Aluminum die casting machine conveyor is used for die-casting machine supporting equipment, mainly used for die-casting aluminum castings from the die-casting area to post-processing or packaging area.
In the aluminum die casting process, a cold chamber die casting machine is commonly used to deal with the high melting point characteristics of aluminum. The molten aluminum is injected into the mold cavity through a gate and solidifies rapidly under high pressure to form the casting.
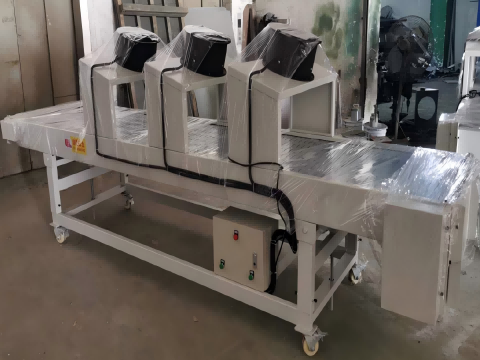
Key Features of Aluminum die casting machine conveyor
High-Temperature Resistance
- Made with heat-resistant materials to endure the elevated temperatures of freshly cast aluminum parts.
Robust Construction of Aluminum die casting machine conveyor
- Typically constructed from stainless steel or durable alloys to handle the weight and stress of cast components.
- Resilient to wear and tear caused by abrasive aluminum parts.
Customizable Dimensions
- Available in various lengths, widths, and configurations to suit specific die casting setups.
- Custom designs can include flat belts, slat conveyors, or modular chain conveyors.
Smooth Part Handling
- Designed for gentle handling to prevent damage to the freshly cast parts, minimizing defects.
Integration with Die Casting Machines
- Easily integrates with die casting machines, ensuring seamless transfer of parts directly from the ejection area.
Cooling Systems
- Often equipped with air or water-cooling units to help cool the cast parts during transportation, enhancing efficiency.
Automated Sorting and Accumulation
- Can include automated sorting systems to separate parts based on size or quality.
- Accumulation zones for temporary storage, optimizing workflow.
Speed Adjustability
Variable speed controls to match the production rate of the die casting machine.
Safety Features
- Safety guards and emergency stop systems ensure worker protection.
- Enclosed designs reduce exposure to hot parts.
Benefits of of Aluminum die casting machine conveyor
- Enhanced Productivity: Reduces manual handling, increasing throughput and efficiency.
- Improved Safety: Minimizes direct human contact with hot and heavy parts.
- Consistent Quality: Ensures steady and uniform transportation of cast parts, reducing defects.
- Cost Efficiency: Lowers labor requirements and speeds up the production process.
Selecting the Right Conveyor
When choosing an aluminum casting conveyor:
- Consider Load Capacity: Ensure it can handle the weight and dimensions of your cast components.
- Check Compatibility: Match the conveyor’s features with your die casting machine.
- Evaluate Durability: Opt for materials and construction that can withstand harsh environments.
- Customization Needs: Ensure it fits seamlessly into your production layout.
Haichen Aluminum die casting machine conveyor
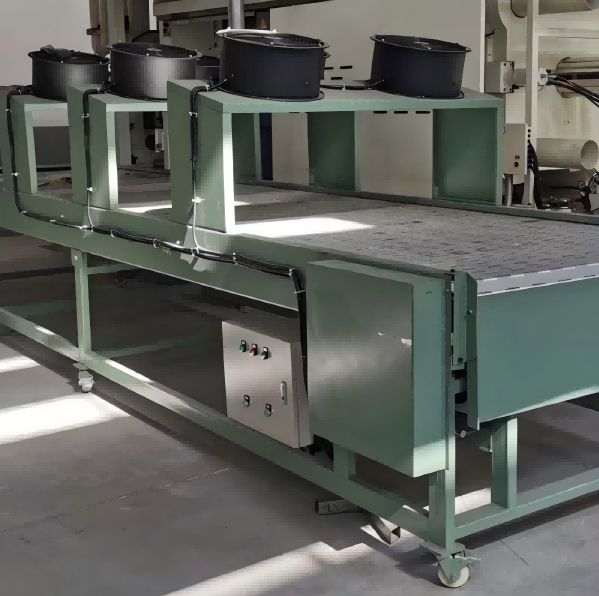
Haichen Machinery, based in Ningbo, China, specializes in manufacturing die casting machines.
However, Haichen specializes in manufacturing cold chamber die casting machines and hot chamber die casting machines, it often integrates auxiliary equipment like conveyors to optimize production workflows.
If you have any questions about die casting conveyor belts, please feel free to ask us.
Aluminum casting conveyor mainly used for die-casting aluminum castings from the die-casting area to the cooling, post-processing or packaging area. It play an important role in die casting machines, they not only improve productivity and product quality, but also enhance operational safety and reduce production costs.