Advantages of Accumulator in Die Casting Processes
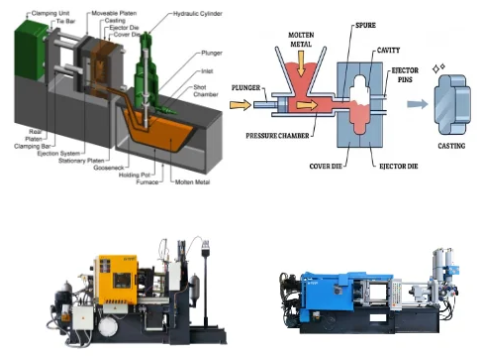
The advantages of accumulators in die casting processes are reflected in the following aspects:
1. Improved Energy Efficiency & Energy Savings
Accumulators store high-pressure energy (e.g., nitrogen or hydraulic oil) and release it rapidly during peak demand, meeting the instantaneous high-flow requirements of die casting.
This reduces the power demand on the main pump, lowers the drive unit capacity, and significantly cuts energy consumption and connected power requirements.
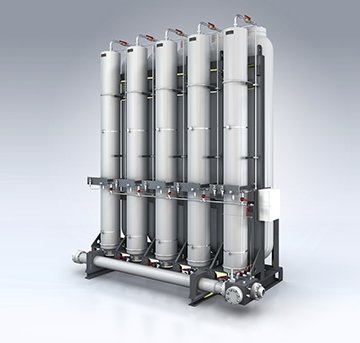
For example, Haichen die-casting machines utilize hydraulic accumulator systems to achieve precise energy release, enabling energy savings and environmentally friendly production.
2. Support for High Pressure & Large Flow Rates
During the injection phase, accumulators deliver high-pressure oil to drive the piston, ensuring rapid mold cavity filling (speeds up to 48 m/s) and shortening filling time (e.g., 6 ms).
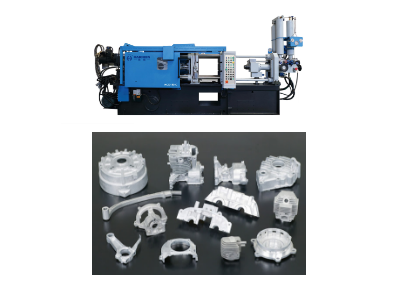
This enhances casting efficiency. Intensification systems amplify pressure (e.g., 450–800 MPa) via accumulators to improve casting compaction and reduce porosity defects.
3. Stabilized System Pressure & Process Control
Accumulators buffer pressure pulsations and shocks, mitigating pressure fluctuations caused by sudden valve closures or load changes. This prevents equipment damage and noise issues.
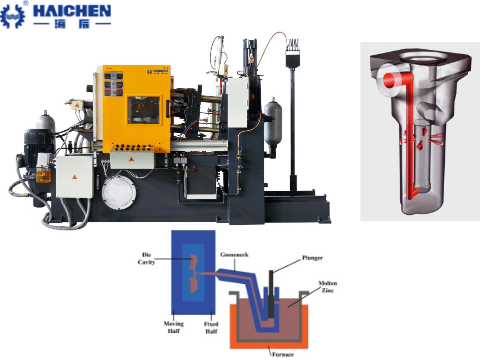
By adjusting accumulator volume and pressure settings (e.g., injection accumulator pressure affects maximum injection speed), process parameters like intensification timing and pressure stability can be optimized for precision.
4. Extended Equipment Lifespan & Reliability
Piston-type accumulators isolate gas and liquid to prevent contamination, making them ideal for high-pressure, high-flow systems (e.g., die-casting hydraulic systems). Their shock-absorption properties reduce vibration and mechanical wear, prolonging the lifespan of molds and hydraulic components.
5. Handling Complex Geometries & Temperature Variations

For parts with significant wall thickness variations (e.g., accumulator housings), multi-stage squeeze casting combined with accumulator-driven high-pressure feeding (e.g., localized squeeze pressures 5× higher than intensification) ensures synchronized solidification, reduces gas pores, and improves density. Accumulators also compensate for liquid volume changes due to temperature shifts, maintaining system pressure stability.
6. Enabling Compact Equipment & Operational Flexibility
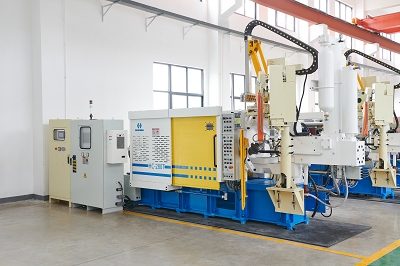
By storing energy during non-driving intervals, accumulators allow downsizing of pumps, shorter cycle times, and adaptability to diverse control modes (e.g., constant pressure or speed).
For example, high-specific-pressure casting uses moderate accumulator pressures to achieve efficient filling, reduce equipment failure rates, and enhance casting quality.
7. Emergency Backup & Safety Redundancy
In marine or industrial applications, large-capacity accumulators serve as emergency power sources for critical operations (e.g., hatch control), enhancing system safety and redundancy.
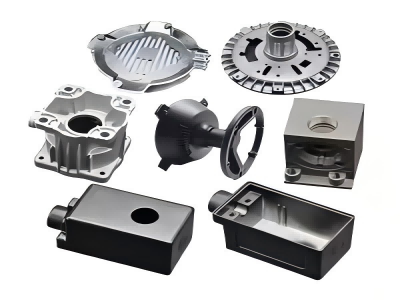
In summary, accumulators optimize die casting processes through energy management, process control, and equipment protection, significantly improving production quality, efficiency, and sustainability.
Working principle of accumulator in die casting machine
The working principle of accumulators in die-casting machines revolves around dynamic energy storage and release, primarily serving to deliver instantaneous high-pressure hydraulic oil for injection processes while stabilizing system pressure. Here’s a detailed breakdown:
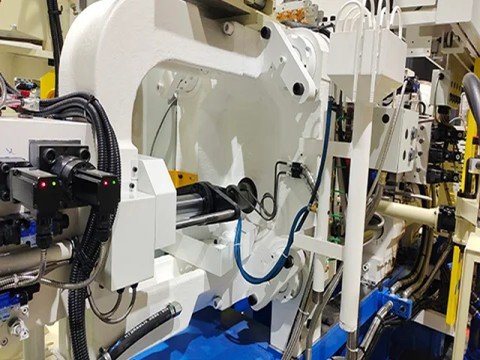
1. Energy Storage and Release Mechanism
Accumulators store hydraulic energy by compressing nitrogen gas (separated from hydraulic oil via a bladder or piston). During the injection cycle:
- Rapid Injection Phase: The accumulator releases high-pressure oil to drive the injection piston, achieving fast mold filling (e.g., plunger speeds of 6–10 m/s).
- Intensification Phase: A secondary accumulator amplifies pressure (200–300 bar) using a piston area differential to ensure casting densification.
2. Dynamic Pressure Distribution & Bernoulli’s Principle
Hydraulic pressure is divided into two components:
- Flow Resistance Pressure: Proportional to the square of injection velocity (Q²), overcoming fluid friction in the injection cylinder.
- Effective Pressure: Directly drives the plunger.
At maximum velocity (no-load speed), all accumulator pressure is consumed by flow resistance (effective pressure = 0). Conversely, at zero velocity, effective pressure equals total accumulator pressure. This balance is visualized in p-Q² diagrams to evaluate machine performance.

3. Multi-Stage Operation
Accumulators support four injection phases:
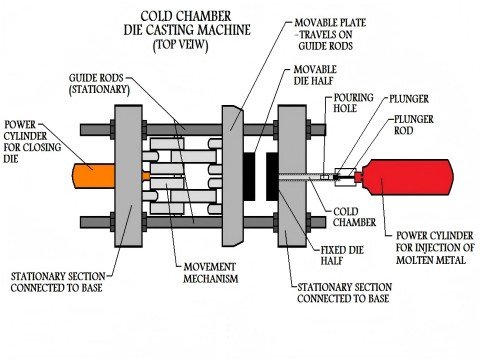
- Slow Injection: Low-pressure oil initiates mold filling.
- Rapid Injection: High-speed oil release from accumulators ensures fast cavity filling.
- Deceleration: Accumulator in die casting flow reduces to prevent mold overflow.
- Intensification: Secondary accumulators sustain high pressure (via amplified piston force) during solidification to minimize shrinkage porosity defects.
4. Pressure Stabilization & Shock Absorption
- Pressure Buffering: Accumulators absorb pressure spikes (e.g., valve closures) and compensate for leakage to maintain system stability (pressure drop <10% post-injection).
- Energy Efficiency: Reduces pump workload by recycling stored energy for subsequent cycles.
5. Design Optimization
- Proximity to Injection Cylinder: Minimizes pipeline resistance for higher no-load speeds.
- Dual-Circuit Systems: Independent control of intensification accumulators improves response time and pressure accuracy.
Key Maintenance Considerations
- Nitrogen Pressure Checks: Monitor gas precharge pressure quarterly (e.g., 70–90% of system pressure).
- Temperature Sensitivity: Gas pressure varies with ambient temperature; recalibrate seasonally.
- Safety Compliance: Use certified accumulators with pressure relief devices to prevent overpressurization.
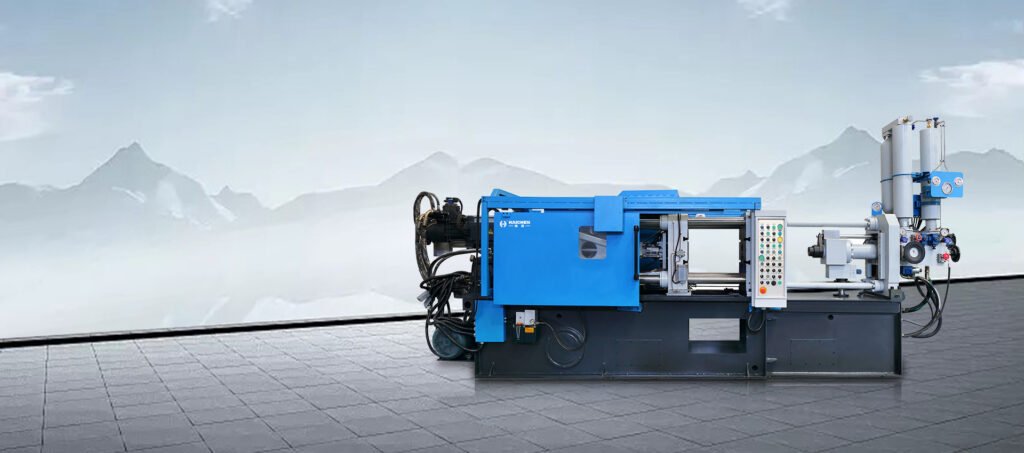
Accumulators are critical for achieving high-speed, high-pressure die-casting while balancing energy efficiency and system longevity.