The sprayer of the die casting machine is an indispensable part of the die casting production.
And its main function is to coat the mould cavity with mould release agent to prevent the casting from adhering to the mould .Help to improve the surface quality of the casting.
The Components of sprayer for die casting machine mainly as follows:
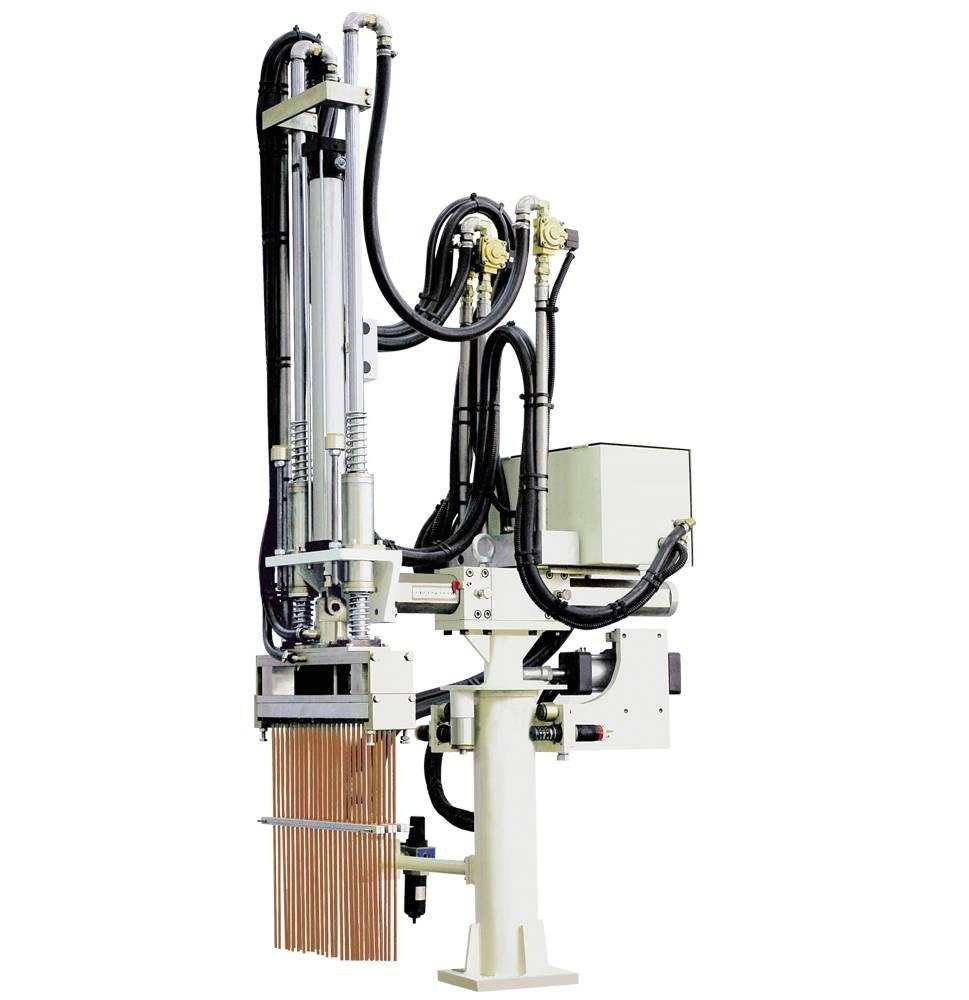
1. spraying pipe:
2. atomising unit
3. electrical control unit:
4. compressed air system:
5. lubricant tank:
6. filter:
1. Spray Pipe:
This is a pipe inside the mould to carry the lubricant to the surface of the mould.
The outlet of the spray line is usually located on the slide or ejector pin .
Ensure that spraying can take place when the mould is open.
2. Atomising device:
Similar to a spraying robot on a die casting machine.
This device atomises the lubricant into fine particles for uniform distribution over the die surface.
This device is usually connected to the electrical control unit of the die casting machine to synchronise the operation.
3. Electrical control unit: It controls the operation of the spraying unit, including the starting and stopping of the atomizing unit.
This unit is usually borrow from the original control module of the die casting machine.
Which simplifies the complexity of the spraying system.
4. compressed air system:
It to assist the spraying process by blowing the lubricant through the spray lines with compressed air.
Help remove residues from the mould surface.
5. lubricant tank: stores the lubricant used for spraying。
Usually a water soluble lubricant, to ensure that the casting can be released smoothly.
6. filter: used to remove suspended matter from the lubricant to ensure the purity of the lubricant when spraying.
These components together constitute the core part of the die-casting machine sprayer.
Through the reasonable configuration and use, can significantly improve the quality of castings and production efficiency.
The use of atomising devices for die casting machine sprayers
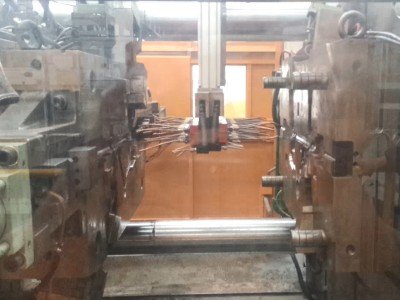
The use of die casting machine sprayer atomising device mainly involves the spraying of mould lubricant to improve the surface quality of castings and production efficiency.
The actual industrial production will appear in the following points about the use of die casting machine sprayer atomisation device:
1. Application of spraying technology within the mould
2. The application of intelligent spraying system
3. New coating atomisation spraying system
4. Mould release agent spraying device
5.Research and application of atomisation technology
- The application of spraying technology within the mould: through the design of spraying pipes and atomizers within the mould, can effectively solve the problems of poor spraying,
local sticking moulds, strains and so on,so as to improve the surface quality of castings and production stability.
- The application of intelligent spraying system: in the die-casting production line, the use of PLC-based robot control system and spray robot fixed-point quantitative spraying technology.
It can achieve spraying, die-casting pickup and a series of processes such as automation, improve production efficiency and safety.
- New coating atomisation spraying system: using compressed air as the driving force of the new coating atomisation spraying system.
Which can realize the uniform control of the coating thickness, suitable for casting spraying and centrifugal casting process.
- Mould release agent spraying device: there is a new scientific research technology introduces a casting mould release agent spraying device, the device includes one or more nozzles and spraying mechanism.
Which can quantitatively distribute the mould release agent slurry and improve the spraying efficiency and quality.
5. Atomisation technology research and application: atomisation technology in die casting is not only limited to spraying, but also includes cooling, dust reduction and many other aspects.
For example, the application of gas-water atomisation nozzle can significantly improve the surface and internal quality of the casting billet.
The use of die casting machine sprayer atomisation device covers from mould lubrication to the production process in many aspects, through technological innovation and system optimization, can effectively improve the efficiency of die casting production and product quality.
The Importance of Lubricant Tanks for die casting machine sprayer
Die casting machine spraying machine lubricant tank is an important part of the whole sprayer for die casting machine-.
Its importance is mainly reflected in the following aspects like:
1. Prevent lubricant pollution and degradation
2. Ensure the stability of lubricant performance
3. Extend the service life of the equipment
4. Improve production efficiency and profitability
5. Environmental protection
1.Prevent lubricant contamination and degradation:
Lubricants may be affected by the external environment during storage.
Such as moisture, airborne pollutants, etc.
These factors may cause changes in the physical and chemical properties of the lubricant.
Thus affecting its lubrication effect and service life. Proper storage conditions can effectively prevent these problems from occurring.
For example, lubricant storage tanks need to be designed with good water and gas separation to keep the oil pure and stable.
2.Ensure that the performance of the lubricant is stable:
the performance of the lubricant is stable for the normal operation of the die casting machine is critical.
Unstable lubricant may lead to increased wear and tear of machine parts, increase maintenance costs, and even affect production efficiency and product quality.
Therefore, the design and management of lubricant storage tanks need to ensure that the lubricant is maintained in the best condition before use.
3.Extend the service life of the equipment:
Correct lubricant storage and use can significantly extend the service life of die casting machines and other equipment.
Improper storage conditions, such as too high or too low temperatures, improper humidity control, etc., can lead to degradation of lubricant performance .
Which in turn affects the normal operation and life of the equipment.
4. Improve productivity and profitability:
By optimising the storage and use of lubricants, machine breakdowns and downtime can be reduced and productivity increased.
In addition, proper lubricant management can reduce maintenance costs and improve the overall profitability of your organisation.
5. Environmental protection:
Proper lubricant storage and use also helps to reduce environmental pollution. Improper handling and storage can lead to lubricant leakage and contamination of soil and water.
Therefore, the use of environmentally friendly storage and handling methods is necessary.
The importance of die casting machine spraying machine lubricant storage tank is not only embodied in the normal operation of the equipment to ensure that the normal operation and extend the service life of the equipment, but also to improve production efficiency, reduce costs and protect the environment and other aspects.
Therefore, enterprises should pay attention to the lubricant storage and management, take effective measures to ensure the quality of lubricants and stable performance.
HAICHEN uses the Highest Quality Components of sprayer for die casting machine
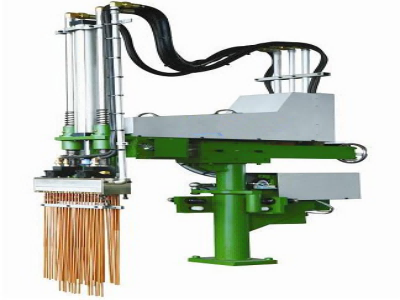
We HAICHEN use high-quality components and advanced design concepts in our die-casting machine spray systems.
These are the actual features:
1.Automatic sprayer and control method
2.Environmentally friendly mould spraying systems
3.Spraying devices for metal die casting machines
1.Automatic sprayer and control method:
HAICHEN has developed an automatic sprayer and its control method, which includes a mechanical part, an electric circuit part and an air circuit part.
The mechanical part consists of a frame, a horizontal travelling mechanism equipped with a unique rolling shaft and a vertical travelling mechanism equipped with guide rods and linear bearings, which replace high-cost linear guides.
The spray block is equipped with adjustable ball joint nozzles. The circuit section includes a power circuit, a signal circuit, a control circuit, a conversion circuit
An execution component (OC) and a human-machine interface device.
The air circuit section uses an air compressor to generate compressed gas and transmits and distributes the compressed gas and release agent through air and water hoses.
2.Environmentally friendly mould spraying system:
Equipped with environmentally friendly perfect die casting special mould spraying system (DCLP spraying system).
It can be widely used in weldable casting, heat treatment casting and thin-wall casting demoulding and other production processes. For you to solve a variety of mould release and mould cooling needs.
3.Metal die casting machine spray device:
One kind of spray device suitable for installation in the metal die casting machine, can connect to the high-pressure air supply source.
The device comprises a nozzle, a fluid supply unit and a control unit. The nozzles include a plurality of gas nozzles connected to the high-pressure air supply source, a plurality of water nozzles, and a plurality of release liquid nozzles.
The liquid supply unit can provide water and release fluid to the nozzles. The control unit connecting to the nozzles and includes a plurality of control elements connected to the gas nozzles, the water nozzles, and the release fluid nozzles.
Which can independently control the opening and closing of each of the nozzles, thereby efficiently increasing the cooling rate and saving the use of the release fluid.
HAICHEN uses high-quality components in its die-casting machine spraying systems.
These include unique mechanical structures, advanced circuit and air circuit designs like environmentally friendly mould spraying systems, so that we can ensure high efficiency and automation.