Die Casting Design 10 Concepts including:
- Material selection
- Stiffener setting
- Wall thickness uniformity
- Local extrusion process
- Improved gating systems and cooling measures
- Mold temperature and parameter optimization
- Rounded and chamfered design
- Rounded corner design
- Dimensional tolerances and accuracy
- Handling of internal features
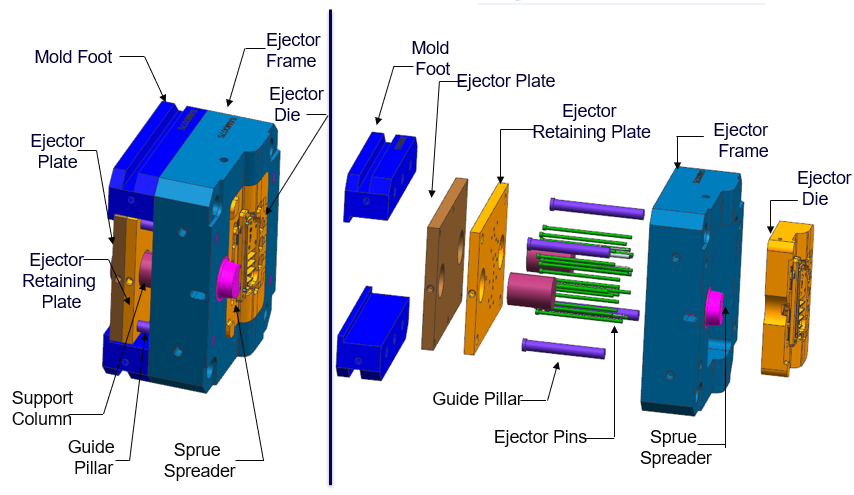
Material selection
Choosing the right die casting alloy is the basis for a successful design.
Commonly used die casting materials include aluminum, zinc, and magnesium alloys, each with specific properties.
Such as strength, weight, corrosion resistance, and thermal conductivity.
When choosing a material, consider its compatibility with the product function.
aluminum alloy
Aluminum alloys are widely used in automotive, electronics, aerospace and medical fields.
Because of their light weight, high strength, good thermal conductivity and corrosion resistance.
Common types of aluminum alloys are ADC7, ADC10, ADC12, etc.
Al-Si alloy has good crystallization temperature interval and low linear shrinkage coefficient.
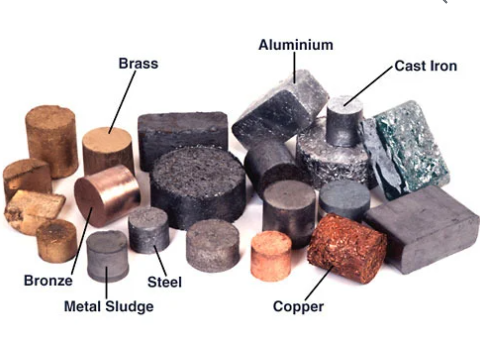
Magnesium alloy
Magnesium alloys, known for their low weight, are suitable for large structural parts molds and products.
And has a wide range of applications in aerospace, military and automotive fields.
Common magnesium alloy models include AZ91D and AZ80M.
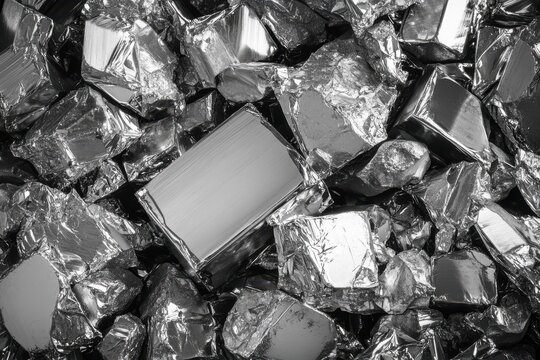
Zinc alloy
Zinc alloys, known for their low melting point and high corrosion resistance.
Making them suitable for the manufacture of lightweight components such as toys, lamps and decorations.
The high ductility and impact strength of zinc alloys also make them useful in the manufacture of complex components.
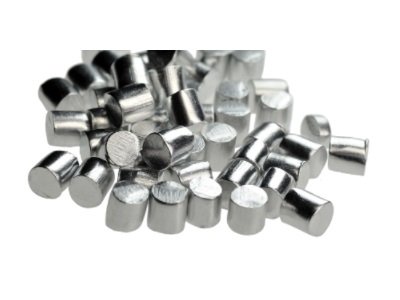
Wall thickness uniformity
Maintaining consistent wall thickness of castings is critical, as uneven wall thickness can lead to poor filling and internal defects such as porosity and cracks.
Uniform wall thickness helps ensure the stability and repeatability of the casting.
Uniform wall thickness design
In the design stage, try to make the wall thickness of the die casting the same everywhere to avoid sudden changes in wall thickness.
If different wall thicknesses are necessary, a gentle transition design should be used.
Stiffener setting
Adding stiffeners to thick walls can not only increase rigidity and strength.
But also help the alloy flow smoothly and reduce defects such as shrinkage holes.
Porosity and cracks caused by excessive concentration of alloys.
The stiffeners should be designed to avoid straight long ribs to prevent internal stress and deformation.
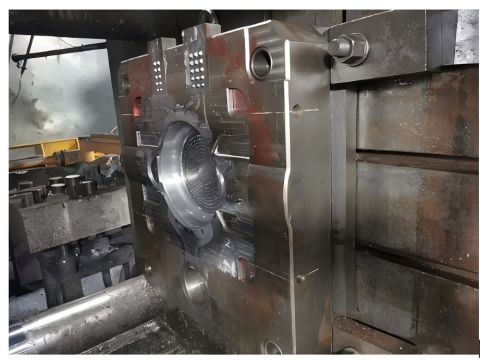
Local extrusion process
For die castings with complex shapes and uneven wall thicknesses.
A local extrusion process can be used to apply pressure to the thick walls during the solidification process of the castings.
To force the shrinkage and porosity defects to eliminate shrinkage porosity defects.
Improved gating systems and cooling measures
By improving the gating and riser system, the whole casting sequence is facilitated.
Increase cooling and water spraying measures in thick parts that are prone to shrinkage porosity, such as the corners of castings.
Add cold iron and cold copper, in the core of the thick-walled part.
This increases the cooling rate and avoids shrinkage and porosity.
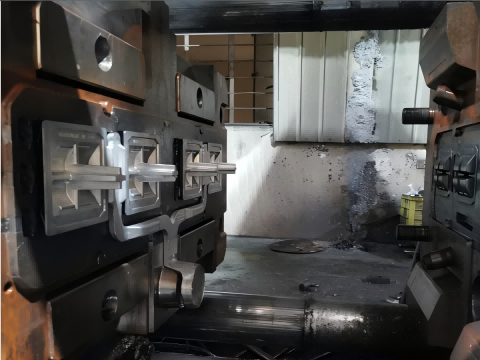
Mold temperature and parameter optimization
Ensure uniform mold temperature and avoid uneven plastic filling due to uneven mold temperature.
At the same time, the parameters are correct to prevent setting too early or too late.
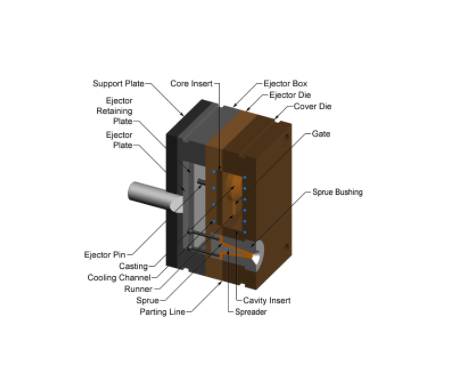
Rounded and chamfered design
Adding fillets and chamfers to the design can effectively reduce stress concentrations, avoid cracks, and simplify mold manufacturing.
For zinc, chamfering of 0.5º , and for aluminium it is 1º-2º.
Rounded corner design
Scope of application
In die castings, all wall-to-wall joints (including right, acute or obtuse angles) should be designed with rounded corners except for the mold parting surface.
Radius selection
The radius of the fillet should generally not be less than 0.5mm, and the maximum should not exceed half of the wall thickness.
For example, for zinc alloys, the minimum corner radius is 0.5mm, while for aluminum, magnesium alloys it is 1.0mm.
The exact value can be adjusted according to the type of alloy.
Purpose:
Rounded corners help the metal flow smoothly, reduce eddy currents or turbulence.
Avoid cracks caused by stress concentrations, and obtain a uniform coating when plating or coating.
Chamfered design
Purpose:
The chamfer design can reduce turbulence in the metal flow, help the casting to demold smoothly, reduce friction and strain, and thus extend the life of the mold.
Application
Add a large number of chamfers to the surface parallel to the direction of the part pop-up, which will help the part pop out.
Best practices for different materials
Zinc alloy
The radius of the fillet is generally 1/2 of the wall thickness ≤R≤ wall thickness to avoid cracks and overly loose shrinkage.
Aluminum alloy
The radius of the fillet is usually not less than 1mm, and the minimum is 0.5mm, depending on the type of alloy.
Copper alloy
The radius of the fillet is usually 1.5mm.
Stiffener design
The strength and rigidity of the casting can be improved through the rational design of stiffeners.
And at the same time, shrinkage and deformation can be prevented.
The stiffeners should be designed to avoid being too thin locally to enhance the overall performance of the part.
Demoulding slope
To ensure that the casting ejects smoothly from the mold, a certain slope or slope is given to the mold features, usually 1-2 degrees.
This helps to reduce friction and extend mold life.
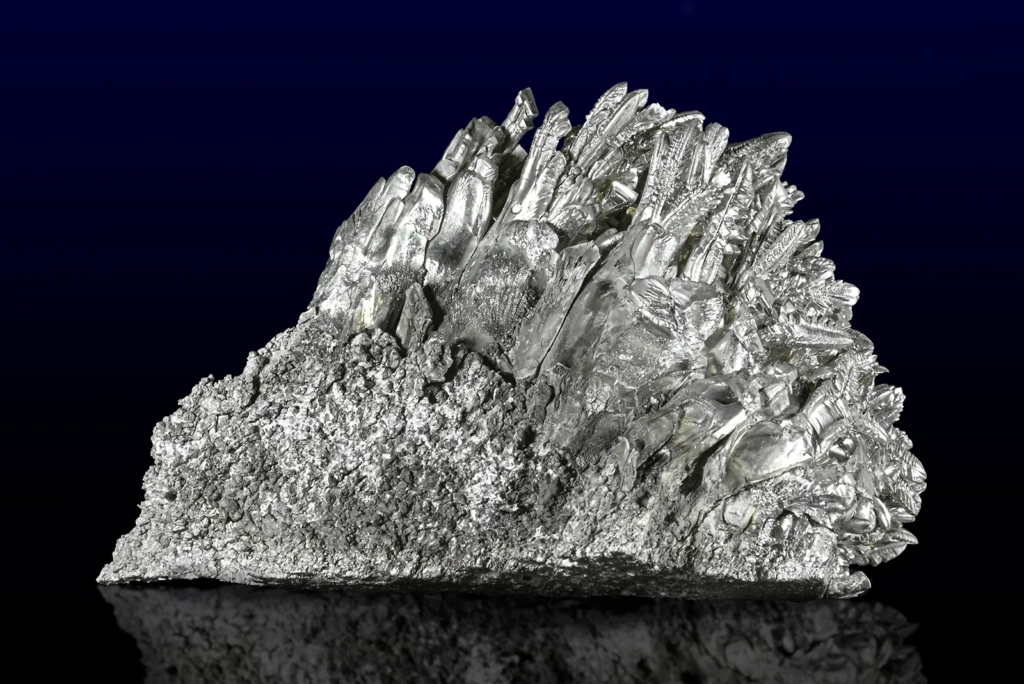
Selection of parting surfaces
Reasonable selection of parting surfaces can simplify the mold structure and ensure the quality of castings.
The position of the parting surface affects the visibility of the final product and therefore needs to be carefully considered.
Casting slope
Casting slopes help reduce friction and make castings easier to remove from the mold while extending mold life.
Handling of internal features
Internal features should be formed by special operations to avoid use in die casting designs to reduce mold complexity and cost.
Dimensional tolerances and accuracy
Reasonably determine dimensional tolerances and avoid excessively strict tolerance requirements to reduce production costs.
Final processing needs
Difficult high-precision features that require final processing to reduce material removal and avoid exposing porosity.
The die casting design process ensures the quality and production efficiency of the product, and the above ten concepts emphasize the factors.
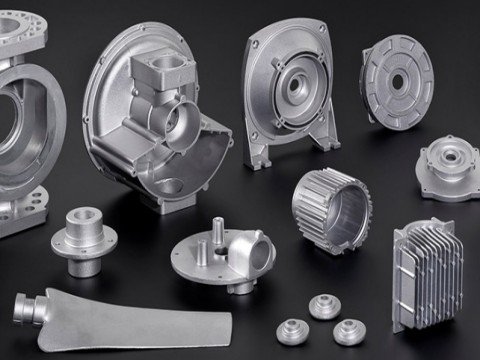
Haichen‘s die casting experience
Best practices for dimensional tolerance and precision control of die castings include comprehensive control from mold design to post-processing.
By strictly controlling the mold material, process parameters, mold temperature and post-treatment process.
And using precision measurement tools for frequent inspection and monitoring.
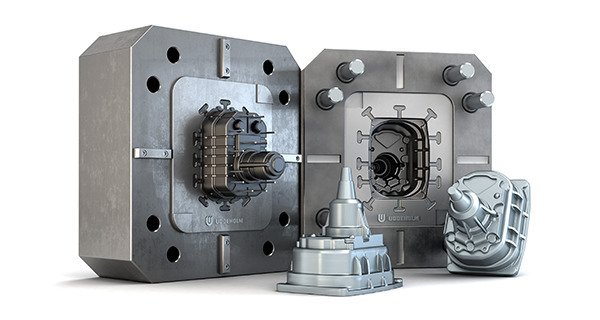