Die Casting Material Selection Guide offers crucial tips for choosing materials based on strength, weight, and cost performance.
Die casting is a versatile manufacturing process used to produce high-quality metal parts with complex geometries and tight tolerances. The choice of material plays a crucial role in determining the performance, durability, and cost-effectiveness of the final product.
Understanding the key characteristics and applications of different die casting materials is essential for making informed decisions. This guide provides an overview of the most commonly used materials in die casting and their specific advantages.
Die Casting Material Selection Guide
Aluminum Alloys: Versatility and Lightweight
Aluminum alloys are the most widely used materials in die casting due to their excellent combination of strength, lightweight, and corrosion resistance. These alloys offer several key benefits:
- Low Weight: Aluminum is significantly lighter than other metals like steel or brass, making it ideal for applications where weight reduction is critical. Such as in the automotive and aerospace industries.
- High Strength: Despite its low weight, aluminum alloys can achieve high tensile strength and mechanical properties, ensuring durability and reliability.
- Corrosion Resistance: Aluminum naturally forms a protective oxide layer, which enhances its resistance to corrosion, making it suitable for various environments.
- Thermal Conductivity: Aluminum has excellent thermal conductivity, which is beneficial for applications requiring efficient heat dissipation. Such as in engine components and electronics.
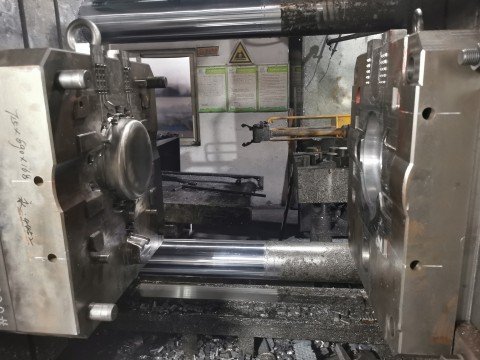
HAICHEN, a leading die casting machine manufacturer, offers advanced solutions tailored for aluminum die casting. Our machines are designed to handle the specific requirements of aluminum, ensuring precise control over the casting process and delivering high-quality parts with consistent performance.
Zinc Alloys: Precision and Detail
Zinc alloys are another popular choice for die casting, particularly when high precision and intricate details are required.
- High Precision: Zinc alloys can be cast with extremely tight tolerances, allowing for the production of complex and detailed parts.
- Ease of Casting: Zinc has a relatively low melting point compared to other metals, making it easier to cast and reducing energy consumption.
- Strength and Durability: Despite its lower melting point, zinc alloys offer good mechanical properties, including high tensile strength and hardness.
- Surface Finish: Zinc castings can achieve excellent surface finishes, reducing the need for secondary machining operations.
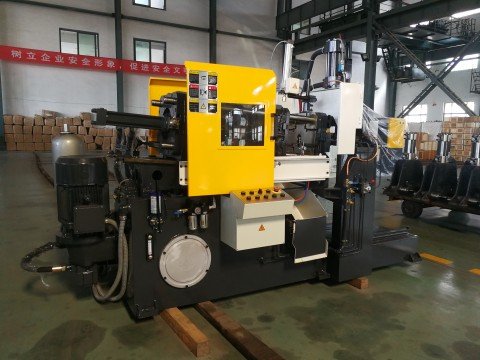
HAICHEN’s die casting machines are equipped with advanced technology to handle zinc alloys efficiently.Our machines ensure precise control over the casting process, resulting in high-quality parts with intricate details and minimal defects.
Magnesium Alloys: Ultra-Lightweight Solutions
Magnesium alloys are gaining popularity in industries where weight reduction is a priority. These alloys offer several unique benefits:
- Ultra-Lightweight: Magnesium is the lightest structural metal, making it ideal for applications where weight savings are critical, such as in automotive and aerospace components.
- High Strength-to-Weight Ratio: Despite its low density, magnesium alloys can achieve high strength and stiffness, ensuring durability without adding significant weight.
- Excellent Damping Capacity: Magnesium has superior damping properties, which can help reduce vibrations and noise in applications such as engine housings and electronic enclosures.
Copper Alloys: High-Performance Applications
Copper alloys, such as brass and bronze, are used in die casting for their exceptional mechanical properties and performance. These alloys offer:
- High Strength and Ductility: Copper alloys provide excellent tensile strength and ductility, making them suitable for applications requiring high mechanical performance.
- Thermal and Electrical Conductivity: Copper is an excellent conductor of heat and electricity, making it ideal for applications in electronics, electrical components, and heat exchangers.
- Corrosion Resistance: Copper alloys offer good resistance to corrosion, particularly in marine and industrial environments.
Material Selection Considerations
When selecting a material for die casting, several factors should be considered to ensure the best possible outcome:
- Application Requirements: Consider the specific requirements of your application, such as mechanical properties, corrosion resistance, and thermal conductivity.
- Cost: Different materials have varying costs, which can impact the overall production budget. Aluminum and zinc alloys are generally more cost-effective compared to copper alloys.
- Production Volume: High-volume production may benefit from materials that offer faster casting cycles and lower tooling costs.
- Post-Processing Requirements: Some materials may require additional machining or surface treatments to achieve the desired finish or performance.
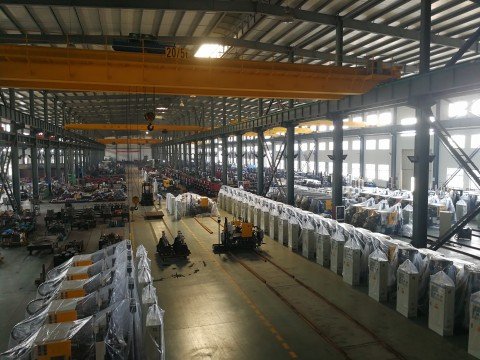
HAICHEN’s expertise in die casting machine manufacturing ensures that our machines are optimized for a wide range of materials and applications.Our advanced technology and customer-focused approach make them a reliable partner for all your die casting needs.
Die Casting Material Selection Guide is essential for making informed decisions. Choosing the right material impacts the performance, cost, and durability of the final product. Aluminum, zinc, magnesium, and copper alloys each offer unique advantages and are suitable for different applications. By understanding their key characteristics, manufacturers can optimize their die casting processes.