Select ladle in die casting includes material selection, size and shape, operation mode, process requirements, etc.
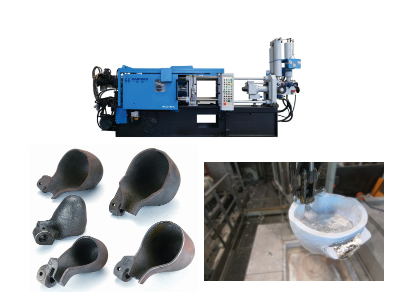
When choosing a ladle for die casting, you need to consider multiple factors, including material properties, operation methods, process requirements, and equipment compatibility.
1. Select ladle in die casting: Material selection
The ladle is usually made of high temperature resistant materials. Such as cast iron, cast steel or heat-resistant steel, which can withstand the impact of high temperature molten metal and reduce heat loss. In addition, the surface of the ladle usually need to coat with a refractory coating to prevent erosion. And moreover, adhesion of molten metal and ensure a longer service life.
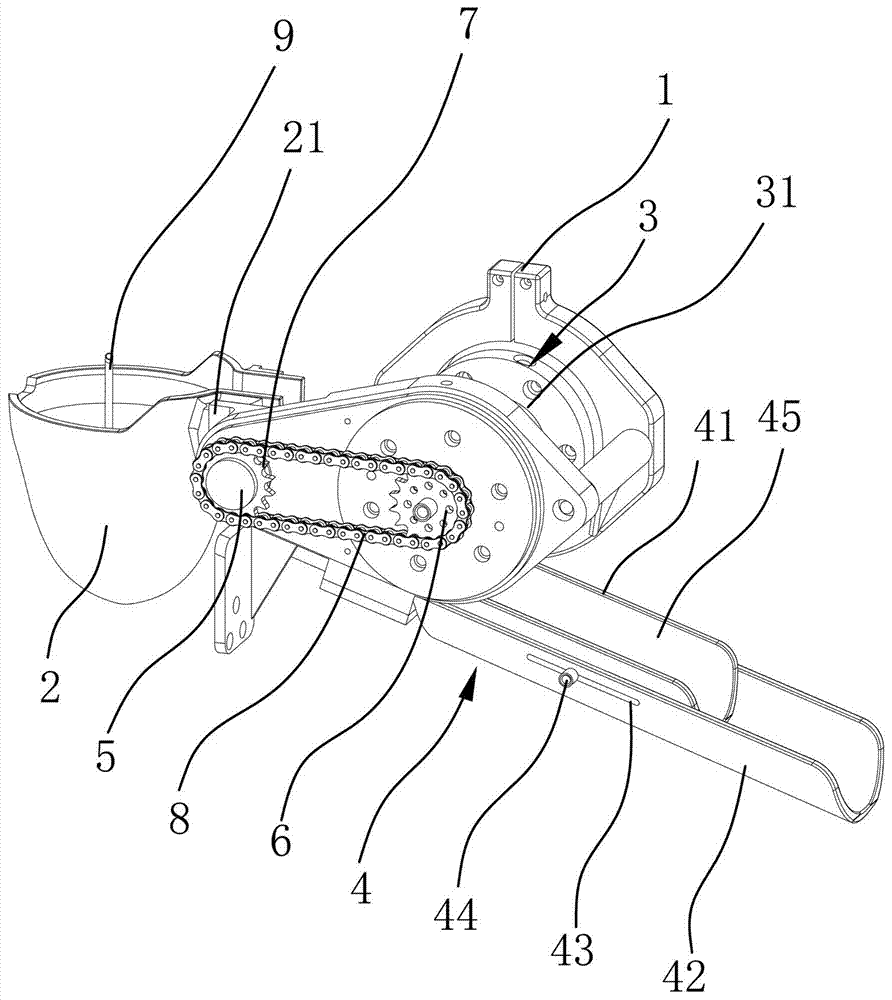
2. Select ladle in die casting: Size and Shape
The size and shape of the ladle should select according to the needs of the die casting process. For example, in the die casting of light alloys such as aluminum and magnesium, the ladle needs to be able to smoothly pour the molten metal into the chamber of the cold chamber die casting machine. The opening design of the ladle is also important. And a wide mouth should use to facilitate the smooth scooping of the molten metal.
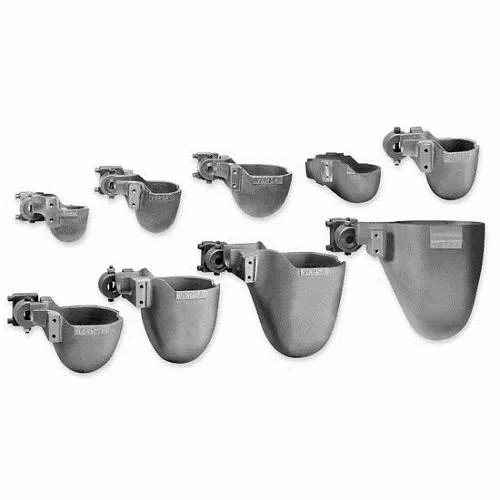
3. Select ladle in die casting: Operation mode
The ladle can manually operate or automate. In automated die casting, the ladle usually mount on a robot or die casting manipulator to achieve efficient and stable metal flow. For manual operation, the handle of the ladle needs to be long enough to allow the operator to safely stay away from the hot metal.
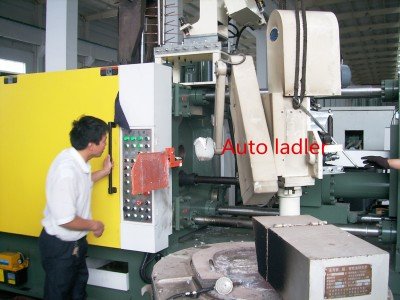
4. Process requirements
In aluminum die casting, special attention should pay to the use of the ladle to avoid oxide film or slag mixing into the molten metal. Therefore, when taking the material, it is necessary to carefully remove the oxide film or slag layer on the surface and ensure that the surface of the molten metal in the ladle is flat. In addition, the ladle need to preheat before using, and the coating should regularly renew during use to prevent contamination.
5. Equipment compatibility
The ladle needs to be compatible with the die casting machine and other related equipment. For example, in cold chamber die casting, the ladle uses to transfer the molten metal from the furnace to the cold chamber. Therefore, the design and specifications of the ladle need to match the production capacity of the equipment.
6. Maintenance and lifespan
The service life of a ladle is closely related to its material and maintenance. For example, in some processes, the use time of the ladle need to control within a certain range (such as 150 hours) to avoid performance degradation due to long-term use. At the same time, regular inspection and replacement of the refractory coating is also an important measure to extend the life of the ladle.
7. Safety and efficiency
The design of the ladle must ensure the safety of operation, such as protecting the operator through reasonable handle length and heat insulation. In addition, efficient ladle design can reduce waste during metal flow and improve production efficiency.
When choosing a ladle for die casting, you need to consider factors such as material properties, size and shape, operation method, process requirements, equipment compatibility, and maintenance life. By making a reasonable choice, you can effectively improve the quality and efficiency of the die casting process.
Haichen die casting machine
Haichen is one Chinese die casting machine manufacturer for more than 10years. We produce both high pressure cold chamber die casting machine , hot chamber die casting machine and spare parts. They have durable and highly precise features.
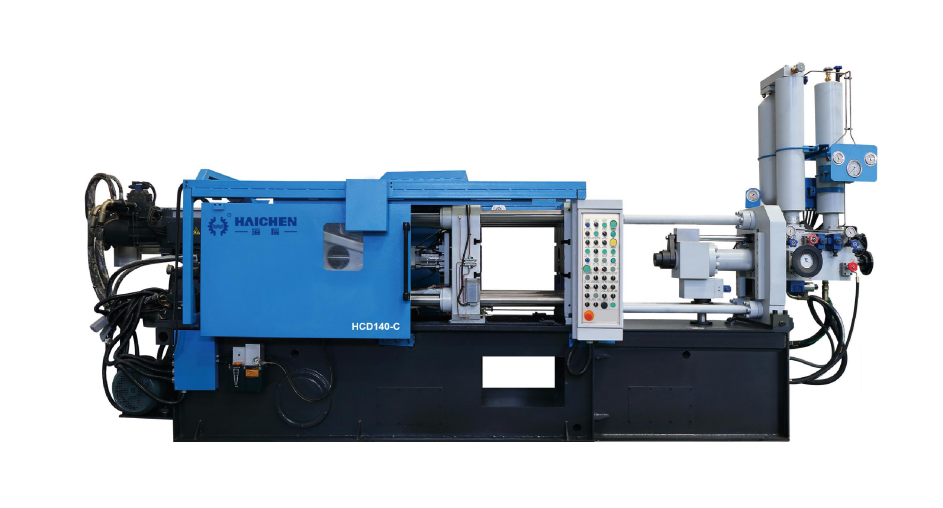
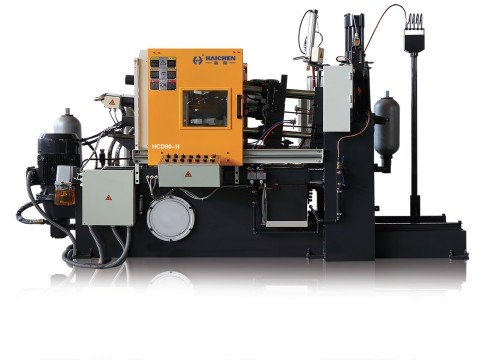
Haichen also produce die casting machine auxiliary equipment. Such as conveyor, vacuum machine, mold temperature controller, industrial robot, sprayer and so on.
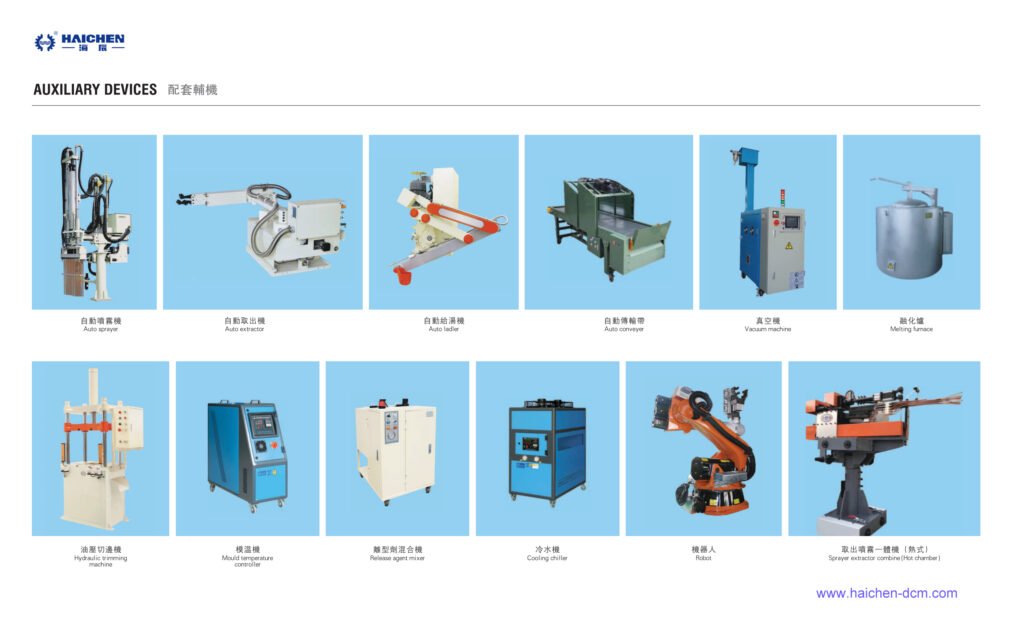
We supply cold chamber and hot chamber die casting machine spare parts.
Welcome contact us.