Conveyor type comparison in die casting include as follows
- Chain plate conveyor
- Stainless steel chain plate conveyor
- Roller conveyor
- Vibrating conveyor
- Belt conveyor
- Trolley and positioning device
In the die casting process, the conveyor is the key equipment for automated production.
And its selection directly affects production efficiency, cost control and product quality.
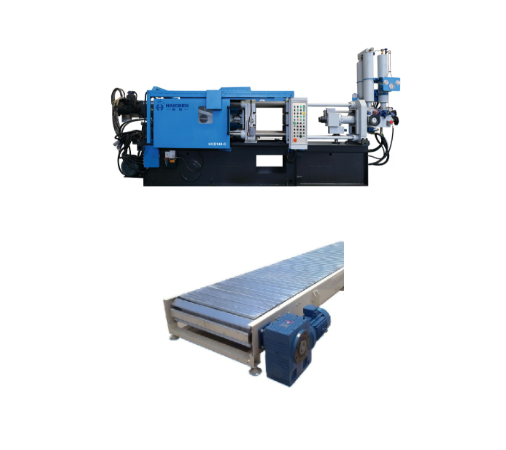
The function of die-casting conveyors
Die-casting conveyors are mainly used to remove die-castings from molds and transport them to cooling boxes or other processing equipment.
For instance, conveyor belts can transport die-castings to the cooling box for cooling, preventing the die-castings from scattering or getting damaged inside the mold.
In addition, the conveying mechanism can also cooperate with the cooling system to redistribute the coolant into the mold through a circulation path, further optimizing the cooling effect.
The role and core functions of conveyors in die-casting processes
In die-casting production, conveyors are an important component of automated production lines, mainly used for the transportation, cooling, cleaning, sorting and other links of die-cast parts.
Continuous production support
It replaces traditional manual or transfer vehicle operations to achieve seamless connection of die-castings from molds to subsequent processing equipment (such as deburring, polishing, and inspection), thereby enhancing production efficiency.
Temperature control coordination
Through air-cooled and water-cooled conveyors, high-temperature die-castings are rapidly cooled to prevent deformation and shorten the production cycle.
Process integration
During the conveying process, sandblasting, cleaning, drying and other processes can be integrated to form a multi-functional assembly line, reducing the time for process switching.
Enhanced safety
Reduced manual contact with high temperatures or sharp workpieces, lowering the risk of work-related injuries.
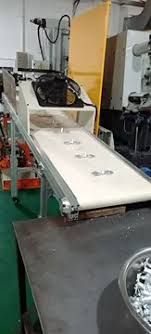
Comparison of conveyor types and technical characteristics
The commonly used conveyor types in the die-casting machine mainly include chain conveyors, stainless steel chain conveyors, roller conveyors, vibrating conveyors, belt conveyors, trolleys and positioning devices.
Chain plate conveyor
Structural features: Composed of chains, metal plates and drive devices.
It has strong traction and can withstand high loads (such as 800 kg/m).
Material: Carbon steel or stainless steel frame, suitable for high-temperature (-20℃ to 100℃) and heavy-load scenarios.
Advantages: The conveying surface is flat with low friction.
It supports horizontal or inclined conveying (inclination Angle ≤45°) and is suitable for automated assembly lines.
Disadvantages: High maintenance cost, the chain is prone to wear and tear, and it may become loose during long-distance transportation.
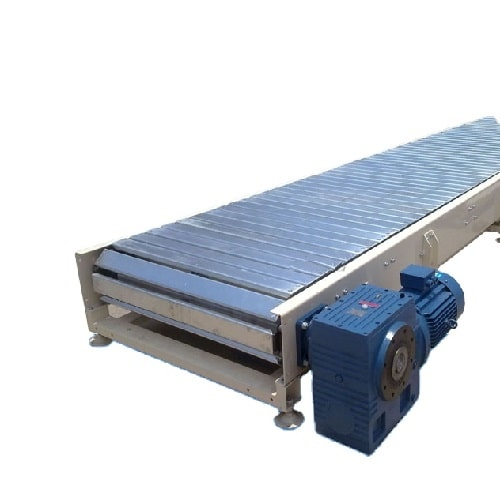
Stainless steel chain plate conveyor
Core performance: Strong corrosion resistance, suitable for scenarios with high hygiene requirements such as food and medicine.
The lifespan exceeds 5 years, and the lifespan of the rollers is 2 to 3 years.
Parameters: Speed 0-25 m/min, maximum width 2 m, length 30 m.
Application: High-temperature die-casting parts cooling, cleaning and drying production line.
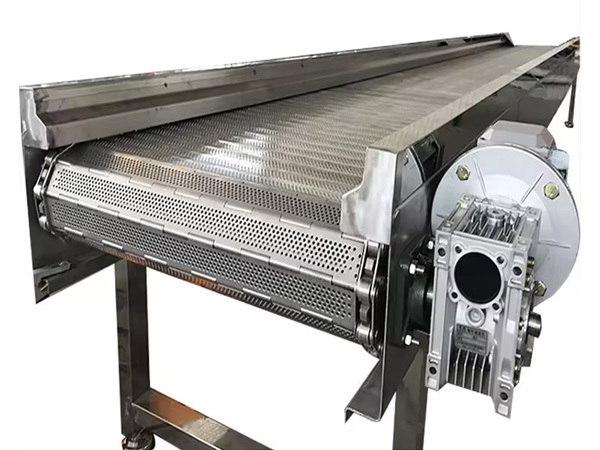
Roller conveyor
Working principle:
It is conveyed by roller rolling and is available in both powered and unpowered types, suitable for sorting and packaging scenarios.
Features:
Simple structure and low maintenance cost.
However, the conveying speed is relatively slow (0-15 m/min), and it is suitable for light materials.
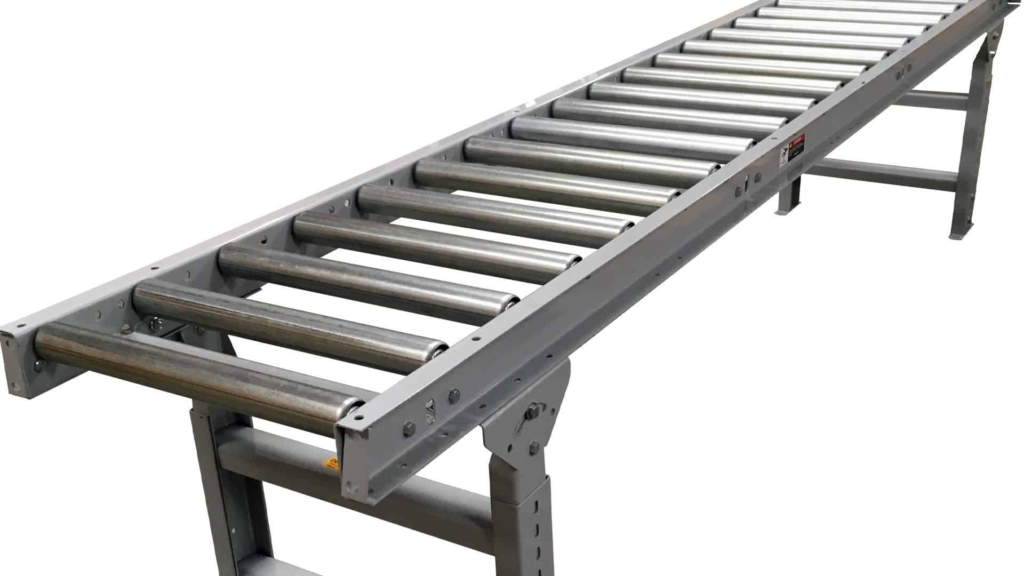
Vibrating conveyor
Function: Specifically designed to convey, screen, and dry materials, this system effectively handles hot reclaimed sand and small castings in production workflows.
Parameters: The system achieves a maximum length of 7.2 meters for single-unit configurations, while dual-unit setups extend this capacity to 30 meters.
Notably, it maintains low energy consumption levels and requires minimal maintenance costs during operation.
Limitation: However, due to its material handling mechanism, it cannot effectively convey highly viscous or damp materials, particularly those exceeding standard moisture thresholds.
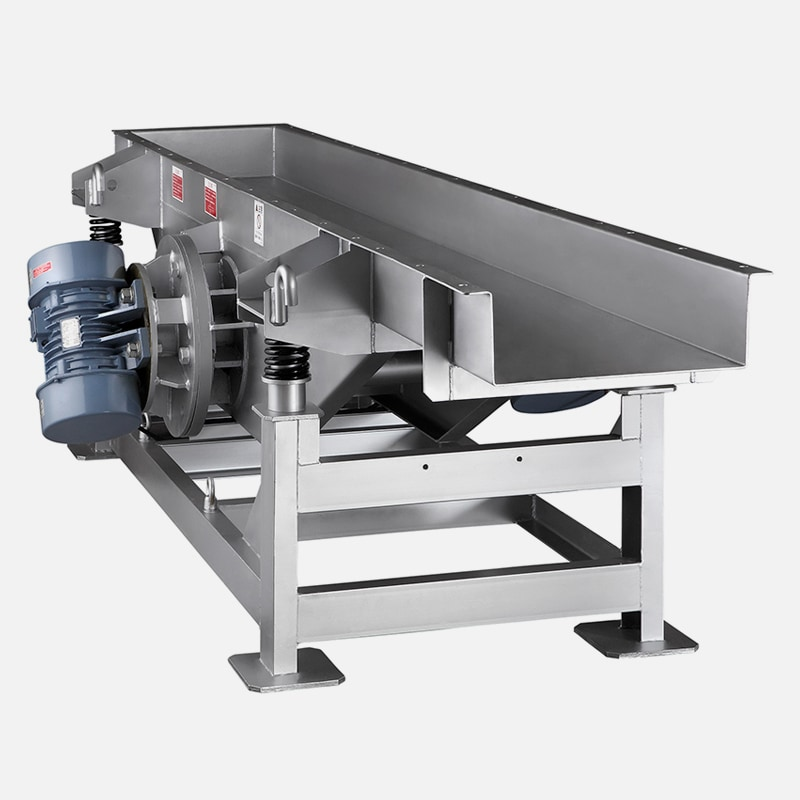
Belt conveyor
Advantages: Long conveying distance (up to kilometer level), smooth and low noise.
The rubber belt has a lifespan of approximately 10 years and is suitable for loose materials.
Disadvantages: It is prone to aging in high-temperature environments and the belt needs to be replaced regularly.
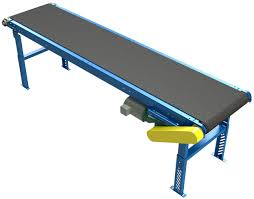
Trolley and positioning device
Application: Loading and unloading of heavy molds or sand boxes, with high positioning accuracy.
For example, the service life of the positioning block is ≥ 20,000 times.
Maintenance: The support system needs to be lubricated and inspected regularly.
Design requirements and key technical parameters of conveyor belts
High-temperature resistance performance
The covering layer needs to withstand instantaneous high temperatures (such as 800℃).
The design must incorporate carbonized layer technology or utilize metal materials for enhanced protection.
Furthermore, the framework material consists of polyester canvas (long-term 150°C).
Or steel mesh (long-term 650°C), specifically chosen to maintain structural strength under varying thermal conditions.
Speed and speed regulation capability
Typical speed range: 0-10 meters per minute, supports variable frequency speed regulation to adapt to different production rhythms.
In high-speed scenarios (such as small castings), it is necessary to optimize the friction of the drive system to prevent material deviation.
Load-bearing capacity and structural strength
The chain plate conveyor belt achieves a single-piece load capacity of 400kg, which necessitates reinforcement of the hinge and support structure design.
Additionally, belt-type conveyor belts improve load-bearing stability by increasing idler density.
Environmental adaptability
Anti-corrosion design
For the oil mist and metal dust environment in the die-casting workshop, stainless steel or surface coating treatment is adopted.
Protective device
The side baffle prevents debris from getting stuck, and the self-cleaning structure reduces maintenance frequency.
Customized requirements
The length and width can be customized (width 100-3000mm) to adapt to different die-casting machine models and production line layouts.
Special path design
Such as climbing slopes (inclination Angle ≤45°), and turning with modular chain plates to achieve spatial optimization.
Typical application scenarios
High-temperature die-casting part cooling and cleaning
Stainless steel chain plate conveyors are heat-resistant and easy to clean.
And are used for cooling lines and cleaning after sandblasting.
Casting sorting and packaging
The combination of roller conveyors and automated sorting systems enhances logistics efficiency.
Sand treatment and recovery
In industrial sand processing, vibrating conveyors first screen hot old sand, subsequently, belt conveyors handle the long-distance transportation of molding sand.
Heavy-duty mold transfer
The trolley device achieves precise positioning and, in conjunction with the hydraulic system, transfers large molds.
Continuous production line
Chain plate conveyors are connected in series with die-casting, assembly and inspection links to form an automated assembly line.