Advantages of Aluminum Die Casting Parts include high strength, lightweight design, precision, cost-effectiveness, and design flexibility.
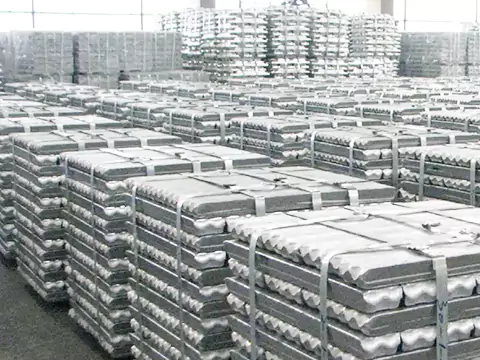
Aluminum die casting is a widely used manufacturing process that involves injecting molten aluminum into a mold under high pressure to produce complex and precise parts. This process offers numerous advantages over other manufacturing methods, making it a popular choice for industries such as automotive, aerospace, and consumer electronics.
Advantages of Aluminum Die Casting Parts
1. High Strength and Durability
Aluminum die casting parts are known for their high strength and durability. Despite aluminum’s relatively low density, it offers excellent mechanical properties, including high tensile strength and good resistance to corrosion. This makes aluminum die casting parts ideal for applications where strength and reliability are crucial, such as in automotive engines, transmission housings, and structural components.
2. Lightweight
One of the most significant advantages of aluminum die casting is its lightweight nature. Aluminum is approximately one-third the weight of steel, which makes it an excellent choice for applications where weight reduction is essential. In the automotive and aerospace industries, using aluminum die casting parts can significantly improve fuel efficiency and reduce emissions, contributing to more sustainable transportation solutions.
3. Precision and Complexity
Aluminum die casting allows for the production of highly precise and complex parts with tight tolerances. The high-pressure injection process ensures that the molten aluminum fills even the most intricate mold cavities, resulting in parts with excellent dimensional accuracy and surface finish. This precision is critical for applications such as electronic housings, where tight tolerances are necessary to ensure proper fit and function.
4. Cost-Effective
Aluminum die casting is a cost-effective manufacturing process, especially for high-volume production. The ability to produce large quantities of parts quickly and with minimal waste makes it an economically viable option. Additionally, the durability and longevity of aluminum parts reduce the need for frequent replacements, further lowering overall costs.
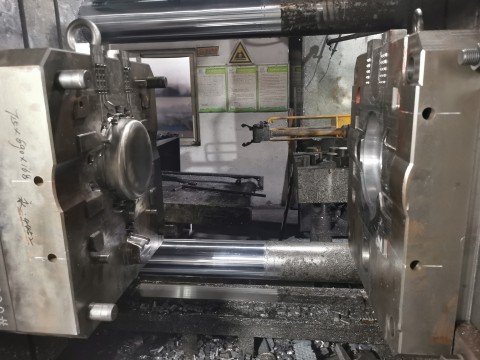
5. Design Flexibility
Aluminum die casting offers significant design flexibility. Engineers can create parts with complex geometries and integrated features, reducing the need for secondary operations and assembly. This not only saves time and money but also enhances the overall performance and functionality of the final product.
6. Energy Efficiency
Aluminum is a highly recyclable material, and die casting processes can be designed to minimize energy consumption. HAICHEN, a leading die casting machine manufacturer, focuses on developing energy-efficient machines that reduce operational costs and environmental impact. By using advanced control systems and optimized processes, HAICHEN machines ensure that aluminum die casting remains a sustainable manufacturing choice.
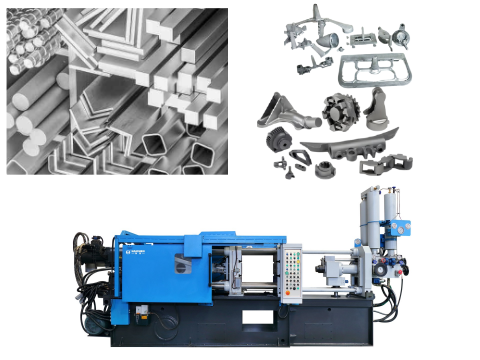
7. Aesthetic Appeal
Aluminum die casting parts can achieve excellent surface finishes, making them suitable for applications where appearance is important. The ability to produce parts with smooth surfaces and fine details enhances their aesthetic appeal, which is particularly valuable in consumer electronics and automotive exteriors.
Advantages of Aluminum Die Casting Parts including high strength, lightweight, precision, cost-effectiveness, design flexibility, energy efficiency, and aesthetic appeal. These benefits make aluminum die casting a preferred choice for a wide range of industries. With manufacturers like HAICHEN leading the way in die casting technology, the future of aluminum die casting looks promising. Whether for automotive components, consumer electronics, or industrial applications, aluminum die casting continues to play a crucial role in modern manufacturing.