Trim press application is to remove excess material from die castings such as sprues, risers, overflows and fretting on parting lines.
A trim press is an essential auxiliary machine used in the die casting process to remove excess material, known as flash, from cast components. Its applications are critical in ensuring the final part is free from imperfections and meets precise dimensional tolerances.
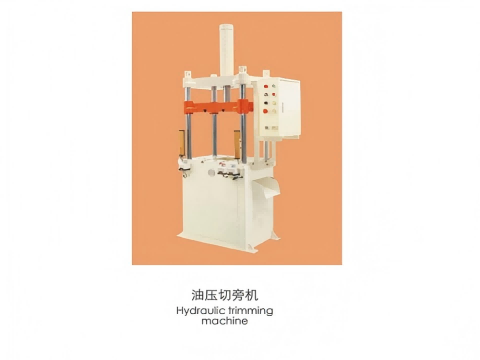
Trim press application
Flash Removal of trim press application
- Purpose: To remove excess material (flash) formed at the parting line of the die during the casting process.
- Application: After the cast part is ejected from the die, then the trim press separates the part from the runner, gate, and other unwanted sections.
Edge Trimming
- Purpose: Ensures clean edges for the cast part, and making it aesthetically and functionally suitable for use.
- Application: Trims burrs and sharp edges, especially critical for parts used in assemblies or where sharp edges could lead to handling issues.
Hole and Feature Punching
- Purpose: To form or refine openings or specific features in the part.
- Application: For parts requiring precise holes, slots, or indentations as part of the design, the trim press punches these features during the trimming process.
Deburring of trim press application
- Purpose: Removes small imperfections or residual burrs after flash trimming.
- Application: Prepares the surface for finishing operations like painting, coating, or anodizing, ensuring smoother finishes.
Quality Control
- Purpose: Provides consistency in part geometry.
- Application: Maintains tight tolerances by ensuring each part conforms to the required design specifications, and reducing the need for secondary machining.
High-Volume Production Efficiency
- Purpose: Speeds up the post-casting process.
- Application: Integrates into automated die casting lines to handle large volumes of parts efficiently, reducing manual labor and increasing throughput.
Scrap Management
- Purpose: Facilitates recycling of excess material.
- Application: The trimmed flash, gates, and runners are collected for re-melting, and reducing material waste in the die casting process.
Common Industries Using Trim Press in Die Casting
- Automotive: For engine components, brackets, and housings.
- Aerospace: For lightweight structural components.
- Consumer Electronics: For casings and structural supports.
- Industrial Machinery: For durable and precision components.
Haichen trim press for die casting machine
Haichen Machinery, based in Ningbo, China, specializes in manufacturing cold chamber die casting machines and hot chamber die casting machines. We also offer auxiliary equipment to enhance automation in the die casting process. This includes devices like trim press, mold sprayers, ladles and extractors, which can be integrated into production lines to improve efficiency and safety.
Advantages of Using Haichen Trim Presses
Improved Efficiency:
Reduces manual labor and secondary machining processes, streamlining production workflows.
Consistent Quality:
Ensures uniformity in trimming across all parts, reducing defects and rework costs.
Customizable Solutions:
Machines can meet specific production requirements, including custom tooling and automation options.
Cost-Effective Operations:
Durable design and low maintenance requirements reduce long-term operational costs.
So Welcome to consult us for trim press machines for die casting machines.
Trimming machines actively remove excess material from die castings, enhance product quality and productivity.