Die casting cooling solutions includes choice of cooling method, cooling medium, cooling system maintenance and so on.
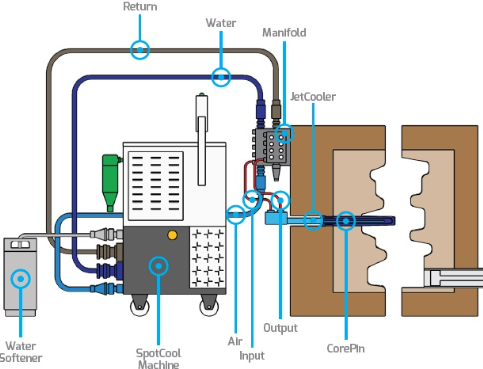
The cooling system plays a vital role in the die casting process, which directly affects the surface quality, dimensional accuracy and reduction of internal defects of the die casting. If the cooling is not done properly, it may lead to surface defects. Also with shrinkage and increased porosity of the die casting.
Die casting cooling solutions: Choice of cooling method
Water cooling: Water cooling one of the most common used cooling methods. With high cooling efficiency, but it will increase the complexity of the mold structure. Water cooling channels usually arrange in the core or insert of the mold to effectively remove heat.
Air cooling: Air cooling is a lower-cost cooling method. And it is suitable for occasions where rapid cooling is required. However, air is less efficient as a cooling medium, not as good as water or oil.
Jet cooling: Jet cooling uses a high-pressure pump to send water into the cooling circuit, using a specific nozzle and piping system to achieve local cooling. This method can accurately control the cooling time, thereby effectively removing hot spots.
Die casting cooling solutions: Choice of cooling medium
Water cooling usually uses water preheated to about 50°C to avoid overheating risks.
The temperature of the cooling water should be above room temperature to prevent condensation on the surface. Air cooling requires fan-driven air circulation.
Die casting cooling solutions : Cooling system maintenance
High-pressure and high-temperature hoses and connections in the cooling system require regular inspection and maintenance to prevent leakage and fire risks.
Cooling system maintenance also includes regular cleaning of filters to prevent casting residues from entering the circulation pump.
Optimization of cooling effect
By optimizing cooling time and temperature parameters, production efficiency and product quality can be significantly improved.For example, in hot chamber die casting, the optimal cooling time is 0.8 seconds.
Using advanced simulation software (such as OpenFOAM) can help predict the temperature distribution and heat transfer characteristics during the cooling process.
Material selection and heat treatment
The design of the cooling system also needs to consider the thermal shock resistance, toughness and high temperature strength of the mold material.
For example, H13 steel widely uses in die casting molds. Due to its excellent mechanical properties and thermal fatigue resistance.
Appropriate heat treatment processes (such as graded isothermal quenching) can effectively reduce mold deformation and cracking.
Thus, the die casting cooling solution needs to comprehensively consider cooling methods, channel design, medium selection, maintenance and optimization, etc. Through scientific design and reasonable management, the quality and production efficiency of die castings can be significantly improved.
Haichen die casting machine
Haichen is one Chinese die casting machine manufacturer for more than 10years. We produce both high pressure cold chamber die casting machine and hot chamber die casting machine. They have durable and highly precise features.
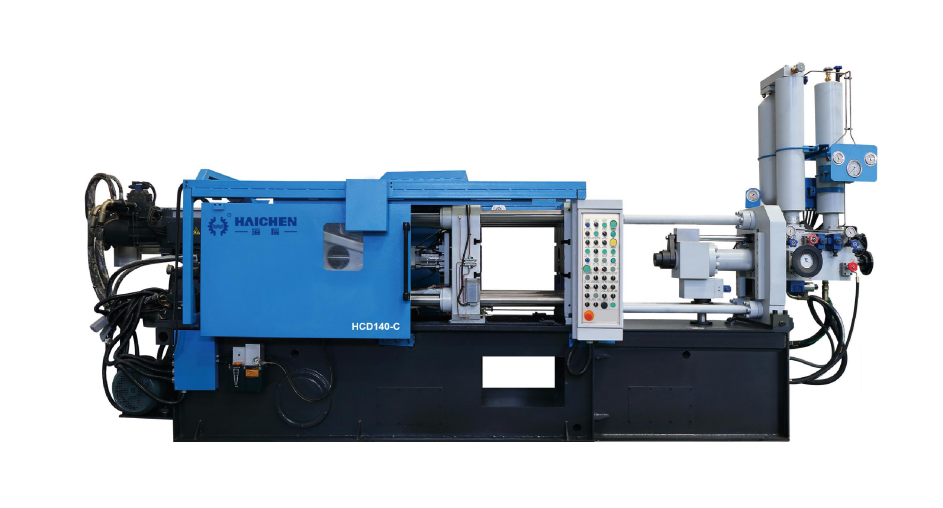
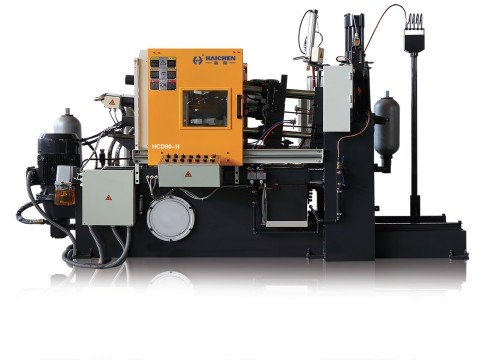
Haichen also produce die casting machine auxiliary equipment. Such as conveyor, vacuum machine, mold temperature controller, industrial robot, sprayer and so on.
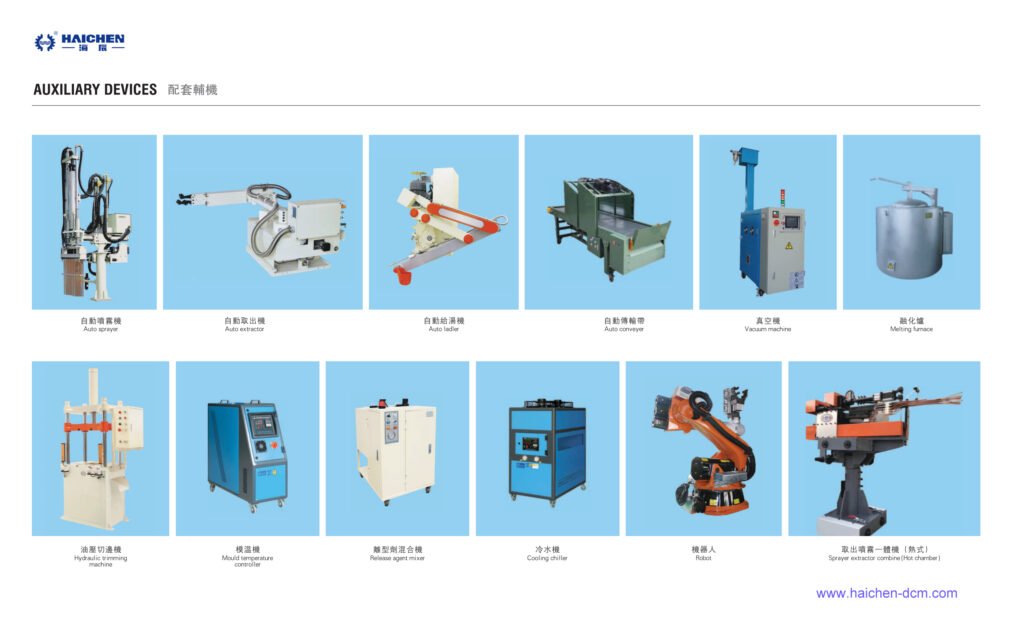
We supply cold chamber and hot chamber die casting machine spare parts.
Welcome contact us.