Choose cold die casting material includes mechanical properties of materials, production cost and demand, product design and so on.
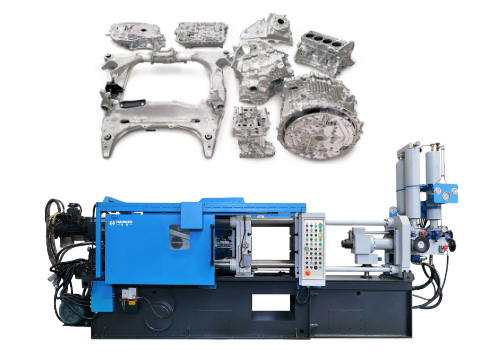
Selecting materials suitable for cold chamber die casting requires comprehensive consideration of multiple factors, including the material’s mechanical properties, production costs, production requirements, product design, environmental factors, and sustainability.
1. Choose cold die casting material: Mechanical properties of materials
Cold chamber die casting is suitable for the use of high melting point metals such as aluminum, copper and their alloys, which have good strength, toughness and durability and can withstand the high pressure and high temperature during the cold chamber die casting process. In addition, light metals such as magnesium and zinc also commonly use in cold chamber die casting because they have lower density and higher corrosion resistance.
2. Choose cold die casting material: Production cost and production demand
When choosing materials, you need to balance cost and quality. For example, aluminum widely uses in automotive parts due to its high strength and lightweight properties. But its cost is high; while zinc and magnesium widely use due to their lower cost and good mechanical properties.
3. Choose cold die casting material: Product design
Material selection should be based on the functional requirements of the product. For example, products that require high strength and durability can choose copper or zinc; products that require lightness can choose aluminum or magnesium.
4. Environmental factors
In the cold chamber die casting process, the corrosion resistance of the material is crucial. For example, aluminum is prone to oxidation in certain environments, so anti-corrosion measures are required.
5. Sustainability
Choosing materials with less impact on the environment is a trend in modern manufacturing. For example, aluminum and magnesium have a high recycling rate, which meets the requirements of sustainable development.
6. Production efficiency
Cold chamber die casting has a long production cycle, so the selection of materials should take into account its filling and cooling properties in the mold. For example, aluminum and magnesium cool faster, which helps improve production efficiency.
Selecting materials suitable for cold chamber die casting requires comprehensive consideration of mechanical properties, cost, production requirements, product design, environmental factors and sustainability. Aluminum, copper, magnesium and zinc are common cold chamber die casting materials, and the specific selection should be optimized according to the actual application scenario and requirements.
Haichen die casting machine
Haichen is one Chinese die casting machine manufacturer for more than 10years. At the same time, we produce both high pressure cold chamber die casting machine and hot chamber die casting machine. They have durable and highly precise features.
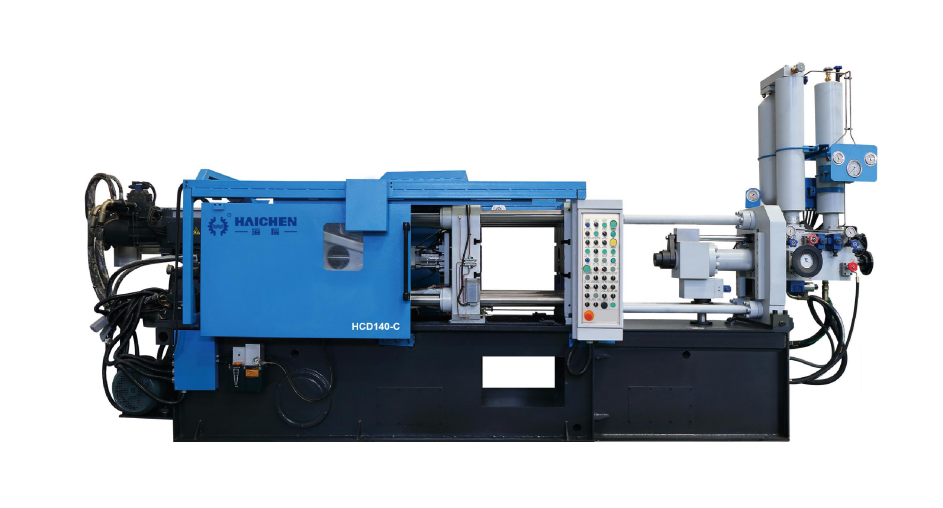
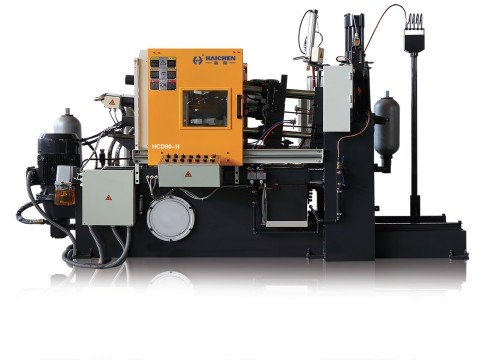
Haichen also produce die casting machine auxiliary equipment. Such as conveyor, vacuum machine, mold temperature controller, industrial robot, sprayer and so on.
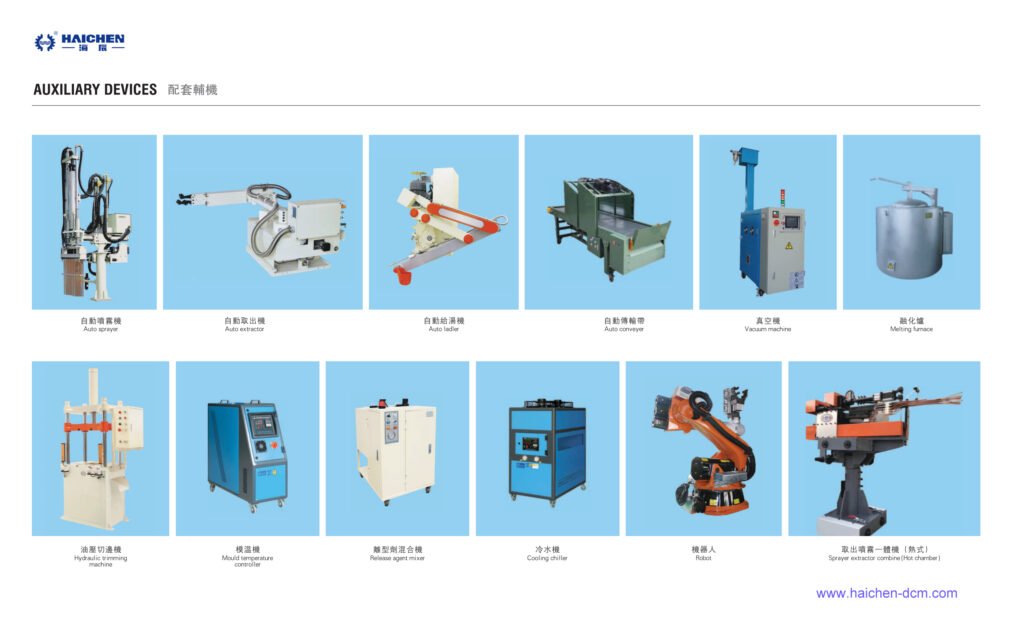
We supply cold chamber and hot chamber die casting machine spare parts.
Welcome contact us.