Crankcase Making Machine has many advantages, which are as follows:
- Increased productivity
- Improving product quality
- Reduced production costs
- Enhanced Structural Strength and Rigidity
- Adapting to complex design needs
- Reduced mold wear
The crankcase is a key component of the engine, which needs to withstand high loads, high temperatures, and has complex structures, such as oil passages and support structures.
Die-casting machines are highly suitable for manufacturing high-precision and high-efficiency parts, and are ideal for producing complex thin-walled components.
In addition, the crankcase needs to have good sealing and heat dissipation properties. Die-casting can ensure the integrity and sealing of the parts and reduce the risk of leakage.
Moreover, high-pressure filling in die-casting can reduce porosity, increase the density of castings, and enhance mechanical properties.
For instance, die-cast aluminum alloy crankcases may be lighter than those made by traditional casting while maintaining strength.
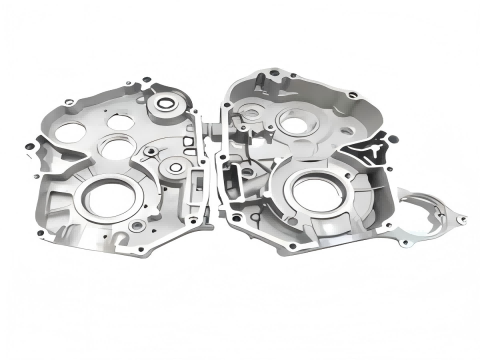
Crankcase Making Machine Advatnages—Increased productivity
The die casting process is an efficient high-volume production process for the demand for large quantities of parts and components in the automotive industry.
By adopting high vacuum die casting technology, the porosity defects of castings can be significantly reduced, and the production efficiency and pass rate can be improved.
For example, all-in-one die casting technology enables the integration of multiple parts in a single form, which significantly reduces manufacturing time.
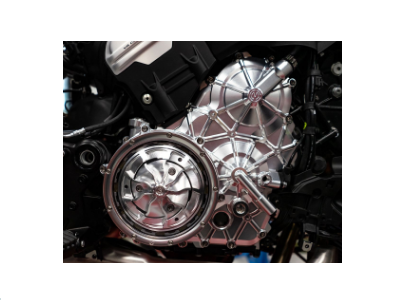
Crankcase Making Machine Advatnages—Improving product quality
The die casting process improves the quality and performance of components by achieving a high degree of precision and consistency.
Ensuring that each transmission body or housing is essentially the same size and shape.
In addition, high vacuum die-casting technology can also improve the internal porosity state and mechanical properties of castings.
And further improve the qualification rate and tensile strength of products.
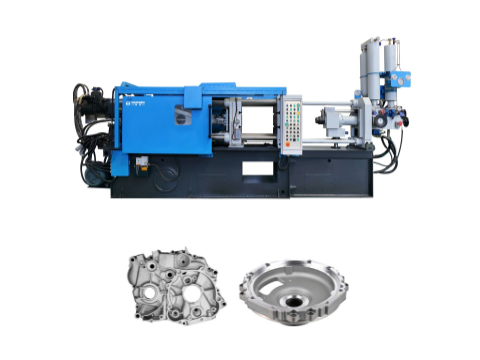
Crankcase Making Machine Advatnages—Reduced production costs
Die casting technology reduces manufacturing costs by reducing the number of parts and welds.
For example, integrated die casting technology can simplify multiple stamping and welding steps in the traditional process into a single mold, resulting in significant savings in equipment and labor costs.
In addition, the high recycling rate of waste further reduces the consumption of raw materials.
Crankcase Making Machine Advatnages–Enhanced Structural Strength and Rigidity
Die-cast manufactured transmission bodies typically have high strength and rigidity.
Which helps ensure that the overall transmission system is structurally robust and improves the durability and safety of components.
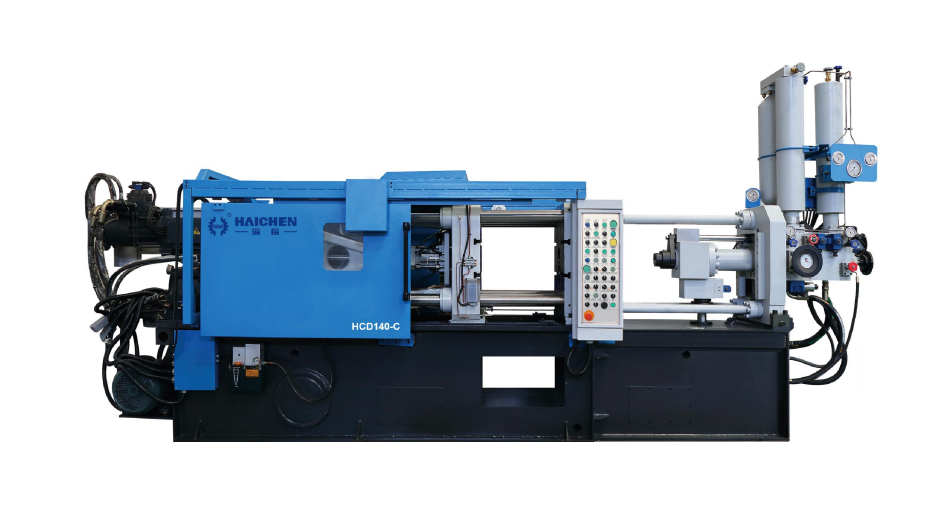
Crankcase Making Machine Advatnages–Adapting to complex design needs
The die-casting process can easily achieve the manufacture of complex shapes and details.
So that components such as transmission valve bodies can be precisely manufactured to meet complex design requirements.
Crankcase Making Machine Advatnages–Environmental protection and energy saving
The use of high vacuum die-casting technology can reduce energy consumption and waste generation.
And at the same time improve material utilization, in line with the development trend of low-carbon environmental protection.
Crankcase Making Machine Advatnages–Reduced mold wear
The real-time injection control system can effectively eliminate flash, extend the life of the mold, and reduce maintenance costs.
How can crankcase manufacturing mechanical technology achieve advantages
- Creating negative pressure
- Removal of gas from the cavity
- Increase the pumping rate
- Optimize mold design
- Reduced cavity back pressure
- Improve filling conditions
- Improve the density of castings
- Optimize the spraying process
- Reduced cavity back pressure
- Improve filling conditions
- Optimize the spraying process
- Reasonable selection of high-speed switching point
Creating negative pressure
By creating negative pressure in the mold cavity, porosity and dissolved gases in the casting are significantly reduced or eliminated.
Thereby improving the mechanical properties and surface quality of the casting.
Removal of gas from the cavity
In the die-casting process, the air in the cavity of the mold is quickly removed by means of a vacuum system to bring the cavity to a near-vacuum state (vacuum degree ≤ 80 mbar).
This step can greatly reduce the possibility of porosity formation due to turbulent molten metal being involved in the gas, and basically eliminate the cause of porosity inside the casting.
Increase the pumping rate
The purpose of vacuuming from the pressure chamber is to increase the pumping rate, reduce the influence of flue gas and water vapor on the casting.
Thereby increasing the vacuum degree in the cavity and ensuring the reliability of high vacuum die casting.
Optimize mold design
High vacuum die-casting technology requires that mold design needs to consider factors such as part structure and product quality requirements to ensure fast and stable filling of metal melt.
At the same time, the gate runner design needs to ensure that the molten metal fills all the grooves of the mold evenly.
Reduced cavity back pressure
Vacuum die casting can significantly reduce the back pressure of the mold cavity, allowing the liquid metal to fill the cavity under negative pressure, thereby reducing the formation of porosity.
Improve filling conditions
The vacuum die-casting method discharges 80%~90% of the gas in the mold cavity before high-speed filling.
Which has a low probability of bubble formation and a small risk of porosity in the casting during high-speed filling.
Improve the density of castings
Through the application of dual-channel high vacuum technology, reduce the gas content in the mold cavity and pressure chamber to make it close to the vacuum state.
And increase the application of purification and degassing technology to reduce the gas content of the melt, thereby reducing the generation of pores inside the casting.
Optimize the spraying process
Adjust the spraying trajectory and time, reduce the residual release agent on the surface of the mold.
Avoid instantaneous vaporization when in contact with high-temperature molten aluminum, and eliminate porosity defects.
Reasonable selection of high-speed switching point
Reasonable selection of high-speed switching point has a great impact on the internal quality of castings.
And at the same time, the mold pouring system is improved according to the internal quality requirements of the product.
Which is of positive significance to the improvement of the quality of die castings.
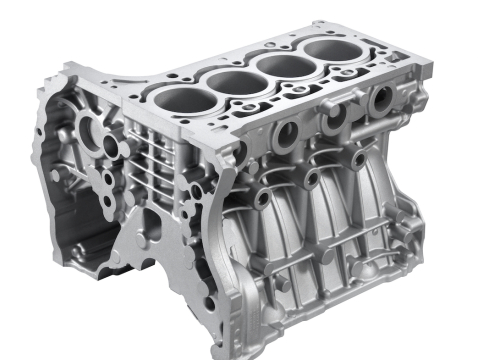
Haichen Die Casting Machine Advatnages
Die casting machines can not only be used to produce key components such as gearbox housings and valve bodies.
But also can significantly improve production efficiency and product quality by optimizing process parameters and mold design, meeting the stringent requirements of the modern automotive industry for transmission components.
Transmission die-casting machine has become an indispensable and important equipment in modern automobile manufacturing by improving production efficiency.
Improving product quality, reducing production costs, enhancing structural strength, adapting to complex design needs, and environmental protection and energy saving.