Die casting design is a procedure intended for the production of metal components with exacting geometric features.
Die Casting Design is an important phase of the die casting sequence as it determines Quality and dimensional accuracy of cast metals achieved through proper design of molds and operating conditions in the design stage. In addition to meeting the functional requirements, a successful die casting design needs to balance various competing constraints, such as manufacturability, cost effectiveness, overall production efficiency, and effectiveness of the operations involved.
Multiple considerations need attention for optimum operation factors which could include: parting surface of the mold ,gate system ,cooling sytem…and core pulling structure. These elements play an important role to achieve desired quality standards regarding defect attributes specified or mandated during design stages. The details are as below:
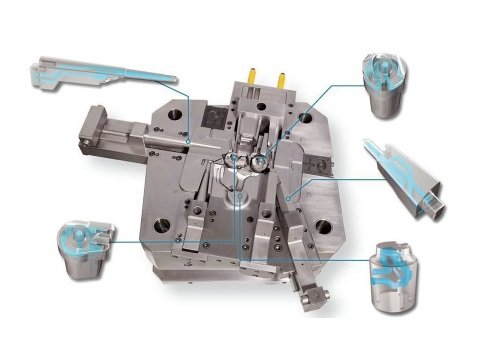
Die casting design materials
Die casting design materials refer to the metal materials used to manufacture parts in the die casting process. Choosing the right die casting material is crucial to ensuring the performance, surface quality and production efficiency of the parts.
The main metals used in the die casting process includes
- Aluminum-based alloys
- Zinc-based alloys
- Magnesium-based alloys
- Copper-based alloys
- Lead-based and tin-based alloys
- Iron-based alloys
- Other metals
Among them, aluminum and magnesium have become the mainstream choice due to their excellent properties, while zinc is widely used in the production of thin-walled castings due to its low melting point and fluidity. The choice of these metals depends on the specific application requirements like cold chamber die casting machine or hot chamber die casting machine. Also with cost considerations, and the required mechanical properties.
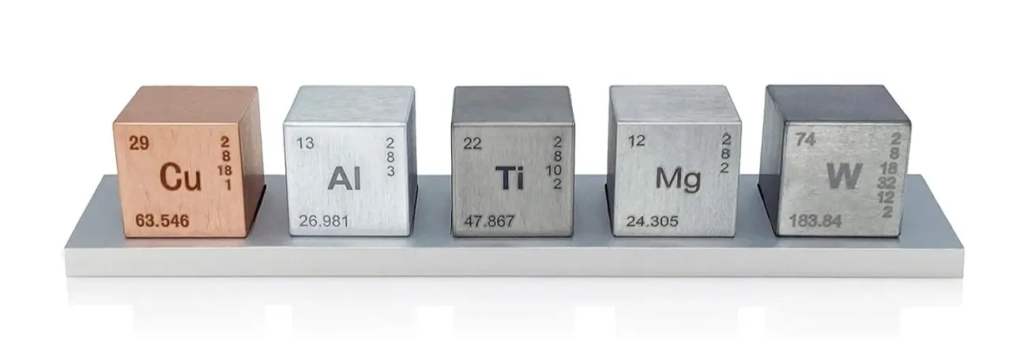
Aluminum-based alloys
Aluminum alloys are one of the most commonly used materials in die casting, with low density, good mechanical properties and excellent corrosion resistance. They are often used to manufacture automotive parts, household appliances and other parts that require light weight and high strength. Common aluminum alloys include AZ91D, AZ60, AM50, etc.
In addition, aluminum-based alloys are also widely used in the production of high-precision die castings, such as automotive engine parts and precision parts in electronic equipment.
Zinc-based alloys
Zinc-based alloys are widely used in die casting due to their low melting point and good fluidity. They are often used to make thin-walled and complex-shaped castings, such as toys, decorations and small mechanical parts. Zinc-based alloys have high impact strength and ductility, but their mechanical properties are relatively poor.
Magnesium-based alloys
Magnesium alloys are one of the lightest die casting alloys currently available, with extremely high specific strength and specific stiffness. They are mainly used in the aerospace, automotive and electronics industries to reduce weight and improve performance. Common magnesium alloys include AZ91D, which has good castability and corrosion resistance.
Copper-based alloys
Copper-based alloys are also used in some special applications, such as where high thermal conductivity and corrosion resistance are required. However, due to the high melting point of copper, its application in die casting is relatively rare.
Lead-based and tin-based alloys
These alloys were mainly used in the early die casting process, but due to their poor mechanical properties, they have gradually been replaced by other more advanced alloys.
Iron-based alloys
Although iron-based alloys are less used in die casting, they can still be used to make specific castings in some cases, such as when using graphite molds.
Other metals
Some special-purpose metals, such as titanium alloys and nickel-based alloys, are also used in some high-end applications, but these materials are usually more expensive and complex to process.
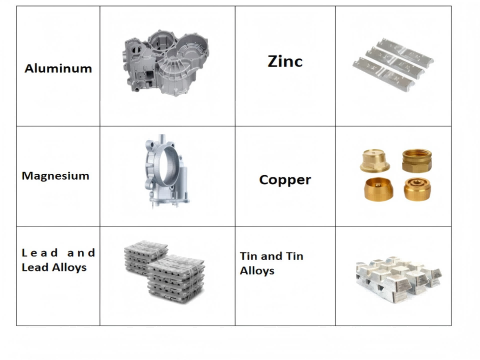
Die casting design of molds
Die casting mold design is a key step in the die casting process, which directly affects the shape, quality, dimensional accuracy, and production efficiency of the final product. Die casting mold design not only needs to consider the structure and material selection of the mold, but also needs to be optimized based on factors such as product design requirements, process conditions, and manufacturing costs.
Die casting mold
A die casting mold is a precision tool used to shape metal parts during the die casting process. It consists of two mold halves (a fixed mold and a movable mold) that, when closed, form a cavity for the molten metal to fill. The mold is usually made of high-strength tool steel to withstand the high temperature and pressure of casting conditions.
Die casting mold technology
The design of die casting mold usually requires a combination of computer-aided design (CAD) and computer-aided engineering (CAE) technologies. Through these professional software to optimize mold’s structure and process parameters.
For example, finite element analysis (FEM) can be used to evaluate the deformation and stress. That may occur during the use of the mold, thereby improving the mold design.
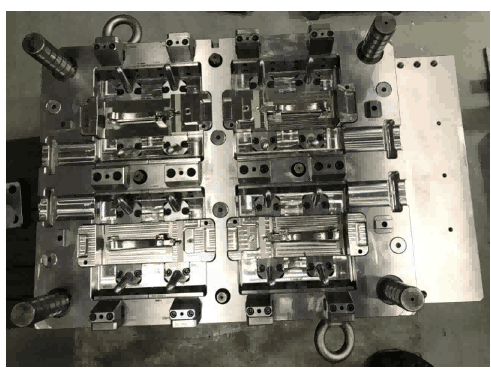
Die casting design Process
Die casting mold design usually includes the following main steps:
- Material selection
- Shrinkage setting
- Cavity design
- Gating system design
- Cooling system design
- Parting surface design
- Vent system design
- Mold strength analysis
Material selection
Select the appropriate alloy material, such as aluminum, magnesium or zinc, according to the purpose of the part
Shrinkage setting
Since the metal shrinks during solidification, the original design needs to be adjusted to compensate for this change
Cavity design
Determine the number, layout and location of the chambers on the mold base to achieve uniform filling and cooling.
Gating system design
Including the design of gates, runners and overflow grooves, which directly affect the metal fluidity and filling time
Cooling system design
Control the mold temperature by arranging cooling water channels reasonably to ensure fast and uniform cooling
Parting surface design
Select the appropriate parting surface position to avoid burrs or flashes and ensure that the mold is easy to open.
Vent system design
Set venting grooves and overflow grooves to exhaust gas and prevent the generation of pores.
Mold strength analysis
Use finite element analysis (FEM) to evaluate the deformation and stress distribution of the mold under high pressure to ensure its structural strength.
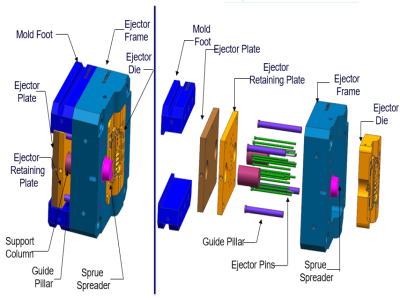
Die casting design cooling system
The cooling system design of die-casting molds is a key component of the die-casting process, with the main purpose of ensuring high-quality castings, improving production efficiency, and extending mold life through effective thermal management.
Water cooling system
Mechanism: By drilling holes or 3D printing cooling channels in the mold, the cooling water circulates to take away the heat in the mold.
Advantages:
High heat conduction efficiency, suitable for high-volume production.
Low cost and easy maintenance.
Disadvantages:
Requires a complex cooling water circulation system.
Additional cooling equipment may be required in high temperature environments.
Application: Widely used in die casting of high thermal conductivity materials such as aluminum and magnesium alloys.
Oil cooling system
Mechanism: Using hot oil as a cooling medium, suitable for mold cooling in high-temperature environments.
advantage:
Suitable for heat sensitive materials such as magnesium alloys.
It can still maintain good cooling effect at high temperatures.
Disadvantages:
High cost and complex maintenance.
The thermal stability of oil is poor, which may pose a fire risk.
Application: Mainly used for magnesium alloy die-casting, such as laptop casings.
Air cooling system
Mechanism: Blow air into the mold through a fan or natural convection to take away the heat.
Advantages:
Simple structure and low cost.
No risk of corrosion.
Disadvantages:
Low cooling efficiency, not suitable for high-volume production.
Uneven cooling may cause deformation of castings.
Application: Suitable for small batch production or prototype development, especially zinc alloy die casting.
The location and layout of the cooling channels need to be carefully calculated and optimized. Thus to ensure uniform temperature distribution in the mold, reduce stress concentration and casting defects.
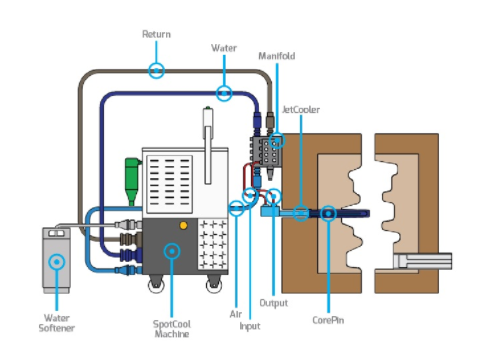
Design gates and runners
In die casting design, gates and runners are crucial components. They not only affect the filling process of die-casting parts, but also directly affect the quality, production efficiency, and cost of the final product. In addition, the gates and runners are also a key parts of die casting .
Reasonable gate position and runner design can effectively control the flow path of molten metal, and reduce the generation of pores and other defects. In modern die casting, automation and modular methods are being widely used to improve die casting efficiency and reduce trial and error costs.
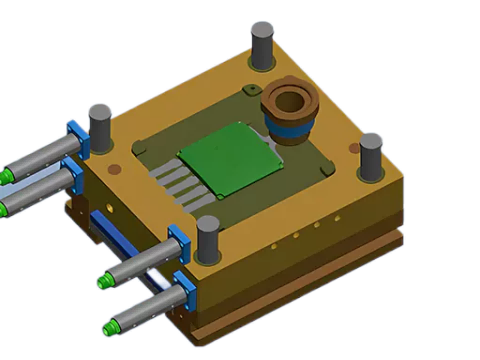
Application areas of die casting design
Automotive industry: Die casting design is widely used in automobile manufacturing, such as engine blocks, door handles, steering columns, etc.
Electronic industry: Die casting design is used to manufacture housings, brackets and other parts of electronic equipment.
Aerospace: Die casting design is used to manufacture structural parts of aircraft and spacecraft, such as wings, landing gear, etc.
Medical equipment: Die casting design is used to manufacture precision parts of medical equipment, such as surgical instruments, brackets, etc.
Conclusion
Die casting design is a complex and multidisciplinary process that requires comprehensive consideration of knowledge from multiple fields such as materials science, mechanical engineering, thermodynamics and computer simulation to achieve efficient and high-quality production goals.