Aluminum vs Magnesium die casting application comparison includes material characteristics, manufacture process, economical, etc.
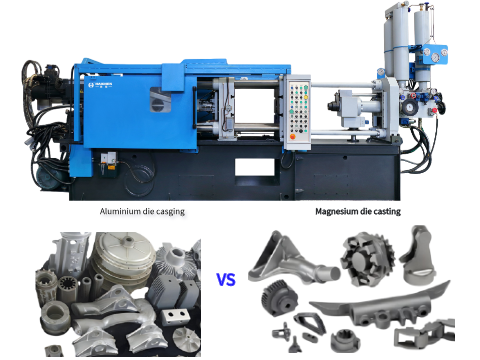
Aluminum die casting and magnesium die casting each have their own advantages in the application field. Also in their choice depends on specific needs. The following provides a detailed comparison in terms of material properties, manufacturing processes, economy, and application areas:
1. Aluminum vs Magnesium die casting application comparison: Material characteristics
Density and strength: The density of magnesium alloy is about 2/3 of that of aluminum. But the specific strength of magnesium alloy is higher than that of aluminum. Which means that magnesium alloy can provide higher strength while reducing weight. However, the yield strength and tensile strength of magnesium alloys are usually lower than those of aluminum alloys.- Thermal conductivity: The thermal conductivity of magnesium alloy is about 1/2 of that of aluminum. Which gives magnesium alloy an advantage in heat dissipation performance. Such as used in car radiator brackets and dashboard frames.
Processing performance: Due to its hexagonal close packed crystal structure, magnesium alloys have poor processing performance. Especially prone to deformation at high temperatures.- In contrast, aluminum has better processing performance. But magnesium alloys can improve their processing performance by optimizing processes such as vacuum die casting.
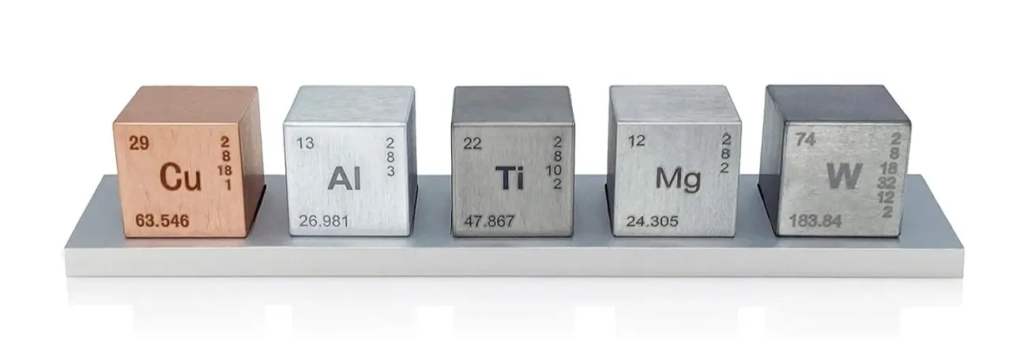
2. Aluminum vs Magnesium die casting application comparison: Manufacturing process
Die casting process: Both magnesium alloys and aluminum are suitable for high pressure die casting (HPDC). But magnesium alloys have shorter die casting cycles and longer die life. In addition, magnesium alloys can be efficiently produced through cold chamber die casting and hot chamber die casting.
Vacuum die casting: Vacuum die casting technology can significantly reduce the pores in magnesium alloy castings. Moreover, improve their mechanical properties and heat resistance. Aluminum die casting rarely uses vacuum technology because aluminum has better fluidity. And it does not require additional gas removal.
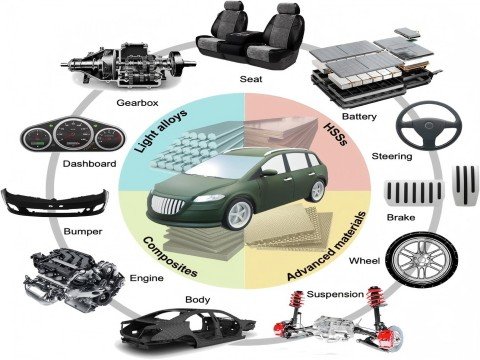
3. Aluminum vs Magnesium die casting application comparison: Economical
- Cost comparison: The smelting cost of magnesium alloy is relatively high, but its lightweight effect is significant. Every 10% reduction in vehicle weight can save 6%-8% of fuel consumption.Although aluminum has a lower smelting cost, it is heavier and cannot completely replace magnesium alloy.
- Energy consumption: The smelting of magnesium alloy requires higher energy. But its energy consumption in the die-casting process is lower than that of aluminum.
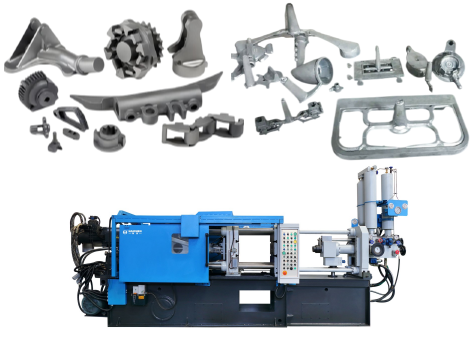
4. Application areas
Automotive industry: Magnesium alloys widely use in automotive parts due to their lightweight properties. Such as dashboard brackets, seat brackets, steering columns, etc. Magnesium alloys also use in complex structural parts, such as gearbox housings and body beams
In contrast, aluminum die casting is more used for body structural parts and engine parts
Other fields: Magnesium alloys are also widely used in consumer electronics (such as mobile phone housings) and aerospace. Aluminum die casting occupies an important position in construction. In addtionally, it’s in industrial equipment due to its good corrosion resistance and mechanical properties.
5. Future development trends
With the decline in magnesium alloy prices and technological advances (such as vacuum die casting and rare earth modification), the application range of magnesium alloys will be further expanded.At the same time, the combined use of magnesium alloys and aluminum alloys (such as magnesium-aluminum composites) is also being studied to further improve performance.
Aluminum die-casting technology is also being continuously optimized, such as improving production efficiency by improving mold design and process parameters.
Magnesium die casting and aluminum die casting each have their own advantages and disadvantages. Magnesium alloys are suitable for areas that need to reduce weight (such as automotive parts) due to their light weight, high strength and good heat dissipation performance, while aluminum die casting is suitable for a wider range of industrial and construction fields due to its low cost and good processing performance. In the future, with the advancement of technology and changes in market demand, the application fields of the two materials may further cross and merge.
Haichen die casting machine
Haichen is one Chinese die casting machine manufacturer for more than 10years. We produce both high pressure cold chamber die casting machine , hot chamber die casting machine and spare parts. They have durable and highly precise features.
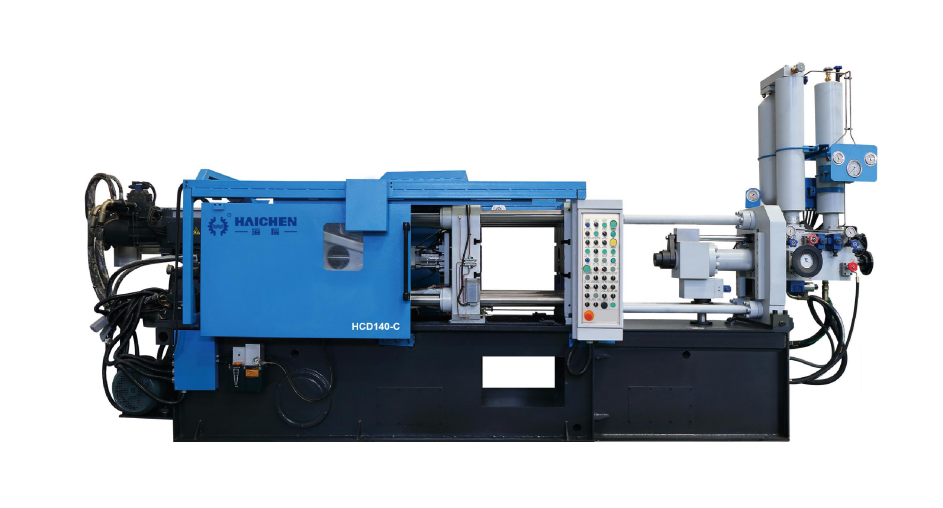
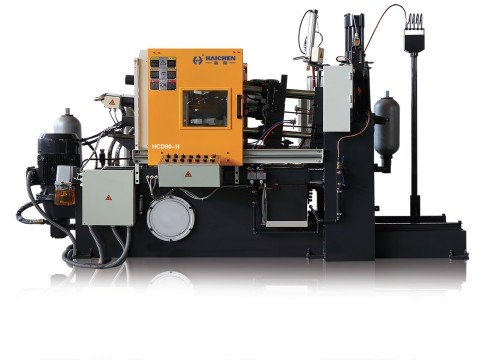
Haichen also produce die casting machine auxiliary equipment. Such as conveyor, vacuum machine, mold temperature controller, industrial robot, sprayer and so on.
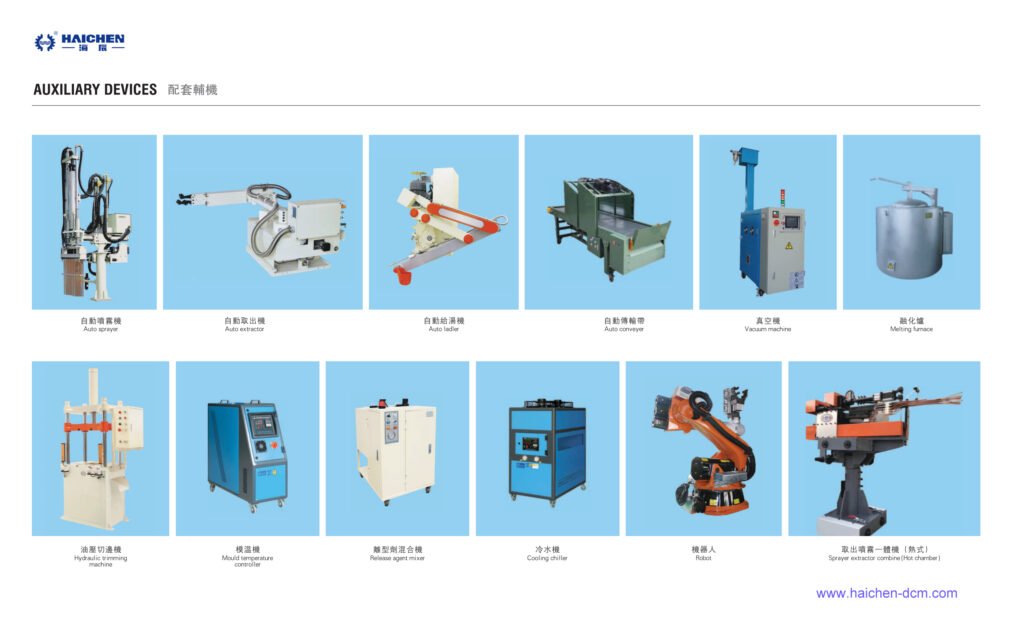
We supply cold chamber and hot chamber die casting machine spare parts.
Welcome contact us.