The function of jet cooling in die casting is to rapidly cool molten metal using high-velocity jets, ensuring uniform solidification.

Jet cooling is a critical process in die casting that significantly enhances the efficiency and quality of the finished product. It involves the use of high-velocity air or gas jets to rapidly cool the molten metal within the mold cavity.
This technique is particularly important in the production of complex parts with thin walls, where uniform cooling is essential to prevent defects and ensure dimensional accuracy.
The function of jet cooling in Die Casting
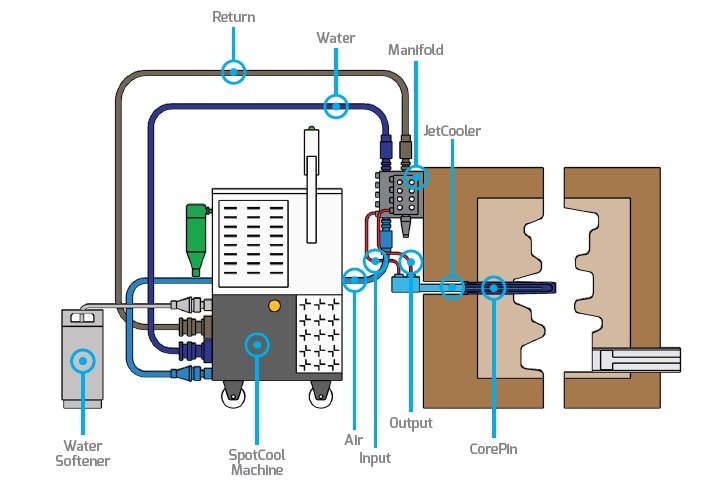
Rapid Solidification
One of the primary functions of jet cooling is to accelerate the solidification of the molten metal. By applying high-velocity air or gas jets directly onto the surface of the metal, jet cooling ensures that the metal cools quickly and uniformly. This rapid solidification helps in reducing the cycle time, thereby increasing production efficiency.
Prevention of Defects
Jet cooling helps in preventing common defects associated with die casting, such as porosity, shrinkage, and warping. By ensuring that the molten metal cools uniformly, jet cooling minimizes the formation of hot spots and reduces the risk of internal voids or surface irregularities. This results in higher-quality parts with better mechanical properties.
Enhanced Surface Finish
The rapid and uniform cooling provided by jet cooling contributes to a smoother surface finish on the finished parts. This is particularly important for applications where the aesthetic appearance of the product is crucial, such as automotive and consumer electronics.
Dimensional Accuracy
Jet cooling ensures that the parts cool uniformly, which helps in maintaining the dimensional accuracy of the final product. This is especially important for complex parts with intricate geometries, where even minor deviations can affect the functionality of the part.
Energy Efficiency
By reducing the overall cooling time, jet cooling contributes to energy savings. This not only reduces operational costs but also aligns with environmental sustainability goals.
HAICHEN: Die Casting Technology
HAICHEN is a renowned die casting machine manufacturer known for its advanced technology and high-quality products. HAICHEN’s machines are designed to incorporate advanced cooling systems, including jet cooling, to enhance the efficiency and quality of the die casting process. Key features of HAICHEN’s machines include:
- Advanced Cooling Systems: HAICHEN machines are equipped with state-of-the-art jet cooling systems that ensure rapid and uniform cooling of the molten metal.
- Precision Control: HAICHEN’s machines feature advanced control systems that allow precise regulation of the cooling process, ensuring consistent quality.
- Energy Efficiency: HAICHEN’s machines are designed to be energy-efficient, reducing operational costs and environmental impact.
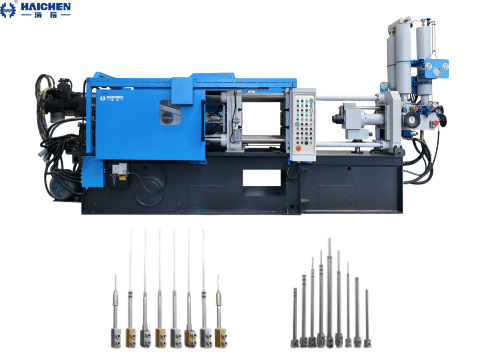
Jet cooling is a vital function in die casting that enhances the quality, efficiency, and dimensional accuracy of the finished parts. Whether for automotive components, consumer electronics, or industrial parts, jet cooling remains a crucial technique in modern die casting.