Components of vacuum machine
Components of vacuum machine including vacuum pumps, vacuum tanks, and vacuum valves, etc.
Which work together to achieve the desired vacuum level.
Thereby reducing porosity and defects in castings, and improving the mechanical properties and surface quality of castings.
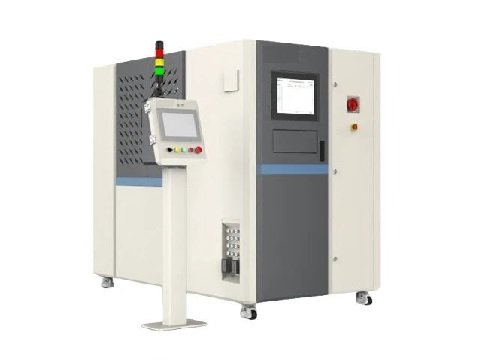
Vacuum pump
The vacuum pump is the core equipment of the vacuum system
Which is used to pump out the air in the mold cavity to form a vacuum state.
Typically, an electric motor drives a vacuum pump that is capable of creating a high vacuum to ensure that the molten metal does not create porosity when filling the mold cavity at high pressure.
Rotary vane pump
Suitable for medium and low vacuum requirements, simple structure, easy maintenance, but the ultimate vacuum degree is relatively low.
Spool valve pump
It is also a type of mechanical vacuum pump and has similar performance characteristics.
Roots pump
Suitable for high vacuum or ultra-high vacuum die casting, high vacuum, strong exhaust capacity and stability.
Diffusion pumps
Suitable for high vacuum requirements, high pumping rates, but long start-up times and heating.
Molecular Pump
Suitable for ultra-high vacuum requirements, stable pumping rate, no need for heating, but higher price.
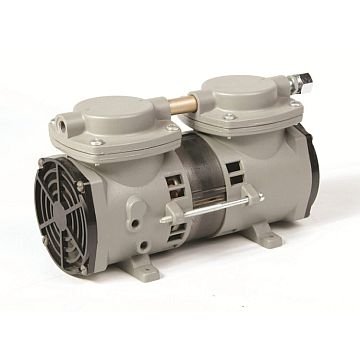
Lon pump
Suitable for very high vacuum and long-term stable operation, but with a small pumping rate.
Tank volume
The vacuum tank volume is 40~60 times the volume of the mold cavity to ensure sufficient vacuum capacity.
Ordinary vacuum die-casting devices generally use high-speed, low-dryness rotary vane vacuum pumps
And the volume ratio of air storage tank to mold cavity is not less than 200:1.
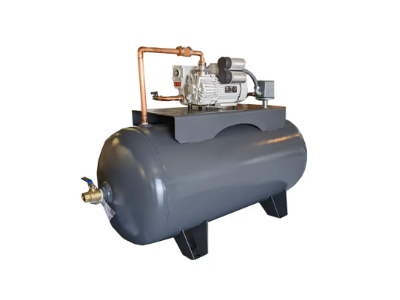
Vacuum valve
Vacuum valves are mechanical and hydraulic, and the mechanical vacuum valve has a long pumping time, high vacuum degree and stable performance.
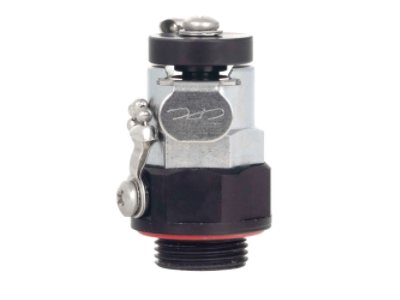
Pure mechanical vacuum valve
Suitable for cold chamber die-casting, using alloy molten kinetic energy to close, simple structure, low cost, but poor mobility and matching.
Rotary Vacuum Valve
Creates a closed exhaust channel when closing the mold, and is suitable for applications that require precise control of the exhaust time.
Pre-Pumping Valve
Drains the gas from the hose before the injection starts, especially effective for cold chamber die casting.
Three-dimensional quenching exhaust valve
By increasing the cross-sectional area of the exhaust channel, the pumping speed is increased.
Which is suitable for occasions that require high-efficiency exhaust.
Location of the vacuum valve
A vacuum valve is set at the point where the alloy melt is last filled in order to pump out as much gas as possible.
In the design process, consider the reasonable setting of exhaust channels and exhaust points on the mold to increase the flexibility of exhaust and the simplicity of exhaust channels.
Measuring device
The measuring device monitors the vacuum level in the chamber in real time.
These devices may include pressure gauges, sensors, etc., that provide feedback and adjust the operating status of the vacuum system.
Pneumatic controls
Pneumatic controls are used to automate the control of various components of the vacuum system.
Such as the opening and closing of vacuum pumps and vacuum valves, to achieve precise venting operations.
PLC touch screen operation device
PLC (programmable logic controller) combined with touch screen operation interface.
So that users can easily set and monitor the parameters of the vacuum system to achieve accurate control of the vacuum process.
Application in vacuum controller
In the design of vacuum controller, the capacitive touch screen is used as the human-computer interaction interface.
which can make the operation more intuitive and convenient.
The user can set the vacuum target value, heating time, temperature value and other parameters directly on the touch screen.
And through the touch screen, the parameters in the vacuum furnace are monitored in real time, such as the vacuum degree.
The actual current of the heater, the voltage and the flow rate of the circulating water cooled by the vacuum sealing ring.
Die-casting model core pin cooling control system
The core pin cooling control system based on PLC and touch screen technology .
Control the working temperature of the small core pin of the die-casting mold.
The system uses high-pressure cooling water and blowing compressed air to control the temperature of the core needle, and uses cooling water in a closed circulation method.
The hardware design adopts the “PLC touch screen” control scheme, with PLC as the host computer.
Combined with embedded touch screen and A/D conversion module to form the core of the whole system.
The software design applies a touchscreen configuration interface in combination with a PLC control program.
The production application shows that after adopting this system.
The temperature fluctuation of the core needle is small, and the service life is greatly extended.
The quality of castings has been improved, and the scrap rate has been reduced to less than 2%.
Vacuum pump control program
PLC and touch screen are used to realize stable monitoring and control of vacuum pump operation.
The touch screen operation interface includes pressure monitoring, pump start and stop control, alarm information display and other functions.
Among them, the pressure monitoring interface displays the pressure change of the pump in real time.
The start-stop control interface of the pump realizes the control of the operation of the vacuum pump, and the alarm interface realizes the alarm display of the abnormal state of the pump operation.
Exhaust Elements
Exhaust elements include a series of mechanical vacuum valves that are used to remove gases and other impurities from the mold cavity during the die casting process, improving the quality of the casting.
Cooling blocks
In some cases, cooling blocks have been developed to meet market needs in order to accommodate the requirements of low-end products and investment budget constraints.
The cooling block has a large exhaust capacity and is suitable for cold and hot chamber high-pressure die casting processes for non-ferrous metals such as aluminum, magnesium and zinc.
Haichen’s vacuum machine
Haichen can adjust the design of the vacuum machine according to different die casting needs, and can customize a variety of configurations according to customer needs.
Such as vacuum from 8 groups to 16 sets of molds, single injection barrel to double injection barrel evacuation and thimble chamber vacuuming to flexibly respond to die casting needs of different sizes and complexities.
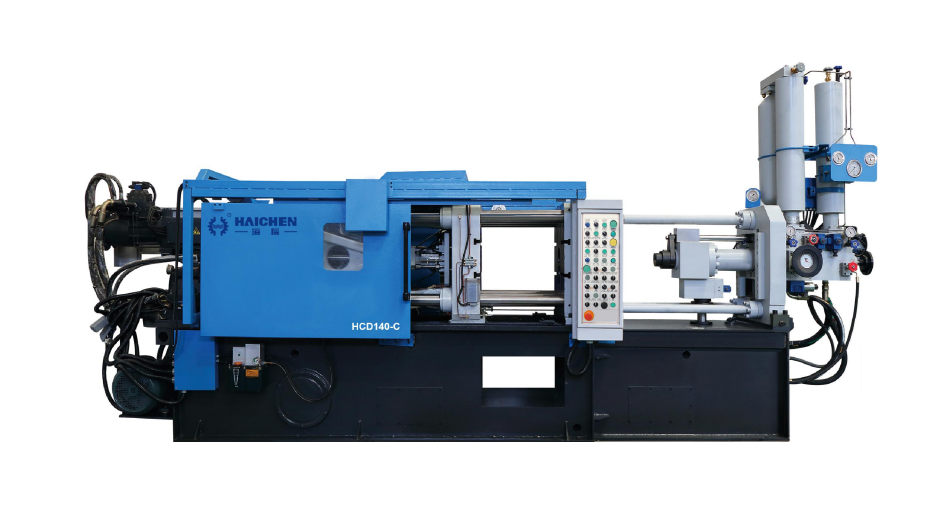