Advantages of release agent mixer in die casting: Ensures uniform coating,extends mold life by precisely blending and applying release agents
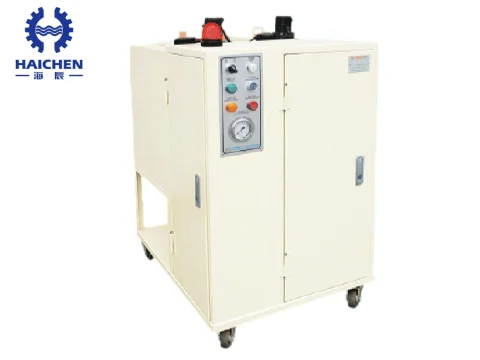
Die casting is an efficient and accurate production process for creating complicated metal parts with close tolerances.
One important stage in this process is the use of release agents to promote the smooth dispatch of cast parts from the mold without adhering to it or forming defects.
In order to achieve the best performance from these agents. A release agent mixer is crucial, in the following we will discuss different benefits provided by it in the die casting process.
Maintaining Uniform Spread
A mixing device guarantees that the release agent is uniformly distributed throughout the length and breadth of the mold surface. This uniformity is important so that certain parts of the mold do not have lots of release agent compared to other areas. Application of the release agent in an inconsistent manner gives rise to defects. Such as stubborn inter-locking of moving parts, shredding, or inconsistent contours on the surface of the manufactured components. By incorporating a mixer, producers are able to achieve adequately controlled layers of charges of release agent which ultimately improves the quality and charm of the products.
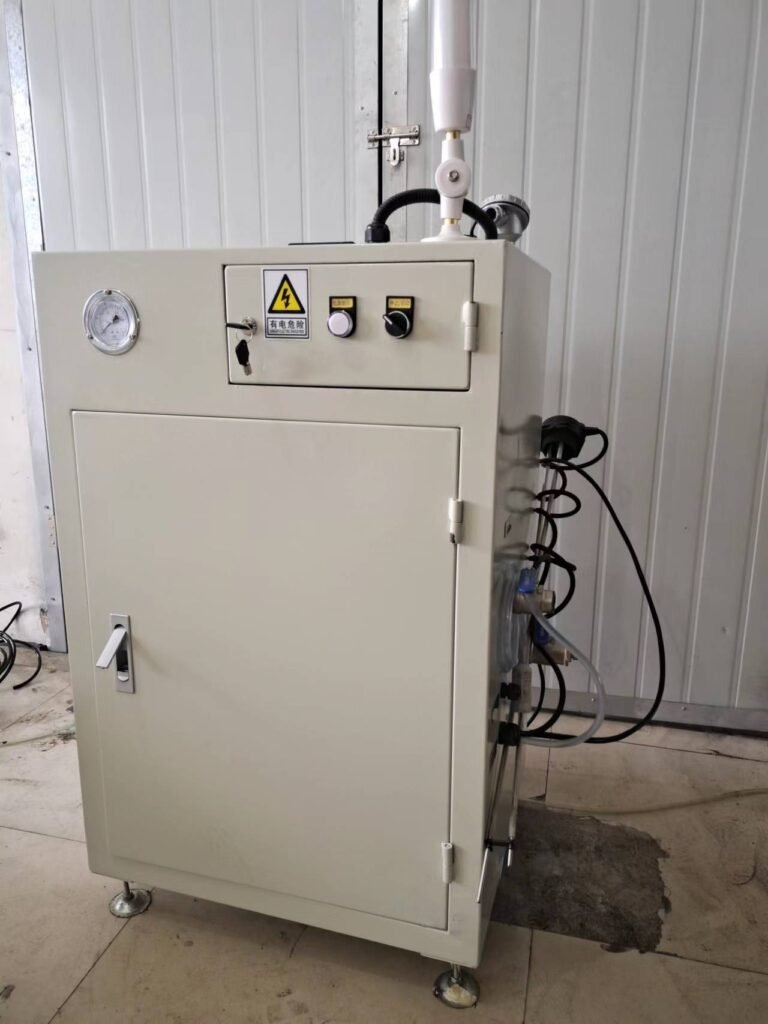
Extending Life Span of the Mold
Proper use of release agents is done with the aid of a mixer. And this goes a long way in preserving the surface of the mold. A release agent that is well mixed is bound to create an ample shield that separates the molten-metal from the mold which diminishes the needless damage caused to mold material. Such guaranteeing marks is going to prolong the lifespan of the mold which translates to lesser replacements. And repair periods for the molds incurred which marks the increased profits to be enjoyed the manufacturer.
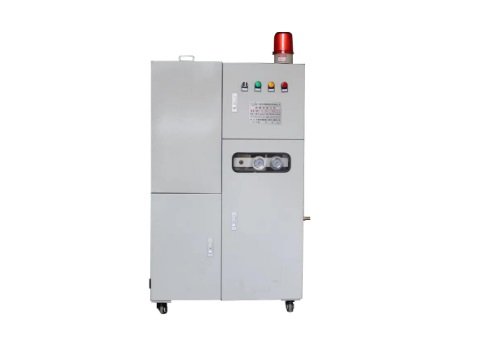
Enhancing Cavity Filling
Release agents and binding agents are consistent when they are properly mixed together. And applied and this enables machines to produce quality work pieces. High standards in the work pieces is further attributed to the aforementioned processes as a guarantee that there are uncontrolled movements of the liquid metal within the gaps in the mold resulting in churning action or capturing of gas bubbles. This leads to castings with less defects, like inclusions or porosity, and a more polished surface finish. Less post-processing is required for high-quality castings unlike low-quality ones. And castings are more likely to pass the rigorous standards of different industries.
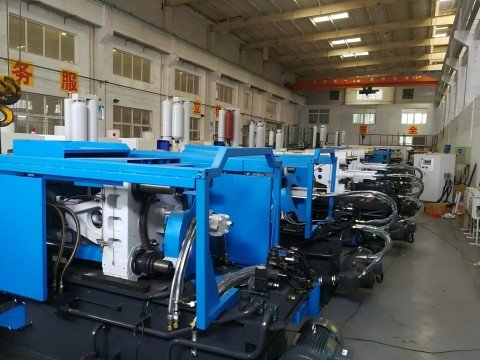
Lowering Greenhouse Gas Emissions
The modern-day release agent mixers have been enhanced to be more ecological in nature. Some of the more advanced models come with controls that limit the application of the release agent, eliminating unnecessary expenditure. In addition to this, some mixers come with capture systems that reuse excess release agents. Further reducing the automatic eco-footprint of the agent. There are numerous other benefits that come with having a release agent mixer. As manufacturers are able to lower their emissions and easily meet eco requirements.
Improvement of Release Agent Mixers
The use of release agent mixers during die casting increases the chances of efficient execution. Quantitative application of release agents alone allows for reduction in cycle time for castings. This has a direct correlation to the parts output within a specific duration. hence resulting in severe improvement of production efficiency. Another improvement is the lowered wastage of materials as a result of lowered defects and re-work subsequently boosted efficiency.
Usage Flexibility and Customization
Release agent mixers are adaptive in terms of die casting operations as they offer various levels of customization to suit specific requirements or preferences of the customers. Release mixing devices can be changed for different release agents, mold dimension, and even the materials used for casting. This freedom allows all manufacturers to adjust their processes for each individual project, providing optimization to achieve the best results every time.
HAICHEN’s Commitment to Medals
At HAICHEN, we put our focus to offer the most competently engineered die casting machines to optimize the productivity and efficacy of the manufacturing process. As a minimum standard, every customer is guaranteed a maximum quality casting. And a minimum of twelve defects because of advanced features, like sophisticated release agent mixers, incorporated into our machines. With our release agent mixers, die casting operations experience greater mold life, better casting quality. And higher production outputs while becoming more eco-friendly.
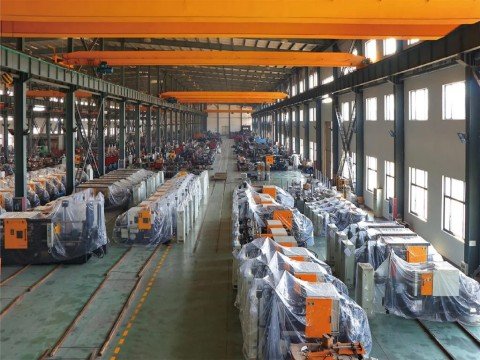
There are many advantages of release agent mixer in die casting. Benefits of using a release agent mixer in die casting include but are not limited to mold life increase, casting quality enhancement, production efficiency improvement and ensured uniform distribution making it a key element for any die casting operation.