High Pressure Die Casting (HPDC) of Aluminum is a manufacturing process that injects molten aluminum into a steel mold cavity under high pressure and speed to rapidly produce complex metal components.
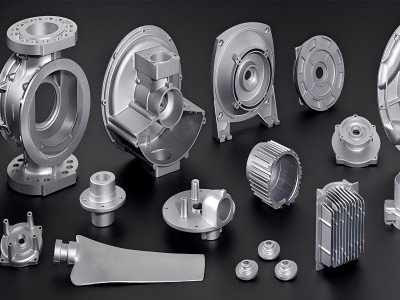
Below are its core principles, technical details, and applications:
Process Principles
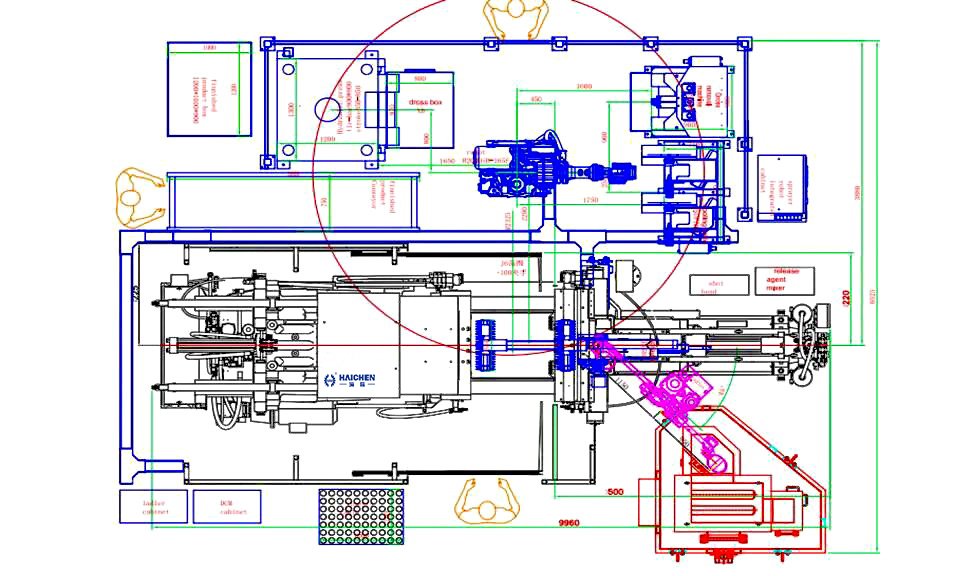
- High Pressure & Rapid Injection:
- The process forces molten aluminum into the mold at pressures ranging from 1,000–25,000 PSI (~7–172 MPa) and speeds of 30–100 m/s, ensuring complete filling of intricate geometries, including thin walls (as thin as 0.5 mm).
- High pressure minimizes shrinkage and improves dimensional accuracy.
- Tooling & Equipment:
- Manufacturers use hardened steel molds (split into fixed and moving halves) for tens of thousands of cycles, though initial mold costs remain high.
- Cold-chamber die casting machines handle aluminum (melting point ~660°C/1220°F) to isolate molten metal from the injection system, reducing thermal stress on equipment.
Process Steps
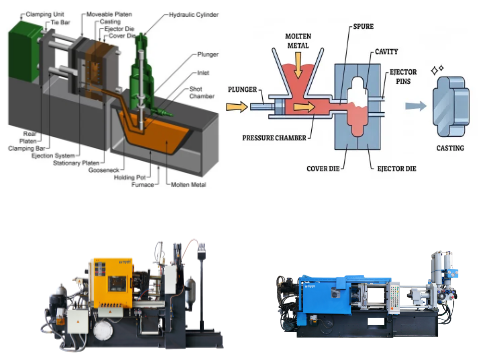
- Melting: A furnace heats aluminum alloy to a molten state (~670–710°C/1240–1310°F).
- Injection: Operators ladle the molten metal into the shot chamber, and a hydraulically driven piston injects it into the mold.
- Cooling & Ejection: The metal rapidly solidifies (seconds to tens of seconds), after which the mold opens, and ejector pins remove the part.
- Post-Processing: Most parts require only deburring, trimming, or drilling.
Advantages
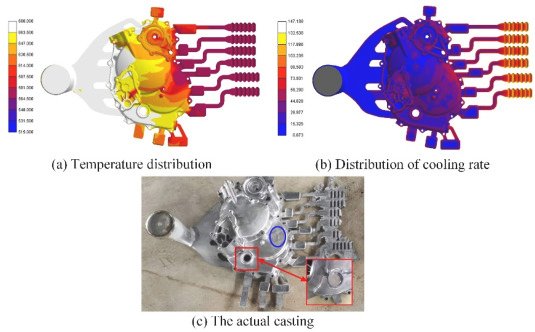
- High Efficiency: Mass production (e.g., automotive parts) achieves cycle times as short as 30–60 seconds.
- Precision & Surface Quality: Tight tolerances (±0.1 mm) and smooth surfaces (Ra 1.6–3.2 μm) reduce post-processing costs.
- Material Properties: Aluminum’s lightweight (2.7 g/cm³), high strength-to-weight ratio, and corrosion resistance support lightweighting in electric vehicles and aerospace.
Limitations
- High Tooling Costs: Complex molds cost 50,000–50,000–1M+, limiting HPDC to high-volume production (typically 10,000+ units/year).
- Gas Porosity: Turbulent filling traps air, causing internal voids. Vacuum-assisted HPDC (vacuum levels >90%) addresses this issue, enabling heat-treatable or weldable parts.
Applications
- Automotive: Aluminum HPDC dominates 70%+ of demand for engine blocks, transmission housings, and structural components like Tesla’s gigacast chassis.
- Consumer Electronics: Factories produce smartphone frames, heat sinks, and housings with thin walls and precision.
- Aerospace: Engineers use it for non-load-bearing components and lightweight enclosures.
Technological Advances
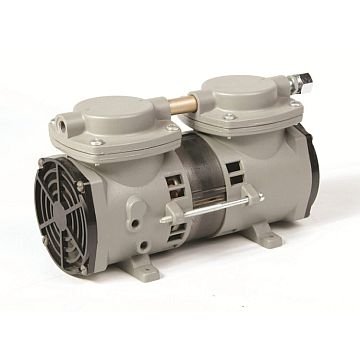
- Vacuum Die Casting: This method reduces porosity, allowing high-integrity structural parts (e.g., automotive safety components).
- Mega Casting Machines: Machines with clamping forces up to 9,000–12,000 tons (e.g., Tesla’s IDRA Gigapress) produce ultra-large integrated parts (e.g., EV underbodies), cutting assembly steps and weight.
High Pressure Die Casting of aluminum combines high-speed, high-pressure molding with aluminum’s material benefits to deliver complex, lightweight, and cost-effective components. It is a cornerstone of modern manufacturing, particularly in industries prioritizing efficiency and sustainability.
What is the die casting tolerance of aluminum?
1. Standard Tolerance Ranges
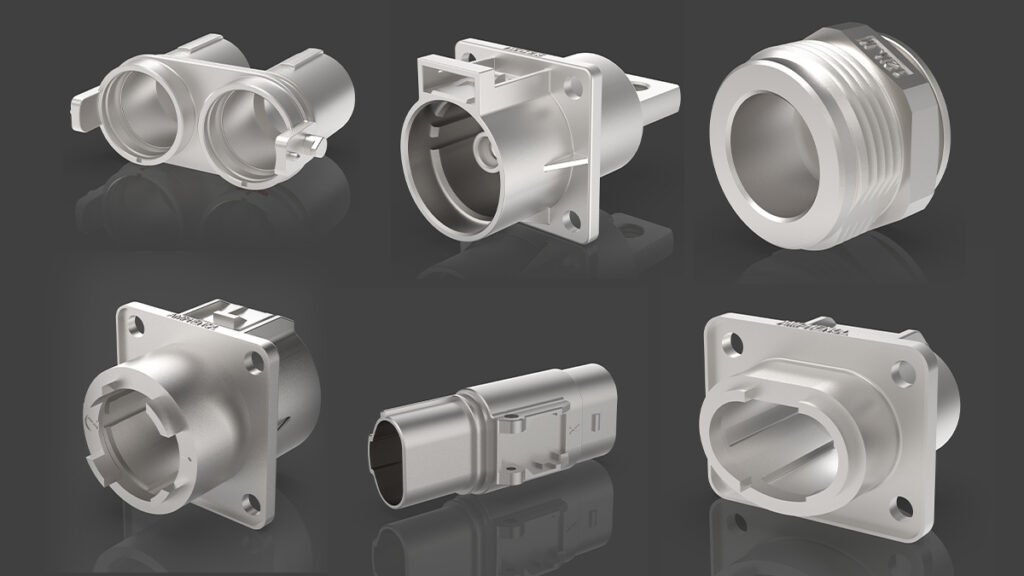
- General Standards:
According to NADCA (North American Die Casting Association) and industry norms, the linear dimensional tolerance for aluminum die casting is typically ±0.010 inches (0.25 mm) per 1 inch (25.4 mm), with an additional ±0.001 inches (0.025 mm) for each subsequent inch.- Example: For a 5-inch (127 mm) dimension, total tolerance would be:
±0.010 + 4×0.001 = ±0.014 inches (\~±0.35 mm)
.
- Example: For a 5-inch (127 mm) dimension, total tolerance would be:
- Parting Line Tolerance: Depends on projected area. For a 75 in² (483.9 cm²) part, parting line tolerance is ±0.012 inches (0.30 mm), leading to a combined tolerance of ±0.026 inches (~0.66 mm) when added to linear tolerance.
2. Precision Tolerance Ranges
- High-Precision Processes:
With optimized tooling (e.g., repeated sampling, mold re-cutting) and strict process control, tolerances can reach ±0.002 inches (0.05 mm) per inch, plus ±0.001 inches per additional inch.- Example: For a 5-inch dimension:
±0.002 + 4×0.001 = ±0.006 inches (\~0.15 mm)
.
- Example: For a 5-inch dimension:
- Extreme Cases: Specialized processes (e.g., high-precision molds and CNC finishing) may achieve ±0.005 inches (0.127 mm) or even ±0.01 mm (~±0.0004 inches), but costs increase significantly.
3. Tolerance Formulas
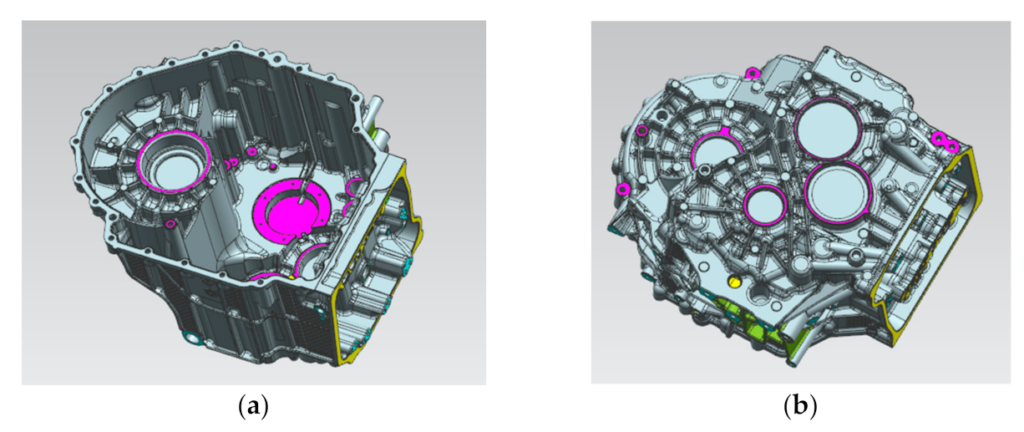
- General Tolerance Formula:
ε = ±(2.15×10⁻³ × L + 0.2) mm
, where L = dimension length (in mm).- Example: For 100 mm:
±(0.215 + 0.2) = ±0.415 mm
.
- Example: For 100 mm:
- Precision Formula:
ε = ±(1.15×10⁻³ × L + 0.1) mm
.
4. Tolerance Variations by Standard
- NADCA: Accounts for projected area, parting line shifts, and moving die components (MDC). For example, MDC tolerance for a 75 in² part is ±0.024 inches (0.61 mm).
- ASTM: Aligns with NADCA for linear, parting line, and flatness tolerances.
- Chinese GB/T 15114: Defaults to CNS 4022/4025 standards. Typical tolerances are IT13–IT15, while high precision reaches IT10–IT11 (~±0.05–0.1 mm).
5. Key Factors Affecting Tolerances
- Material Behavior: Aluminum’s thermal expansion (24 µm/m·°C) requires shrinkage compensation during cooling.
- Tooling Complexity: Moving components (e.g., sliders, ejector pins) introduce tolerance stacking risks.
- Surface Finish: Standard roughness ranges from Ra 3.2–6.3 µm, while high precision achieves Ra 0.8 µm.
Recommendations
- General Applications: Use standard tolerances (±0.010 inches/inch).
- High-Precision Needs: Apply NADCA’s precision guidelines and collaborate closely with suppliers.
- Cost Considerations: Ultra-tight tolerances (e.g., ±0.01 mm) may double tooling costs; evaluate necessity carefully.
For critical projects, consult die casting suppliers early and reference the latest NADCA or GB/T standards during design.
Haichen machine high Pressure Die Casting of aluminum
Haichen Machinery, a leading Chinese manufacturer of die-casting equipment, has over 20 years of expertise in high-pressure aluminum die casting. Its cold chamber HPDC machines are renowned for precision, efficiency, and versatility.
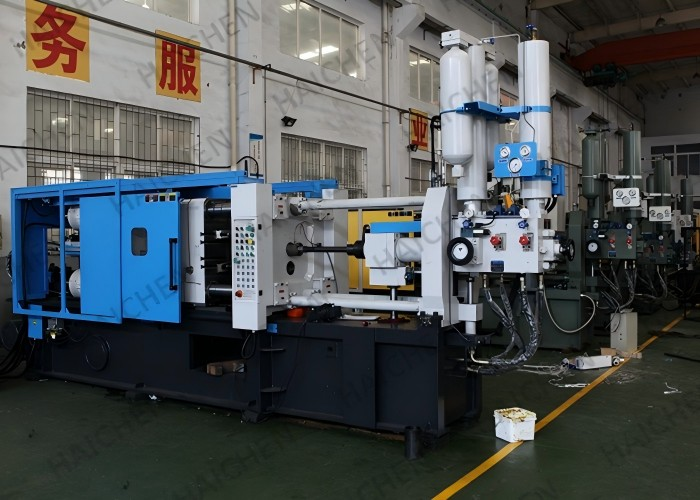
1. Equipment Models and Technical Specifications
Haichen’s HCD-C Series cold chamber HPDC machines are core products for aluminum die casting, with clamping forces ranging from 350 kN to 20,800 kN (approx. 35 to 2,080 tons). Examples include:
- HCD580-C: Clamping force of 5,800 kN, injection force range of 222–559 kN, adjustable injection speed (suitable for complex aluminum parts).
- HCD200-C (200-ton model): Casting pressure of 50.4–127.3 MPa, maximum aluminum shot weight of 1.8 kg, and multi-stage pressure/speed control (ideal for thin-walled precision components).
2. HPDC Process Features
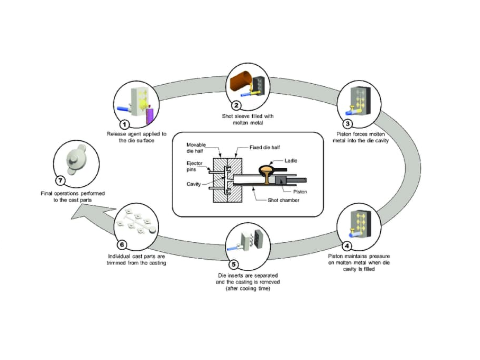
- High-Speed Injection: Molten aluminum is injected into molds at 4 m/s under pressures of 50–250 MPa, ensuring cavity filling and minimizing porosity.
- Four-Stage Control: Slow shot, first fast, second fast, and intensification stages optimize melt flow stability, enhancing part density (up to 99.5%) and surface finish (Ra ≤1.6 μm).
- Smart Control: Siemens PLC systems enable real-time injection curve monitoring and closed-loop control, supporting multi-language interfaces (English/Chinese/Russian).
3. Applications
- Automotive: Engine blocks, structural components (e.g., battery housings for EVs), and lightweight parts (cycle time as low as 30 seconds).
- Thermal Management: Integrated aluminum heat sinks for electronics and HVAC systems.
- Consumer Goods: Thick-walled cookware with uniform heat distribution.
4. Technological Advantages
- Energy Efficiency: Dual-pump hydraulic systems and servo drives reduce energy consumption by 30% (noise ≤75 dB).
- Material Compatibility: Supports aluminum alloys (melting point >700°C) and magnesium alloys. Cold chamber design prevents thermal damage to injection systems.
- Digital Integration: Cloud-based production management systems enable remote monitoring and process optimization.
5. Partnerships and R&D
Haichen collaborates with global leaders like Mitsubishi Heavy Industries and SHW, using German/Japanese hydraulic components. Its Ningbo facility (5,000 m²) produces 4,000 machines annually, with R&D focused on innovations like vacuum-assisted HPDC.
6. Industry Comparison
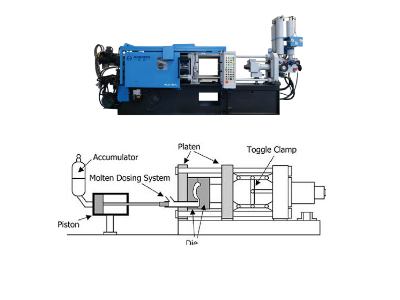
Compared to traditional casting, Haichen’s HPDC aluminum parts offer:
- 30% higher strength-to-weight ratio vs. steel.
- Near-net-shape precision (minimal post-machining).
- Scalability: Cost-effective for high-volume production (e.g., automotive batches of 100,000+ units).
Conclusion
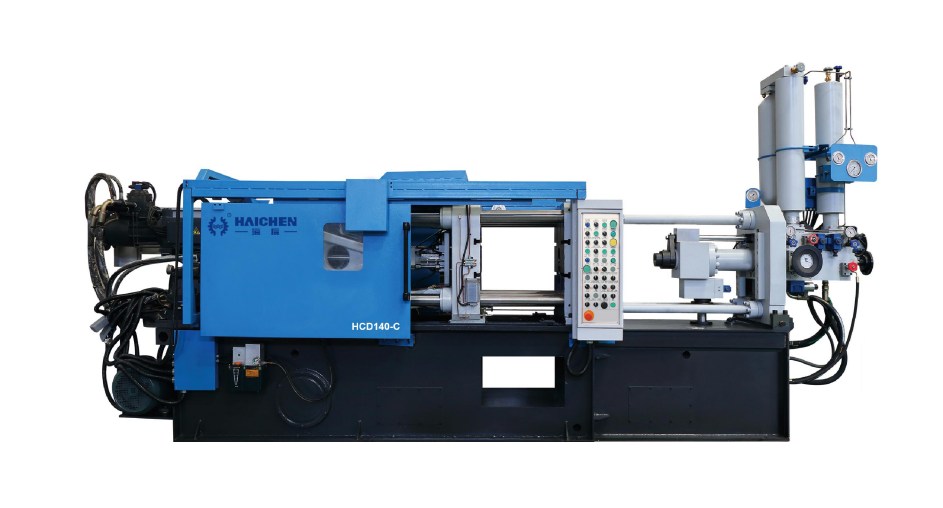
Haichen’s HCD-C Series combines multi-stage pressure control, intelligent systems, and energy-saving designs to lead in automotive, electronics, and consumer goods HPDC. Its focus on R&D (e.g., hybrid HPDC-vacuum technology) positions it as a key innovator in lightweight, high-performance aluminum manufacturing.