The most popular casting method is high-pressure die casting (HPDC).
Especially the integrated die casting technology that has emerged in the field of automobile manufacturing in recent years.
These two technologies have become one of the core processes of industrial manufacturing due to their high efficiency, high precision and lightweight advantages.

The most popular casting method–High-pressure die casting
Mainstream technology and core advantages
High-pressure die casting achieves efficient molding of complex geometries by rapidly injecting molten metal.
Such as aluminum alloys, magnesium alloys into molds at high pressures (typically up to 100-1000 MPa).
High precision and consistency
Produce parts with thin walls (as small as 0.5 mm) and tight tolerances (± 0.1 mm) to meet the needs of precision components in the automotive and electronics industries.
High productivity
Short cycle times (typically only a few seconds to minutes) make it suitable for large-scale production.
Such as critical components such as automotive engine blocks and transmission housings.
Lightweight and performance optimization
Aluminum alloy die castings reduce weight by 30%-50% compared to traditional steel.
While maintaining high strength, significantly improving fuel economy or electric vehicle range.
Typical application fields
Automotive industry: engine block, transmission housing, suspension arm, wheel hub, etc.
Such as the integrated rear body of Tesla Model Y is produced by a die-casting machine of more than 6000T).
Consumer electronics
Mobile phone/computer shells, radiators, connectors, etc., using the electromagnetic shielding and heat dissipation performance of die-castings.
Home appliances and industrial equipment
Washing machine motor rotors, power tool housings, etc., taking into account both light weight and durability.
The most popular casting method–Integrated Die Casting
Technological Innovation and Industry
Transformation Integrated Die Casting is an extension of high-pressure die casting.
Which subverts the traditional stamping-welding process by integrating multiple parts into a single casting through a super-large die casting machine.
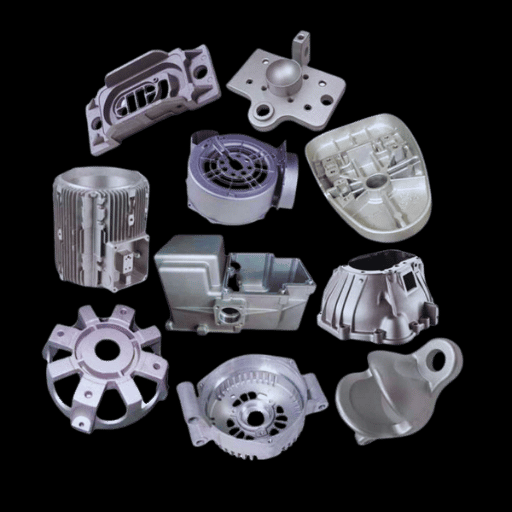
Lightweight and performance-driven
The one-piece die-cast body significantly improves safety and handling.
The weight reduction effect directly extends the range of electric vehicles.
Material Innovation Trends
Heat-free aluminum alloys
Traditional aluminum alloys require heat treatment to improve strength, but they are prone to deformation and surface bulging of castings.
The heat-free alloy directly reaches the state of high strength and high toughness after die-casting, breaking through the technical bottleneck.
Chinese companies have realized the localization of heat-free materials and broken the monopoly of foreign countries.
Magnesium alloy application extension
Magnesium alloy has a density of only 2/3 of aluminum alloy and excellent electromagnetic shielding, which is suitable for electronic equipment housings and automotive structural parts.
Exploration of composite materials
In the future, composite materials such as carbon fiber may be combined with die-casting processes to further achieve lightweight and high strength
Technical characteristics and classification of high-pressure die casting
High-pressure die casting enables rapid prototyping of complex-shaped parts by injecting molten metal into a steel mold (die) at high pressures of 2,000–20,000 PSI.
High precision and surface quality
The molten metal is filled under high pressure to reproduce fine mold textures up to IT11-IT13 and a surface roughness of Ra 0.8–3.2 μm.
Thin-walled and complex structures
Suitable for parts with wall thicknesses as low as 0.5 mm, and can form complex features such as pores and threads at one time.
High productivity
Short cycle times (typically seconds to minutes) make it suitable for high-volume production.
Cold-Chamber Die Casting
Applicable materials: metals with high melting points (such as aluminum alloys, magnesium alloys, copper alloys).
Process characteristics
The molten metal is insulated by the external furnace body, and the mold is injected from the cold chamber by a hydraulic plunger.
The short contact time between the metal and the equipment reduces the risk of hot corrosion.
Typical applications
Automotive engine blocks, structural parts (such as Tesla’s integrated die-cast body).
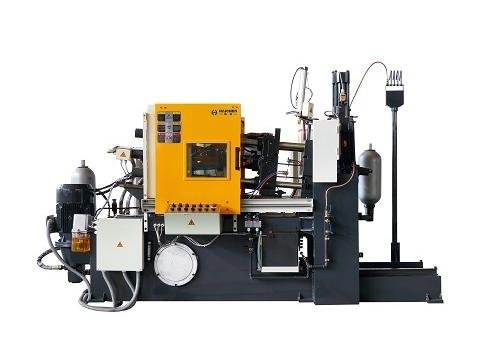
Hot-Chamber Die Casting
Applicable Materials
Low melting point metals (such as zinc alloy, tin alloy).
Process characteristics
The molten metal is melted and injected directly in the “gooseneck” of the equipment.
Which is more efficient, but long-term contact with molten metal may accelerate the wear of the equipment.
Typical applications: electronic connectors, small hardware.
Technology Development Trends
Despite the dominance of high-pressure die casting, the industry is still exploring the direction of technological upgrades:
Vacuum-assisted high-pressure die casting (Vacuum HPDC) reduces porosity in castings by vacuuming, improving mechanical properties (e.g., 15–20% increase in tensile strength).
Semi-Solid Die Casting (SSDC) metal is formed in a solid-liquid two-phase state to reduce shrinkage defects and is suitable for medical implants with high density requirements.
Limitations: The cost of equipment is high, and the current market penetration rate is less than 5%. Intelligence & Sustainability Robot automatic pick-up and real-time monitoring system improve yield.
The scrap recycling rate is increased to more than 95%, and the energy consumption is reduced (e.g. aluminum die casting energy consumption is reduced by 30% compared to traditional casting).