Aluminum Die Casting for Crankcases includes material selection and performance, die casting process, Design and Optimization and so on.
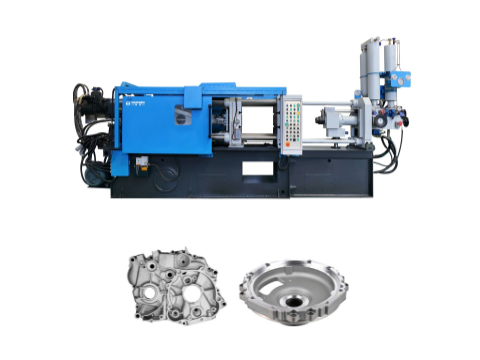
The application of aluminum die casting in crankcase manufacturing has significant advantages and a wide range of applications.
1. Aluminum Die Casting for Crankcases: material selection and performance
Aluminum alloys are ideal materials for crankcase manufacturing due to their light weight, high strength and good corrosion resistance. AS41A alloy (containing 4% aluminum and 1% silicon) has better creep strength at high temperatures than other magnesium alloy die-casting materials. And it has good elongation, yield strength and tensile strength. So it widely uses in crankcases of air-cooled automobile engines.
High-purity aluminum alloys (such as A356) are also commonly used in crankcase manufacturing. Their excellent mechanical properties and microstructure further improve through improved processes (such as direct water cooling).
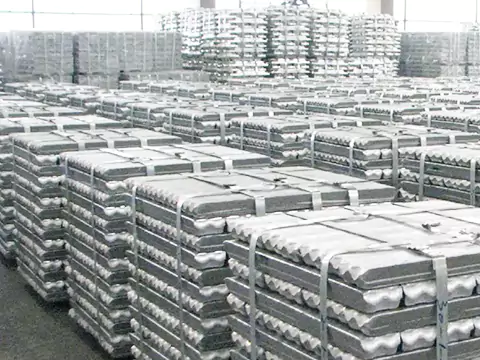
2. Aluminum Die Casting for Crankcases: die Casting Process
Aluminum die casting is an efficient and precise manufacturing process that uses high pressure to inject molten aluminum into a prefabricated mold, rapidly cools and solidifies to form parts. This process is particularly suitable for producing thin-walled, complex-shaped parts.
High pressure die casting (HPDC) is the most commonly uses method in aluminum die casting, capable of producing parts with high dimensional accuracy and good surface quality. In addition, low pressure die casting (LPDC) and gravity casting are also use for specific applications, such as steering knuckles.
3. Aluminum Die Casting for Crankcases: Design and Optimization
The design of the crankcase needs to consider its structural strength and durability. Through finite element analysis (FEA) and numerical simulation (NI), the design can optimize to improve the performance of the parts.
During the design process, should pay special attention to the design of the oil channel to avoid oil leakage caused by casting defects.
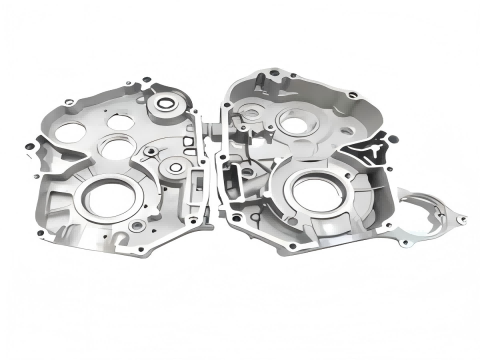
4. Manufacturing process
Aluminum die-casting molds for crankcases usually made of high-quality steel and are precision machined to ensure the dimensional accuracy of the mold.
Mold design and manufacturing are the key to the success of aluminum die casting. The application of modern mold design tools and CNC processing technology makes mold manufacturing more efficient and accurate.
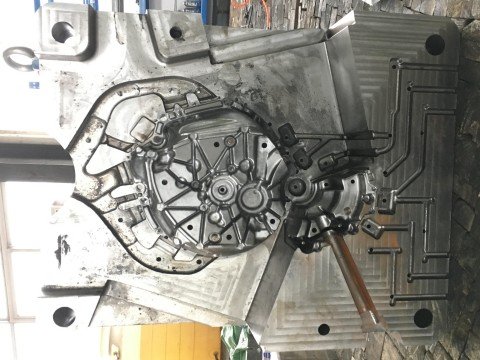
Above all, aluminum die casting technology has significant advantages in crankcase manufacturing, which can meet the needs of modern industry for high performance, light weight and low cost. The performance and reliability of crankcases can further improve by optimizing material selection, process design and mold manufacturing.
Haichen die casting machine
Haichen is one Chinese die casting machine manufacturer for more than 10years. We produce both high pressure cold chamber die casting machine and hot chamber die casting machine. They have durable and highly precise features.
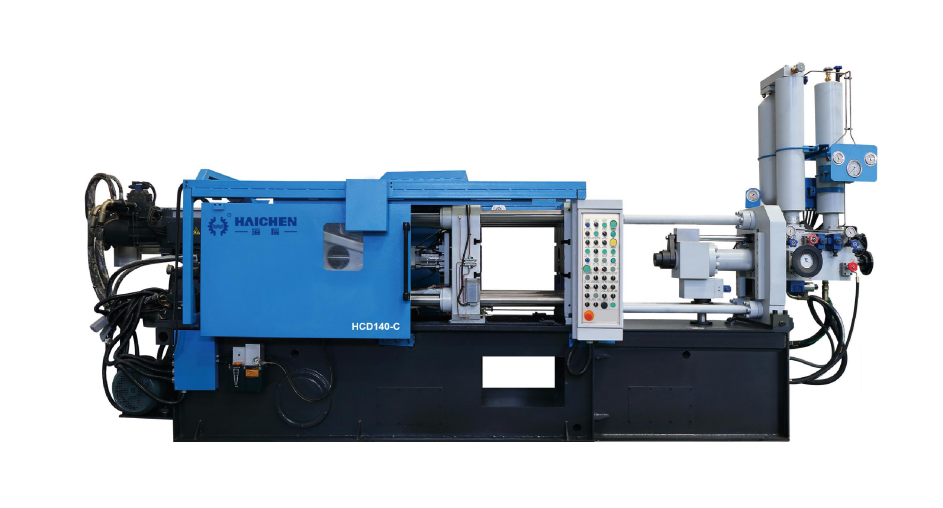
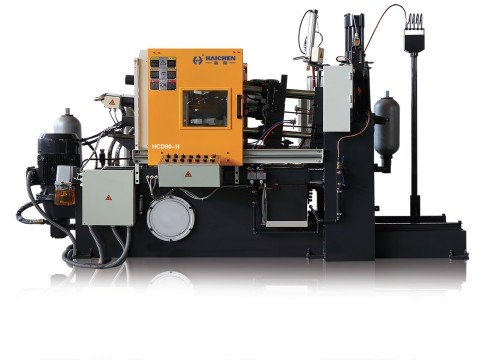
Haichen also produce die casting machine auxiliary equipment. Such as conveyor, vacuum machine, mold temperature controller, industrial robot, sprayer and so on.
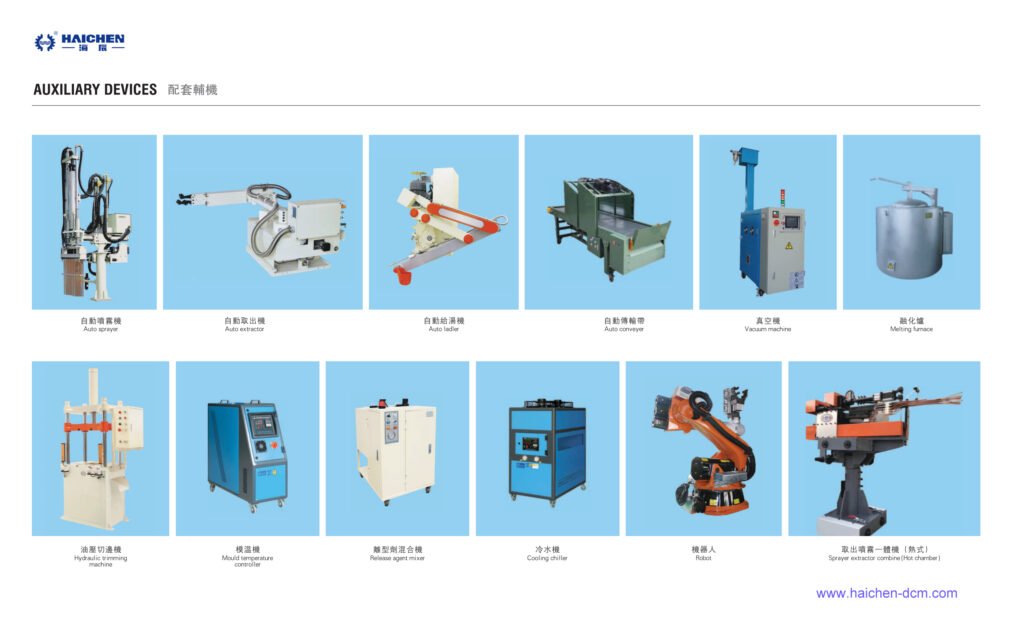
We supply cold chamber and hot chamber die casting machine spare parts.
Welcome contact us.