The cooling system in a die casting mold is a critical component designed to manage the temperature of the mold during the die casting process. It plays a vital role in ensuring the quality of the cast parts, the efficiency of the process, and the longevity of the mold.
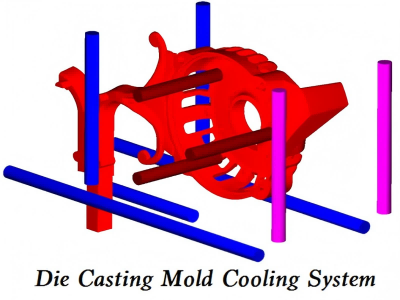
Function of the Cooling System
The primary function of the cooling system is to regulate the mold temperature uniformly. This helps in achieving consistent solidification of the molten metal, preventing defects such as warping, internal stresses, and porosity. Effective cooling also reduces cycle times, improving production efficiency.
Components of the Cooling System
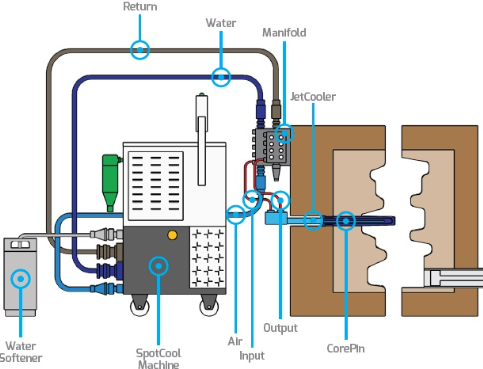
The cooling system typically consists of:
Cooling Channels
These are internal passages within the mold that allow coolant (usually water or a water-based fluid) to circulate. Place the channels strategically to ensure even heat distribution and rapid cooling.
Cooling Inserts
Some advanced molds use conformal cooling inserts to match the shape of the mold cavity. This allows for more efficient heat transfer and better control over the cooling process.
Cooling Accessories
These include baffles, bubblers, heat pipes, and other components that enhance the cooling efficiency.
Benefits of an Efficient Cooling System
Improved Part Quality
Uniform cooling reduces defects and enhances the mechanical properties of the cast parts.
Increased Mold Life
Proper cooling reduces thermal fatigue and wear on the mold, extending its operational life.
Reduced Cycle Time
Efficient cooling allows for faster solidification, leading to shorter production cycles and higher efficiency.
Design Considerations of the cooling system
Channel Placement
Position cooling channels closely enough to the mold cavity to be effective but not so close that they weaken the mold structure.
Uniform Cooling
Design channels to ensure even cooling across the mold to avoid uneven solidification and part defects.
Flow Rate and Pressure
The cooling system must provide adequate flow rate and pressure to remove heat efficiently.
Material Compatibility
The cooling medium and channel materials must be compatible to prevent corrosion or clogging.
The cooling system in a die casting mold is essential for maintaining consistent mold temperatures, improving part quality, and enhancing production efficiency. Proper design and implementation of them are crucial for achieving high-quality castings.
Haichen Cooling System in Die Casting Mold
Haichen is a well-known manufacturer and supplier of die casting machines (cold chamber and hot chamber die casting machines)and related equipment, including cooling systems for die casting molds. Our cooling systems are designed to enhance the efficiency and performance of the die casting process by ensuring precise temperature control and optimal heat management in the mold.
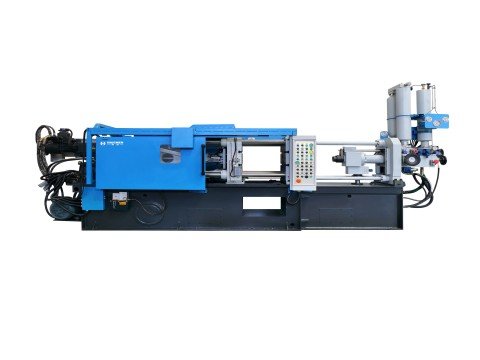
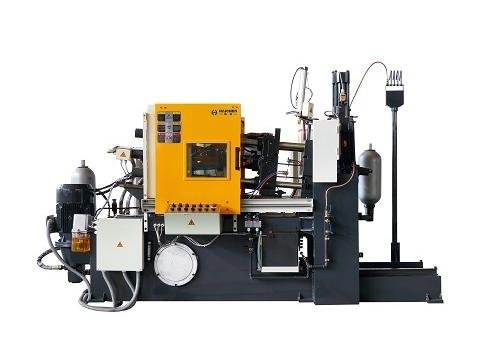
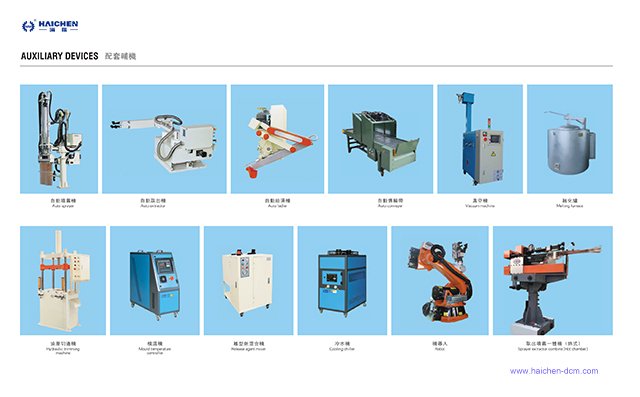
Key Features of Haichen Cooling Systems
High Efficiency: Haichen cooling systems are engineered to provide efficient heat removal, reducing cycle times and improving production rates.
Precision Temperature Control:These systems ensure uniform cooling across the mold, which is critical for producing high-quality castings with minimal defects.
Durability: Haichen cooling systems are built to withstand the harsh conditions of die casting, including high temperatures and pressures.
Customizable Solutions: Haichen offers tailored cooling systems to meet the specific requirements of different die casting applications and mold designs.
Advanced Technology: Their systems often incorporate advanced features like automated temperature monitoring and control, ensuring consistent performance.