Improve die casting mold quality by focusing on precision design, selecting high-quality materials, and maintaining regular mold upkeep.
Improving die casting mold quality is crucial for achieving high-quality, consistent, and cost-effective production. A well-designed and well-maintained mold can significantly enhance the performance of the die casting process, reduce defects, and extend the mold’s lifespan.
How to improve die casting mold quality?
1. Precision in Mold Design
The foundation of high-quality die casting lies in precise mold design. A well-designed mold ensures that molten metal flows smoothly into the cavity, fills it completely, and solidifies uniformly. Key considerations include:
- Cavity Design: Ensure that the mold cavity accurately reflects the final part dimensions, accounting for shrinkage and tolerances.
- Venting: Proper venting allows gases to escape during the injection process, preventing gas porosity and improving surface finish.
- Draft Angles: Incorporate draft angles to facilitate easy ejection of the part from the mold without causing damage.
- Parting Lines: Minimize parting line thickness to reduce flash and ensure clean part surfaces.
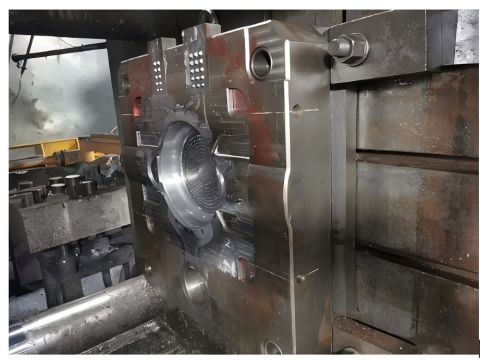
HAICHEN, a leading die casting machine manufacturer, offers advanced technologies and support to ensure that molds are designed and manufactured to the highest standards. Our machines are equipped with precise control systems that enhance the accuracy and repeatability of the die casting process.
2. Material Selection for Mold Construction
The choice of mold material is critical for durability and performance. High-quality mold materials can withstand the pressures and temperatures of the die casting process while maintaining dimensional stability. Key considerations include:
- Tool Steel: High-grade tool steel is preferred for its hardness, wear resistance, and ability to withstand thermal cycling.
- Surface Treatments: Applying surface treatments like nitriding or coating can enhance mold life and reduce maintenance.
- Heat Treatment: Proper heat treatment ensures the mold material reaches optimal hardness and toughness.
3. Maintenance and Inspection
Regular maintenance and inspection are essential for maintaining mold quality. A well-maintained mold not only reduces defects but also extends its operational life. Key practices include:
- Regular Cleaning: Remove residual metal and debris from the mold after each production cycle.
- Lubrication: Apply mold release agents to prevent sticking and ensure smooth ejection of parts.
- Inspection: Regularly inspect the mold for signs of wear, damage, or erosion. Address any issues promptly to prevent further damage.
- Storage: Store molds in a controlled environment to prevent rust and damage when not in use.
4. Process Control and Optimization
Optimizing the die casting process parameters is essential for maintaining mold quality. Key factors include:
- Injection Speed: Adjust injection speed to ensure proper filling of the mold cavity without causing turbulence or defects.
- Temperature Control: Maintain consistent mold and metal temperatures to ensure uniform solidification and reduce thermal stress.
- Cycle Time: Optimize cycle time to balance production efficiency with mold longevity.
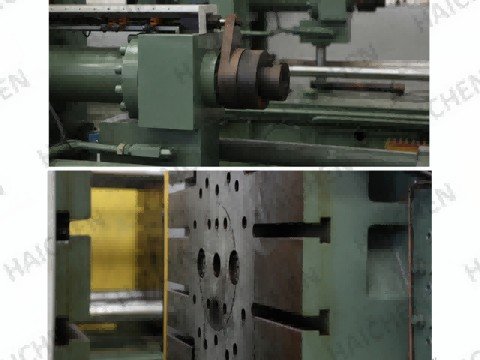
HAICHEN’s advanced die casting machines come equipped with state-of-the-art control systems that allow for precise monitoring and adjustment of process parameters. This ensures consistent quality and reduces the risk of mold damage.
5. Collaboration with Experienced Mold Makers
Working with experienced mold makers is crucial for achieving high-quality molds. Mold makers with expertise in die casting can provide valuable insights into design, material selection, and maintenance practices. HAICHEN partners with leading mold makers to ensure that their customers receive the best possible support and solutions.
Improving die casting mold quality involves a combination of precise design, high-quality materials, regular maintenance, and optimized process control. Investing in mold quality not only enhances part performance but also reduces long-term costs and downtime.