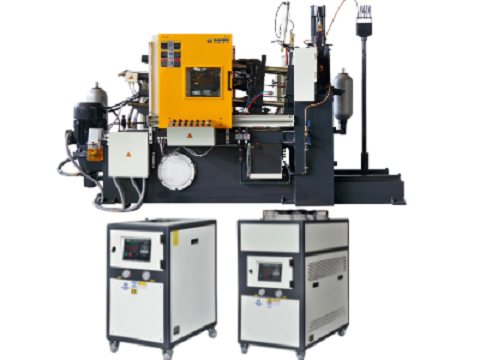
Die casting machine oil cooling chiller is the most conventional cooling equipment in die casting industrial production.
It has the following characteristics:
- High efficiency and reliability
- Versatility
- Compact design
- Precise temperature control
- High adaptability
- Easy maintenance
- Energy-saving design
- A variety of models to choose from
High efficiency and reliability:
Die casting machine oil cooling chiller can accurately control the temperature of hydraulic oil and cooling oil to ensure the stable operation of die casting machine.
These devices usually have high efficiency, low noise and small vibration characteristics.
And equipped with a variety of protection devices, can effectively save energy.
Multifunctionality:
Die casting machine oil cooling chiller can use hydraulic oil cooling die casting machine each heat link.
Can also using servo motor and its controller heat dissipation, there by improving the performance and reliability of the entire system.
Compact design:
Die casting machine oil cooling chiller is usually very compact design, easy to operate and maintain, suitable for use in a variety of industrial applications.
Such as die casting machines, machine tools, plastic injection moulding machines and so on.
Precise temperature control:
Die casting machine oil cooling chiller can provide precise temperature control.
This is essential to keep the mould temperature within the ideal range, thus improving the mechanical properties and density of die castings.
Adaptability:
Die casting machine oil cooling chiller can adapt to different working conditions, such as different cooling needs and ambient temperature changes.
Ensure that the equipment can operate safely and reliably in various environments.
Easy maintenance:
Die casting machine oil cooling chiller operation is simple and intuitive, fault points can be directly displayed, easy to quickly diagnose and repair.
Energy-saving design:
Through optimised design, die casting machine oil cooler chiller can improve productivity and reduce operating costs while reducing energy consumption.
Multiple model selection:
According to different cooling needs, die casting machine oil cooling chiller provides a variety of models to choose from, ranging from 0.98kW to 21kW, to meet the needs of different sizes of die casting machine.
These features make the die casting machine oil cooler chiller become indispensable equipment in modern die casting production.
They can significantly improve the quality of die casting parts and production efficiency.
How to use various types of die-casting machine chiller
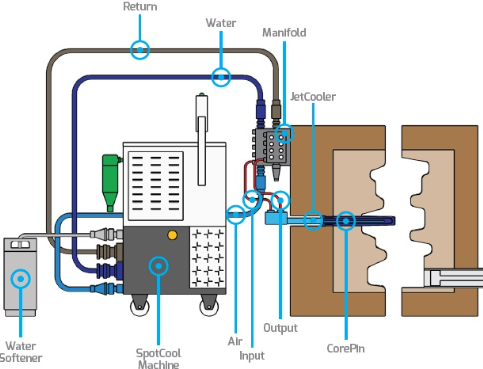
The chiller (cooler) of the die casting machine plays a vital role in the die casting process.
It can effectively reduce the temperature of the mould and casting, so as to improve the production efficiency and product quality.
The following are detailed instructions on how to use various types of die casting machine chiller:
- Equipment installation
- Connect the power supply
- Operate the switch
- Adjusting the temperature
- Maintenance and safety
Equipment installation:
Place the die casting machine chiller on a solid, smooth, level and temperature-resistant surface, and regularly clean the mounting surface as well as the feet on the equipment.
For units equipped with cast iron, the application of a locking brake is required to prevent them from slipping out of place.
When mounting, press the lever down to release the locking brake on the casting wheel, then press the lever up to lock the brake.
Connect the power supply:
Before connecting the power supply, ensure that the unit is left upright for approximately 2 hours to minimise the risk of failure.
Plug the cooler into a suitable socket, switch on the rear switch and the ‘Power ON Status’ indicator will light up.
When connecting the power cable, insert the 3-pole connector into the socket of the unit.
Ensure that it is pushed firmly into place, then insert the power cord plug into the power outlet.
When disconnecting the power cord, remove the plug from the power outlet and then disconnect the unit from the power cord.
Operate the switch:
When switching on the device, press the switch paddle upwards to the ‘I’ position; when switching off the device, place the switch paddle in the ‘O’ position.
Adjusting the temperature:
The thermostat of the chiller of the die-casting machine can adjust the temperature of the water.
Turning the thermostat knob clockwise will lower the water temperature; turning it counterclockwise will raise the water temperature.
Turn the thermostat knob fully counterclockwise to ‘0’ or ‘STOP’ position, the compressor will shut down.
Maintenance and safety:
During use, avoid placing heavy objects on the unit to avoid affecting the stability and operating efficiency of the unit.
Regularly check the water inlet and carbon dioxide pipeline of the equipment to make sure there is no leakage to ensure the normal operation of the equipment.
Through the above steps, you can effectively use all kinds of die casting machine chiller to ensure that it plays the best performance in the production process.
Correct operation and maintenance can not only improve production efficiency, but also extend the service life of the equipment.
Haichen provides all types of die-casting machine chiller
Haichen provides all types of die casting machine chiller (cooling system) plays a vital role in the die casting process.
The design of the cooling system of die casting machine directly affects the service life of the mould and the quality of the die castings.
Listed below are the detailed technical details of the die casting machine chiller provided by Haichen:
- The importance of cooling system design
- Application of cooling technology
- Optimisation of cooling system
- Intelligent control system
The importance of cooling system design:
The temperature control of die casting mould is crucial for the quality of die casting and the service life of mould.
Reasonable cooling system can not only shorten the production cycle, but also improve the quality of the product and the service life of the mould.
In the die casting process, the design of the cooling system needs to consider the temperature of the cooling water, the diameter of the cooling water pipe and its position and other factors, which will have a significant impact on the temperature field of the mould.
Application of cooling technology:
Haichen developed a die-casting mould core needle temperature control device based on high-pressure cooling circulating water.
The device has the functions of automatic constant temperature of cooling water and combination of water cooling and air cooling.
It can effectively reduce the shrinkage/shrinkage defects at the bottom of the core needle of the casting mould, improve the internal quality of the casting and extend the service life of the core needle.
Haichen has also developed a low-pressure high-flow pump idle cooling system.
Through the feedback control algorithm to control the motor speed according to the oil temperature to improve the cooling effect, energy saving and environmental protection.
Optimisation of cooling system:
In the design of the cooling system of the aluminum alloy cover die-casting mould, a copycat cooling scheme is adopted.
Greatly improve the cooling effect, so that the comprehensive scrap rate from the original 12% to less than 4%.
For the application in aluminium alloy cylinder block die casting, the integral pressure chamber cooling system is used to reduce the temperature difference of the pressure chamber in the whole working process.
Reduce the deformation of the pressure chamber and improve the service life of the chamber.
Intelligent control system:
Haichen has achieved intelligent monitoring and adjustment of mould temperature by developing heat source identification temperature control device.
It makes the die-casting mould temperature control method simple and efficient, and the production cost is reduced.
PLC-based die-casting mould temperature intelligent control system design.
Through the combination valve and PID control of cooling water flow, it realises the function of preheating and continuous die-casting temperature maintenance.
Various types of die casting machine chiller provided by Haichen have significantly improved the quality of die castings and the service life of moulds through advanced cooling technology and intelligent control system.
The application of these technologies not only improves the production efficiency, but also achieves the goal of energy saving and environmental protection.