The casting force in die casting machine is the force that the working fluid in the injection cylinder of the die casting machine acts on the injection punch to push the liquid metal to fill the mold cavity.
The unit of casting force is KN.
The casting force is one of the key indicators of the performance of the die-casting machine. Because it directly affects the quality and production efficiency of the castings. First of all the die-casting machine applies pressure to the molten metal through its injection system. Then the injection/casting force ensures the alloy material can quickly and uniformly fill the mold cavity. Thereby obtaining high-quality castings, the higher pressure before it solidification,.
In the die-casting process, the size and control accuracy of the casting force have a direct impact on the density, strength, and surface quality of the castings. For example, appropriate casting force can reduce pores and defects in the castings and improve the mechanical properties of the castings. In addition, the control of the casting force also involves the real-time adjustment of the injection speed and pressure. It is crucial to improve the quality and precision of the castings.
The calculation formula for casting force
In die-casting production, the injection force is an important parameter, usually represented by P or F.
It is the main factor in obtaining die castings with dense structures and clear outlines. And we can adjuste the casting force on the die-casting machine.
The calculation formula of injection force is:
Pr=PG•πD²/4
- Pr: is the casting force
- PG: is the pressure of the pressure oil
- D: is the diameter of the injection cylinder
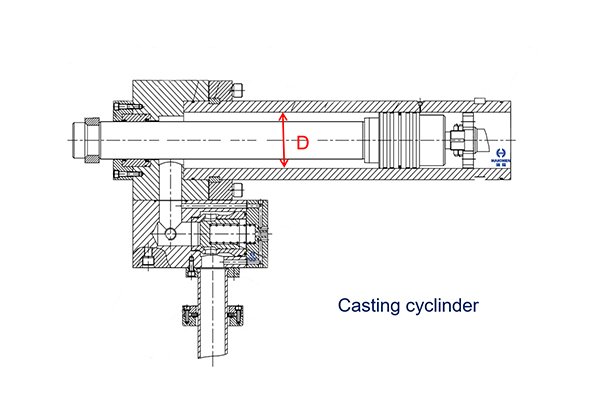
In general, casting force is Pressure multiplied by area.
Four main stages of casting/injection force:
- The first stage: slow injection.
The main purpose of this stage is to prevent the molten metal from splashing. And ensure that the molten metal surface does not roll up to form bubbles. The punch moves at a low speed to slowly raise the molten metal to the inner gate.
- The second stage: fast injection.
After the slow injection is completed, the punch continues to advance at a higher speed. The molten alloy will fill into the mold quickly. The speed of this stage has an important impact on the quality of the product.
- The third stage: pressurization.
After the molten metal basically fills the cavity, the system will increase the pressure. It ensures that the molten metal is completely compacted and the internal pores are eliminated.
- The fourth stage: pressure maintenance.
After the cavity is completely filled, the system maintains a certain pressure for a period of time. It makes the density and strength of the casting.
The speed and pressure during the injection casting process can be adjusted. The adjustment through the speed regulating valve of the die casting machine. The adjustment has to meet the requirements of different materials and castings.
The main function of casting/injection force
- Generation and transmission: The injection/casting force is generated by the injection pump of the die-casting machine. Through hydraulic oil, it is transmitted to the injection cylinder. Then to the injection piston, and finally to the injection punch, pushing the metal liquid to fill the mold cavity.
- The object of action: The injection/casting force directly acts on the metal liquid surface. It pushing the metal liquid into the mold cavity. The magnitude of this force determines the flow velocity and filling effect of the molten metal. If the injection force is too low, it may cause the molten metal not fully fill the mold, thereby affecting the quality of the casting.
- Change and Regulation: In the die-casting process, the injection/casting force is not constant. But varies with different stages of the injection process. For example, during the boosting phase, the injection force will increase. It compacts the solidifying metal liquid and improves the density of the casting. In addition, by adjusting the cross-sectional area of the injection cylinder and the pressure of the working fluid, the magnitude of the injection force can be changed.
- Influencing factors: The magnitude of the injection force is influenced by various factors. It including the pressure of the hydraulic system, the cross-sectional area of the injection cylinder, and the speed of the punch.
In summary, through a series of hydraulic systems and mechanical structures and acting on the molten metal, we can transmit the casting force. Its magnitude and variation directly affect the fluidity of the molten metal and the quality of the final casting.
The casting force setting
- The setting of injection/casting force affects the density and contour clarity of castings.
During the die-casting process, injection force is divided into dynamic injection force and pressurized injection force. - Dynamic injection force is used to overcome various resistances. It ensures that the molten metal is filled at a certain speed. Also, we will improve the density of the casting part, by using intens injection force after the filling is completed.
- The setting of injection force is closely related to factors such as the shape, size, complexity, and alloy properties of the die casting.
We will use the higher pressure for the casting prats with large wall thickness or complex structure. Because it ensures the die casting parts forming and usage requirements. - The injection force directly affects the internal quality of the casting. Such as the formation of defects such as porosity and shrinkage. Properly increasing the injection force can help reduce these defects and form a denser structure.
Therefore, when selecting die-casting process parameters, setting the injection force reasonably is one of the key factors to ensure the quality of castings. By optimizing the injection force, the mechanical properties and surface quality of castings can be improved, while reducing the scrap rate in the production process
Haichen die casting machine technical parameters of casting force
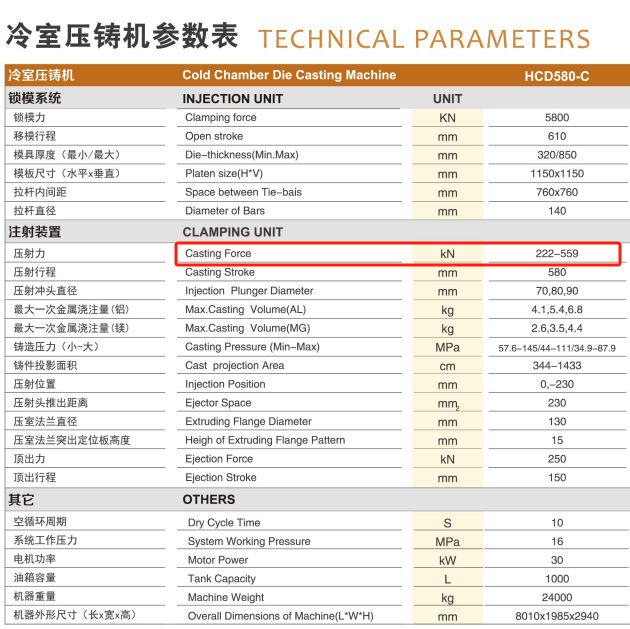
Haichen die casting machine
Haichen is one of die casting machine manufacturers in Ningbo. And it produces high pressure cold chamber die casting machines and hot chamber die-casting machines. These machines with up-to date die casting technology and high-speed press injection devices.
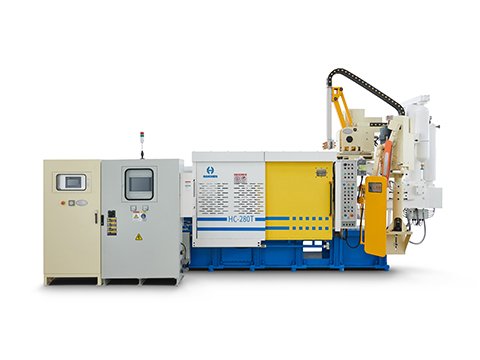
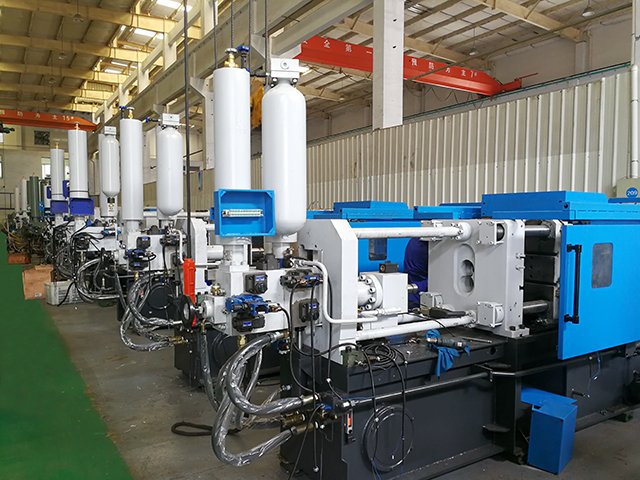
Conclusion
In short, the casting force of the die-casting machine is one of the key factors to ensure the smooth progress of the die-casting process. It not only affects the physical properties of the casting, but also affects the overall production efficiency and cost control.