The function of accumulator is to support the high-pressure, fast and precise metal fusion injection process through energy storage and release mechanisms.
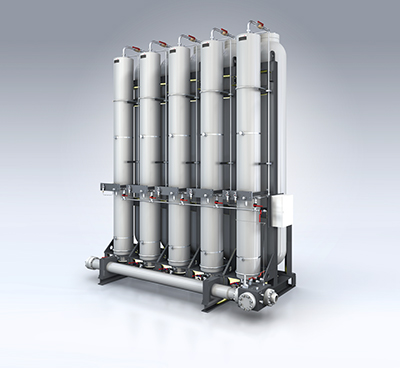
The core function and working principle of the accumulator
Energy storage and rapid release
Accumulators store hydraulic energy by compressing gas, usually nitrogen.
When the system pressure is high, the hydraulic oil enters the accumulator compressed gas.
When the system needs instantaneous large flow.
The accumulator quickly releases the stored hydraulic oil to meet the high-speed action requirements of the injection mechanism.
This mechanism is based on Boyle’s law (the volume of a gas is inversely proportional to the pressure).
For example, the pressure can be doubled when the volume of a gas is compressed to half.
Pressurizing effect
In the pressurization stage of die casting, the accumulator provides additional pressure through independent circuits.
For example, when a booster accumulator is activated after injection is complete.
Its stored high-pressure oil pushes the booster piston to further compact the molten metal.
Reducing porosity inside the casting and increasing density.
In the dual-circuit design, the booster accumulator is separated from the injection accumulator.
To ensure the independence and controllability of the booster pressure.
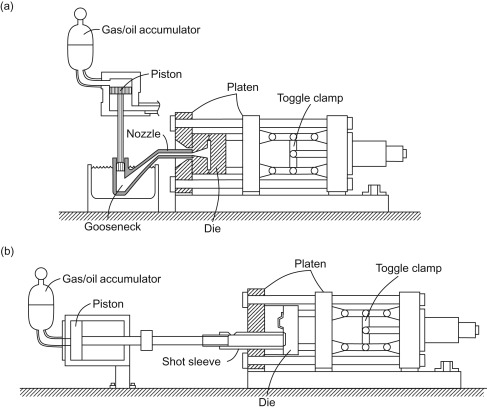
Stabilize system pressure
The accumulator maintains the pressure stability of the hydraulic system by supplementing leaks and buffering pressure fluctuations.
For example, in the slow injection phase, the accumulator balances the intermittent oil supply to the pump and avoids sudden pressure drops that can lead to unstable injection velocities.
The national standard stipulates that the pressure drop of the accumulator shall not exceed 10% of the working pressure for each injection.
Leakage compensation and emergency backup
In the event of a minor leak in the hydraulic system, the accumulator automatically replenishes the fluid, maintaining a stable system pressure and avoiding process interruptions due to pressure drops.
In addition, in the event of a sudden power failure or pump failure, the accumulator can be used as an emergency power source to complete the injection or pressure holding operation of the current cycle and prevent mold damage.
Shock absorption and vibration suppression
The rapid opening and closing of valves in hydraulic systems can trigger pressure shocks (water hammer effect).
Accumulators extend equipment life by absorbing transient pressure spikes and protecting pipes and seals.
Accumulator applications
High-speed production of thin-walled parts, such as aluminium mobile phone housings, which require injection speeds of up to 5–10 m/s.
And accumulators provide instantaneous high-pressure oil to ensure complete filling.
Large and complex castings
During the pressure holding stage, the accumulator continuously replenishes the pressure to compensate for the solidification and shrinkage of the metal and reduce the shrinkage of shrinkage.
Multi-cavity molds
When producing multiple parts at the same time, the accumulator supports stable flow distribution and avoids uneven filling due to insufficient pressure.