The advantages of mould temperature controller include improved surface quality, enhanced structural integrity, and increased production efficiency.
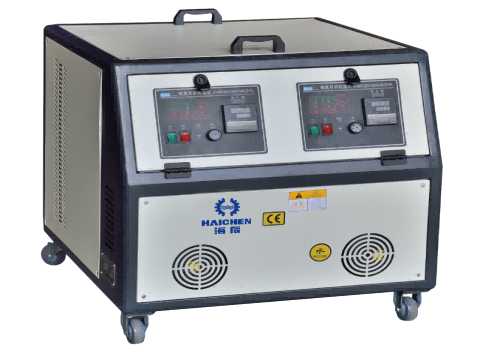
Die casting mold temperature controller is a system designed to regulate the mold temperature during die casting operations.
Advantages of Mould temperature controller
Improved Surface Quality
Maintaining consistent mold temperature helps achieve an even and smooth surface on your castings. This is because even temperature distribution prevents hot and cold spots, which can lead to surface defects.
Enhanced Structural Integrity
Proper mould temperature control contributes to the structural integrity of your castings. It ensures that the molten metal solidifies evenly, reducing the risk of internal defects such as porosity and shrinkage.
Improved Production Efficiency
By maintaining an optimal mold temperature, the cooling time of your castings can be significantly reduced. This results in faster cycle times and increased production output.
Reduced Material Waste
Consistent mould temperatures lead to fewer casting defects, which means less material waste due to rejected parts. This not only saves on material costs, but also improves the efficiency of the entire process.
Advantages of Mould temperature controller-Extended Mold Life
Exposure to extreme temperatures causes molds to wear and degrade over time. Mold temperature controllers help reduce thermal shock and fatigue, thereby extending the life of your molds.
Better Dimensional Control
Regulating mould temperature ensures dimensional stability in your castings. This is critical for parts that need to fit and function precisely in their end application.
Haichen-Mold Temperature Controller
At Haichen, we proudly integrate advanced mould temperature controllers into our die casting machines.
Our systems provide precise temperature regulation, ensuring optimal conditions for each die casting cycle and resulting in superior part quality.
Our mould temperature controllers are able to provide even heat distribution across the die, which is critical to maintaining dimensional accuracy and reducing defects in the final product.
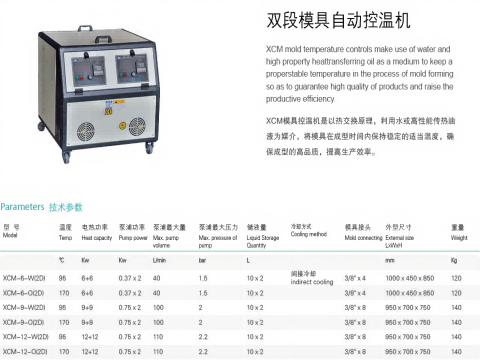
Using a die casting mould temperature controller offers many advantages, including improved part quality, increased production efficiency, and reduced material waste.
By maintaining optimal mold temperature, manufacturers can achieve consistent performance and energy efficiency while extending the life of their equipment.