Choose mould temperature controller need consider factors like metal material type, mold structure, select cooling medium, and so on.
Mold temperature is one of the most important parameters in the die casting process. It directly affects the quality of castings, production efficiency and the service life of the mold.
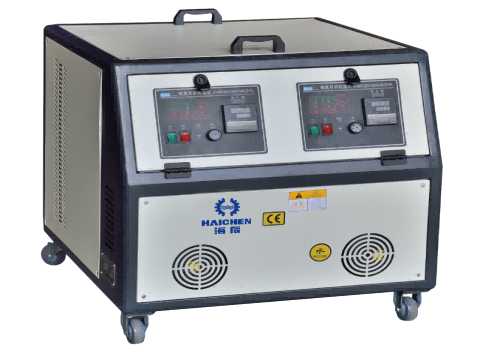
To choose mould temperature controller for the die casting machine, below are the detailed factors:
1. Mold type and alloy type of mould temperature controller
Different types of die casting alloys have different requirements for mold temperature.
For example, the recommended operating temperature for zinc alloys is 160-200°C; magnesium alloys are 180-240°C,; aluminum alloys are 200-250°C, and copper alloys are 280-350°C. So it is crucial to choose appropriate mold temperature controller according to the type of alloy used.
2. Mold structure and cooling conditions of mould temperature controller
The thermal balance of the mold has an important influence on the mold temperature control. Factors such as the mold preheating temperature, pouring temperature, alloy liquid capacity. And mold volume, layout of the casting and overflow system, and mold cooling conditions will affect the thermal balance. Therefore, when choosing mold temperature controller, these factors must be considered to achieve a good thermal balance.
3. Selection of cooling medium
Mold temperature controllers are usually divided into three types: water cooling, oil cooling and air cooling.
Water is a good heat transfer medium and is easy to control; oil has a higher specific heat capacity and can provide more uniform cooling; air as a cooling medium is less efficient but has a lower cost. It is key to select the right cooling medium according to specific application needs and environmental requirements.
4. Temperature Sensors and Monitoring Systems
Temperature sensors are used to measure the temperature of various parts of the mold to ensure uniform temperature distribution and avoid hot and cold spots. Advanced temperature monitoring systems, such as thermocouples or thermal imagers, can monitor the mold temperature in real time to ensure stability during production.
5. Power and pump selection of mould temperature controller
Calculate the required heating power based on the size of the mold, operating temperature and heating time, and select the appropriate pump to meet the flow and pressure requirements. This helps ensure that the mold can quickly and evenly reach the set temperature.
Haichen die casting machine
Haichen is one Chinese die casting machine manufacturer for more than 10years. We produce both high pressure cold chamber die casting machine and hot chamber die casting machine.They have durable and highly precise features. Haichen also produce die casting machine auxiliary equipment. Such as conveyor, vacuum machine, mold temperature controller, industrial robot, sprayer and so on.
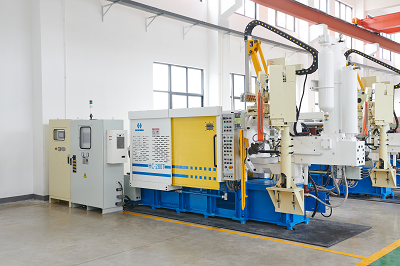
By comprehensively considering the above factors, you can effectively choose mould temperature controller to improve the quality and production efficiency of die-casting products. In addition, with the development of die-casting technology, new temperature control methods continue to emerge. The application of these new technologies can further improve the mold temperature control level and meet the needs of complex mold design.