Cold die casting process involves injecting molten metal under high pressure into a reusable mold cavity to form metal parts of precise dimensions and smooth surfaces.
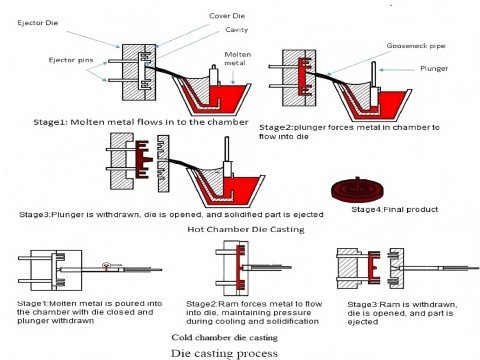
Cold die casting process
Cold die casting, also known as cold chamber die casting, is a manufacturing process used to produce high-quality metal parts with complex shapes and tight tolerances. Here is a step-by-step overview of the cold die casting process:
Preparation of the Die
Die Design and Fabrication: The first step involves designing and creating the die, which is a mold made of high-strength steel. The designer must precisely design the die to match the desired shape, size, and tolerance of the final part.
Mounting the Die: The operator mounts the die onto the cold chamber die casting machine. The engineers equipped the machine with clamping units to securely hold the die in place.
Melting the Metal of cold die casting process
Operators typically melt a low melting point alloy such as aluminum, magnesium, or zinc in a separate furnace.
The furnace is not attached to the die casting machine, which allows for the handling of metals with high melting points.
Transfer of Molten Metal
After the metal melting, operators transfer it to the cold chamber die casting machine using a ladle. Preheating the ladle prevents the metal from solidifying prematurely.
Injection into the Die
The molten metal is poured into a shot sleeve within the machine. A hydraulically operated plunger then forces the metal into the die cavity at high pressure, typically ranging from 2,000 to 20,000 psi.
This high-pressure injection ensures that the metal fills the mold completely and takes on the desired shape.
Cooling and Solidification of cold die casting process
The metal is allowed to cool and solidify within the die after it is injected. The cooling process is crucial as it affects the final properties and dimensions of the part. Proper cooling channels in the die help manage the cooling rate.
Ejection of the Part
Once the metal has solidified, the die is opened, and the part is ejected using ejector pins. The part is then removed from the machine for further processing or inspection.
Post-Casting Operations and Quality Control
The cast part may undergo additional processes such as trimming, machining, or surface treatment to meet specific requirements.
Quality control personnel perform checks to ensure that the part meets the desired specifications.
Haichen cold die casting machine supplier
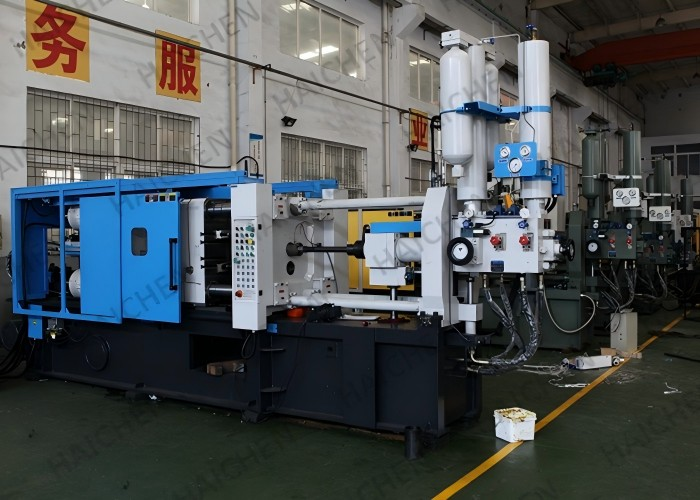
Haichen is a cold chamber die casting machine factory located in Ningbo, China, Besides, we also supply hot chamber die casting machine and die casting auxiliary equipments.
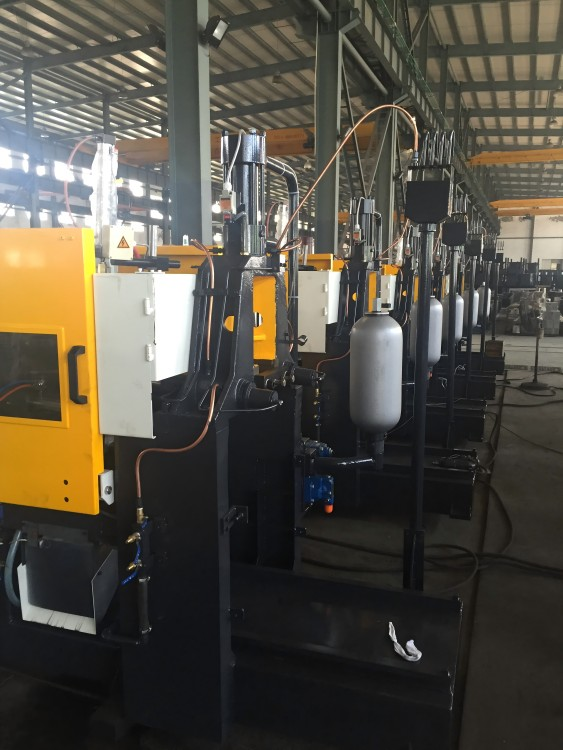
The advantage of Haichen cold die casting machine
Experience and Expertise
Over 20 Years of Experience: With more than two decades in the die casting machine industry, Haichen has accumulated extensive experience and expertise.
This experience enables them to provide reliable and efficient solutions tailored to specific customer needs.
Global Reach: Haichen exports its machines to many countries, demonstrating the company’s ability to meet diverse market demands and adapt to different local requirements.
Cost-Effectiveness and Efficiency
Energy-Efficient Solutions: Haichen offers energy-saving options such as fixed pump and servo systems, which help reduce energy consumption and lower operational costs.
Cost-Effective Pricing: As a manufacturer, Haichen sells directly to customers, eliminating middlemen and providing competitive pricing.
This makes their machines an affordable option for businesses looking to invest in high-quality die casting equipment.
Cold die casting is particularly suitable for producing complex, lightweight parts with high precision and dimensional accuracy. The technology widely uses in industries such as automotive, aerospace, and electronics.