Selecting the conveyor for a die casting operation need consider material handling requirements,conveyor type, safety and efficiency, and etc.
The best conveyor depends on your part size, temperature, production rate, and automation needs. For most die casting applications, mesh belt or drag chain conveyors are common for cooling, while belt or roller conveyors work well for transfer and sorting.
Steps to selecting the conveyor in die casting
- Material Handling Requirements
- Determine the Type of Conveyor Needed
- Safety and Efficiency
- Durability and Longevity
- Additional Features
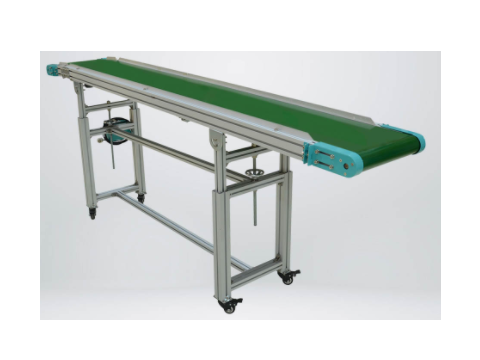
Material Handling Requirements
- Type of Material: Conveyors need to handle both die cast parts and metal scrap. For example, steel belt conveyors are commonly used for moving die cast parts, while special scrap conveyors are designed for handling metal scrap.
- Load Capacity: Ensure the conveyor can handle the weight and volume of materials. Heavy-duty, abrasion-resistant construction materials are essential to withstand the harsh demands of die casting.
Determine the Type of Conveyor Needed
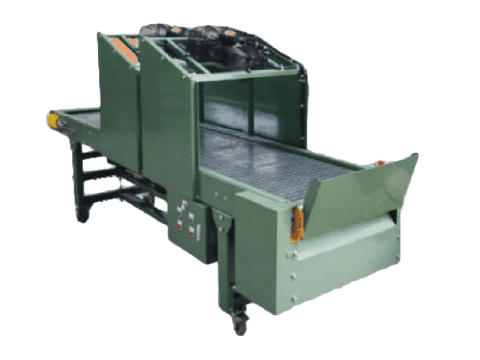
Different conveyors serve different purposes in die casting:
- Cooling Conveyors: Used to cool castings after ejection (e.g., mesh belt, drag chain).
- Transfer Conveyors: Move parts between processes (e.g., belt, roller, or chain conveyors).
- Trim Press Conveyors: Transport parts to trimming stations.
- Sorting/Assembly Conveyors: Used for automated sorting or feeding into secondary operations.
Safety and Efficiency
- Automation: Automated conveyors reduce manual handling, improving workplace safety and reducing the risk of accidents.
- Energy Efficiency: Conveyors with optimized designs and controls can lower energy costs. For example, furnace feeders that continuously meter-feed scrap into the furnace improve energy efficiency.
- Maintenance: Select conveyors with features that reduce maintenance needs, such as heavy-duty construction, belt-tracking enhancements, and auto-lube systems.
Durability and Longevity
- Construction Quality: High-quality welds, reinforcement features, and abrasion-resistant materials contribute to a longer service life.
- Overload Protection: This prevents excessive payloads from overtaxing the conveyor motor
Additional Features
- Drip pans (for lubricant/coolant drainage).
- Cleaning systems (for removing excess oil/debris).
- Adjustable speed controls (for varying production rates).
- Emergency stop & safety guards.
Common Conveyor Types for Die Casting
Type | Best For | Pros | Cons |
---|---|---|---|
Mesh Belt Conveyor | Cooling hot castings | Heat-resistant, allows air/water cooling | Higher maintenance |
Drag Chain | Heavy or abrasive parts | Durable, handles high loads | Noisy, requires lubrication |
Belt Conveyor | General part transfer | Versatile, cost-effective | Not ideal for very hot parts |
Roller Conveyor | Manual or robotic transfer | Simple, low maintenance | Limited cooling options |
Vibratory Conveyor | Sorting and feeding small parts | Gentle handling | Not for heavy parts |
Overhead Conveyor | Space-saving, long-distance transport | Maximizes floor space | Higher initial cost |
What to Consider When Selecting Forging or Die Casting Conveyors
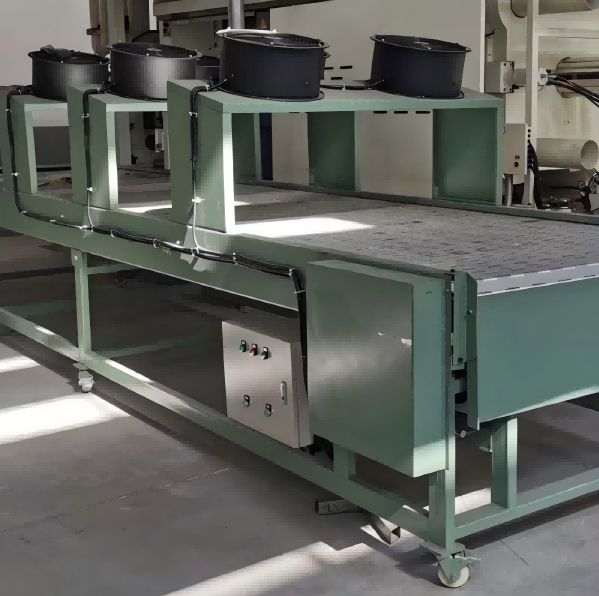
When selecting conveyors for forging or die casting operations, several key factors must be considered to ensure efficiency, safety, and reliability. Here are the main considerations:
Safety
Conveyors that automate material handling can significantly reduce the risk of injuries. Operations that implement automated conveyors have seen workplace safety improve by up to 25%.
Efficiency and Part Quality
Determine whether the parts or materials need to move horizontally, vertically, or at an incline. For longer distances, multiple conveyors used in combination may be more efficient. Features like auto-lube systems and overload protection can reduce downtime and extend the conveyor’s service life.
Durability and Reliability
Use heavy-duty, abrasion-resistant materials to withstand harsh conditions.
How to determine which conveyor is right for my application
To determine which conveyor is right for your application, you need to consider several key factors. Here’s a comprehensive guide based on the latest information:
Determine Transport Volume and Speed The throughput (e.g., scraping or daily processing volume) and speed of the pipe system are key factors in determining the performance of the pipe machine. For example, high throughput requirements may require a wider pipe belt or a higher chain speed.
Die casting machine supplier: Haichen Machinery
Haichen is a die casting machine factory located in Ningbo, China, mainly supplying cold chamber die casting machine and hot chamber die casting machine. Besides machines, we also supply die casting auxiliary equipments and spear parts, including conveyor, spray systems, mold temperature controllers, and industrial robots.
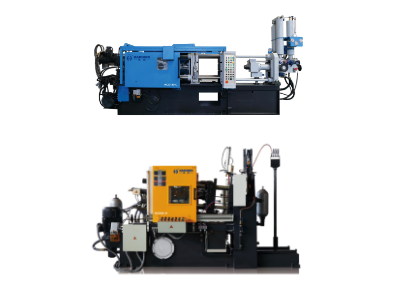
When selecting conveyor belts for die casting production lines, it is necessary to make comprehensive considerations from a number of aspects such as usage conditions, material properties, chain and roller design, load capacity, maintenance costs, and technical parameters, etc., in order to ensure the high efficiency and reliability of the conveyor system.