Aluminum or magnesium are both die-cast materials.
But the right choice in die casting also needs to be seen from many aspects.
Aluminum and magnesium are both lightweight and high-strength, but magnesium is lighter and less dense.
Aluminum is more resistant to corrosion than magnesium, but it is less resistant to corrosion in some environments.
Magnesium alloys can significantly improve their mechanical properties and corrosion resistance by adding elements such as aluminum and zinc.
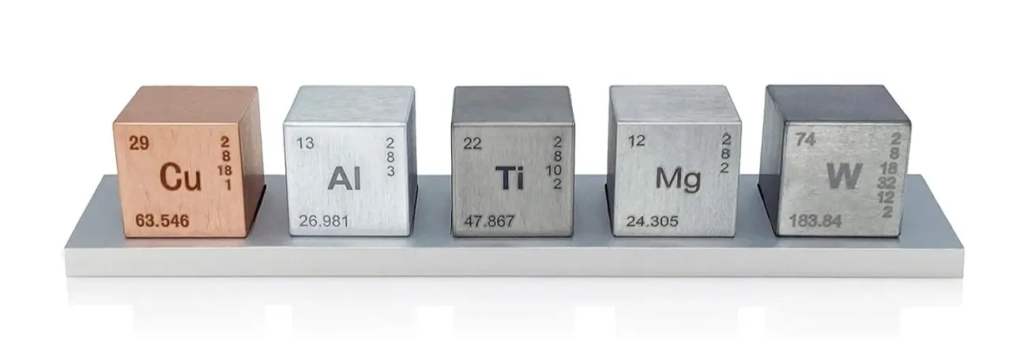
The basic properties of aluminum
Physical
Appearance: Silvery-white light metal with metallic luster and soft texture.
Density and classification: The density is 2.7 g/cm³, which is a light metal.
Melting and boiling point: melting point 660.4 °C, boiling point 2467 °C.
Performance characteristics: electrical conductivity is second only to silver and copper, excellent thermal conductivity.
And ductility, and can be processed into foil, silk, powder and other forms.
Chemical properties
Reaction with non-metals: a dense oxide film (Al₂O₃) is formed on the surface at room temperature.
And it burns violently at high temperature (4Al 3O₂ → 2Al₂O₃).
Reaction with acid: Reaction with dilute sulfuric acid and hydrochloric acid to produce hydrogen.
But passivation occurs at room temperature when it encounters concentrated sulfuric acid or concentrated nitric acid.
Reaction with strong base: soluble in NaOH solution (2Al 2NaOH 2H₂O → 2NaAlO₂ 3H₂↑).
Thermite reaction: Reduction of metal oxides (e.g. Fe₂O₃) at high temperatures for welding rails.
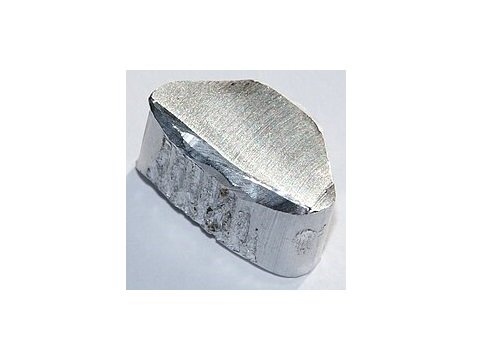
Magnesium basic properties
Physical
Magnesium is element number 12 in the periodic table, with an atomic weight of 24.31.
And a density of 1.74 g/cm³, making it the lightest of structural metals and 36% lighter than aluminum.
Its crystal structure is close hexagonal (HCP), melting point 648.8 °C, boiling point 1107 °C.
Magnesium has high thermal conductivity (156 W/(m·K)), low coefficient of thermal expansion (26×10⁻⁶/K).
And excellent damping properties, which can effectively absorb vibrational energy.
To improve performance, pure magnesium requires alloying due to its inherent limitations in mechanical strength and corrosion resistance.
Chemical properties
Magnesium is chemically active, forming an oxide film in the air at room temperature, burning violently at high temperature, emitting dazzling white light (reaction formula: 2Mg O₂ → 2MgO).
It reacts with acid to form hydrogen gas (Mg 2H⁺ → Mg²⁺ H₂↑), and magnesium hydroxide and hydrogen gas (Mg 2H₂O → Mg(OH)₂ H₂↑) in boiling water.
Magnesium also reacts with CO₂ (2Mg CO₂ → 2MgO C), which allows it to use dry sand instead of carbon dioxide for extinguishing fires.
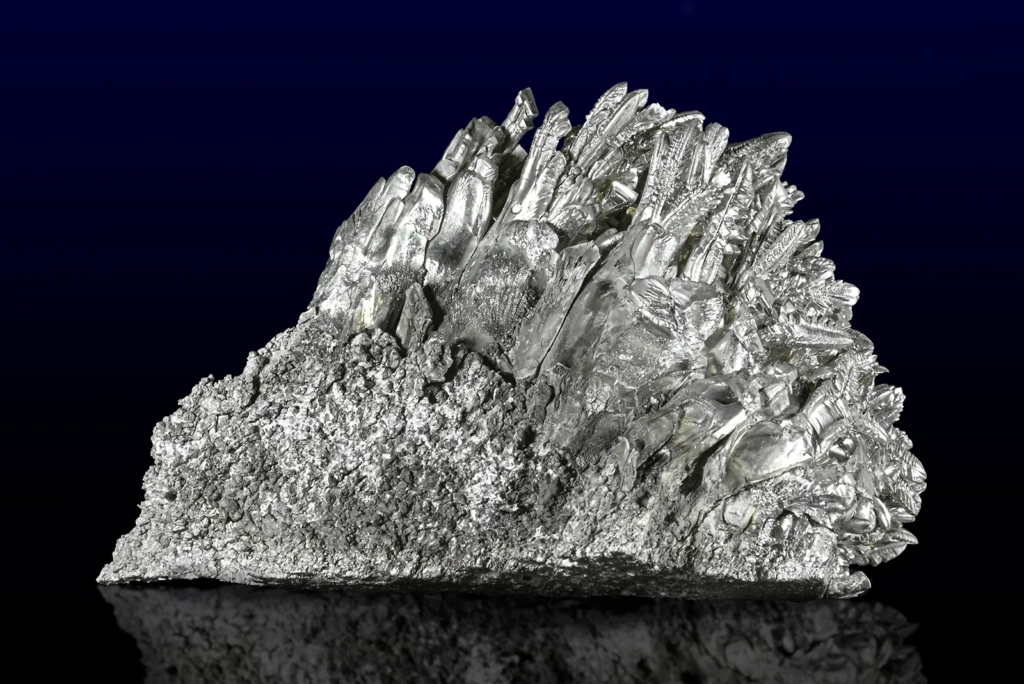
Comparison of physical and chemical properties of materials
Density and lightweighting
With a density of only 64% of that of aluminum (2.70 g/cm³), magnesium is the lightest choice of structural metals and can significantly reduce the weight of parts.
Applicable scenarios: Magnesium is suitable for applications that require high weight reduction.
Such as aerospace, portable electronic devices, and automotive lightweight components (instrument panels, seat frames).
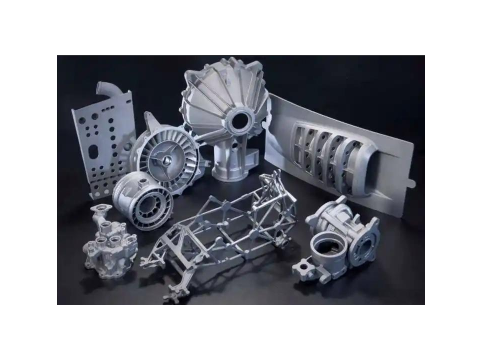
Mechanical properties
The strength and ductility of aluminum are better than those of magnesium, and the rigidity is higher (Mohs hardness 2.0~2.9 vs. magnesium 2.0).
Magnesium has a higher strength-to-weight ratio, but needs to be alloyed (e.g., AZ91D, AM60) to improve creep and fatigue resistance.
Applicable scenarios: aluminum is suitable for components bearing medium to high loads (engine blocks, structural parts).
Magnesium is suitable for use in scenarios where shock absorption is required (tool handles, chassis parts).
Corrosion resistance
The surface of aluminum is easy to form a dense oxide film, which is naturally corrosion-resistant.
Magnesium needs surface treatment (anodizing, coating) to prevent oxidation and corrosion.
Applicable scenarios: aluminum is suitable for outdoor or wet environments (ship components, building structures).
Magnesium is used in corrosion-controlled closed systems (automotive interiors, electronics housings).
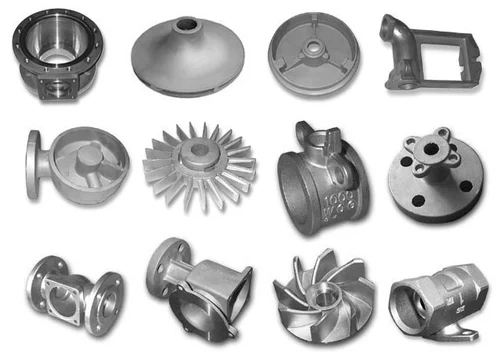
Thermal and electrical properties
The thermal conductivity of aluminum (237 W/m·K) is better than that of magnesium (156 W/m·K), making it suitable for heat sinks and electronic component packaging.
Magnesium has better electromagnetic shielding performance and is suitable for 5G equipment and medical imager housings.
Selection of aluminum metal die casting machine
The core requirements of aluminum die casting are to overcome its high melting point (about 660°C) and to achieve efficient molding of complex thin-walled structures.
According to the material characteristics and process requirements, the cold chamber die casting machine is the preferred equipment for aluminum die casting.
Device type and principle
The metal is melted in an external furnace, and the molten aluminum is injected into the mold at high speed through the hydraulic piston.
Which is suitable for high melting point alloys.
It is divided into two types: horizontal and vertical, and the horizontal type is more mainstream.
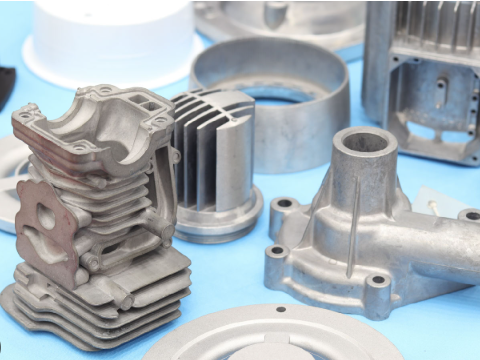
Key parameters
Pressure range: 400-4000 tons, large and complex parts need higher pressure (such as Tesla integrated die-casting needs more than 6000 tons).
Injection speed: 5–10 m/s is required to meet thin-wall filling requirements.
Vacuum-assisted: High vacuum die-casting technology can reduce porosity.
And increase density (e.g., Tesla Model Y uses a 6,000-ton vacuum cold chamber die-casting machine for the rear floor).
Selection of magnesium metal die casting machine
Magnesium alloys have a low melting point (about 650°C), but they are chemically active, easy to oxidize, and require special process control.
Hot Chamber Die Casting Machine
The pressure chamber is immersed in magnesium liquid, the filling speed is fast (the filling time is 30% shorter than that of aluminum),
And it is suitable for thin-walled small parts < 1 kg (e.g. 3C product housing).
Limitations: The clamping force is typically < 7840 kN, not suitable for large, thick-walled parts.
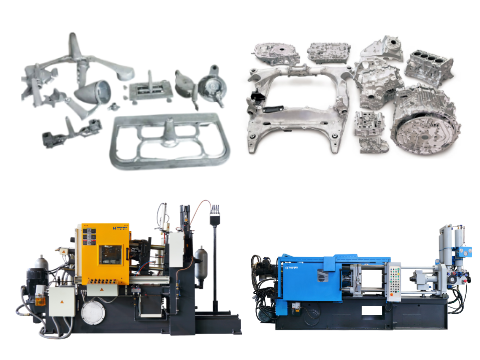