In die casting operations, the boosting handwheel (or booster handwheel) is a specialized manual control device used to enhance precision, safety, and efficiency in machine adjustments. Below are its key applications:
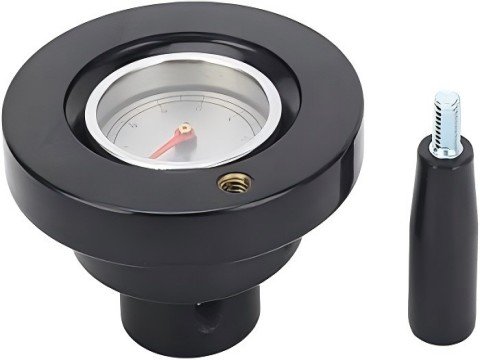
Applications of Boosting Handwheel in Die Casting Operations
Boosting handwheels are not a common term in die casting operations. However, the concept of “boosting” in die casting is widely used, especially through boosting cylinders, which have several important applications in die casting operations:
Improving Casting Quality
Boosting cylinders are used to increase the injection pressure during the die casting process. This helps in filling the mold cavity more effectively, especially for complex shapes and thin-walled parts.
By providing a higher pressure, the metal can flow more uniformly into the mold, reducing defects such as porosity, cold shuts, and misruns.
Enhancing Production Efficiency
Boosting systems can significantly improve production efficiency. By ensuring that the mold is filled quickly and completely, the cycle time can be reduced. This leads to higher throughput and overall productivity in the die casting process.
Handling Complex and Thin-Walled Parts
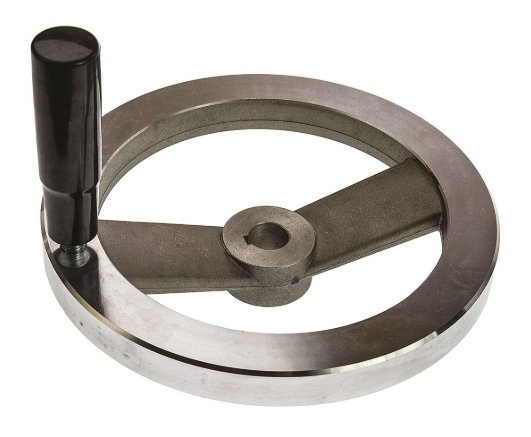
In the production of complex and thin-walled parts, boosting cylinders play a crucial role. These parts require precise control of injection pressure and speed to ensure proper filling and solidification.
Boosting systems provide the necessary pressure boost to achieve this, making it possible to manufacture parts with intricate designs and thin sections.
Reducing Defects and Scrap
By improving the filling and solidification process, boosting systems help reduce defects such as shrinkage porosity, blowholes, and inclusions. This leads to fewer scrap parts and higher overall yield, which is critical for cost-effective die casting operations.
Enhancing Tensile Strength
In some applications, such as sports goods manufacturing, boosting the injection pressure can lead to improved tensile strength of the die-cast components. This is particularly important for parts that need to withstand high stress and impact.
Integration with Modern Die Casting Machines
Modern die casting machines often come equipped with advanced boosting systems that can be controlled and monitored in real-time. These systems can be integrated with sensors and data analytics tools to optimize the process parameters dynamically, ensuring consistent quality and performance.
Safety and Ergonomics
Boosting systems can also be designed with ergonomic features, such as easy-to-use handwheels or automated controls. This makes the operation safer and more comfortable for workers, reducing the risk of accidents and repetitive strain injuries.
Die casting machine supplier: Haichen Machinery
Haichen Machinery is a supplier of die casting machines and related spear parts. We specialize in providing die casting production solutions for various materials, including aluminum, magnesium, zinc, and copper alloys. Our cold chamber and hot chamber die casting machines are used for manufacturing products such as automotive parts, LED lamp shells, radiators, and household appliance components.
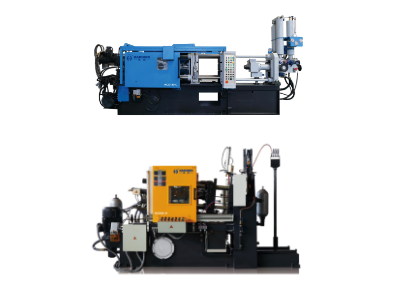
Boosting systems, including boosting cylinders and related components, are essential in die casting operations for improving casting quality, enhancing production efficiency, and enabling the production of complex and high-performance parts.