Aluminum die casting manufacturers are NEMAK, RYOBI, GEORGFISHER, Alcoa Corporation, PIERBURG, Wencan Co., Ltd., and Xusheng Group.
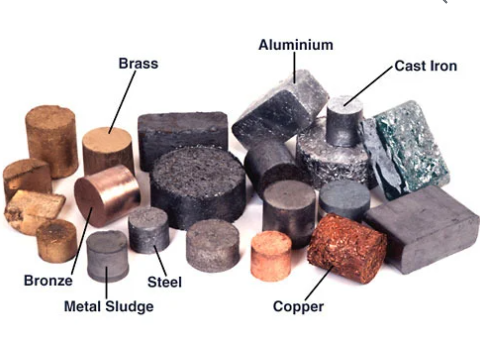
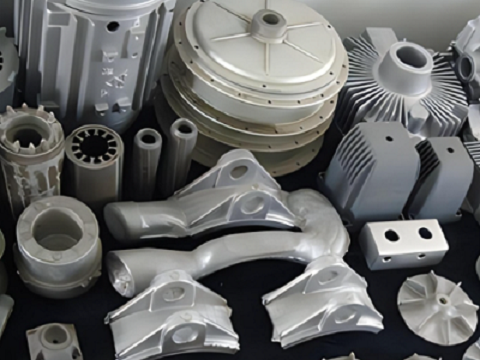
Core application areas
Automobile industry: engine parts, transmission housings, body structural parts, etc., accounting for more than 70%.
Aerospace: lightweight airframe components and engine parts.
Electronics & Communications: Heat Sinks, Connector Housings.
Consumer goods: home appliances, power tools, etc.
Alcoa Corporation
Production capacity and technology
In 2023, the output of primary aluminum will be 2.1 million tons, with 39 smelters, 87% of the production capacity will use renewable energy, and the carbon emission intensity will be 1/3 of the industry.
Market position
The world’s top five aluminium producers, with revenue of $2.9 billion in 2023, and high margins despite volatile alumina prices.
Customer rating
Employees rated 3.9/5 and customers recognized the high quality of its low-carbon aluminium products, such as EcoLum, in the automotive and aerospace sectors.
Dynacast International
Located in North Carolina, USA, with an annual output of more than 5 billion pieces, focusing on precision micro die castings (zinc/aluminum alloy).
Leading precision die casting technology for high-complexity, small-size (millimeter-level) parts.
And the California factory has been certified for automotive applications.
Market share
The global die casting market accounts for about 9.6%, focusing on the medical and electronics fields,
With 13 production bases (the United States, Europe, Asia), and the Suzhou factory in China accounts for 15% of its global production capacity.
Ryobi
Founded in 1943 (formerly known as a Japanese die-casting mold manufacturer), the company is headquartered in Hiroshima Prefecture, Japan.
It has the world’s largest tonnage die-casting machine (12,000 tons) and can produce 2.5 meters × 1.8 meters of integrated body panels.
In 2024, it will invest $50 million to expand its plant in Mexico and add five new large-scale die-casting machines to target the electric vehicle market.
Technical advantages
The output of sub-frames has increased from 25,000 pieces/year in 2005 to 400,000 pieces/year in 2021, and the global production network covers the United States, China and Thailand.
Ryobi occupies the high ground in the wave of automobile lightweight by virtue of ultra-large die-casting technology, Japanese lean manufacturing, and in-depth customer binding.
Nemak
Founded in Mexico in 1979 as part of Alfa S.A.B.
The core business is die-casting of aluminum auto parts, such as engine blocks, transmission housings, new energy battery trays, etc.
Nemak is one of the world’s largest suppliers of automotive aluminum die castings, accounting for 12% of the global automotive die casting market.
With an annual production capacity of more than 3 million tons, and 35 factories worldwide (12 in Mexico, 8 in Europe, and 3 in China).
Guangdong Hongtu Technology Co., Ltd
The first listed company in China’s aluminum die-casting industry.
The only two companies in the world that have mastered the 6800T ultra-large integrated die-casting technology.
Has the largest domestic market share, with a revenue of 7.615 billion yuan in 2023, and the die-casting business accounts for more than 70%.
Core customers include Mercedes-Benz, Volkswagen, and NIO.
And have won the “Global Excellent Supplier” award from General Motors for six consecutive years.
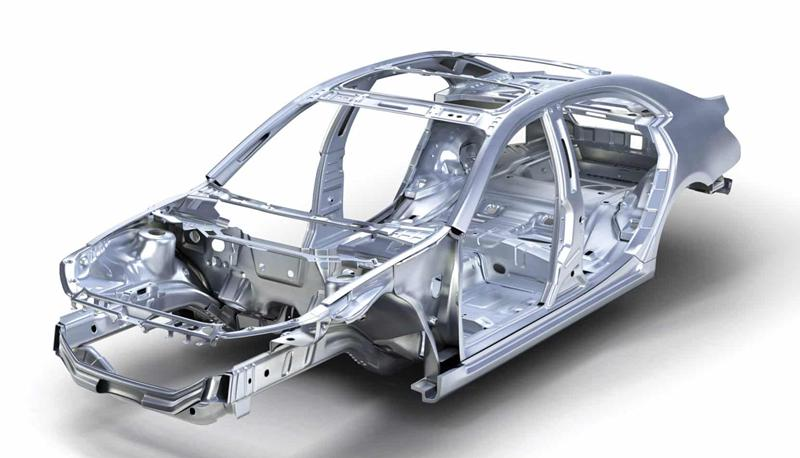
Technological breakthrough
integrated die-casting technology realizes corner overtaking, and the weight of body structural parts is reduced by 30%.
The world’s first 6800T die-casting machine (jointly developed by LK Technology), and mass production of Tesla Model Y rear floor in 2022.
In 2024, the 12,000T die-casting island will be put into production, which can form a 2.2m size front cabin assembly (40% weight reduction and 600 connection points).
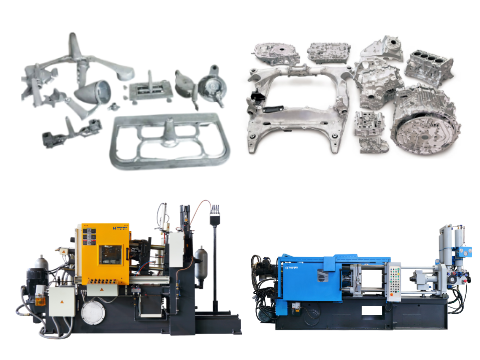
Wencan
It is the first company in China to achieve integrated die-casting mass production of front and rear body (NIO ET5).
And is one of the world’s top five suppliers of body structural parts, with a market share of 8% in Europe (through the acquisition of the French Bailian Group).
In 2023, the revenue of new energy business will account for 67%, ranking first in the industry.
The core business includes aluminum alloy high-pressure/vacuum die-casting, focusing on new energy body structural parts and three-electric systems.
Ningbo Xusheng
The company, which was founded in 2003 and is based in Ningbo, Zhejiang Province, primarily focuses on manufacturing die-cast components for new energy vehicles’ three-electric systems, such as battery trays, electric drive housings, and thermal management parts.
The ultra-thin-wall die-casting technology can mass-produce radiators with a wall thickness of 1.2mm (the industry limit of 1.5mm) and reduce weight by 30%.
In addition, the porosity of vacuum die-casting is 0.07%, which meets the requirements of air tightness of battery explosion-proof valve (IP67 standard).
Patent layout
Xusheng has 61 patents related to thin-walled die-casting (including 3 PCT patents in the United States).
And at the same time, the original “gradient pressurization” technology solves the problem of insufficient filling of thin-walled parts.
Industry status
The world’s largest supplier of battery trays for new energy vehicles (35% market share).
At the same time, it is also the core supplier of Tesla’s die-casting parts (more than 10 years of cooperation, Model 3/Y single car worth 2,500 yuan).
In 2023, the gross profit margin will be 29.1% (the industry average is 22%), and the profitability will lead the industry.
Ningbo Haichen
Ningbo Haichen machinery was founded in 2005, Located in Ningbo, Zhejiang, China.
HAICHENspecializes in the production and sale of hot chamber die-casting machines, cold chamberdie-casting machines, servo die casting machines, magnesium alloy die casting machines and relative auxiliary equipment.
HAlCHEN always places more emphasis on the technology and management. Because of its ad-vanced fechnology, high quality and effective management, “HAlCHEN”‘s hot chamber as well ascold chamber die-casting machines has won the trust from our clients at home and abroad.
Industry technology trends
High vacuum die-casting and heat treatment optimization: improve the mechanical properties of parts and reduce porosity defects.
Intelligent manufacturing
Industrial Internet and AI defect detection system improve efficiency, Guangdong Hongtu introduces dynamic optimization algorithms.
Material innovation
The development of high-silicon aluminum alloys (such as AlSi12Cu) to meet the needs of thin-walling, and the utilization rate of recycled aluminum has been increased to 60%.
Market demand and growth forecasts
Market size
The global aluminum die casting market will be 89.2 billion yuan in 2024 and is expected to reach 124.4 billion yuan in 2030 (CAGR 5.7%).
Driving factors
lightweight of new energy vehicles (200kg of aluminum for a single vehicle → 350kg in 2030) and heat dissipation requirements for 5G base stations.
Regional growth
The Asia-Pacific region accounts for 46%, China contributes 30% of the world’s production capacity, and North America favors local manufacturers due to tariff policies.
Challenges and coping strategies
Cost pressure
Aluminum price fluctuations affect net profit (3-5% profit for every 10% increase).
And companies control costs through futures price locking and recycled aluminum substitution (such as Alcoa’s use of 30% recycled aluminum).
Environmental protection regulations
In order to meet the foundry industry air pollutant emission standards (particulate matter ≤20mg/m³).
Guangdong Hongtu has invested 5% of its annual revenue in green process upgrades, demonstrating its commitment to environmental sustainability
Technical talent gap
The demand for compound talents in the industry has increased by 15% year-on-year, and school-enterprise cooperation training has become a trend.
Competitive Landscape Analysis
Global concentration: CR5 is about 35%, with Alcoa, Ryobi, and Nemak as the first echelon.
Chinese companies go overseas
Guangdong Hongtu and Wencan build factories in Mexico.
With a cost 40% lower than that in North America, seizing Tesla’s supply chain.