The production steps of Aluminum pot and pan include nine main links from raw material preparation to die-casting until the completion of packaging:
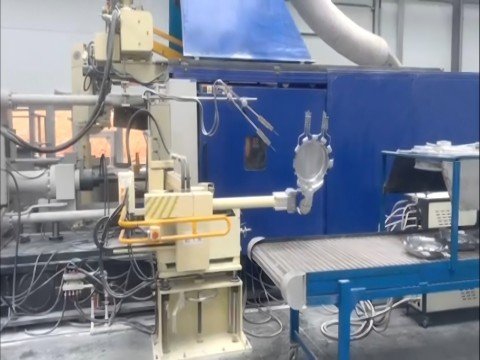
- Raw material preparation
- Melting and die-casting
- Customised aluminium pot moulds
- Trimming and moulding
- Heat treatment and annealing
- Surface treatment and Teflon coating
- Installation of fittings
- Quality control and inspection
- Packaging and Distribution
Raw material preparation:
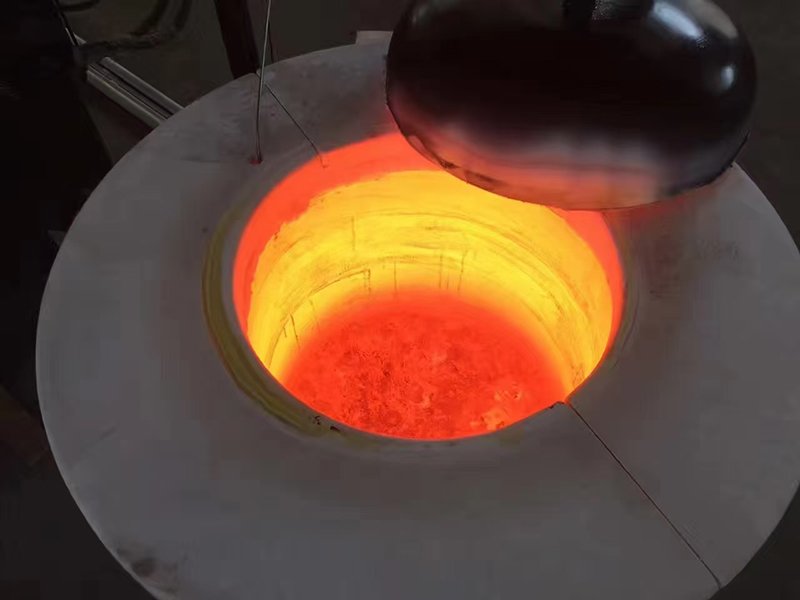
Select aluminium alloy blocks with uniform density, good thermal conductivity and condensation properties as raw materials.
Melting and die-casting:
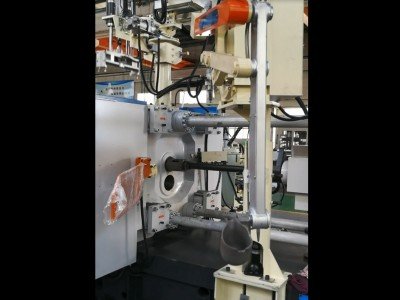
Melt the aluminium alloy block into liquid, and then press it into the mould to form aluminium pot by cold chamber die casting machine.
Custom aluminium pot moulds:
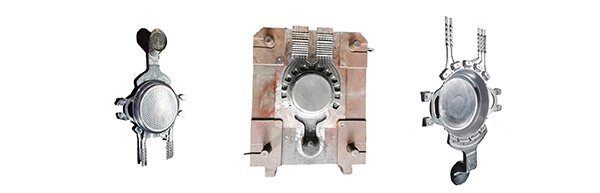
Moulds are made according to design drawings, usually made of steel and divided into two parts: cavity and core.
Trimming and forming:
The external runners and packings of the aluminium pots are trimmed using a hydraulic trimming machine, and polished and regularised using a polishing machine.
Heat treatment and annealing:
Heat treat aluminium pans to improve mechanical properties and reduce internal stresses.
Surface treatment and teflon coating:
A thin oxide layer is formed by grinding, polishing and anodising, followed by a Teflon coating to increase durability and non-stick properties.
Mounting accessories:
Configure and attach accessories such as handles, lids, etc. according to different aluminium pan product applications.
Quality control and inspection:
Strict quality checks are carried out on each aluminium pan to ensure that it meets the standards for size, surface finish and overall quality.
Packaging and Distribution:
After manufacture you will need workers to pack finished aluminium pans are carefully to prevent damage during transportation and storage.
These steps ensure efficient and high quality production of aluminium pans from raw material to finished product.
Die casting production steps for Aluminum pot
Aluminium alloy pot die casting production steps mainly has five steps from melting to post-treatment:
- Aluminium alloy melting and heat preservation
- Aluminium alloy pot mould preparation
- Aluminium alloy pot die-casting moulding
- Removing the mould and taking out the aluminium alloy pan
- Aluminium alloy pot follow-up treatment
Aluminium alloy melting and holding:
It is obvious that you need to heat the ingot or aluminium alloy to a high temperature of 600℃-750℃ to melt it into liquid aluminium.
Aluminium alloy pot mould preparation:
Before die casting, clean the mould and spray the mould release agent to reduce the adhesion between the die casting and the mould, so as to facilitate the release of the mould.
Aluminium alloy pot die-casting moulding:
The cold chamber high-pressure die-casting machine injects molten aluminum into the mold cavity at high pressure and speed, and cools and solidifies it under high pressure.
Mould release and take out the Aluminum pot:
After finishing the die-casting process, open the mould and take out the moulded castings.
Aluminium alloy pot subsequent processing:
The castings are trimmed, deburred, cleaned and sandblasted to improve their surface quality and performance.
These steps ensure the high quality and durability of aluminium alloy pots.
Aluminum pot die-casting mould customization steps
Aluminium alloy pot die-casting mould custom steps from design to production has six key links:
- Aluminium alloy pot die casting mould design and planning
- Drawing review and drawings
- Material preparation and processing
- Assembly and testing
- Trial mould and optimization
- Production and maintenance
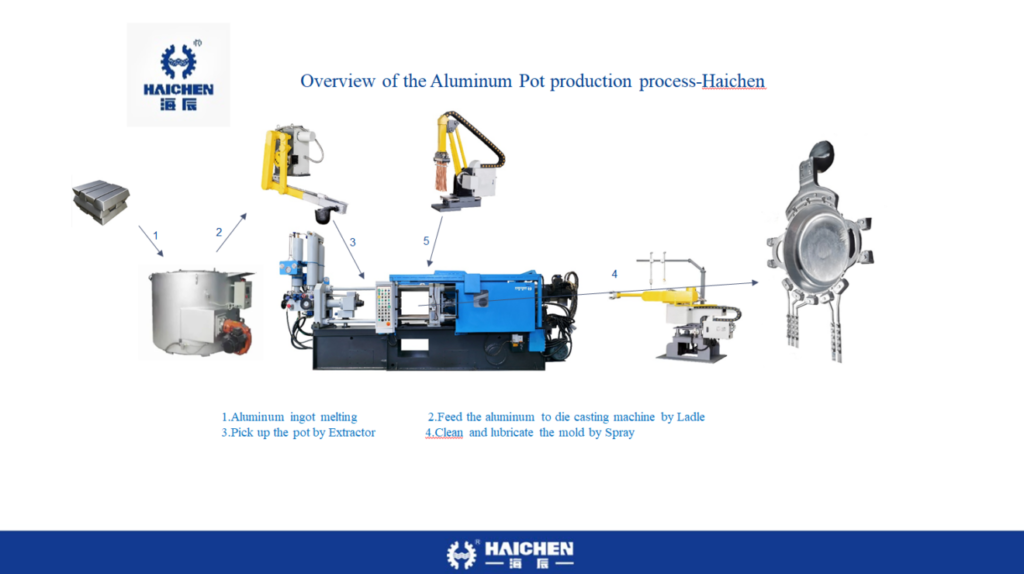
Aluminium alloy pot die casting mould design and planning:
Then the first step is to design the mold according to the requirements of the aluminum pot die-casting mold.
Simply put, these processes include product parting, runner planning, slider, ejection mechanism, exhaust and slag removal design.
Drawing review and drawings:
Under normal circumstances, we first use the industrial design software Soildworks to complete the product modeling. Draw the drawings. Print them into a book, and then send the design draft to the customer for review
Draw the designed aluminium alloy pot die-casting mould structure into 3D and 2D drawings and review.
Material preparation and processing:
Including mould frame processing (such as playing number, A/B plate processing, panel processing, etc.).
s a resultMould core processing (such as flying edge, rough grinding, CNC processing, etc.) and mould parts processing (such as slider, compression block processing, etc.).
Assembly and inspection:
After completing the previous process, the mould is assembled and tested to ensure the precision and function of each part.
Trial mould and optimisation:
Install the aluminium alloy pot die-casting mould on the die-casting machine for trial mould.
Check whether the parameters such as runner system, positioning, pressure and temperature meet the requirements.
If there is any problem need to adjust the mould structure and remanufacture.
Production and maintenance:
After the trial mould qualified, aluminium pot die-casting mould can be put into production.
And in the production process of regular maintenance to ensure the long-term use of the mould.
These steps ensure the quality and production efficiency of aluminium alloy pot die-casting mould.
Heat treatment and annealing steps for aluminium pots
The heat treatment and annealing steps for aluminium alloy pans usually include the following methods:
- Homogenising annealing:
- Complete annealing
- Rapid annealing
- Quenching and ageing
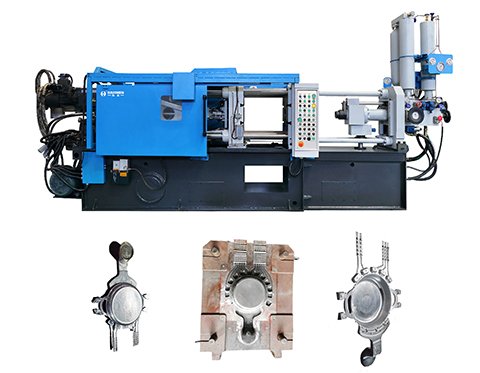
Homogenising annealing:
Heat the aluminium alloy pot to 480-495°C, hold for 12-14 hours, and then furnace cool.
Complete annealing:
Heat the aluminium alloy pot to 390-430°C, hold for 30-120 minutes, furnace cool to 300°C and then air-cool.
Rapid annealing:
Heating aluminium alloy pot to 350-370 ℃, holding time 30-120 minutes, air cooling.
Quenching and aging treatment:
Aluminium alloy pot quenching temperature is 495-505℃.
Water cooling; artificial aging temperature of 185-195 ℃, holding time 6-12 hours.
Air cooling; natural ageing is carried out at room temperature for 96 hours.
These steps are aimed at optimising the properties of the aluminium pot, such as improving strength, hardness, toughness and corrosion resistance.
Haichen has many years of experience in manufacturing die casting lines for aluminium Pot and pans.
The production process for aluminium pots includes several steps from the processing of raw materials to the finished product.
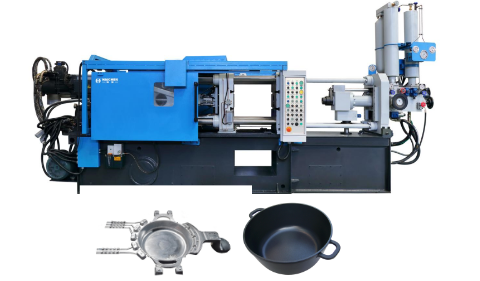
For example, mould design, machine selection, die casting, welding, assembly, turning and polishing.
In addition, Haichen has gained experience in aluminium pot production lines for factories all over the world.
Haichen has extensive experience and expertise in the production steps of aluminium pots.