Temperature control equipment is an electrical and mechanical device used to regulate the temperature of the mold.
The purpose of temperature control equipment is to ensure that the mold is kept within the optimal temperature range during the die-casting process, thereby improving product quality and production efficiency.
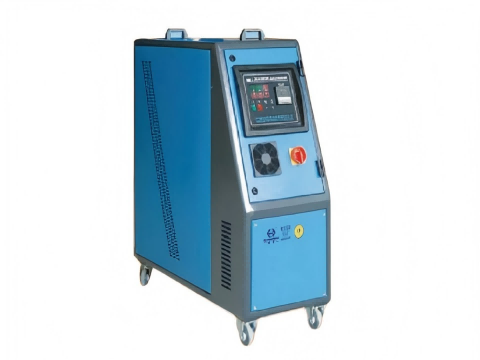
Key points of temperature control equipment for die casting machines
The importance of temperature control:
Die casting process, the temperature of the mold has a decisive influence on the quality of the casting. Unsuitable mold temperatures are the main cause of errors in the die casting process.
Therefore, the use of temperature control units is the first key measure for process optimization.
Mold heat balance:
During the die casting cycle, the heat released from the mold into the environment is exactly the same as the heat introduced by the molten metal until demolding.
The absorbed heat is dissipated through the heat transfer medium in the temperature control unit.
The task of temperature control:
Mold temperature is very important for heat dissipation of the molten metal, mold filling and solidification of the die casting.
The task of the temperature control unit is to heat the mold to operating temperature and maintain that temperature.
Components of temperature control equipment technology:
A complete temperature control system consists of a temperature control channel system within the mold, a temperature control unit, a heat transfer medium and a connection between the unit and the mold.
Performance of the unit:
When selecting a temperature control unit, the following criteria need to be considered to determine the performance of the temperature control system:
Material to be processed
Mold temperature
Heat transfer medium (water/oil)
Mold weight and heating time
Quantity per treatment
Temperature gradient in the mold
Pump pressure and flow conditions
Temperature Control Modes:
The temperature control system can control the mold temperature through the following three modes:
Medium temperature control: This is the most commonly used method and the control accuracy is sufficient in many cases.
Mold Temperature Control: If it is necessary to maintain the mold temperature within a particularly narrow range and if fully automatic operation is required, temperature sensors will need to be installed.
Cascade control: This method combines the above control modes and further improves temperature control within the mold.
Properly designed temperature control units offer many advantages to production, including increased mold life, reduced production costs, increased productivity and improved quality.
Haichen Temperature control equipment
Haichen is a die casting machine factory located in Ningbo, China, mainly supplying cold chamber die casting machine and hot chamber die casting machine. Besides machines, we also supply die casting auxiliary equipments, including temperature control equipment, ladles and extractors and so on.
The advantage of Haichen Temperature control equipment
Die Durability: Prevents thermal cracking or excessive wear.
Casting Quality: Ensures proper material flow, reducing defects like porosity or uneven surface finishes.
Cycle Time Optimization: Minimizes cooling and reheating times, improving productivity.
Energy Efficiency: Optimizes heat usage, reducing energy consumption.
If there is any requirement, please feel free to consult us.
Temperature control equipment in the die-casting process plays a vital role, it can not only improve product quality and production efficiency, but also extend the service life of the mold, reduce production costs.