Common Products Created from Die-Casting
Die-casting is a versatile manufacturing process used to produce high-precision, durable metal parts across industries. Below are key products made via die-casting, categorized by sector:
1. Automotive Industry
- Engine Components: Cylinder heads, engine blocks, piston housings.
- Transmission Parts: Gearbox housings, clutch plates, torque converter components.
- Structural Components: Brackets, chassis parts, suspension components.
- Exterior/Interior Parts: Door handles, wheel rims, dashboard frames.

Lightweight aluminum/zinc alloys reduce vehicle weight while maintaining strength.
2. Consumer Electronics
- Housings: Laptop/phone casings, smartwatch frames, router enclosures.
- Heat Sinks: For CPUs, GPUs, and LED lighting systems.
- Connectors: USB ports, battery terminals, charging docks.
- Internal Components: Shielding plates, brackets for circuit boards.
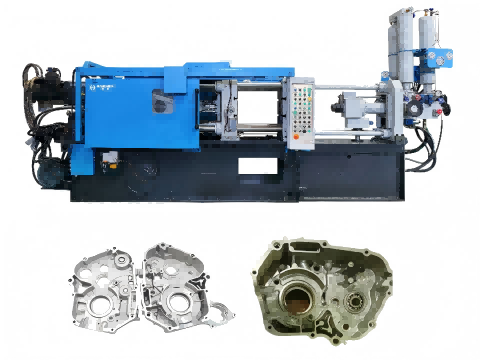
High dimensional accuracy and smooth finishes for sleek, functional designs.
3. Aerospace & Defense
- Aircraft Components: Turbine blades, landing gear parts, hydraulic system housings.
- Avionics: Radar and sensor housings, cockpit control panels.
- Drone Frames: Lightweight magnesium alloy structures.
Why die-casting? Strength-to-weight ratio critical for fuel efficiency and performance.
4. Industrial Machinery
- Pump/Valve Housings: Corrosion-resistant parts for fluid systems.
- Gearboxes: High-strength aluminum or zinc housings.
- Tooling Components: Die-cast molds, press machine parts.
Durability under high-stress conditions.
5. Household & Consumer Goods
- Appliances: Washing machine drums, refrigerator compressor parts.
- Plumbing Fixtures: Faucet handles, pipe fittings, showerheads.
- Power Tools: Drill housings, saw blades, battery casings.
- Toys: Model car bodies, LEGO-like building blocks, action figure parts.
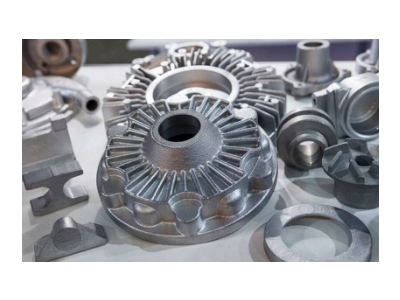
Cost-effective mass production of complex shapes.
6. Medical Devices
- Surgical Instruments: Scalpel handles, forceps, biopsy tools.
- Imaging Equipment: X-ray machine components, MRI housing parts.
- Prosthetics: Lightweight, custom-shaped joints and connectors.
Why die-casting? Precision and biocompatibility (e.g., aluminum/zinc alloys).
7. Energy & Renewable Tech
- Solar Panel Frames: Corrosion-resistant aluminum mounts.
- Wind Turbine Parts: Gearbox components, rotor hubs.
- Battery Housings: For EVs and energy storage systems.
Resistance to environmental wear and thermal stress.
Key Materials Used
- Aluminum Alloys (A380, A383): Lightweight, corrosion-resistant (common in automotive and aerospace).
- Zinc Alloys (Zamak): Excellent fluidity for intricate designs (electronics, toys).
- Magnesium Alloys: Ultra-lightweight (drones, aerospace).
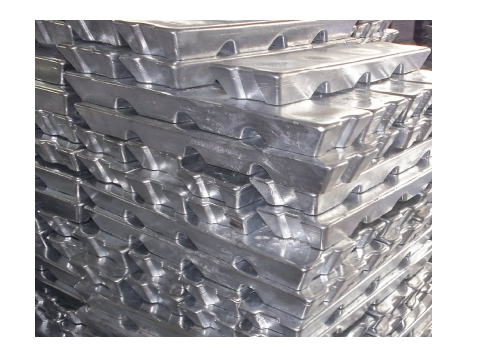
Why Choose Die-Casting?
- High Efficiency: Mass production with minimal post-processing.
- Complex Geometries: Thin walls, internal channels, and fine details.
- Cost-Effective: Low per-unit cost for large batches.
Emerging Applications
- EV Components: Battery trays, motor housings.
- 5G Infrastructure: Antenna housings, heat dissipation units.
Is die casting expensive?
Is Die Casting Expensive? A Cost Analysis
Die casting costs depend on factors like production volume, part complexity, material choice, and tooling requirements. While it can be expensive upfront for low-volume projects, it becomes highly cost-effective for mass production. Below is a detailed breakdown of costs and scenarios where die casting shines or falters.
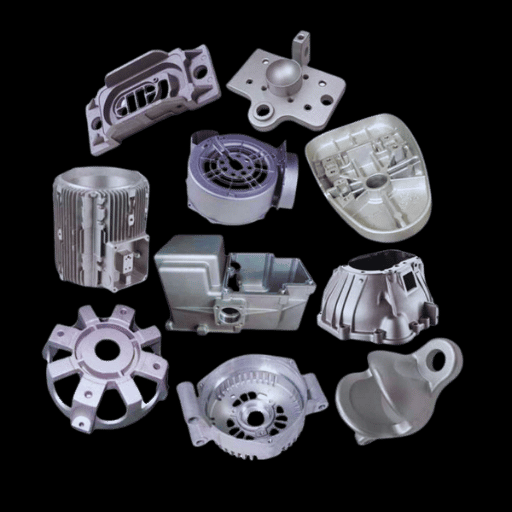
1. Key Cost Drivers
Factor | Impact on Cost |
---|---|
Tooling (Mold/Dies) | High initial cost (10,000–10,000–100,000+) for hardened steel dies. Dominates low-volume projects. |
Material | Aluminum (2–4/kg),zinc(2–4/kg),zinc(3–5/kg), and magnesium ($5–8/kg) affect per-part costs. |
Production Volume | High-volume runs (10,000+ units) reduce per-unit costs significantly. |
Part Complexity | Intricate designs (undercuts, thin walls, cores) increase tooling and cycle time costs. |
Secondary Processes | Machining, anodizing, or powder coating add 0.50–0.50–10+ per part. |
2. Cost Comparison with Other Processes
Process | Tooling Cost | Per-Unit Cost | Best For |
---|---|---|---|
Die Casting | 10,000–10,000–100,000+ | 1–1–50+ (high volume) | Mass production of complex metal parts. |
Plastic Injection Molding | 5,000–5,000–50,000 | 0.10–0.10–10+ | High-volume plastic components. |
Sand Casting | 1,000–1,000–20,000 | 10–10–100+ | Low-volume, large, simple parts. |
CNC Machining | Minimal (no molds) | 50–50–500+ | Prototypes or low-volume metal parts. |
3. When Die Casting Is Cost-Effective

- High-Volume Production (10,000+ units):
- Tooling costs amortize over many parts, driving per-unit costs down (e.g., 1–1–5 for aluminum auto parts).
- Complex Geometries:
- Thin walls, internal channels, and fine details are cheaper to cast than machine.
- Material Efficiency:
- Near-net-shape casting minimizes waste vs. machining from solid billets.
Example:
- Producing 50,000 aluminum car door handles via die casting might cost $3 per unit (including tooling).
- Machining the same part could cost $20+ per unit due to material waste and labor.
4. When Die Casting Is Expensive
- Low-Volume Production (<1,000 units):
- High tooling costs dominate (e.g., a 50,000diefor500parts=50,000diefor500parts=100 per part).
- Simple Parts:
- Basic shapes are cheaper to produce via sand casting or stamping.
- Exotic Materials:
- Magnesium alloys or specialty aluminum grades (e.g., A356-T6) raise material costs.
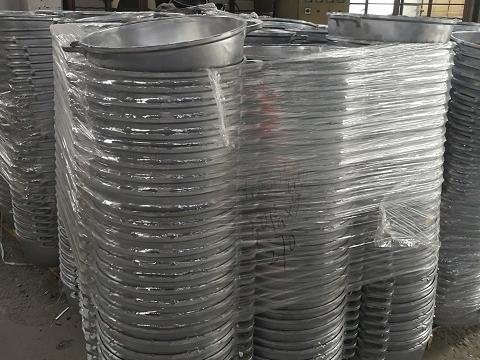
Example:
- A prototype run of 100 zinc alloy brackets could cost **150+perunit∗∗(vs.150+perunit∗∗(vs.10 via CNC machining).
5. Hidden Costs to Consider
- Design Changes: Modifying a die costs 1,000–1,000–10,000+ depending on complexity.
- Maintenance: Dies require periodic refurbishing (5–10% of initial cost annually).
- Energy: High-pressure machines consume significant electricity, adding 0.05–0.05–0.50 per part.
6. Cost-Saving Tips
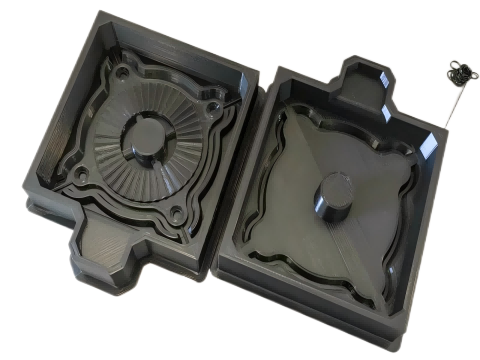
- Optimize Design: Simplify geometries, avoid undercuts, and standardize wall thickness.
- Use Multi-Cavity Molds: Produce multiple parts per cycle (e.g., 4–8 cavities).
- Choose Standard Alloys: A380 aluminum or Zamak 3 zinc are cheaper and easier to cast.
Haichen Die Casting Equipment Professional Manufacturer
Haichen is a Chinese manufacturer specializing in the R&D, production and sales of die-casting equipment. Headquartered in Ningbo, Zhejiang Province, Haichen has more than 20 years of industry experience.
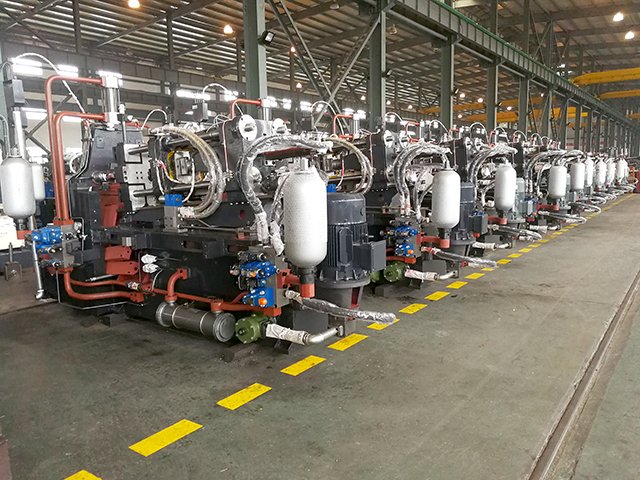
Detailed analysis of Haichen’s core competitiveness:
1. Product line and technical advantages
Cold chamber die-casting machine:
Covering a tonnage range of 90 tons to 1,600 tons, it complies with the national JB/T8083-2000 standard and the EU CE safety standard, and uses computer-aided design (CAD/CAE) and finite element dynamic analysis to optimize key components.
For example, the 880-ton aluminum radiator cold chamber die-casting machine supports high-precision production of complex radiator profiles, suitable for the automotive and home appliance industries.

Hot chamber die-casting machine:
Suitable for low-melting-point metals (zinc, lead, tin, etc.), with tonnage ranging from 15 tons to 280 tons, the design focuses on environmental protection and energy saving, and adopts advanced technologies such as multi-stage pressure control and hydraulic planetary gear adjustment to ensure the surface finish of castings and long mold life.
Servo control and intelligence:
Equipped with hydraulic components of German and Japanese brands, the four-stage injection control system (such as Siemens PLC) achieves precise injection speed and pressure adjustment, supports multi-language operation interface, and improves the level of automation.
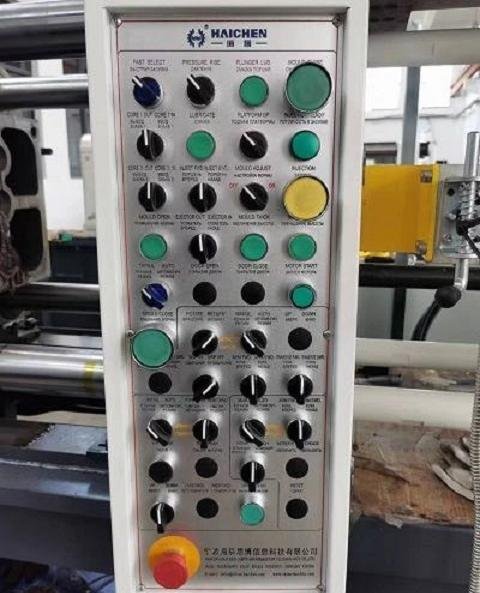
2. Application fields and market coverage
Industry application:
The products are widely used in automotive parts (such as motorcycle accessories, LED lamp housings), home appliances (such as aluminum cookware, radiators), 3C electronics, hardware products and other fields.
For example, a 200-ton cold chamber die-casting machine can produce 1.3-1.8kg aluminum alloy castings to meet precision manufacturing needs.
Global market:
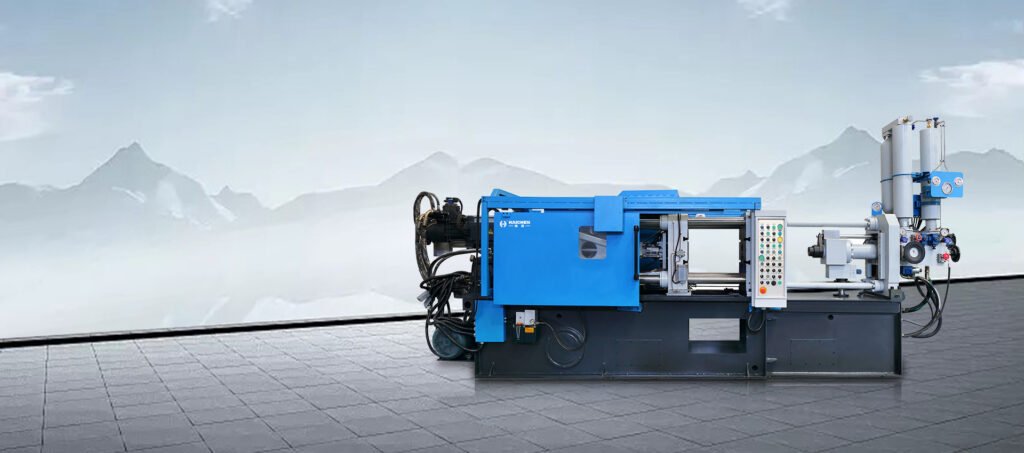
Exported to more than 30 countries or regions including India, Russia, and Mexico, especially in the Mexican automotive industry due to the growing demand for integrated die-casting technology.
3. R&D and certification
Technical certification:
Through ISO9001 quality management and CE certification, ensure that the equipment meets international safety and performance standards.
Innovation investment:
Continuous breakthroughs in vacuum casting, extrusion casting and intelligent manufacturing technologies, such as vacuum systems can reduce casting pores and improve product density.
4. Production and service capabilities
Capacity and delivery:
Annual production of 30 sets, delivery time of 15-45 days, support for customized services (such as mold design, automated supporting equipment).
Localization support:
Provide multi-language technical support and engineer on-site services to assist customers in optimizing production processes.
Die casting is expensive for prototypes or low-volume runs but highly cost-effective for mass production.
- High Volume: Automotive parts (e.g., transmission housings) cost 2–2–10 each.
- Low Volume: Custom industrial components may cost 50–50–200 each.
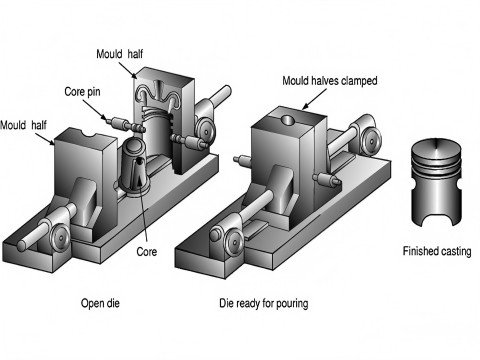
For projects requiring complex, high-volume metal parts, die casting offers unmatched efficiency and per-unit savings. For small batches, consider alternatives like CNC machining or 3D printing.
Pro Tip: Use simulation software (e.g., MAGMAsoft) to optimize designs and reduce trial-and-error costs.
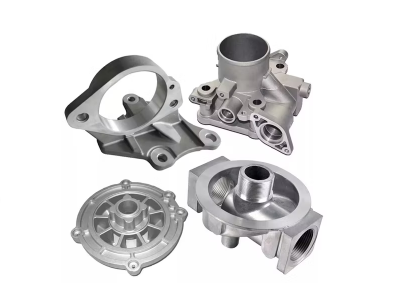
From everyday gadgets to mission-critical aerospace parts, die-casting bridges innovation and practicality, making it indispensable in modern manufacturing.