Servo valves play a critical role in die casting machines by ensuring precise control of hydraulic systems.

Application of servo valve in die casting machine
The high-performance valves improve efficiency, accuracy, and repeatability in the die casting process. Below are the key applications of servo valves in die casting machines:
High-Speed Injection Control
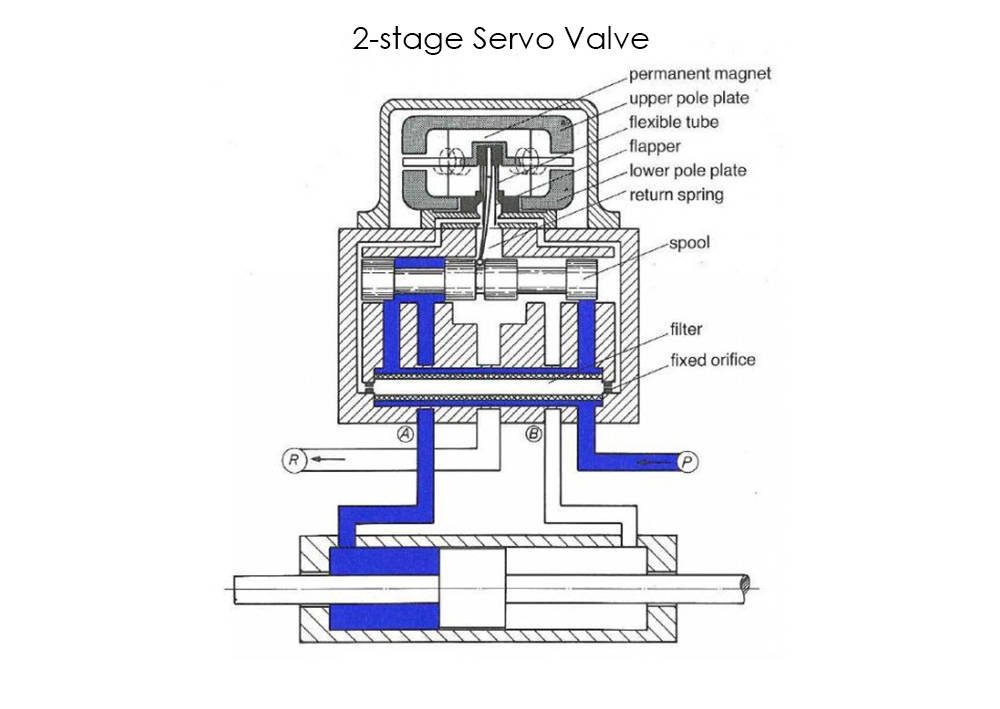
It is designed to provide high-speed response, which is essential for the rapid injection processes in die casting.
These valves can achieve injection speeds of up to 4 meters per second for aluminum and 8 meters per second for magnesium. This high-speed capability ensures that the molten metal fills the mold cavity quickly and uniformly, improving the quality and consistency of the castings.
Energy Efficiency
In traditional die casting machines, hydraulic systems often consume significant amounts of energy, especially during idle periods.
Servo valves, in combination with servo motors and variable pumps, can significantly reduce energy consumption. By directly controlling the flow and pressure according to the system’s needs, servo valves minimize energy losses and improve overall efficiency.
Improved Contamination Resistance
Servo valves are designed to be more resistant to contamination compared to traditional hydraulic valves.
This feature is particularly important in die casting environments, where hydraulic fluid contamination can lead to valve malfunctions and reduced performance. The improved contamination resistance of servo valves ensures more reliable operation and reduces maintenance requirements.
Enhanced Precision and Accuracy
Servo valves offer high precision and accuracy in controlling the movement of the die casting machine’s components. This precision is critical for maintaining tight tolerances during the casting process, resulting in higher-quality parts with fewer defects.
Additionally, the ability to precisely control the injection speed and pressure allows for the production of more complex and intricate castings.
Simplified Maintenance
The structure of servo valves is relatively simple, which leads to easier maintenance and fewer potential points of failure.
This simplicity not only reduces maintenance costs but also minimizes downtime, improving overall productivity.
Die casting machine servo valve supplier: Haichen Machinery
Haichen Machinery is a leading supplier of high-performance servo valves specifically designed for die casting machines. Our servo valves ensure precise hydraulic control, improving efficiency, accuracy, and energy savings in cold chamber and hot chamber die casting operations.
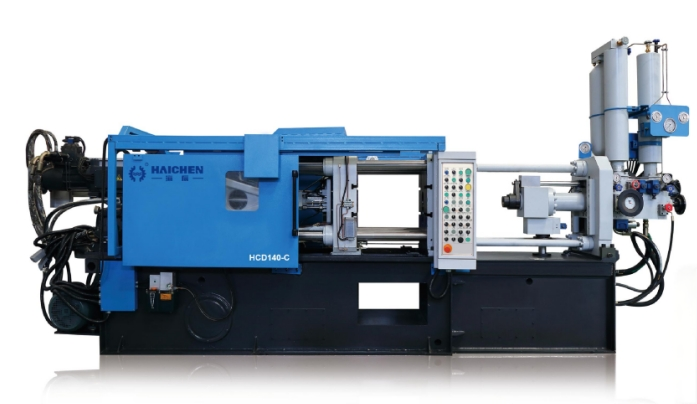
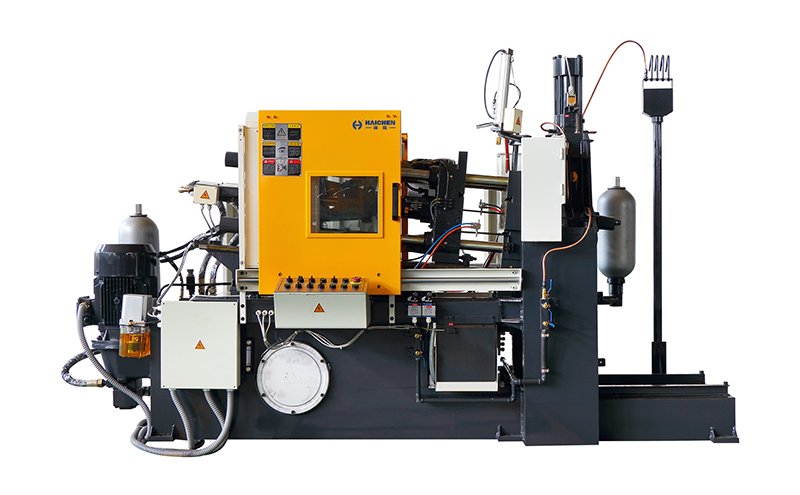
The key advantage of servo valve:
Precision Control:
Ensures accurate injection speed, pressure intensification, and clamping force for defect-free castings.
High Response Speed:
Delivers fast and stable adjustments to meet dynamic die casting demands.
Energy Efficiency:
Reduces power consumption compared to traditional hydraulic systems.
Durability & Reliability:
Built for high-pressure, high-temperature die casting environments.
Custom Solutions:
Offers tailored servo valve configurations for different die casting machine models.
If there is any demand for servo valve, welcome to consult us.