Force Casting optimization in Die Casting enhances precision and quality by optimizing injection parameters and mold design.
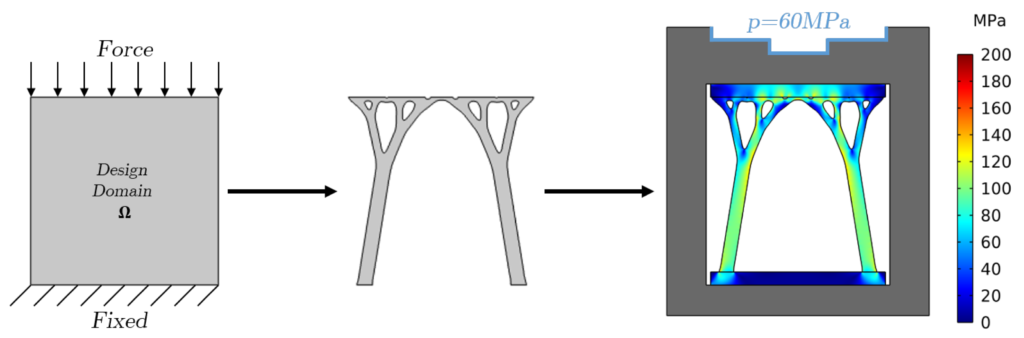
Die casting is a precision manufacturing process that involves injecting molten metal into a mold cavity under high pressure. One of the critical aspects of this process is force casting optimization, which ensures that the molten metal flows smoothly and fills the mold cavity uniformly. This article will explore the concept of force casting optimization and its significance in the die casting process.
What is Force Casting Optimization?
Force casting optimization refers to the process of fine – tuning the injection parameters to ensure optimal flow and filling of the mold cavity. This involves adjusting the injection speed, pressure, and timing to achieve consistent and defect – free castings. Proper optimization can significantly reduce the risk of defects such as porosity, cold shuts, and incomplete filling.
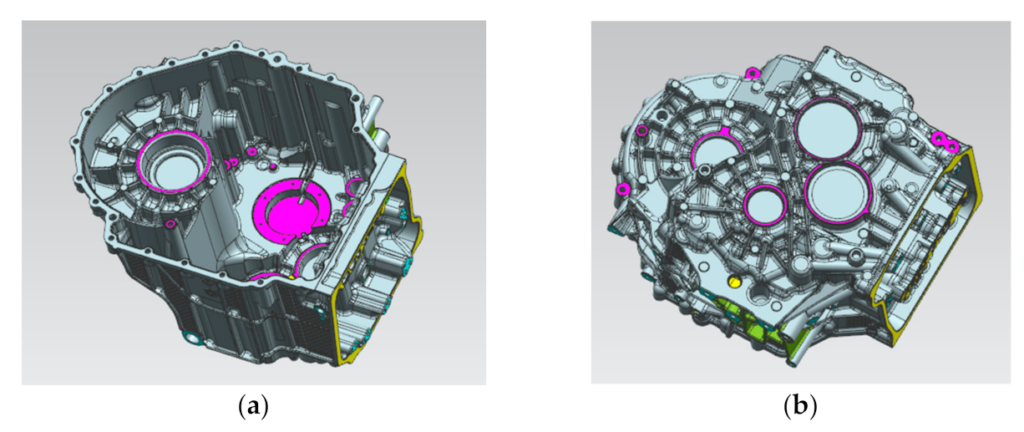
Importance of Force Casting Optimization
1 Consistent Part Quality
Optimizing force casting ensures that each casting is produced with consistent dimensions and surface quality. This is crucial for applications where tight tolerances and high – quality finishes are required.
2 Reduced Defects
By optimizing the injection parameters, manufacturers can minimize common defects such as porosity, cold shuts, and incomplete filling. This leads to higher – quality castings and reduced scrap rates.
3 Improved Efficiency
Force casting optimization can improve the overall efficiency of the die casting process. By ensuring that the molten metal flows smoothly and fills the mold cavity uniformly, manufacturers can reduce cycle times and increase production output.
Optimization Techniques
1 Simulation Software
Modern die casting machines, like those from HAICHEN, often come equipped with advanced simulation software. This software allows engineers to model the injection process and predict potential issues before production begins. By simulating different injection parameters, manufacturers can identify the optimal settings for their specific application.
2 Real – Time Monitoring
Real – time monitoring systems provide valuable data on the injection process. By monitoring parameters such as injection speed, pressure, and temperature, manufacturers can make real – time adjustments to ensure optimal performance. HAICHEN’s machines are equipped with advanced monitoring systems that provide detailed insights into the casting process.
3 Process Control Systems
Process control systems play a crucial role in force casting optimization. These systems automate the adjustment of injection parameters based on real – time data, ensuring consistent performance and high – quality castings. HAICHEN’s machines feature advanced process control systems that provide precise control over the injection process.
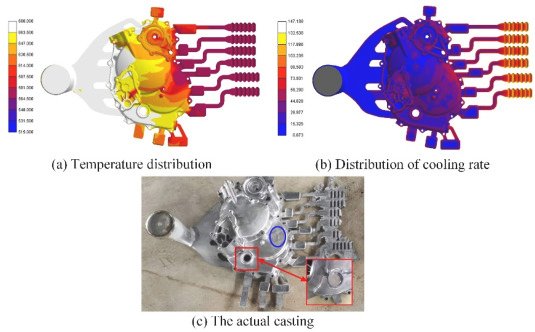
HAICHEN: Your Partner in Die Casting Excellence
At HAICHEN, we specialize in manufacturing high – quality die casting machines designed for precision and efficiency. Our advanced features actively maintain casting quality and process consistency in every production cycle. Whether you are starting a new project or upgrading your existing equipment, HAICHEN has the solutions to meet your needs.
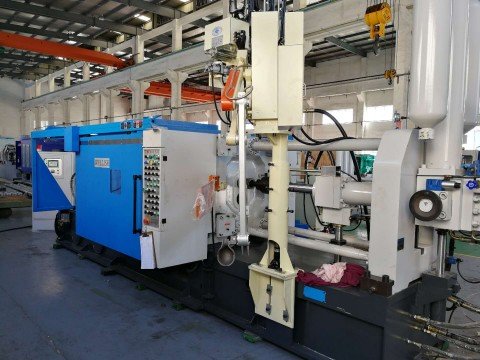
Force casting optimization is essential for achieving high – quality and efficient die casting production. By optimizing the injection parameters, manufacturers can reduce defects, improve part quality, and increase production efficiency.