The Cold Chamber Die Casting Process Steps include die preparation, metal melting, injection, cooling, ejection, and post-processing.
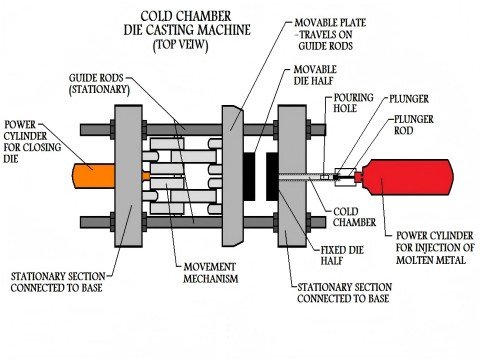
Die casting is a highly efficient and precise manufacturing process used to produce complex metal parts with excellent dimensional accuracy and surface finish.
Cold Chamber Die Casting Process Steps
The cold chamber die casting process particularly suits metals with high melting points, such as aluminum and magnesium alloys. It allows manufacturers to produce complex parts with excellent dimensional accuracy and surface finish. Here are the key Cold Chamber Die Casting Process Steps:
1. Preparation of the Die
The first step is to prepare the die, which is the mold that will shape the final part. Dies are typically made from high-quality tool steel and designed to withstand the high pressures and temperatures involved in the die casting process. Operators carefully clean and lubricate the die to ensure that the molten metal can flow smoothly and to facilitate easy ejection of the finished part.
2. Metal Preparation
The metal melts in a separate furnace, usually outside the die casting machine. This differs from the hot chamber process, where the metal melts within the machine itself. After melting, we transfer the molten metal to the shot chamber of the die casting machine. This step is crucial because it allows for better control over the melting process and reduces the risk of contamination.
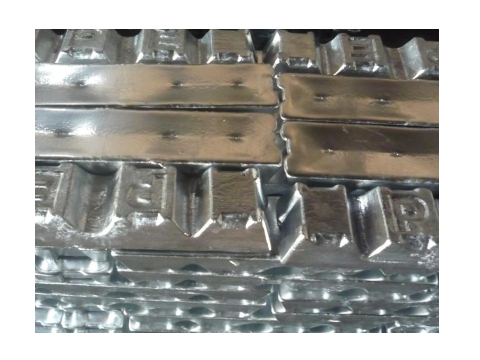
3. Injection of Molten Metal
The molten metal is injected into the die cavity under high pressure. The pressure can range from a few hundred to several thousand psi, depending on the size and complexity of the part. We carefully control the injection speed to ensure that the metal fills the die cavity quickly and completely, minimizing the formation of air pockets and other defects.
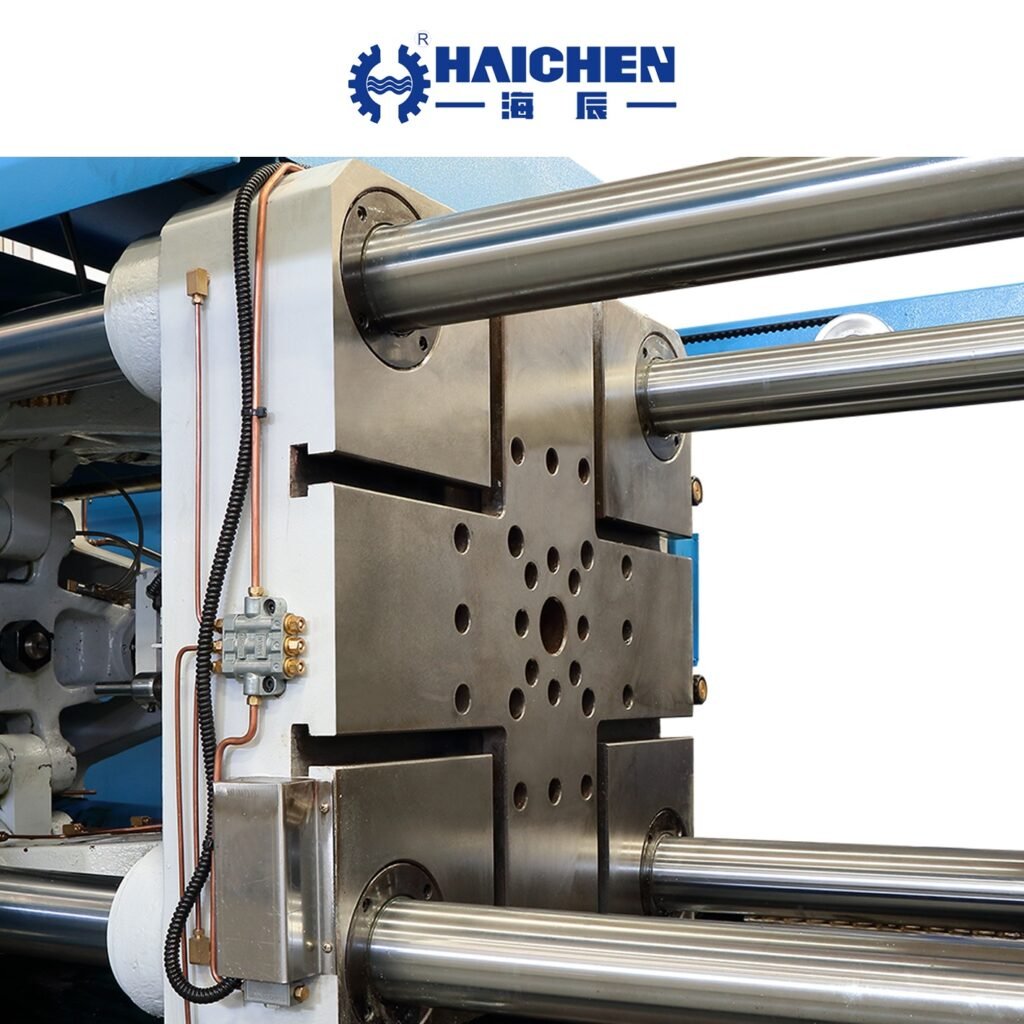
4. Cooling and Solidification
Once the molten metal is injected into the die, it begins to cool and solidify. The die, designed to cool the metal rapidly, helps achieve a fine-grained microstructure and enhances the mechanical properties of the part. We carefully control the cooling process to ensure uniform solidification and prevent defects such as shrinkage or porosity.
5. Ejection of the Part
After the metal has solidified, the die opens, and ejector pins carefully push the part out. Carefully design the ejector pins to remove the part from the die without causing damage. After that, we inspect the part for defects and, if necessary, perform secondary operations such as trimming, machining, or surface treatment.
6. Post-Processing
The final step in the cold chamber die casting process is post-processing. This can include trimming excess material, machining critical dimensions, and applying surface treatments such as painting or plating. These steps are essential to ensure that the final part meets the required specifications and quality standards.
HAICHEN Die Casting Machine Manufacturer
HAICHEN is a leading manufacturer of die casting machines, known for its innovation and commitment to quality. With years of experience in the industry, HAICHEN offers a wide range of cold chamber die casting machines designed to meet the needs of both small and large-scale production.Our machines are equipped with advanced features such as precise control systems, high-speed injection capabilities, and energy-efficient designs.
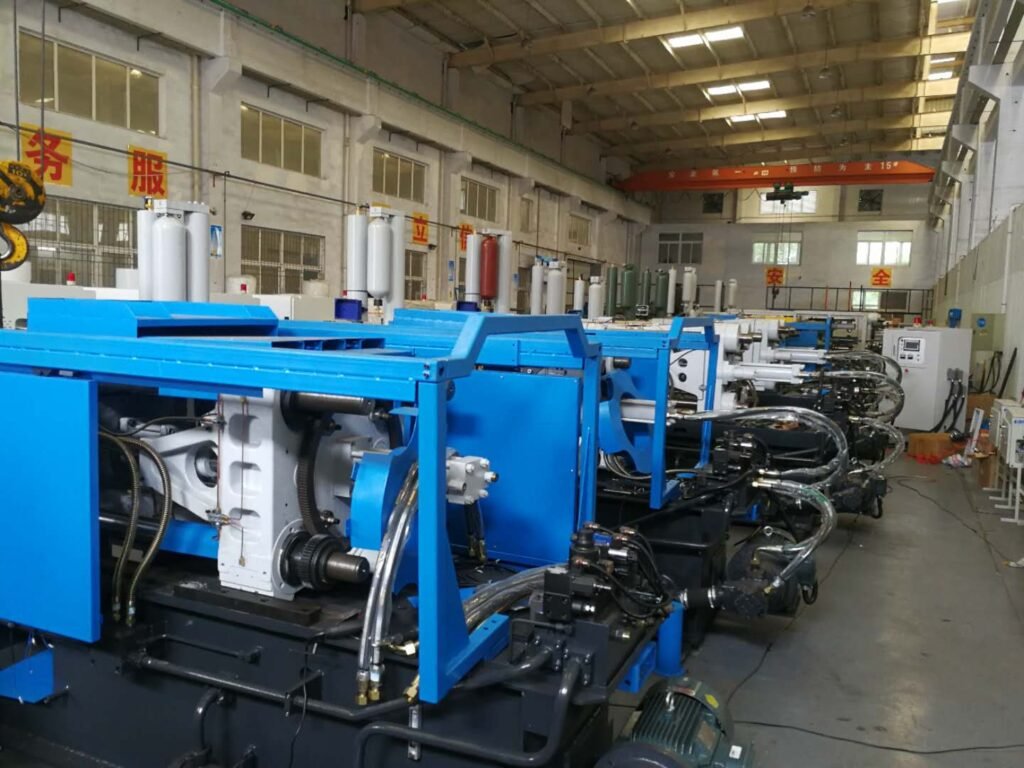
The Cold Chamber Die Casting Process Steps are essential in manufacturing high-quality metal parts with precision and efficiency. From die preparation to post-processing, each step plays a vital role in ensuring the final product meets the highest standards.